Wireless technology is ideal for remote measurements, explains Robert C. Jackson, senior industrial and embedded product marketing manager at National Instruments (www.ni.com). "The one area where wireless sensor networks with embedded logic might first evolve for control is embedded distributed control. In these systems, the control, for example, a PID algorithm, would execute on an embedded processor instead of over the wireless network," he says.
Wireless control is extremely promising, but its application in industry is a bit more complicated, says Eric Hollister, product sales engineer, Pilz Automation Safety (www.pilz.com). "Industry is loaded with difficult and complex moving applications where wireless I/O and control have huge potential," he says. "However, wireless technology has not yet reached a point where it is stable or reliable enough to be used for industrial control," he says.
WirelessHART, the wireless extension of the HART protocol, could go beyond just measurement and monitoring functions to handle control functions, but this would need to be limited to non-critical, non-safety applications, says Robert Schosker, product manager at Pepperl+Fuchs (www.pepperl-fuchs.com). With wired communication there is 100% certainty that no information is lost between the controller and the field instrument, unless there is a failure in the wired lines, he says.
InduraNetp features coexistence frequency management (CFM), so the system can coexist with other wireless systems in the 2.4 GHz ISM band and give immunity to interference from other wireless services. InduraNETp can be added to a new or existing I/O block without changing hardware. A maximum of 64 operational and safety input/output modules, each with two or four I/O, can be installed in any order alongside a single PSSuniversal head module.Pilz Automation Safety734/354-0272
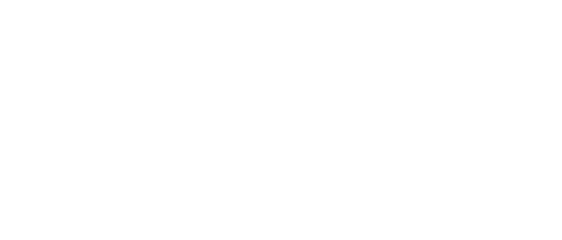
Leaders relevant to this article: