Speed is important in processing sensor/transmitter output signals, but speed alone doesn’t necessarily give you the good signal controller input you need to ensure proper operation. Truly valid measurements are achieved sometimes only when you apply isolation and signal conditioning, but separation and protection are always a good place to start.
“For a plant to work reliably year-in and year-out, the protection of analog and digital signaling through good installation practice is a high priority,” says Alan Balcombe, global product engineering manager at Weidmüller Application Center NAFTA. “Apart from the basics of cable separation, grounding and shielding, the foundations for this protection are in high-quality signal isolation, conversion and surge protection.”
Michael Manning, vice president of engineering, Automation Systems Interconnect, suggests selecting a modular device that’s programmable. “A universal programmable signal conditioning device allows engineers to easily configure the unit to fit most applications. This gives engineers the ability to reduce inventory and cost by standardizing on one part number,” he says.
“Network engineers need to consider the performance goals and failure mode effects of their signal conditioning,” says Don Lupo, sales & marketing director at Acromag. The failure mode effect on the system means asking what happens if the sensor fails or the input/output/power wires break open or short, he explains.
“Is the signal conditioner software configurable, as well as DIP switch configurable with zero/span capabilities?” asks Tracy Lenz, senior product engineer at Wago. “Simplify by finding models that can be configured from multiple sources for multiple signal types.” This eliminates ordering wrong part numbers and minimizes on-hand stock, explains Lenz.
“Physics have not changed galvanic isolation needs, and analog signals are all around us,” says R. Coregsey, system engineer at Lutze. “We have to deal with them now and in the future.”
When relying on accurate analog signals from outdoor applications, such as wastewater plants, think about the possibility of electrical noise and interference that could affect the system, warns Mark Dietzsch, product manager at Turck. “By incorporating signal conditioners that utilize galvanic isolation, which eliminates noise and interference, the chance of disruptions to the control circuits is greatly reduced,” he explains.
Any good design inherently rejects as much noise as possible, declares Helge Hornis, Ph.D., manager, intelligent systems, at Pepperl+Fuchs. “For data networks this is typically accomplished by utilizing symmetrically designed electronics and floating signals, possibly combined with shielding,” he explains.
Signal conditioners have benefited from advances in circuit design technology, says George Tsakir, process and fluid power product manager, AutomationDirect. “They are smaller yet offer advance features such as one-touch calibration based on incoming signals and DIP-switch settable input and output ranges.”
If you’ve had problems on past applications, you probably experienced signal crosstalk, common-mode voltages, DC or AC common-mode rejection or over-range and input protection issues, explains Bill McGovern, national sales manager at Dataforth, who emphasizes all of these nightmares can be eliminated with isolated analog signal conditioners.
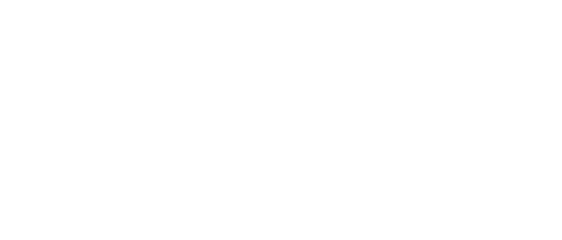
Leaders relevant to this article: