Todd Bauernfeind is president of Summit Machine, a machine designer and builder in Shoreview, Minn.
For Summit Machine in Shoreview, Minn., precision is absolutely essential as it engineers, designs and builds custom web converting equipment for a variety of industries and applications.
Summit recently built a high-precision servo-driven web converting machine for a developer, manufacturer and supplier to the electronics industry that was launching a new product but had antiquated machinery incapable of production of the new line. Summit's challenge was to design a machine having a robust, yet flexible control system without the need to program all the advanced functionality from the ground up — a process that could make the machine cost-prohibitive.
"The customer really didn't have sophisticated web-converting equipment," says Russ Hubrich, engineering manager at Summit Machine. "They were built around brakes and very basic technology. This new machine was a step above. They had an old rubber-mixing machine with big gear boxes that they'd bought used, and it was worn out and oversized for what they were doing. The adjustment for the gas was manual. It was very crude. They were running material through it and moving it off-line and cutting it, and they wanted it all in one machine. Our new machine uses two web-converting rolls as the heart of the machine."
Built-in Functionality From the Ground Up
The web converter Summit designed and built for this application is a 20-axis converting machine that takes material compounds and precisely forms them against a substrate to create the final product, which usually resembles a soft pad and comes out of the machine as a sheet or on a roll (Figure 1).
The machine is composed of two sections with a curing oven in between. The front section has three unwinding spindles and a coating section with one fixed cylinder on the leading edge side and one movable cylinder on the finishing side that allows the operator to control the gap distance precisely. The backing material unwinds from the spindles and passes through the coating section as product is pumped in between to a given thickness.
The converted web material then passes through the curing oven to the back half of the machine where chill rollers, a main product rewind, and a slitter-sheeter are in place.
As the converted web material is cooled to room temperature using the chill rollers, it can be either rewound in a roll-to-roll process or cut into sheets. For the roll-to-roll process the materials go onto a rewind, which can also involve two other rewinds for liner removal if desired.
If the final product is requested in sheet-form, the material passes over the rewind and enters a nip conveyor. The nip conveyor uses two conveyors that are pneumatically loaded together to create a nipping action without crushing or deforming the final product. Afterward, the material goes through a standard shear-cut slitting head and die station. The liner is peeled back and replaced with a new one to eliminate wrinkles and then run through a precision die cutter so it can be cut into different sizes before moving to an output conveyor.
For flexibility, the machine can be split electronically into two machines allowing the web-converting section to run a roll-to-roll process while the slitting-sheeting section can run roll-to-sheet. Summit's customer was bringing a new product into production, so the new machine was critical. "We built two machines," explains Hubrich. "The first machine increased capacity; they could cure it in-line. The second machine went to another plant so they had redundancy."
More Flexibility, Less Programming
"Developing tension-control algorithms takes a bit of time and energy," explains Hubrich. "We buy discrete components and configure them and then figure out a way for them to communicate." To help develop the control system, Summit worked with local automation distributor Motion Tech Automation, which specified the Synax 200 control platform, a PLC and motion control solution from Bosch Rexroth.
"We found this Bosch Rexroth platform with a motion package," says Hubrich. "To get a machine like this up and running, you do some configuration in the motion end of the software and some tuning and you're done. You don't have to create it from scratch." Intelligent servo drives using SERCOS communication, servo motors and two operator interfaces rounded out the proposed machine specifications. "To start this from scratch would have made this project cost-prohibitive," explains Hubrich. "We had to get our customer's buy-in, so we proposed this as a solution. We talked about a few alternatives with discrete components, but that wasn't a good idea for them. They were very open to the platform we suggested."
Specifically designed for the converting industry, the Synax 200 is a freely scalable control and drive solution that helped Summit build in flexibility without a lot of time-intensive programming. "You can add as many drives as you want and change around your servos as you see fit," says Hubrich. The Synax 200 replaces wear-prone mechanical drive elements with electronic line shafting (ELS) and uses tightly synchronized digital servo drives and dynamic servo motors running off a standardized control platform. "The original machine had only two motors, so there was no line shaft," explains Hubrich. "The old rubber-mixing machine had three rolls. The only other option was line shaft, and that was never a consideration for us. There's no flexibility with line shaft."
Standards Help
In addition, the system includes numerous IEC 61131-3 motion functions such as electric gearing and camming, tension, winding and registration controllers and IEC 61131-3 logic functions. Motion control is achieved by parameterizing highly flexible motion profiles, while advanced functions can be programmed in an IEC 61131-3 language as needed. With the built-in functionality in Synax, Summit could focus on adding other functions to customize the machine for an individual customer. For example, a special function block was used to calculate and download motion cam profiles to the die axis, allowing the machine to create variable length sheeting 2-24 in., without changing the dual knife cylinder.
"Synax is an excellent solution because we didn't have to write a variety of low-level codes," says Hubrich. "The software saved us a lot of time and headaches in getting the machine up and running. The Synax system has really good application-specific functionality that allowed us to work more efficiently. You can get a web machine up and running once you configure the software. If you've created the software already, then it's that much faster."
Motion Tech Automation was instrumental in helping to program the machine, adds Hubrich. "The effectiveness of the software made it easier for MTA to help program the machine and helped us get it to market very quickly— with a programming and debug time of only three weeks," says Hubrich. "The Synax software also provides more flexibility in running the machine in a variety of configurations for different product recipes."
Digital Control
In addition to easier programming, precise control is also crucial to the machine, particularly for gap control in the rollers, says Hubrich. Summit's customer makes hundreds of different sizes, versions and varieties of product, so adjustment of the machine's rollers must be controlled carefully. The IndraDrive digital intelligent servo drives provided exactly what was needed. The converting portion of the machine is composed of two rollers — one fixed and one movable. The movable roller allows for precise control of the gap distance via linear encoder feedback from the roller's motor into the drive. Linear scales also feed directly into the drive. "We use Heidenhain linear scales as a secondary position input to the drives for tighter control of the position," explains Hubrich. Using dual loop control, the drives provide tight control of the actuator positions, which allow for minute changes in the gap distance. "They set a gap, say a quarter-inch, and the servos hold the gap until you move it again," he explains.
For the machine motors, Summit is using IndraDyn synchronous servo motors that offer complete scalability and compact construction with increased torque density. Hubrich adds that MTA helped Summit size the motors appropriately on the machine and matched them to different gear ratios so that they had an optimized system of drives and motors.
Two IndraControl VEP operator interfaces with embedded Windows CE systems, providing the power and functionality of a PC but with flash card technology, also were used for recipe management with the touchscreen (Figure 2). The dual HMIs are used to help provide split capabilities so the machine can run as two separate units. The OIs also are beneficial for recipe management, which is important for Summit's customer because of the variety of products it makes. Applications for the machine can be created with the WinStudio configuration software, and parameters for product changeover can occur with the push of a button.
Short Learning Curve
Because it was supporting Summit from the ground up, MTA had to be certain it could deliver an easy-to-use system. Potential roadblocks were avoided through technical support.
"Rexroth transferred its knowledge to us very quickly and efficiently so that we could become experts in a short period of time," says Hubrich. "They provided an applications engineer who became our liaison to make it a very successful project. He came out on-site and helped train everyone on how to use the application so it went very smoothly."
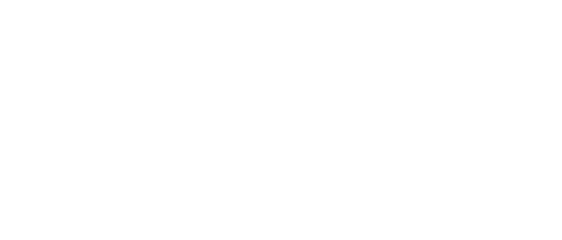
Leaders relevant to this article: