Energy is a critical element in any attempt to realize a sustainable production environment. The influences on this issue are both the obvious substantial savings that can come from using less energy per unit of production output, as well as the necessities for energy conservation and carbon footprint reductions that might soon be either encouraged by incentives or punished via penalties for insufficient action.
At the Manufacturing Perspectives press event this week at Rockwell Automation's Automation Fair, an experienced panel sought to define the actions that manufacturers need to take to better manage and reduce these costs, and to speculate on what new approaches might be available in the future.
Frank Peel, electrical support specialist at Owens Corning Canada, put the opportunities in perspective, saying of the Owens glass-melting process that the annual energy bill is on the order of $1 billion.
The underlying message of the panel makes it clear that this is a battle on two fronts: Compliance with legislative actions being considered in the U.S. Congress and more self-initiated actions by companies in both the private and public sectors.
Most of the discussion about possible legislative actions revolved around the Waxman-Markey bill, which includes a requirement for 20% of electricity to come from renewable fuels by 2025; carbon capture and storage incentives; smart grid and electrical car provisions; higher energy efficiency standards for buildings, lighting and appliances; a cap and trade program; reduction of global warming gases by 83% of 2005 levels by 2050; programs to compensate energy-intensive industries for costs incurred under the bill, and green job creation.
The panel soberly considered the bill's goal of global warming gases reduction in a growing economy―a reasonable likelihood over the next 40 years. Terry Gebert, Rockwell Automation vice president of systems and solutions business, asked how that goal can be achieved. "I don't know," said a man who, if anyone, should: Isaac Chan, program supervisor-technology development at the Department of Energy. "There are no clear options if that legislation becomes law. The GDP could rise three-fold [by 2050]." Chan said that implementing state-of-the-art technology in every applicable area might save 30% of greenhouse gas emissions—nowhere near the 83% target.
Bigger gains would have to come from incentives or penalties that encouraged or pushed companies to action. Even if we eliminated all fossil-fuel-based electricity generation, and all fossil-fuel-consuming vehicles, that wouldn't address the enormous energy consumption of steel-making, cement manufacturing and other heavy industrial segments, with enormous legacy equipment bases that cannot be turned quickly, Chan said. In addition, these renewable sources of energy such as wind, solar and others will have to be commercially viable technologies that companies will invest in. "So we need to invent something," said Chan. "We'll need to replace steel. We have to drive the next industrial revolution."
Despite the panel's opinion that even a 30% reduction by 2050 is not a realistic goal, they reported increasing levels of company action in reducing both energy consumption and carbon footprint.
Gebert reported a quote from Owens Corning's CEO in its sustainability report, saying "The cheapest and most sustainable energy is the energy saved by never using it." Asking panelist Frank Peel about Owens Corning's approach, Peel reported that upper management has some of its compensation based on meeting greenhouse gas and other emission targets. "That program filters down to us at the plant too," he said. "Our engineering and maintenance heads targeted cutting $100,000 from our energy budget this year." Asked if those goals were met, Peel said the plant actually is on target to save $160,000.
Opportunities are there in oil and gas, as well, stated Will McBride, an oil and gas industry veteran of more than 30 years who works as a consultant for the Alaska oil and gas industry, who also recognizes that the industry is largely very energy inefficient.
"We have equipment in place in Alaska, much installed in the ‘70s and ‘80s, sized for oil flow rates that now are twice the needed capacity," he said. "There are 15,000-hp turbines that could be replaced by a 3,500-hp motor and variable-speed drive. But the electrical room wasn't big enough for a new drive and the power infrastructure at the facility wasn't set up to do that." The power generation system will be replaced, he says, "but whether that's in my working lifetime, I don't know."
Frustrating obstacles that have nothing to do with the technology also get in the way, said Hand, referencing alternative sources for electricity production. "We have a number of places in California that would be good places for solar," he says. "In order to be cost-justifiable we need to build capacity that would over-generate. But we'd get no credit for feeding the excess back into the grid for others to use."
Peel later spoke of how Owens has begun using Kaizen improvement in its energy efforts, as it had been doing in other segments of the operation, recognizing that engaging everyone towards the objectives is essential. He got there reluctantly. "To me, being a controls guy, it was more something for the process guys," he admitted. "So we caved in, and established an energy Kaizen." It exposed some low-hanging fruit immediately. "We put dampers on furnaces to close them down a bit. We found moth-balled parts of the facility with steam heaters still turned on during the summer. It was an eye-opener when we questioned why we were doing stuff that we'd been doing all along."
Asked if his company is holding energy-reduction expenditures to standard ROI criteria or viewing it as some level of systemic need, Peel says in some cases, energy projects have three-year or more ROI, compared with the standard six months for other capital projects.
Not so much in oil and gas, lamented McBride. "Unless it has a solid ROI or has a regulatory requirement, it typically doesn't get funded."
Hand added that ConAgra also is pursuing a "use no more than you need" approach to cooking temperatures and cooking time with the help of Rockwell Automation controls.
The products and solutions that Rockwell Automation offers to help companies attack sustainability opportunities and problems are on full display on the exhibit-hall floor. A short theater presentation by John Nesi, vice president, market development, emphasized that to Rockwell Automation green means lean. "Sustainable production is about your bottom line," Nesi said. "It's not just energy. It's about raw material consumption, worker safety and product safety and life cycle."
During a second presentation, Marcia Walker, market development manager, sustainable production, for Rockwell Automation, emphasized the need to use less energy, use energy at cost-effective times or optimize if you have a choice of energy sources. "It's about cost, brand protection, stability of supply and compliance."
Walker outlined the "seven pillars" of Rockwell Automation's "greenprint," a manufacturing blueprint for energy sustainability, that emphasize:
- monitoring the energy entering the facility;
- production monitoring--a real evaluation of how energy actually is used by various plant segments;
- making energy consumption a bill of material item just like any other consumable;
- production modeling—think about optimizing energy as a process variable;
- active controlling of energy use by considering timing and other use adjustments;
- active response to energy changes using integrated automation and controls that include an energy component;
- scorecarding--know if you're making progress.
In addition, exhibit hall visitors were encouraged to take advantage of a series of self-guided tours that highlight the products and solutions available at several booths as well as non-commercial technical sessions, to confront sustainability opportunities. Rockwell Automation's Angel Sustaeta demonstrated the value of bringing energy issues, such as boiler performance, natural gas availability and cost and permitted emission levels, into your process modeling as key components in the optimization process. "You can evaluate the potential of using a lower-priced fuel supply and how that impacts emissions, along with production demands, and determine the optimum energy choice."
For more immediate impacts, exhibit-hall visitors can check out variable-speed drives for HVAC systems in Rockwell's FanMaster retrofit kit. Substantial energy savings can result.
Hall visitors also can get an overview of the sustainability consulting services that Rockwell Automation provides in a fashion similar to the company's safety consulting initiatives. "We can look not only at the facility energy opportunities, but also look at the production equipment as well," explained Rockwell Automation's Doug Burns. "We categorize savings in three areas: things that are behavioral in nature; things that can be improved with training and awareness; and those that will require capital expenditure." He explained that simple awareness that recharging lift truck batteries overnight instead of at the shift change could take advantage of lower electric rates. Automation Fair visitors will find other such examples to consider.
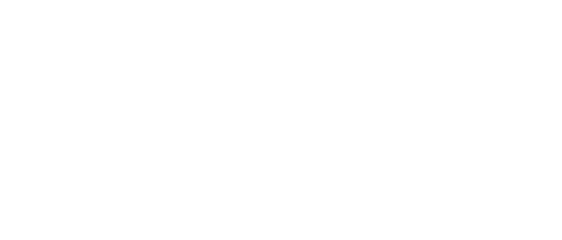
Leaders relevant to this article: