Industrial Ethernet is the unquestioned digital network leader in manufacturing, but alternative networks continue to thrive in its shadow. Industrial Ethernet, heretofore referred to as just Ethernet, has overcome many limitations in recent years, but barriers to widespread application in some manufacturing applications remain.
One of the most obvious barriers is an installed base of non-compatible automation hardware.
The Other Players
“We will continue to use ControlNet, DeviceNet and DH+/RIO for connectivity to legacy equipment that is installed all over our plant,” says Dave Jones, automation engineer/IT administrator at Ash Grove Cement in Leamington, Utah.
“Ethernet might eventually supplant these other networks, but I still see others in our position. Just look at how long the DCS has hung around. Ethernet adoption still is hindered by the fact that the process control world doesn’t move nearly as fast as the IT world—thank goodness.”
ADCO Manufacturing in Sanger, Calif., makes packaging, cartoning and box-making equipment (Figure 1). In addition to Ethernet they use DeviceNet, Data Highway+ and, infrequently, ControlNet. “Besides being deterministic, these non-Ethernet networks provide backward compatibility with many other devices and integrate into our mostly PLC control structure more easily,” notes Kevin Gilpin, electrical engineering manager at ADCO.
Figure 1: This ADCO Manufacturing Intermittent Auto Loader collates and loads ice cream sandwiches into a carton. Its Ethernet network links the PLC, the touch screen and the VFD.
Source: ADCO MANUFACTURING
One reason for the large market share of non-Ethernet networks is that customers have machines that were developed many years ago and are still assembled the same way today, says Stephan Stricker, product manager at B&R Industrial Automation (www.br-automation.com). “As long as these machines work well, there is little pressure for the machine builder to change the network,” says Stricker. “In retrofit applications, many old controllers can’t be upgraded to Ethernet, but the newer controllers can support Ethernet as well as older technologies,” adds Stricker.
If installed base were the only issue holding back Ethernet, then we’d expect Ethernet to eventually triumph as end users upgrade over the years. But proponents of alternative networks point to other Ethernet problems, chief among them topology.
Hard to Deal with Stars
Dealing with stars can be difficult, whether it’s the movie industry or industrial networks. “The biggest problem with Ethernet is the star topology. If I have ten devices, I need at least a 12-port switch, and that’s expensive,” explains ADCO’s Gilpin. “If each Ethernet-enabled device had a minimal switch built in, it would be simple to construct a ring topology network, and Ethernet adoption would progress at a more rapid rate.”
Others agree with Gilpin’s assessment. “Ethernet cables typically need to come back to a central location rather than daisy chain down the length of a system,” says Jonathan Van Sweden, electrical engineering supervisor at Möllers North America in Grand Rapids, Mich. Möllers makes packaging/material handling equipment, primarily bag palletizers and stretch-hooders. “Some manufacturers are starting to integrate unmanaged switches into their Ethernet-enabled devices, but this adds additional hardware costs.”
Suppliers agree. “Ethernet offers only the limited star topology unless each device is equipped with an integrated switch,” notes Helge Hornis, PhD and manager of the intelligent systems group at Pepperl+Fuchs. “While it’s doable, it clearly drives the cost up.”
A network issue related to star topology is power over Ethernet (PoE). “While PoE is available, the limitations are significant, and it’s currently not possible to use it to power a large number of field devices,” explains Hornis. “In practical terms, this means that each field device must be powered separately, and that creates a complex solution.”
Yet another topology-related issue is distance limitation. “While Ethernet is limited to 100 m cable runs, CAN-based buses support cable lengths up to 5,000 m without any additional hardware,” notes Stricker.
Overkill
Using Ethernet to transmit small amounts of data “is like using an 18-wheeler for a trip to the grocery store,” observes Tom Edwards, senior technical advisor at Opto 22. “It’ll work, but it’s not the most efficient way to go. We like to say that nothing is too complex for Ethernet, but some things are too simple. Simple serial-based industrial approaches such as RS-232, RS-422 and RS-485 likely will always have their place, as will the protocols commonly used to communicate over these networks such as Profibus and BACnet.”
An experienced end user has his take on Ethernet overkill. “Ethernet sends out 1,500 words at a time in one packet,” explains Gary Crenshaw, electrical engineer at Beam Global Spirits & Wine in Clermont, Ky. “Even though overall transmission rates are fast, for moving small amounts of data like discrete I/O in a PLC, Ethernet is so inefficient that it’s actually slower than some competing networks.” So, just like computers use a different protocol for communications on the motherboard, it appears that certain parts of the plant aren’t always best suited for Ethernet.
“The overhead associated with carrying one bit of data from an on/off device over Ethernet makes it impractical for very simple applications,” thinks Carl Henning, deputy director of Profibus and Profinet in North America. “Industrial Ethernet protocols that use all layers of the TCP/IP stack have lots of overhead. EtherNet/IP and Modbus TCP, for example, insist on using all layers of the stack at a large cost in overhead and therefore processing time. The TCP and IP layers add their own header and trailer data, increasing the overhead, so Profinet skips these layers for real-time data. Profinet, like all the serial field buses, uses just layers 1, 2 and 7 of the ISO stack.”
Better Than Ethernet
Many think that lower-level device and instrument networks will continue to thrive in Ethernet’s shadow for years or even decades to come. The leading candidates for survival fall into two main categories: device-level networks used for moving small amounts of discrete information and instrument networks for communications among analog instruments.
The device-level networks include AS-i, DeviceNet, Profibus-DP, CANopen, CompoNet and Modbus.
Most of these device-level networks are CAN-based. This is crucial as the worldwide motor-vehicle industry makes extensive use of CAN and this gives CAN-based networks the economies of scale to compete against Ethernet, a point often overlooked by Ethernet proponents.
Industrial Ethernet Weaknesses1. Star Topology
|
According to many end users, these other networks are simply better than Ethernet for their particular applications. “We need a device-level network, for example DeviceNet or AS-i, that is relatively noise-immune and can be routed or integrated with I/O device power cabling. The network topology of DeviceNet and AS-i permits devices to be daisy chained together so that you only need to run one cable down the length of a system and tap into it for any device nodes,” explains Möllers’ Van Sweden. “Ethernet does not have a power-integrated cabling system that provides enough power for any significant field outputs such as pneumatic or hydraulic solenoids. DeviceNet and AS-i both have the option of having auxiliary power integrated into the cabling system.”
Many manufacturing facilities need a low-tech device network that offers very simple, often automatic, device replacement. “Ethernet has some of this ability if the networks are set-up properly, but this often requires additional hardware and planning,” concludes Van Sweden.
AS-i collects low-level data so that it can be transmitted as one Ethernet data frame. “It features replacement of field devices without configuration tools, deterministic data acquisition and Ethernet-independent safety implementation for devices such as e-stops and light curtains,” adds P+F’s Hornis. “AS-i’s low-cost hardware permits a highly distributed I/O layout, and its insulation-displacement technology allows field devices to be mounted anywhere on the network.”
Triangle Package Machinery in Chicago makes packaging machines, specifically vertical form, fill and seal bag machines, horizontal cartoners and combinational weighers. In addition to Ethernet, Triangle uses DeviceNet for a variety of reasons. “The capability of branching to multiple devices in a tree configuration makes installation simple, and there is no need to add a switch or hub to connect a new device,” notes Steve Bergholt, chief engineer, electrical/electronic at Triangle. “We also use the automatic device replacement feature of DeviceNet, so our customers don’t need a laptop to program a device when doing a field replacement. With Ethernet, many devices need to be programmed and have an address configured with a laptop before use, and this is inconvenient for many end users.”
A more detailed technical explanation of DeviceNet is provided by the Open DeviceNet Vendors’ Assn. (ODVA), the organization that supports network technologies built on the common industrial protocol (CIP), including DeviceNet, EtherNet/IP, CompoNet and ControlNet.
“DeviceNet uses a predefined master/slave connection set to simplify movement of I/O messages,” says Katherine Voss, executive director of ODVA. “Many sensors and actuators are designed to perform some predetermined function in which the type and amount of data the device will produce or consume is known at power-up. So after powering up the network, the only remaining step necessary is for a master device to claim ownership of the predefined connection set of its slaves.”
Instrument Networks Have Their Place
The leading instrument networks include Foundation fieldbus, HART and Profibus-PA. Like device-level networks, many industry participants think they will remain viable for years to come. “The design goals of Foundation fieldbus were different from Ethernet,” notes Lee Neitzel, senior technologist at Emerson Process Management.
“Foundation fieldbus was designed as a multi-drop bus that allows devices to be interconnected on the same run of cable up to 1,000 m long. This simplifies installation and significantly reduces installation costs. It is also bus-powered, so separate electrical runs are not necessary, as they are in Ethernet,” describes Neitzel.
Foundation Fieldbus was designed to be intrinsically safe, unlike Ethernet, “so the power levels on the bus cannot be high enough to cause flammable gases to ignite,”adds Neitzel. “Finally, Foundation fieldbus has security mechanisms built in that detect and report unauthorized devices. Ethernet limits its recognition of devices based on their MAC addresses and has no mechanism to actually identify a device.”
Security Concerns
Security is, indeed, a key relative strength of other networks over Ethernet. “Vulnerability issues will limit Ethernet’s growth in certain sectors,” says Tracy Lenz, senior product support engineer at Wago. “Hackers can penetrate Ethernet, obtain sensitive proprietary information and inflict various types of damage. Non-Ethernet networks provide isolation from Ethernet and security issues, and it’s virtually impossible to hack into these networks from the outside world.”
Ethernet topologies open the factory up to security risks, agrees David Kaley, product marketing manager for HMIs, networks & SCADA at Omron Electronics.
“Anyone able to use a computer can plug in and disrupt production and gather manufacturing intelligence over an Ethernet network,’ he states. “The [security] solution is to run two different Ethernet networks, one office-based and one industrial, but this adds cost and complexity.”
Eventual Winner?
Many of the initial weaknesses and limitations of industrial Ethernet have been overcome, and some think the time has come to unite. “Ethernet should be adopted and used for all aspects of system integration in business, manufacturing, high- and low-level distributed supervisory controls and security,” says Rick Hakimioun, senior instrument/electrical control systems engineer for Paramount Petroleum in Paramount, Calif. “No other networks are needed—Ethernet can be used with a variety of control system protocols like Modbus/TCP and EtherNet/IP in addition to HTTP. The only thing holding back Ethernet is the lack of end-user understanding with respect to its determinism, its association with business IT networks and its vulnerability to hackers.”
At least one vendor agrees with Hakimioun. “Our industry is slow to follow consumer and commercial electronics, but ultimately it always does,” observes Scott Evans, business unit director at Kollmorgen Industrial Automation. “We simply can’t ignore the low material cost and orders-of-magnitude, greater engineering horsepower of Ethernet. The tens of thousands of engineers working in non-industrial electronics have figured out ways to make Ethernet deterministic and have set standards such as IEEE 1588 for Ethernet synchronization.”
Another Ethernet strength is easy connectivity to the enterprise. “Ethernet eventually will supplant other industrial networks because manufacturers need access to real-time production floor data,” says Mike Hannah, NetLinx product business manager at Rockwell Automation. “The convergence of Ethernet technologies between traditional IT systems and manufacturing operations provides manufacturers with substantial opportunities to reduce risk and costs, provides secure access to information and improves agility and overall business performance.”
Industrial Ethernet Strengths1. Can handle even the most complex application
|
When Ethernet first emerged on the plant floor, it clearly wasn’t suitable for most applications. But as Ethernet has improved, the barriers to industrial implementation have fallen one by one. Proponents are betting that Ethernet eventually will overcome all current limitations and emerge as the one bus to rule them all. Opponents say this will never happen as special-purpose buses will always have their place.
Network Wars
There are wars at every level of industrial networking, as vendors try to promulgate their standards as the one true solution. For many users, the best course of action is to pick a battlefield where the combatants are more limited. This gives users a fighting chance of picking a winner.
Competitors are most numerous at the Ethernet protocol level. “Our biggest concern with Ethernet is that there are so many different protocols across an Ethernet wire, each with a narrower supplier base than any of the device-level networks,” explains Jeff Hanna, manager of control product development at Intelligrated in Mason, Ohio.
Data Sort
Intelligrated built this high-speed shipping sorter to route goods at a distribution center. Intelligrated relies heavily on Profibus for communications within its material handling systems.
Source: INTELLIGRATE
Intelligrated is a supplier of integrated material handling systems. Its equipment performs high-speed case sortation, accumulation and merging. “At a recent conference, I heard eight vendors claim to be the No. 1 supplier of industrial Ethernet, and they all had different wiring standards and interface chips,” he adds. “Right now, using industrial Ethernet is like trying to implement eight different types of Profibus, and this is not appealing.”
When the standards for industrial Ethernet stabilize, that’s’ when Hanna thinks it will grow. “It would be ideal to move to Ethernet for a variety of reasons, but without a broader base of vendor support for components that work on the network, it is hard to justify the investment,” he adds. “Security and performance issues can be mastered and managed, but trying to support and troubleshoot a system with many different protocols is not a worthwhile task.”
A vendor seconds Hanna’s concerns. “End users and manufacturers need to reach agreement on Ethernet protocol standards,” observes Ian Verhappen, director of industrial networks at MTL Instruments. “We face the same dilemma as we did during the fieldbus wars of a decade or so ago. Because of Ethernet's bandwidth this issue is not as difficult as with the slower-speed fieldbuses, but it is important that the end user have a single interface to the data.”
The General SpeaksGeneral Motors might be in a world of financial trouble, but the company remains one of the largest users worldwide of industrial networking technology. Gary Workman, principal engineer at the Control Conveyors, Robotics and Welding (CCRW) group at GM in Warren, Mich., is one of the world’s foremost authorities on real-world applications of industrial networks. “At GM CCRW, we use DeviceNet as a cost-effective device-level I/O network that supplements our use of EtherNet/IP as a controller-level network,” says Workman. “If I weren't concerned with support and legacy installation issues, AS-i also would seem to be an alternative complementary device-level network.” Workman says device-level networks provide more cost-effective connectivity to machine control-I/O-level sensors and actuators than Ethernet does. “The combined power and communication capabilities of both AS-i and DeviceNet better suit the environment than any power-over-Ethernet proposals I'm familiar with,” he adds. “These networks also feature simplicity in their addressing and installation practices. Freedom from virus and malware distribution-security concerns is another big advantage.” For industrial Ethernet to compete at the device level, “individual network-capable components need to be cheaper,” believes Workman. “An Ethernet-capable I/O block needs to be cheaper than a functionally identical DeviceNet-capable I/O block. Also, Ethernet has inherent power-up timing limitations that make it difficult to apply to time-sensitive tool-changer applications.” |
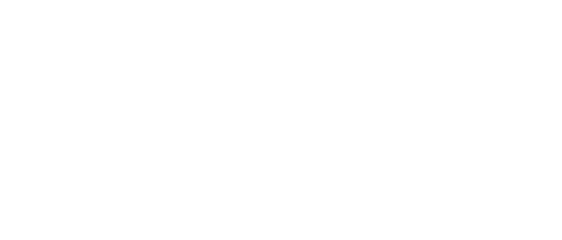
Leaders relevant to this article: