Software Replaces Machine Hardware, but Mechanical Solutions Still Have Their Places
The futuristic technology of the Star Trek macrocosm always has been centuries ahead of its time, both literally and figuratively.
"Gene Roddenberry had real buttons all over the place in the original 'Star Trek' series," notes T.J. McDermott, senior project engineer at Formost Fuji (www.formostfuji.com) in Woodinville, Wash. "Seventy-five years after that, they were replaced by touchscreens in 'Star Trek: The Next Generation.' In reality, software controls on touchscreens arrived centuries before Gene envisioned it."
Software continues to replace machine hardware for a variety of reasons, but some machine builders offer words of caution.
"Theoretically, the only real control necessary is an e-stop button," continues McDermott. "The rest can be touchscreen buttons. That said, there are instances where mechanical coupling of a system is better than electronic gearing; a mechanically coupled system can never be out-of-time under normal operating conditions."
Camco-Ferguson indexing drives used to be an important component of Formost Fuji's machines, explains McDermott. "They can be replaced by a servo drive and motor, along with software to create an equivalent cam profile," he says. "The servo drive and software solution allows for infinite flexibility over the mechanical drive; changing the cam profile table is easy, compared to changing out the indexing drive. Given a choice, I would much rather create a cam profile via software; if I want to fine-tune the motion profile—a polite way of saying I want to correct a mistake—changing numbers stored in RAM is easy. Cutting a new cam plate is a rather expensive way of creating a new profile."
Temperature controls now get integrated into the logic processor instead of being external devices, adds McDermott. "The on/off switches, dials and indicators now reside completely inside the logic processor and the display screen," he explains. "Again, given a choice, I'd rather have the software-driven temperature controls. When they're not needed, they're off-screen and out of the way."
However, software does not lend itself to intuitive troubleshooting, notes McDermott. "With a mechanical system, it's relatively easy to track the various chains, cams and gears to see how the motion is generated," he says. "With a software-generated cam profile, the education level of the troubleshooter must be much higher. The trade-off thus is flexibility vs. the skill level of the maintenance staff."
Nick Shea, project engineer at DMC (www.dmcinfo.com), Chicago, has worked with safety PLCs on several projects and seen some direct advantages of replacing hardware such as a safety relay with a safety program in the safety PLC. "Some benefits of going this direction are wiring advantages, flexibility and configuration," he explains. "By wiring only to a PLC, you get both safety functionality and monitoring and diagnostics. Plus, you have a single pair of contacts as PLC inputs, rather than wiring to both an input card and safety relay. It also simplifies wiring for construction and future wiring for troubleshooting."
Software also is more flexible, explains Shea. "Safety logic and conditions can usually be quickly modified programmatically without physical modifications to system," he says. "And custom variations to safety logic that are impossible or limited with hardware alternatives are possible in software. Also, machine guarding or manufacturing-line e-stop zoning can be done in software, rather than multiple safety relays. Safety zones also can be dynamically modified based on machine operating status. And intelligent devices such as laser scanners and light curtains usually are made to integrate smoothly into the software development environment of a safety PLC."
Rapid Conductor, a hot plate welder designed and built by Extol (www.extolinc.com) in Zeeland, Mich., is a good example of replacing mechanical systems' controls with electronic control, says Rob Bouws, product development engineer at Extol. "Traditional hot plate welding uses hydraulic cylinders with mechanical stops on the fixture and heated tooling," he explains. "Adjustment of melt depth and seal depth is time-consuming and difficult on these machines because shims need to be inserted under the hard stops in order to tune in the process."
Extol's Rapid Conductor uses coordinated servo control instead of cylinders. "The user can adjust melt and seal depth just by changing parameters on the HMI," says Bouws. "The machine is also much faster because the motors can move quickly with controlled accel/decel and it doesn't open farther than necessary to remove the heated tool. Servo motors also offer control features previously not possible on traditional hot plate welders. The speed at which parts contact and pull away from the heated tools can be controlled. Both parts can be loaded in the lower fixture, and the upper fixture can come down and pick up the upper part half before welding."
Pete Mansfield, engineering fellow hardware systems at Kiva Systems (www.kivasystems.com) in Woburn, Mass., recalls around the early '90s when multi-axis controller card vendors were starting to come out with packaged features with names related to "cam" or "gear," implying one could replace the mechanical linkages between different shafts with independent, though software-linked, direct drive control.
"The obvious benefit is you don't have to commit to one specific drive ratio or cam profile between axes, for example, but on the flip side, if you only have one drive ratio you care about, then the hardware solution would likely still be more cost-effective," he says. "My general approach to new machine design is to look for the mechanical linkage solution first. But there certainly are areas where independent control is needed to perform coordinated movements."
In Kiva's robotic drive units, to move forward, both drive wheels are rotated in the same direction, explains Mansfield. "One might think only a single motor is needed for this, with the wheels fixed to rotate at the same speed," he says. "But in reality, we also have to stay on course. We need to adapt to the real system conditions where drive wheels are not exactly the same size, floor surfaces are not perfect and can result in an occasional wheel slip and other random events that conspire to throw the drive unit off course. So we use one motor for each drive wheel with independent controllers and where one wheel or the other can adapt its speed slightly to compensate for the disturbances."
Lee Hilpert, president of HilTech (www.hiltecheng.com) in Tomball, Texas, says his company manufactures a positive displacement centrifuge feed system. "Because it's positive displacement, the pump rate is directly related to pump RPM," he explains. "Therefore the pump RPM must be adjustable so that the process rate can be optimized for the application or fluid properties. There are two ways to accomplish this. The most widely used in our industry is a mechanical variable speed drives where the mechanical ratio is manipulated through a series of cones and rings or adjustable sheaves. The other option is to replace the mechanical variable speed drive with a variable frequency drive."
HilTech offers both, but the industry has been slow to accept stand-alone VFDs due to the harsh conditions and classified area requirements, says Hilpert. "Until recently the only VFD-driven pumps sold were associated with fully VFD-driven centrifuge systems where the controls are remotely located in a safe area and handled with special care," he says. "However, we just recently sold two stand-alone VFD-driven centrifuge feed pump systems where the only function of the VFD was to replace the variable mechanical drives."
The VFD provides a much wider range of operation and additional functionality, such as automatic pressure control and the ability to safely reverse the flow to drain back hoses, explains Hilpert. "All of the variability and functionality is a result of the software running in the VFD," he says. "In addition, it provides for a much more compact system and cost about 10% less. The downside to the VFD replacement is reliability in the harsh operating environment. To address that issue we developed a fully isolated NEMA 7 enclosure with external cooling that protects the VFD from vibration and the environment. Only time will tell if we have done a good job of protecting the VFD."
Jeff Hanna, manager of control product development at Intelligrated (www.intelligrated.com), Mason, Ohio, hasn't seen much replacement of hardware with software. "We are certainly among those that can replace hardware with an HMI in some cases," he says. "Even in those cases, many customers end up with both as a matter of convenience. New hardware, part of technology evolution, will make new combinations possible. We replaced some typical servo applications with high-end VFDs due to the speed of software, the performance of the drives and the availability of appropriate networks."
The evolution from centralized I/O in big cabinets has been slowly but surely changed to more networked approaches, he adds. "PC- or server-based software can replace PLCs, but this is changing, not eliminating, hardware," says Hanna.
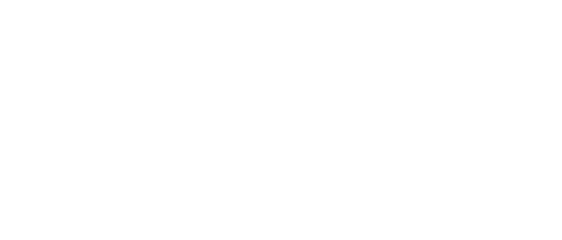
Leaders relevant to this article: