We’ve used servo motors for most of our axis-positioning requirements. We hear that some newer stepper motors now incorporate closed-loop position control that rivals servos, and still provide better torque. Any evidence out there about this?
—from May ’09 Control Design
ANSWERS
Don’t Exceed Expectations
Stepper systems are much less expensive than servo motor and amplifier systems. Some vendors have added functionality to their standard stepper amplifiers that allow for closed-loop operation. It’s been my experience that this type of functionality adds significant cost and makes the stepper amplifiers approach the cost of a servo amplifier. I would say that the majority of stepper systems sold are your basic open-loop amplifier and motor without a feedback device.
What are you giving up for the discounted price of a stepper system? Mainly performance and stability. Because of the inherent design of a stepper system, high-speed operation is not really practical. At speeds above 500 rpm or so, the available torque drops to around 30-40% of stall-torque value. As you increase speed, the available torque drops to almost nothing. Stepper motors also stall—they become unsynchronized, losing torque and position—when the torque demand is greater than the available torque. This means you normally need to account for a significant safety factor when sizing a step motor. This also makes stepper systems not so ideal when the load changes or when the load is not consistent in the application. You have to size for the worst-case scenario. There is no intermittent peak torque level with a step motor.
Stepper systems also have unavoidable resonance points. These are specific operating frequencies where loss of torque could occur. There is a low-speed resonance point around 50 rpm and a mid-range resonance point around 500 rpm. Most stepper amplifiers these days take some measures to counteract these resonances, but normally the user will end up simply designing around these speed ranges. Stepper motors are ideal for low-speed applications in which the load is unchanging.
Once you try to get more than that out of a stepper, you’re in for some problems. As far as digital networks and integrated safety go, steppers are not that high up on the food chain. The standard for controlling stepper amplifiers is with a pulse and direction command, typically coming from a PLC or other simple pulse-generating device.
I am not aware of any stepper amps that have integrated safety.
Scott Carlberg, product marketing manager,
Yaskawa Electric America
Two Steps Forward
Stepper motors are synchronous motors with a high number of poles, which can be regarded as direct drives. The advantages of stepper motors include high holding torque and very-good positioning capability. Individual steps or partial steps can be approached directly (i.e., without return system) through intelligent control of the stator windings in full-step or micro-stepping mode. This distinguishes stepper motors from servo motors and makes them a cost-effective alternative.
Excessive acceleration and fast load cycles can cause the stepper motors to become unable to follow the rotary field and “lose” steps. An encoder can help avoid problems in this situation. Stepper motors have their maximum torque in the lower speed range and an overriding holding torque at standstill. In many applications this makes a holding brake unnecessary.
Our I/O system features stepper motor terminals that can store suitable current curves for any speed or load profile, permitting optimum adjustment of the thermal motor load.
Bob Swalley, applications/support engineer,
Beckhoff Automation, www.beckhoff.com
Generally, servo motors are available in a much wider power range than stepper motors. We offer servo motors from 0.1 to 160 hp and stepper motors from 0.1 to 1.8 hp. As a result, servo motors offer more choices for a wide power range of applications.
A fairly new development in stepper control is to incorporate a rotor-position feedback—encoder or resolver—to optimize torque generation according to actual rotor position. This turns the stepper motor into a high-pole-count, brushless servo motor. An advantage of this technique is to normally run the motor in open-loop mode and only enter closed-loop mode if the rotor position error becomes too large.
The added encoder system feeds back the actual position to the drive to correct the number of steps performed if the motor loses some steps due to high load inertia and fast acceleration. However, it still does not position the motor between two steps. Hence, the added feedback does not improve the resolution and positioning accuracy of stepper motors. This typically is between 500 and 50,000 steps per revolution, while a servo motor with a sin/cos encoder offers a resolution of > 4 x 106 counts per revolution.
Ralph Baran, product manager,
Siemens Energy & Automation, www.sea.siemens.com
Servo Stepper Controller
Stepper motors and associated components have evolved, taking on new functionalities. An example would be our servo stepper controller that is equipped with encoder feedback capabilities to function as a closed-loop controller.
The torque is there with these servo stepper controllers; however, it’s also important to consider how well the component actually transmits that torque to your application. Select servo stepper controllers operate on a resolution of 64 microsteps, preventing step losses caused by acceleration and a finer step position. High resolutions prevent excessive wear on mechanical components. Furthermore, these servo steppers have current control, minimizing any power dissipation while increasing torque efficiency. Also consider vector control. When paired with the incremental encoder, vector control creates highly efficient rotational speeds.
Servo stepper controllers also offer six configurable inputs for start/stop, end-stop, reference, jog/tip, and can be processed directly via internal software. Two outputs can be linked with internal functions or used freely. This ensures servo stepper controllers can adapt easily to meet application needs via various acceleration ramps, command tables, auto reference and other event-driven characteristics while ensuring no position loss.
Mark DeCramer, product manager,
Our printing machines consist primarily of discrete I/O with a small quantity of analog I/O. We ship these machines worldwide, and to reduce startup time and travel we plan to start doing more extensive shop testing. Right now, we test on-machine I/O to some extent. But some I/O cannot be tested easily as it’s either field-installed or requires actual production for responses to make sense. For those I/O points, is software simulation the answer? Or should we go with hardware simulation by wiring at least some outputs to devices and reading responses at the inputs?
SEND US YOUR COMMENTS, SUGGESTIONS OR SOLUTIONS FOR THIS PROBLEM. We’ll include it in the September ’09 issue and post it on ControlDesign.com. Send visuals if you’d like—a sketch is fine. Email us at [email protected]. Please include your company, location and title in the response.HAVE A PROBLEM YOU’D LIKE TO POSE to the readers? Send it along, too.
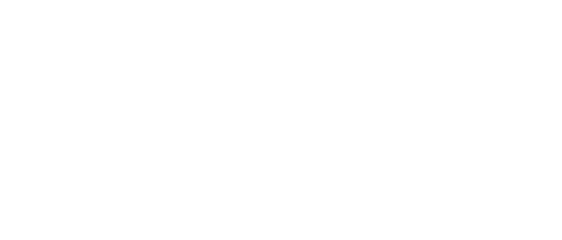
Leaders relevant to this article: