By Loren Werneke, MoCo Engineering and Fabricating
The flagship 10-axis stickering stacker is our most sophisticated machine. Used on sawmill lines, the stickering stacker inserts wooden or aluminum spacers, called "stickers," on 1- or 2-ft centers between each course of cut-to-length lumber while simultaneously stacking the courses.
Typically, the motion on a stickering stacker was driven by hydraulics, variable-speed ac motors or a combination of both. MoCo had been considering an all-electric, servo-driven stacker designed to improve performance and reduce energy use. An experiment we conducted a few years ago proved that servos could operate well under sawmill conditions, but our company was unsure that the market would support such a machine.
New Opportunities
Figure 1: The line-regenerative, electric servo-driven synchronized stickering stacker is designed to reduce energy use and environmental impact.
MOCO ENGINEERING
Where the Drive Meets the Bus
To choose components that would make the servo-electric concept a reality, MoCo teamed with Northwest Motion (www.nwmotion.com), a local automation distributor that had been a supplier to MoCo since 2000. "The two suppliers we considered for this were Rockwell Automation and Rexroth," explains Hahn. "We went with Rexroth because I'd used their components at a previous company and was familiar with the ease of use with them. One of the biggest selling points was the follow-up help we had previously received working with Northwest Motion. They spent two weeks with us with the first startup, and then they helped with the fieldbus. I knew we'd get that level of support from them."
Based on its experience with servo designs, Northwest Motion recommended an IndraDrive system, IndraDyn servo motors and a common dc bus with regenerative capabilities so that excess power could be diverted from one axis to another or back onto a mill's main power grid. The final lineup included IndraDrive M digital intelligent servo drives with a CCD master communicating with a third-party PLC via DeviceNet, IndraDyn synchronous and asynchronous servo motors with IP65 protection class and the common dc bus with an HMV-R 65 kW regenerative power supply.
All motion functions and synchronization are handled by parameterizing drive firmware with no PLC code or programming required at the drive level. The drives are synchronized through high-speed Ethernet-based SERCOS III communications protocol and simultaneously control synchronization of the machine's fork lift, carriage, stick shuttle, stick placer, rake off, pull back and other motions.
"We put a Web port on the system, so we can get on the control system and troubleshoot while sitting at our desks via the Internet to diagnose issues such as servo sync or losing zero and to read the fault codes right from the drive," says Hahn.
The stacker has a 30–40% improvement in throughput over the hydraulic machine. Handling 8-ft-wide courses at up to 12 cycles/min and loads up to 40000 lb, the stacker receives lumber while delivering stickers into evenly spaced courses of wood. The lumber then is arranged and stacked automatically on the main hoist to be prepared for kiln delivery.
Each axis of motion follows its own onboard electronic motion profile while maintaining precise synchronization with other axes by simultaneously following a virtual master (VM). Each drive is capable of hosting a VM, and any axis in the system can be directed to follow any VM in the system. Free assignment and sharing of VMs for axis synchronization is a key to the system. Communication between drives is achieved using Rexroth's Cross Communication Drives (CCD) ring, with synchronization data traveling via SERCOS III communications protocol over Cat. 5e cable.
Figure 2: Each axis of motion follows its own onboard electronic motion profile while maintaining precise synchronization with other axes. No limit switches, timing gears or external encoders are needed to determine or control axis positioning.
MOCO ENGINEERING
"With the hydraulic machine, if you had to hit an e-stop, you jogged one of the axes and had to remember where it was at," says Hahn. "Now that everything is off of cams, you can jog whatever axes you want, and as soon as you put them back in auto mode, everything comes back to where they're supposed to be."
Capture Before You Dump
While the servo system makes the machine easy to use, it's the regenerative power bus that puts the servo-electric stacker in another league for energy savings. The servo drives use a common-rail, line-regenerative power supply to capture energy from the stacker's machine cycle. The stacker can regenerate power from any motion cycle—horizontal or vertical—and share the power with other axes as needed. Drives that are regenerating power, such as a lowering hoist, can dump this power back on the common power bus so other drives can use that energy. Power from multiple drives can be directed to the main incoming line. On a typical hydraulic stacker this regenerative power would be dumped to a resistor bank and dissipated in the form of heat.
"This machine is operated over two shifts, about 16 hr/day," says Hahn. "The rate in the Spokane area is 7.223¢/kWh." Energy reductions of 40–75%, with savings of up to $45,000 per year have been documented. The line-regenerative power supply can put approximately 5 kW of power lasting several seconds back onto the ac power grid during deceleration of the main hoist. "We could do that, but we don't," he explains. "The regenerative system has a common bus between all of the axes on the stacker." The other vertical axes also contribute regenerative power savings.
Diagnostics and Safety
In addition to energy savings and easier operation, the all-electric servo system provides other benefits for diagnostics and safety. "We can isolate the Ampere draw in the motors and quickly determine if there's a problem," says Hahn. "In addition, pre-set torque and force limits are monitored automatically and independently at each axis, so the control system can sense an unweighted load and prevent the hoist from dropping, causing a potentially unsafe condition (Figure 3)."
The transition from hydraulics to electric went smoothly, explains Hahn. "After five days of training on the new machine, we were fully proficient with setup, commissioning and operation," he says. "When we install a new machine, we train the operators on the functions of the machines, and we train the maintenance people or millwrights how to zero. We put a picture of the timing mark on the panel view so they know where it's supposed to be before they can zero it."
Loren Werneke is electrical hydraulic manager at MoCo Engineering (www.mocoeng.com) in Spokane, Wash.
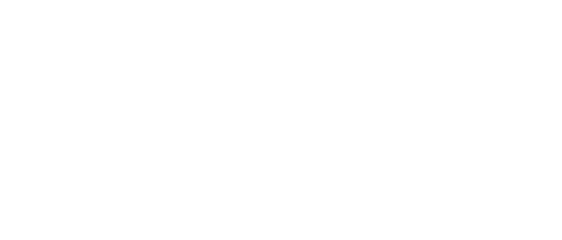
Leaders relevant to this article: