By Markus Schmolz, Schwäbische Werkzeugmaschinen
Nowadays, machine tools can connect to a comprehensive data acquisition regimen via the Internet that goes beyond just status-oriented maintenance information. Maintenance, production and management groups can use the acquired data. This means, for example, a manufacturer can make accurate statements about the total cost of ownership (TCO) of the machines it uses.
Online or Offline?
There's been considerable discussion for several years about the appropriateness of online services in the machine tool environment. Some companies already use these technologies to bring transparency not only to the associated states of their machines but also to the production processes.
Other companies still ask, "Why should we investigate the value of machine-status monitoring? Does it make sense to spend money for such services? Isn't it dangerous for a company to connect operating machines to the Internet? Can the machine status data be used to make decisions for production processes, beyond the obvious maintenance requirements?"
[pullquote]Schwäbische Werkzeugmaschinen (SW), a major German machine tool manufacturer in Schramberg-Waldmössingen in the German Black Forest, has a positive view of the benefits these initiatives provide. For many years, the company has provided comprehensive monitoring of its machines' data. "What is new is that this global data acquisition allows us not only to determine the ideal intervals for use-dependent maintenance, but also to provide customer-specific, matched solutions with very useful background information for the production," says Peter Siegel, responsible for the development of online services at SW. "This gives the management an operational transparency that it doesn't have otherwise."
Productivity and High Accuracy
Schwäbische was founded in 1994 and since 2004 has been the competence center within the EMAG group (www.emag.com) for the machining of prismatic workpieces. The company, with about 330 employees, produces about 160 machine tools annually, including high-performance one- to four-spindle machining centers and special machines (Figure 1). About 70-80% of SW's customers come from the automotive industry, with other application areas including medical technology and the hydraulics industry. SW sells its machine tools worldwide, with Europe as its main focus.
A Comprehensive View
More than 65% of the SW machines sold today connect to the Internet. "However, by no means do all customers use the resulting information fully," Siegel says. "Many still envision reactive maintenance service as the only possible use, and only when a fault has occurred."
Nowadays, however, it is possible to use the data to react in advance and not just to the operational status of the machines. The current state-of-the-art allows the machine's operational data to be recorded continuously (Figure 2). As a consequence, the user can draw conclusions about performance.
Figure 2: Machine uptime reporting for a machine tool is one of the lifecycle data reporting capabilities provided to customers by the SW Online Services.
SW
This capability requires that all relevant data be gathered. Consequently, several years ago, SW equipped its spindles with sensors that could check spindle status without removing them from the machining head.
Meanwhile, the global data recording allows useful conclusions to be obtained for maintenance, production and management. "Our services provide the maintenance department with a powerful tool that makes its work simpler and faster," Siegel says. "The maintenance staff no longer needs to wait for our alerts and updates. They can work with the data themselves."
For production analysis, the same data source can be used to determine, for example, how often the "JOG" operation has been selected, how long the setup took, if and for how long the machine stopped without the presence of a malfunction, or how long the response time was to a malfunction.
"All this data makes it possible to determine the causes of qualitative problems, why processes are instable or why the number of produced parts falls suddenly," Siegel says. "Ultimately, a company can achieve process optimization and/or productivity increases."
Data Means Euros
Johannes Zuckschwerdt, SW technology development project engineer, provides an example of what complete data monitoring can achieve. "During a performance evaluation, one machine had, for example, a utilization time of 24 hours and apparently no optimization potential," he says. "The data monitoring, however, showed that the machine stopped for 100 minutes per day to wait for loading acknowledgements. On a cycle time of 1.2 minutes, 83 more parts could have been processed during this time."
At €8 (~$11.10 at $1.39/€ on 10/15/10) per part, Zuckschwerdt adds, this would mean an added output value of €239,000 (~$332,200) over a year. This is a theoretical value. However, even if we divide this value by five or 10, a very impressive amount remains when all the machines are considered. Our customers have learned that these services pay for themselves very quickly.
Operating or company management obviously has an interest in optimum production and often needs to document process reliability. This group clearly can benefit from the comprehensive data obtained. Documentation is particularly critical in the automotive industry, where suppliers require a process validation protocol. Of particular importance for management is the overall cost of a machine during its lifecycle, or TCO.
Realistic TCO values require operational data from actual use. This data can be derived from the previously used condition monitoring or the acquisition of usage data. Although this allows the user to calculate lifecycle costs over several years, hidden potentials such as process monitoring and optimization remain undiscovered.
More-complete data acquisition also reveals creeping process deviations, machine-state fluctuations or resource consumption, which can be included in the overall cost evaluation. At the same time, it is possible to counter their causes or correct them in a planned manner.
A global data storage approach also gives machine constructors and end users the ability to prepare comparisons of machines and processes that might point out location-related issues for end users, and to create reports that document process reliability.
Hurdles Remain
The data that SW can provide gives the machine operator and its customers security. "All we need is Internet access," Siegel explains, "and our customer receives the complete services."
Although this might appear simple, in practice, the execution frequently encounters hurdles. There is general mistrust of Internet connections in production. This also means that the IT department is involved. "In the past, IT departments were not much concerned with numerical controllers and other onboard controls," Siegel says. "Today, controllers are part of the global network, so it is necessary to involve the IT department and to open the required communications paths and establish some mutual trust within the company."
Existing reference points help the builder here, most of which are based on theoretical factory runouts that are quite rigorous and certainly real-world. In most cases, the empirical data are being referenced to time charts kept by the end user, the builder, Siemens or all parties for instant analytics.
SW Leverages ePS Services
SW knows when to partner for services outside its core competencies. "It is not economical for us as machine tool manufacturers to provide the data-processing platform for all these services," Siegel says. "Consequently, for many years, we've used ePS services, which have supported us well."
ePS Network Services, a Siemens subsidiary, describes itself as an Internet-based infrastructure with high-performance servers, storage media and connections to email and SMS text messaging systems, as well as a source for software for the acquisition, preparation and archiving of machine-specific data.
"For customers, this means project cost reliability for the creation of Teleservice services, the use of a proven structure and a high level of data security provided by the network," explains Jochen Heinz, consulting team leader for Value Added Services at Siemens (www.usa.siemens.com/cnc).
The services are compatible with current IT security standards, Heinz adds. "The communication between the machines or service PCs and the ePS servers is limited to the ePS server and uses only certified software components," he says. "Access from external servers is not possible. In such a case, the client server simply does not execute the scripts. The communication is generally established only from the machine or the service PC to the ePS servers."
Siegel emphasizes that this method and an additional encryption has meant that "to date, no data leakage whatsoever has occurred."
Future Aspects
This certainly can have positive effects on spare parts planning. "When I consider machine components that originate from third parties—spindles, for example—it now is possible to involve their manufacturers," Siegel says. "We can provide notification of pending maintenance or for a soon-to-be-required replacement."
It is important to note, he concludes, "We are neither spies nor robber barons. We want to support our customers in the best possible manner, so they can operate our machines without problems. I think we're proving the value of this ePS service every day."
Markus Schmolz is a manager at Schwäbische Werkzeugmaschinen (www.sw-machines.de), a metal-processing machine manufacturer in Schramberg-Waldmössingen, Germany.
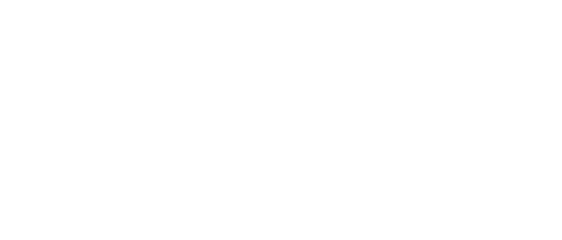
Leaders relevant to this article: