By Philip Burgert
Sensing and measuring based on laser technology that offers tightly focused measuring-spot ranges and flexible mounting-distance options are finding their places in a wide range of applications that need very accurate alternatives to 3D vision.
Very-high-speed measurements with high resolution and repeatability are possible with lasers sensors. Other advantages include an ability to “reach” into difficult-to-access locations to provide precise metrology.
On the Spot
“A small spot size is really the only practical way to measure certain components or to measure an inside dimension, because lasers are used mainly for dimensional measurement; camera sensors, on the other hand, are used to determine the presence or absence of a part,” says David Lacey, president of system integrator Oryx Systems, Indian Trail, N.C. (www.oryxsystems.com). “When you get to actual metrology, that’s when the lasers really show off their strength.” Oryx builds custom and special-purpose measurement machines.
Lacey says, compared with proximity sensors, a key advantage of laser sensors is their stand-off distance. “They don’t have to be very close to the thing being measured,” he says. “They also have a good measurement range. Unlike cameras, of course, laser sensors don’t need special lighting. They can work in dark and shadows.”
Lacey notes that lasers sensors come in a variety of configurations. “Almost as many types as proximity switches,” he says. “They rival proximity because of the non-contact nature and the stand-off distance. But their greatest advantage is in doing high-accuracy, high-resolution measurements in non-contact mode looking for dimensions.”
Topography is area where lasers excel, says Lacey. “Vision systems can sense height but not as accurately as lasers can.” The non-contact nature of laser sensors is also an advantage for measuring parts that could easily be damaged, he notes. “To measure soft parts, for example, solder paste or metals such as lithium, you can’t touch the stuff with anything,” says Lacey. “The only way to do dimensional measurement is with a non-contact gauge and in most cases the lasers are more suitable than other types.”
Mind the Details
Lasers can be difficult to use on a highly polished surface. In those cases a capacitive sensor that is less dependent on surface textures is a better solution, says Lacey. “But the capacitive sensor will measure even the smallest oil spot as well, whereas the laser doesn’t. There’s always a compromise.”
The spot size of the laser also sometimes works against it. With a really tiny spot size in the one-half micron range, it can pick up small, inconsequential deviations in the surface, which create problems. A larger area sensor tends to average and provide a smoother signal, says Lacey.
“With the correct application, the laser sensor can outperform these other devices for accuracy, repeatability and access to a small area,” he says. “But you still have to do the right signal processing and averaging to get data from the signals to process it properly. You simply can’t aim the laser and get a reading.”
Of the many laser-based applications that system integrator Vista Solutions (www.vistasolutions.ca), Windsor, Ontario, has developed, about 90% use laser sensors such as a displacement sensor for precise and accurate sensing results, says Aaron Bouchard, vision specialist. “We tend to always use the smallest laser point that you can get,” he says. “That would be the main advantage.”
Along with other machine-vision systems, Vista Solutions uses displacement laser sensors in determining the 3D position of objects in manufacturing systems. “We do a lot of 2D robot guidance and we’ll sometimes need a third dimension,” says Bouchard. “Rather than use a full-blown 3D pickup system with a lot of development costs, for the right application you can use a 2D camera and two or three displacement sensors to get the plane of the part so you’ll know where it is in space and you can adjust your robot to pick it up. It’s really a complementary technology that can be much less expensive.”
Vista Solutions also uses laser presence sensors for critical timing in applications that look for a part moving on a manufacturing line. The laser sensor provides much greater accuracy because, as the part passes, it only has to break the small laser dot rather than a larger photo-eye surface, says Bouchard. He notes that the cost of laser sensing might be a little higher than some other solutions, so depending on the applications an inductive sensor or photo-eye might be a preferable way to achieve presence detection or other results.
Lasers also can be best to detect, for example, the presence of a rubber seal on a black part when there’s poor contrast between the two pieces, says Bouchard. “You throw a laser line across it and you actually can see it with just a standard 2D camera,” he says. “You’re not doing any measurement calculations based on an algorithm. You’re just checking to make sure it is present based on a laser line skipping up rather than running straight across.”
Rick Bondy, product manager for Sick (www.sickusa.com), says that in the past most photoelectric sensors used infrared light sources and the wavelength was not visible to the human eye. “It made alignment very difficult and trial by error in most applications,” he says. “With visible-red-light-emitting-diode sources, installation and setup improved significantly, since the installer could see the light hitting the target.”
The problem with both of these light sources was the control over the physical size of the light spot at varying distances, he adds. Similar to the light from a flashlight tending to flair out as it exits the housing of the flashlight, the optical-light-beam diameter of a photoelectric sensor also gets larger further from the lens.
Controlling the size of the light spot size is especially critical in manufacturing applications that call for smaller machine footprints on the factory floor, in which targets are getting smaller, says Bondy.
Laser Specs
Laser light sources enable factory automation applications that require precise, pin-point light-spot sizes to be developed reliably and at competitive cost, states Bondy. “Most lasers used today in factory automation are Class I or Class II lasers, as regulated by government agencies, and are considered safe due to their extremely low average power output,” he says.
Typical applications include product height/width, diameter, thickness, roundness, eccentricity, and profiling, notes Bob Hosler, regional product sales director for Keyence of America (www.sensorcentral.com), adding that the laser technology that has become very popular recently is two-dimensional, laser-displacement sensing. This technology essentially combines laser distance measurement (triangulation) with vision technology involving either two-dimensional charge-coupled device (CCD)or complementary metal–oxide semiconductor (CMOS) receiving elements to create a displacement profile of the target and enabling stable defect inspection or gauging without problems frequently associated with machine vision, such as inconsistent lighting and part variation, explains Hosler.
In packaging applications, lasers can be used to count a magazine of unfolded corrugated cardboard cases or cartons or to verify if minor and major flaps are fully inserted, says Jeff Allison, product manager for Pepperl+Fuchs (www.pepperl-fuchs.com). He notes that material-handling applications often employ laser displacement sensing for absolute positioning of automated storage and retrieval or printing applications can use laser sensors to count individual sheets of paper in a sheet-fed press.
Philip Burgert is a freelance writer, specializing in technical trade media.
Sensing Resources
North American Sensor Catalog and Selection Guide is nearly 900 pages of capacitive, inductive, weld immune, special application, NAMUR, ultrasonic and photoelectric sensors. It also includes amplifiers, counters, timers and controls, as well as cordsets and accessories. A selection guide aids in choosing the proper sensor for a given application. A copy of the catalog can be requested at www.am.pepperl-fuchs.com/literature/literature.jsp?source=FA. Pepperl+Fuchs330/486-0001
SENSORS WORKING OVERTIME
Sensors catalog features many unique and specialty products, as well as selection guides. New to the catalog is a line of harsh-duty sensors for extreme temperatures, washdown environments and mobile equipment applications. Many new specialty products have also been included in this issue, including inclinometer sensors for angular tilt detection, extended range uprox+ sensors, an expanded stainless steel sensor line and magnetic analog and cylinder sensors.
Turck
763/553-7300
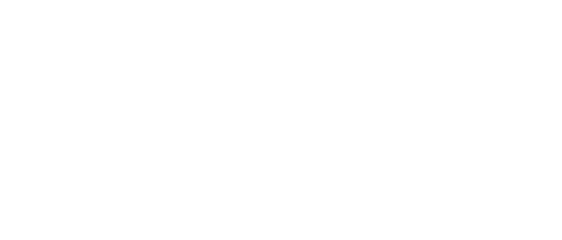
Leaders relevant to this article: