By Jim Montague, Executive Editor
Aside from the Rocky Mountains, the North American West used to be mostly uncrowded. In fact, Wyoming once competed with Alaska for least populous U.S. state. Well, times and demographics have changed. While most of the westward population shift in recent years has gone to Arizona and Nevada, more than a few folks also have migrated to states like Montana and Wyoming.
As usual, this influx of people and families has meant more houses and steadily growing communities requiring basic necessities such as water, natural gas, public services and especially electricity.
As a result, two Black Hills subsidiaries, Black Hills Power and Cheyenne Light, Fuel and Power, spent the past couple of years adding two new power plants to two existing plants at their 320-acre energy complex in Gillette Wyo. Black Hills Power (BHP) has 69,000 electricity customers in South Dakota, Wyoming and Montana, and Cheyenne Light has 39,800 electricity customers and 33,300 natural gas customers in Wyoming. Black Hills also owns and operates a coal-mining division, Wyodak Resources Development, which fuels the power plants and is the oldest continuously operated, open-pit coal mining operation in the U.S. BHP and Cheyenne Light are divisions of parent Black Hills, which has a total generating capacity of 1,000 MW.
Progressive Improvement
On the surface, the three Wygen plants appear to be copies of the utilityās initial Neil Simpson II facility. However, because they were designed and built in succession, the developers naturally sought to make each one more efficient to operate, while also decreasing the environmental footprint of each, and minimizing equipment and construction cost increases due to economic changes over the 15 years these plants were built.
To help it achieve the same power-generating capacity as the other plants at less cost, BHP asked its engineers and contractors to come up with innovative ideas for the new Wygen III 110-MW, coal-fired power plant (Figure 1) now under construction at the complex. One of the most significant changes is Wygen IIIās far greater use of fiberoptic lines for its network communications. This not only saves on materials, but also will generate other long-term savings for the utility.
Figure 1: POWER SOURCE
The 110-MW Wygen III power plant arises on the prairie at Black Hills Powerās 320-acre energy complex in Gillette, Wyo.Ā
BLACK HILLS POWER
BHP broke ground for Wygen III a year ago, and the plant is now 60% finished. The plant is scheduled to begin serving customers in June 2010.
āComparing Wygen III to the other plants is like comparing todayās Cadillac to one from 1994,ā says Shawn Lesmeister, Wygen IIIās assistant project director. āIt has a lot of technical upgrades to its controls, combustion, emissions and environmental technologies, includingĀ a new distributed control system.ā
BHPās other three plants have DCSs from ABB; however, Wygen III is the first place ABB will integrate all ABB electrical equipment and controls, including motor control centers (MCCs), secondary unit substations (SUSs) and medium-voltage switchgear, at one of the plants.
Fiberoptics is orders of magnitude less costly and labor-intensive to install and will be far less expensive to maintain and troubleshoot.
āThis will help all the controls play better together, make operations easier and allow us to secure data that took more work to get before,ā adds Lesmeister. āFor example, common technology will make it much simpler for our protective relays, current meters, limits switches and other protective devices to pass data and trips through to the control system.ā However, 15-20 other unit protection relays, turbine relays and other protective devices will still remain hardwired from their original devices to the plantās unit trip coils.
ABBās Power Systems division reports itās also been working with mechanical engineering contractor Black & Veatch and civil engineering contractor Kuljian on the new plant. Other ABB iICE solutions for Wygen III include protection systems, isolated and non-segregated phase buses, generator circuit breaker, medium-voltage switchgear and MCCs, low-voltage switchgear and transformers, low-voltage MCCs, instrumentation and an ac/dc system.
First, Play Tag
To implement Wygen IIIās fiberoptic network, BHP first identified about 4,000 I/O tags in its DCS tag database, including 3,200 coming from hundreds of remote relays, meters and switches. Signals and information from these tags travel via hardwire to 10-15 remote I/O (RIO) cabinets and then on to the ABB 800xA DCS. Traditionally, cabinet-to-DCS communications at the Wygen plants also were hardwired, which meant thousands more wires going back to centralized controls. This is where the project employs fiberoptics. āThese lines carry the plantās heartbeat, so we need to monitor it just like an electrocardiogram,ā says Lesmeister. āHowever, using fiberoptics instead of hardwiring is orders of magnitude less costly and labor-intensive to install and also will be far less expensive to maintain and troubleshoot. Overall economics mean itās more important than ever for us to ensure weāre operating as cost-efficiently as possible.ā
Kevin deRee, project manager at ABB Power Systems, reports that along with using fiberoptics, BHP integrated many of its I/O cards directly into Wygen IIIās electrical devices or located them in the field (Figure 2). This is expected to eliminate more than 54,000 ft. of hardwired control cable that BHP would have had to use if it hadnāt employed fiberoptics. This reduced tray, conduit and labor costs, and it saved installation time. āUsing fiberoptics and moving DCS I/O points to the field is pretty innovative for the power industry,ā says deRee. āHowever, BHP was previously facing some limits with relying primarily on hardwiring and sought another solution.ā
Figure 2: Electrical Engineering Capabilities, Black Hills Proposed Remote I/O
To integrate fiberoptic communications into its under-construction Wygen III power plant, Black Hills Power and its contractors integrate control I/O cards into the plantās equipment. This allows BHP to run fiberoptic communication cables to its DCS, instead of installing a wire for each signal it needs.
BLACK HILLS POWER
On most of the fiberoptic lines at Wygen III, BHP and its contractors installed 12 pairs of armored fiber cable to provide ample backup to the two pairs required for functioning. The plantās network uses Profibus communication protocol. āNot only is the fiber robust and easier to terminate now, but the copper-to-fiber media converters function better and are less costly now,ā says deRee.Ā
Ā āWygen III was supposed to be a copy of Wygen II,ā he adds. āHowever, we all sat down together and found we could relocate some MCCs and rearrange electrical loads to be closer to the end devices and this saved cable, too.ā ABB also helped redesign Wygen IIIās grounding system, improved its layout and reduced its cost compared to the earlier plants.
It also recommended running underground cables through duct banks at the plant. The underground cable runs now could be housed in a more robust but less costly material than standard galvanized-steel tubing.
Fiber Is Robust
Lesmeister says traditional criticisms that fiberoptic cables are too delicate, prone to breaks and hard to terminate didnāt phase BHP because it used fiberoptics on a limited basis for a single motor control center running the air quality control system (AQCS) at Wygen I, which started up in mid-2003, and at Wygen II, which started in January 2008. āWe ran fiber from the I/O points in the AQCS as a test,ā he explains. āWe were a little leery early on because we hadnāt done it before, but we just pulled several additional pairs of fiber. That way, if the one we terminated broke, then we could just move to and terminate another. Due to the low cost of the added fiber, this was easy to justify. However, we terminated those lines once, and we havenāt had to rewire any of them since. I think fiber still has a few drawbacks, but itās well worth it. Fiber is a lot more robust than many people believe. You just have to look at your whole application and pick the right routingāone thatās less risky and less likely to be damaged. Our experience with fiber gave us the confidence to take a much bigger step into it at Wygen III.ā
Lesmeister adds that BHP also had some early help learning about, experimenting with and finally adopting fiberoptics from Black Hills Fiber Communications, a former division of BH, whose staff still helps BHP when needed. āThey taught us, did splices, performed testing and fixed pairs when we lost them,ā he says. āOur fiber may be used for data communications and controls, but itās still the same physical cable as on any phone or TV system, which means we can call in help when we need it, and so can anyone else who uses it.ā
Engineering Innovations = Savings at Wygen IIIInstead of copying prior electrical designs used in its first two Wygen power plants, Black Hills Power encouraged āfresh engineeringā and innovations that led to cost savings at the Wygen III plant thatās now under construction.
|
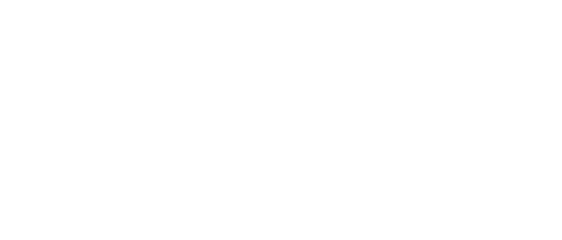
Leaders relevant to this article: