Wireless communications in industrial facilities have moved decisively to become a practical solution. Practicality for industry means saving money without taking undue chances, and wireless has advanced to the point where it delivers concrete benefits with manageable risk.
The most obvious cost savings for wireless are delivered in installation, especially for projects in existing plants. It takes lots of money and time to dig trenches, lay conduit and pull wires. Even for above ground installations, the costs of conduit and wiring are often substantial.[sidebar id="4"]
Savings over and above lower installation costs are realized during operations because of reduced maintenance costs and greater flexibility. Wireless is cheaper to maintain because there no wires or cables that can be damaged. Wire and cable damage can occur through accidents such as lightning strikes, contact with moving in-plant equipment and inadvertent cutting during unrelated construction activities.
Wireless is a natural fit in applications such as robot arms where I/O must be connected to moving parts. Motion Controls Robotics (www.motioncontrolsrobotics.com) provides full-service robotic solutions to customers worldwide from its 57,000 ft2 facility in Fremont, Ohio.
One of its customers is a leading manufacturer and marketer of paper and plastic disposable packaging for the food service industry. This customer needed a robotic system to palletize cases of product.
The system consists of five robots (see Figure 1), each mounted on a 50-foot rail system. At the end of the robotic arm is a tool with eight double-solenoid valves and one photoeye sensor, requiring 16 outputs and one input.
To provide adequate wired I/O, the system would require expensive high-flex cable the length of the rail system along with soldering three separate connection points with approximately 20 wires per connection. Working with Phoenix Contact (www.phoenixcon.com), Motion Controls Robotics found a solution that instead uses Bluetooth wireless.
The PLC that controls the overall system connects via EtherNet/IP cable to a bus coupler. The coupler connects to five Bluetooth wireless I/O base stations located nearby. Each of the base stations then connects wirelessly to two Bluetooth wireless I/O devices mounted on each of the robotic arms, located 80 to 120 ft away from the base stations. Each of the I/O devices has eight inputs and eight outputs.
The bus coupler, the five base stations and the 10 Bluetooth-enabled I/O modules all are housed in IP65/IP67 blocks for direct machine mounting. Because Bluetooth operates in the 2.4 GHz license-free spectrum, it is resistant to most common plant-floor electrical noise and interference.
Unlike Wi-Fi, which also uses the 2.4 GHz spectrum, Bluetooth uses the frequency-hopping method of spread-spectrum wireless. Frequency hopping results in higher energy per bit, and thus punches through any noise floor that might be present. These hops occur 1,600 times per second, so when a packet is lost to interference, the next transmission is sent 625 μsec later.
Eric Hohman, PLC programming and systems design engineer for Motion Controls Robotics, says that wireless I/O eliminated about 20 hours of wiring and soldering per robot.
J.P. Yeager, electrical designed for Motion Controls Robotics, says that wireless cuts downtime. "Wireless eliminated the need for two separate cables in two different areas that are continually flexing," observes Yeager. "The lifespan of these types of cables can be from several months to several years, but eventually those cables will fail and require time consuming replacement."
Normal wear and tear of wire and cables is most prevalent with connected components that move such as those mounted on cranes, material handling equipment and robot arms. Wiring and cabling to both moving and stationary components also can suffer wear and tear through corrosion, insulation breakdown and degradation due to temperature changes.Another key advantage of wireless is flexibility. Once a wireless network is installed, the cost of adding another device is very low. Need an extra I/O point 2,000 ft from the control room? No problem with wireless, but very expensive with a wired system.
Wireless saves costs during installation and throughout the operational life of the control and monitoring system, but these savings are accompanied by the risk of implementing what for many is a new technology. Many users get around these risks by limiting the scope of the wireless system in terms of bandwidth, criticality and other parameters.
Cheaper to Install
In most instances, it is cheaper to install a wireless system than its wired counterpart. "We were hired by a major steel producer in the Midwest U.S. to replace the DCS controls on four large boilers that supplied steam to its steel making process," says Timothy Stout, PE, manager process systems for system integrator Matrix Technologies (www.matrixti.com) in Maumee, Ohio. "Wireless saved money because it replaced very long conduit and cable runs of up to 2 miles. This saved miles of conduit and wire which equates to several hundred thousand dollars in installation costs."
Another long-distance application that resulted in substantial savings is detailed by Michel Dubé, automation coordinator at the Montreal facility of Para-Chem (www.parachem.com), a manufacturer of coating, emulsion polymers and adhesives. "We implemented remote monitoring with security cameras via a Wi-Fi wireless system. The monitored site is 1.2 km away from our security office, so we saved an estimated $200,000 Canadian on fiberoptic cables and installation," relates Dubé.
Wireless also can save money on a smaller scale. "We have used wireless to connect portable and stationary label printers," notes Harry Pettit, manager of systems and infrastructure engineering at Pepperidge Farm (www.pepperidgefarm.com), headquartered in Norwalk, Conn..
"Wireless provides flexibility in equipment location that you don't get with hardwired, and we also estimate installation savings at $1,500 per printer," adds Pettit.
Wireless not only saves money on installation labor, it also can cut design costs. "With wireless, engineers don't need to sort through rolls of schematic diagrams, installation and termination details, and the drawings for the fabrication and layout of the cable tray, conduit, junction boxes and interface panels," observes Joe Bingham, president and CEO of system integrator AES Global (www.aesglobal.com), Anaheim, Calif.
[pullquote]Installation savings for wireless compared with wired are often obvious, especially where long distances must be spanned. But in many instances, operational savings due to wireless are just as important.
Cheaper to Operate
Gestamp Automoción (www.gestamp.com) is a Tier 1 Spanish-based automotive supplier with 56 production centers in 17 countries. Its facility in McCalla, Ala., implemented a wireless Ethernet link from ProSoft Technology to connect a ControlLogix programmable automation controller to I/O for a press-stamping application.
"Since going to the wireless system almost three years ago, we have replaced only one bolster cable, whereas in the past we would have to replace one every other month," says Mike Mullins, press maintenance team leader at Gestamp.
Wireless allowed Gestamp to reduce downtime associated with cable failure and replacement, translating to savings of up to $174,000 per year plus the value of parts produced during that time, says Kevin Zamzow, ProSoft Technology's (www.prosoft-technology.com) strategic product manager for wireless technologies.
Wireless technology also can help manufacturers reduce the skill set required for maintenance tasks. "Most maintenance issues are mechanical problems," observes Cliff Whitehead, manager of strategic applications at Rockwell Automation (www.rockwellautomation.com).
The central wastewater treatment plant of Lapuan Jätevesi Oy, a Finish company located in Lapua, Finland, treats household and industrial wastewater (see Figure 2). The original automation system from 1992 was replaced in 2008 with new controllers, SCADA software and a wireless communication network.
The control system upgrade was performed in collaboration with Schneider Electric and system integrator Seinäjoen Teollisuussähkö Ky. In the new automation system, six Modicon Premium controllers communicate over wireless links using Modbus TCP/IP communicated through 9 ProSoft Technology RadioLinx industrial Ethernet radios.
About 2,000 process variables are transmitted over the wireless network, and the network also is used for programming and maintenance purposes. A number of locations had to be linked as the control system has six controllers located in different buildings along with two control rooms.
From the user point of view, the main advantage of was the cost and time savings for the installation as there was no need to dig trenches or modify existing cable paths.
From the integrator point of view, Seinäjoen says the wireless RadioLinx network was "the easiest part of the implementation. We didn't have any problems as these radios are very easy to configure and mounting recommendations given by ProSoft Technology were very clear. Schneider Electric made some tests in their offices and then explained to us how to implement the wireless network in the field."
Local Schneider reps had no wireless experience, but still found the technology straightforward in implementation. "When we started the project, we didn't have any local specific RF expertise," explains Jouni Aarnu, application sales and key account manager for wood and bioenergy at Schneider Electric Finland. "We provided ProSoft with the basic layout of the network. They made some calculations provided us with the recommended lists of accessories for each radio location including cables, antenna and lightning protectors. They also provided guidance for field mounting and implementation."
"Rather than alerting a highly-skilled, high-cost controls engineer for every fault, manufacturers can alert locally based mechanical technicians. These mechanical technicians are better- equipped to solve the majority of problems, but sometimes need the support of controls engineers. To accomplish this, manufacturers can make a wireless cellular modem part of the mechanical toolbox to create a connection that is locally manned by mechanical technicians and remotely manned by centralized controls engineers," explains Whitehead.Wired systems not only experience wiring and cable failures, but also other problems linked to hard-wiring. "Wired instrumentation tends to get damaged through power spikes in the system that can burn out analog input channels. These defects are difficult to troubleshoot, but burnt analog input channels are a thing of the past with wireless instruments, and the loss of the instrument is easily detected through the loss of communications," observes Bingham.
Not only does wireless save money during on-going operations, it also can be safer. "Wireless improves safety by simplifying monitoring, modification and upgrades," says Robert Konermann, product marketing manager for automation & safety at Schneider Electric (www.schneider-electric.us). "This can be significant with electrical panels containing high-voltage equipment, particularly when water or other hazardous conditions are present. Because of the wireless network, workers don't need to be in physical contact with the panel or open the panel doors to expose the wiring, components or live equipment."
Long-term savings also are abundant due to the flexibility of wireless ,which makes it easy to add, replace or modify components, adds Konermann.
What's Holding Wireless Back?
Wireless works in the right application but, like any technology, it has limitations. "Wireless has its place when you can get by with gaps of missing data or when you have difficulties in getting wiring to sensors or I/O," says Gary Crenshaw, electrical engineer at Beam Global Spirits and Wine (www.beamglobal.com) in Clermont, Ky. "But I don't see wireless replacing all control system hard-wiring. Cell phones are some of the best wireless devices we have, but they are not 100% reliable. They are dependable enough to be very useful, but they can't be counted on in an emergency."
Some of the reliability issues raised by Crenshaw are being addressed by newer wireless technologies. "Features available in industrial wireless products now include Orthogonal Frequency Division Multiplexing, a technique that distributes data over multiple carriers assigned to individual frequencies to reduce distortion and interference," notes ProSoft's Zamzow. "Internet Group Management Protocol querying permits wireless multicast packet filtering, which limits unnecessary re-broadcasting of data that can crowd the network."
Table 1: Wireless Advantages1. Cheaper installation
|
Table 2: Wireless Challenges & Issues1. Slow data transmission rates
|
Wireless Wells "The sensors and instrumentation are several hundred feet away from the area where the information is needed. In addition to this the drilling rig moves about every 45 days. Without wireless it would be necessary to dig a trench, bury a conduit to run a communication cable, pull and terminate the communication cable and hope that nobody compromises the cable during the drilling process. With wireless, the only thing necessary is to set it up and turn it on, and installation takes less than a man-hour." With wired installation you have to disconnect, pull wire, remove the conduit and remediate the trench. It was obvious in this case that the wireless solution is very cost effective and less intrusive, notes Hilpert. The two RF modems installed at the oil rig and at the system computer have some limitations. "The transfer rate is low compared to a wire or fiber optic system, but data exchange requirements are low," observes Hilpert. "When radio-operated explosives are lowered into the well bore, no wireless devices can be energized, but most of the rig is shut down during these periods anyway." Hilpert says the savings are significant. "The wireless link costs less than $1,000, says Hilpert. "The Digi 900 MHz modems are about $300 each and are essentially plug and play. Compare this to hard wiring where, at best, it's going to take two men at least a day. Also, the risk of delays and additional costs are much greater with hard wiring." |
Then, There's Those Standards
The lack of standards for wireless has delayed implementation in many instances, but this situation is improving. "Wireless standards such as IEEE 802.11 will contribute to user confidence because its spread-spectrum modulation techniques are less susceptible to interference," argues Bingham. "The ISA 100 wireless standard helps make wireless technology implementation easy due to wide acceptance in the instrumentation and automation industries."
Vendors and industry organizations are jumping on the standards bandwagon. "At one time, we expected to create a Profibus process wireless standard," comments Carl Henning, the deputy director for Profibus and Profinet in North America (www.us.profibus.com).
"But with the release of WirelessHART, we realized that was no longer necessary. Instead we formed a cooperative team with Fieldbus Foundation and the HART Communication Foundation to simplify access to WirelessHART from our respective technologies," adds Henning.
Integrating Wireless“We have implemented wireless in a variety of applications and industries,” says Joe Bingham, the president and CEO of system integrator AES Global (www.aesglobal.com) in Anaheim, Calif.For a municipal water distribution SCADA system, AES replaced a PSTN phone line with a 900 MHz wireless network. “As PSTN is a slow connection and relies on a third party network, it was not a reliable and cost effective system for our client. We performed both a virtual and an on-site wireless survey, and concluded that the 900 MHz wireless radio system was the best solution,” explains Bingham.“The cost of the wireless system was equivalent to two years of rent payments for the PSTN. The city now has a more reliable system that provides real-time updating and less downtime. The true advantage of the wireless system came after two years of installation, when the city built a new five million gallon reservoir and considered it necessary to integrate the new site into the existing SCADA wireless network. Due to the scalability of the wireless network, the job was done in a one day,” adds Bingham.AES also installed a wireless system for a ten-acre oil tank farm. From past experience, AES knew that such projects are costly, time consuming and labor intensive. “Running conduits, junction boxes and copper wires throughout an entire tank farm - and maintaining or upgrading the system after installation, are nightmares,” notes Bingham.A fill-check sensor embedded with a wireless transmitter was installed on each tank, and the master receiver was installed in the operator house. “Installing and configuring the entire wireless sensor network took less than sixty percent of the time that it would have taken to accomplish the same solution using copper wire; and it cost thirty percent less than a copper wire solution,” relates Bingham.“Besides saving time and money during installation and configuration, it was also easier to architect and manage the wireless system. Years after installation, we found that the wireless sensor network was easier to troubleshoot and maintain. The flexibility and scalability of the system were also immense advantages,” adds Bingham.For another municipal water distribution system, AES used wireless instruments to monitor tank levels. This was a cost efficient solution as the city saved money because they didn’t have to run conduit and wire from the tanks to the control panel. The controllers instead acquire tank levels from the instrument over a wireless network, and then use this data to control the pumps.The controllers shared tank level information over a wireless network using radios instead of communication cables. “This simple setup saved the city thousands of dollars in conduit, wire and electrical labor expenses. The flexibility of this system came into use when the city decided to replace their tanks with new ones,” concludes Bingham. |
Standards already promote use in some applications. "ISA 100 compliance was a key factor in selecting Honeywell for our project," comments Dubé. "The standard will allow us to add wireless devices from many different suppliers in the future, and these additions will show much higher payback because the wireless infrastructure is already in place."
Advances in technology and widespread adoption of standards promise to reduce cost, increase reliability and improve performance of industrial wireless systems. This should promote more widespread use in industrial applications worldwide.
Wireless Crane Control
|
Figure 3: Because the manufacturing plants span such a wide area, airplane assembly is an ideal application for wireless.
Source: Rockwell
Mobile Wireless
When control components must be mounted on mobile platforms, wireless often is the best solution. A major steel manufacturer in Canada uses PLCs mounted on mobile production machines in their coke plant. The ControlLogix PLCs communicate via wireless Ethernet to Rockwell Automation RSView-powered HMIs located in the control room.
According to a plant engineer, the greater part of wireless communications is data collection as the machines are essentially autonomous units that don’t need communications to the control room HMIs to operate. The 2.4G Ethernet radios have static IP addresses and reside behind a firewall.
The plant engineer says that Weidmuller's (www.weidmuller.com) 2.4G radio solution was the most economical they could find. He also notes that Weidmuller's people came in free of charge to assist with equipment and antenna selection.
The ability to collect timely data has been the biggest benefit. The data is used to monitor and adjust process parameters for optimum operational performance. Equipment parameters are also monitored for maintenance purposes.
The biggest challenge has been to find safe locations for antennas, and still be able to transmit and receive in a situation that is not line-of-sight. In one instance, the plant had a fully operational system until another project put up a steel wall in the way of the transmissions. Weidmuller worked with plant personnel to find a location for a relay unit that gave them another route for the signals.
The plant remains reluctant to use wireless Ethernet for control, with dropped data the biggest concern. As wireless systems become faster and more dependable, the plant anticipates more acceptance and more widespread use.
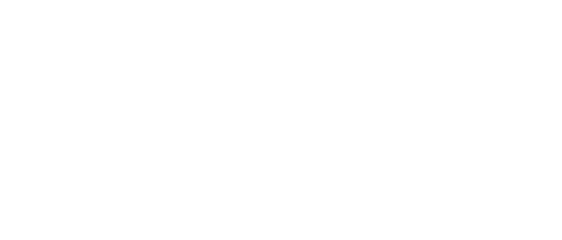
Leaders relevant to this article: