By Joe Feeley, Editor in Chief
The vibratory bowl conveyor used in many parts-picking operations provides an economical and reliable method of presenting small parts in a given orientation. However, a key weakness of the vibratory bowl feeder lies in its dependence on mechanical channels and guides to orient parts, which limits it to handling just one part or a family of similar parts.
The task of loading aerospace fasteners into a press would seem to be ideally suited for automation with a vibratory bowl feeder and a pick-and-place robot. The problem in an application presented to Rixan Associates (www.rixan.com) of Dayton, Ohio, was that the 415 parts involved would have required dozens of different feeders.
Rixan Associates developed a unique take on the vibratory bowl feeder concept by using machine vision to replace the channels and guides in order to handle a virtually unlimited number of parts within a certain size range.
Traditional, but Inflexible
Traditional vibratory bowl feeders use a helical, shelf-like, inclined ramp winding upward from the bottom of a bowl to a discharge passageway. The reciprocating motion pushes the parts up the ramp. Obstructions, cutouts and other orienting devices arranged along the passageway cause parts that are improperly oriented to topple off and allow only those parts that are properly oriented to pass through.
[pullquote]"Vibratory bowl feeders normally can handle only a single family of very similar parts," says Stephen Harris, president. "Each different part in a family requires changing or adjusting the obstructions and orienting devices, which can take considerable time or require the high expense of multiple bowls. With a typical bowl feeder, a part rides up a ramp, and then the part will fall back into the bowl if it did not get oriented correctly. It's really used to singulate and orient the part so it can be fed."
As a result, despite its high efficiency and relatively low cost, the vibratory bowl concept usually is not seriously considered for applications involving large numbers of different parts.
Harris felt that recent improvements in the speed, accuracy and reliability of machine vision systems would make it possible to use a vision sensor to replace channels and guides in the design of a flexible vibratory bowl feeder. "We got the opportunity to validate this concept when Rixan competed for a potential customer application that processes a wide variety of high-value aerospace fasteners in a forging press," says Harris.
Previously, an operator picked parts out of a bin and loaded them in the proper orientation in the press. This was an entirely manual process—just an operator and bins of different parts that had been made all at once. The manufacturer wanted to automate this operation because of the potential danger involved in having the operator place his hands into the press. Additionally, the repetitive nature of the task required the operator to take frequent breaks, which limited the productivity of the application.
New Vibratory Feeding Concept
Rixan engineers, led by Chief Technical Officer Mark Battisti, developed a unique flexible feeding concept that uses a track on a 24-in. vibratory bowl without the obstructions and cutouts (Figure 1). "Every part that reaches the top of the bowl is presented onto a raised semi-transparent plenum so the vision system mounted above easily can identify the type of each part and its orientation," says Battisti. "The robot picks the correct parts, while incorrect parts are recycled into the bowl."
Rixan selected a Cognex In-Sight 5401 vision system and a Mitsubishi Electric RV-6SL-S11 robot that were integrated through a joint development effort between the two companies. Mitsubishi Melfa-Vision software incorporates robotic programming software, and Cognex In-Sight Explorer software is used to set up both the robot and the vision system simultaneously as an integrated solution. This new approach makes it easier to create vision-driven robotic applications with capabilities such as locating and inspecting parts that go far beyond what robots alone can accomplish.
You could buy the vision system separate from the robot and robot software and integrate them, but Battisti thinks that's not a good idea. "That would be an option," says Battisti, "but the process of getting a camera and a robot talking to each other sometimes involves special programming and is costly to do on a one-off basis. Cognex and Mitsubishi aren't the only companies to collaborate like this, but the other important piece in our selection is the teach-a-part wizard concept that is a part of the higher-level software package and is the key offering of the Melfa-Vision software."
Melfa-Vision includes standard job programs supporting most common robot applications, enabling novices to more easily develop robotic vision applications with up to three robots and seven vision sensors. "Rixan engineers picked the Mitsubishi Electric robot because it is fast—moving at up to 6 m/sec—and has a long reach," says Battisti. "We selected the Cognex In-Sight 5401 vision system because it provides up to seven times the processing power of other models and acquires up to 60 eight-bit images per second (Figure 2)."
Program New Parts in Minutes
To develop the application, Rixan engineers first perform a one-time Melfa-Vision wizard that calibrates the robot in relation to the feeder. They then put a part in the robot gripper in the orientation that's ideal for pickup. They jog the robot over the feeder and set the part down on the plenum. This sequence teaches the robot to pick up the part in this orientation at this point on the plenum. Next, they select a Melfa-Vision wizard that runs the Cognex PatFind object-location tool and draw a rectangle around the part on the screen. "The PatFind tool instantly recognized the part in the zero angle of orientation," says Battisti. "This process, which took only a few minutes, is all that was required to program the feeder to handle a single part."
Most parts in this application are symmetrical top to bottom so the camera can identify them from their silhouette with the plenum backlit as described above. "But some other parts must have a certain side facing upward before they can be loaded on the press," says Battisti. "The Cognex PatMax tool is used to recognize which side is up on these parts. The pattern training process described above automatically learns the correct image of a right-side-up part and ignores the rest. Top-down lighting is used for parts where pattern recognition is required. White lighting is used for some parts and glare-free polarized lighting for others."
The feeder uses the vibratory bowl feeder concept to randomly present the parts in the bowl in any possible orientation. Parts that are in the wrong orientation, says Harris, simply recycle back into the bowl and continue going around until they become properly oriented. The vision system is able to distinguish one part from another so operators do not have to clean out the bowl when changing from one part to another. The parts remaining from the previous run will pass through the feeder without being used until the corresponding program runs again.
Productivity Payoff
The fastener manufacturer originally ordered a single Rixan feeding system and programmed it for a few parts. "The first feeding system was so successful that the manufacturer purchased two additional systems for automation of other presses and is in the process of programming them to handle its full range of parts," says Harris. "The feeding system is slightly slower than an operator working at full speed, but since the system does not take breaks it provides an increase of 20% in productivity per shift compared to a human operator. The vision system also eliminates errors that can occur in manual feeding, such as putting the part into the press in the wrong orientation, potentially damaging the tooling and causing substantial downtime."
The patent-pending Rixan RFS-1000 system costs about $45,000, "but with its 20% improvement in productivity and eliminating the need for an operator, it provides less than a one-year return on investment for most users," adds Harris.
Rixan believes the key to the success of this application is the ease-of-setup, accuracy and reliability of Cognex In-Sight vision sensors. "The customer is extremely pleased with the vision system performance, as well as the tight integration between the vision sensors and robots," says Harris. "The PatMax tool that we use to recognize part features is much faster and more accurate than other comparable industry tools that we have seen. Finally, the easy integration between Cognex vision sensors and Mitsubishi robots drastically reduces the amount of time required to develop vision-enabled robot applications and, in most cases, eliminates the need for writing a single line of code. Vision-enabled robots now make it possible for the first time to apply efficient and economical vibratory bowl feeding to automate applications with many parts."
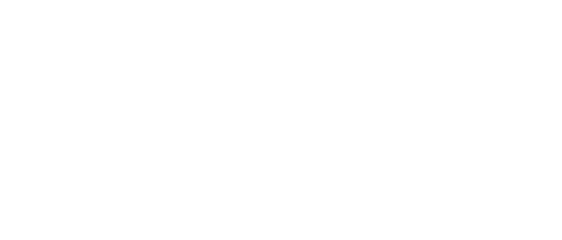
Leaders relevant to this article: