By Matthias Falk, programmer, Bionade Abfüll
Mix enzymes common to honey bees, secondhand material handling and processing equipment, machine-mount I/O, a Profibus/CANopen hybrid and new cabinet-free IP67 I/O system, and you’ve got a cost-effective beverage production system that produces Bionade, the alcohol-free, malt beverage.
Bionade transformed Germany’s struggling Peter Brewery in Ostheim into a European powerhouse. Faced with closure, the brewery broke with centuries of tradition and bet on a healthful isotonic beverage, Bionade, which is brewed as beer is, following Germany’s stringent Reinheitsgebot purity law.
Bionade’s buzz comes from what happens during fermentation. Rather than producing alcohol, microorganisms transform natural sugar into gluconic acid. This is similar to bees producing honey, as both use glucose oxidase—a bee saliva enzyme. Per Reinheitsgebot, no artificial ingredients are used for color and flavoring, and only local, organic produce and herbs are allowed.
With demand outstripping production and a 2007–2008 expansion into the Pacific Rim and U.S., which required additional product runs and new flavors, Bionade needed a production system capable of 35,000 bottles/hr.
Programmers, engineers, electricians and production managers deftly purchased and blended used components including Polish pasteurization equipment, Swiss material handling and unpacking equipment and a Danish case washing system into one system.
“Selecting used equipment from these beverage processing facilities was financially prudent; everything was purchased for the price of one new pasteurization system,” explains Matthias Hansmann, Bionade electrical systems manager. “Of course, there were complications.”
Missing operator manuals, incomplete documentation and approximated specifications—substituting for CAD drawings featuring conveyor belt heights and other data—created a substantial challenge. Bionade turned to Husslein Controls & Automation in Eltmann, Germany, to help unify the hodgepodge of components.
“Without a detailed integration plan, we relied on collective ingenuity,” says Martin Husslein, director.
Then, there was the legacy system, consisting of aging PLCs from a variety of manufacturers. Like Bionade drinks themselves, the production system was organically grown and mixed; newer PLCs were purchased on an as-needed basis. Essentially, the production system consisted of several smaller systems, with each running under its own proprietary controls — there were no distinct hallmarks of a unified production system. There was also no way to get the consistent reliable data communication that an expanded production system would need.
“When we first looked at Bionade’s existing production system, we knew we’d need a capstone system,” Husslein recalled. “As a result of Bionade’s European shopping spree, some of the used components purchased had control units, and some didn’t. Of course, all the secondhand components had to work with virtually everything Bionade already owned.”
During the planning stages, Husslein also noted that a fieldbus-independent system would be needed to ensure all existing and future components could be readily accommodated by the new I/O system.
Electricians removed all control units, no matter how relatively new they were, from the factory and prepared to move to one consistent control system. Among the challenges the programmers, engineers and electricians faced was finding an I/O system with nodes compact enough to fit footprints of existing panels. Wago’s I/O modules can accommodate up to eight channels in a ½-in. housing.
“Our production relied on dated technology, complete with plug-in logic elements. Because the system was so reliant on secondhand components, we basically had to remove whatever control systems were in place, as the system was running on several different proprietary platforms. We also had to contend with the fact that there were several used modules purchased without control units. We needed to ensure those modules could be efficiently repurposed as well,” Hansmann recounted. “We selected the Wago-I/O-System, as it can accommodate all component-specific needs and is scalable.”
The granularity of the Wago-I/O-System allowed Hansmann to add digital and analog inputs and outputs of differing potentials all on the same fieldbus-independent node simply by adding additional compact modules according to Bionade’s specific requirements. As Bionade evaluated the Wago-I/O-System, they felt the system’s accommodation of up to 64 bus terminals held promise for future system expansions. For instance, there is a node for conveyor controls that is completely full with bus terminals, and yet the entire system has the potential to readily accommodate future needs.
“It’s pretty straightforward now; I just attach what I need,” explains Hansmann. “If I need more, I add more. I’ve never had to install another node because it was maxed out.”
Because the former production system was a jumble of modules and units purchased on an as-need basis, many pieces operated on "vendor or contractor" control—lots of little bits doing their own thing.
Basically, Bionade, guided by Husslein, chose Wago I/O because of its granularity, fieldbus-independence, connection technology and ability to tie in older units.
The granularity allowed Bionade to just buy or place what's needed. The I/O’s fieldbus-independent nature and the wide availability of modules accommodated existing components. Price and economy of motion also were big factors. Why waste time testing and respecifying new components when they can be repurposed via I/O? Bionade also wanted to avoid screw-type terminations. Because systems were hodgepodged together, Bionade needed a way to ensure reliable data transmission throughout the plant; thus all control units were pulled and new units were dropped in.
Go the Distance
Engineers determined that no common bus protocol could fulfill all of the patchwork system’s requirements. Thus, Bionade selected a Profibus/CANopen combination, using Ethernet for machine-to-machine communication.
“Profibus alone would’ve added approximately 450 more euros to each of the nine panels we were focusing on,” explains Husslein. “Overall, diagnostics would have been more complicated, too. During evaluation, CANopen surfaced as a cost-effective solution.”
With data transfer rates of 1 MB and 500 Kb, the CAN-based I/O-System can accommodate virtually any task, except palletizing. The plant’s existing Siemens PLC-equipped palletizer, which ran its own system of conveyor belts for transporting cases of empty bottles into the plant, required retention of an S7 program. The engineers opted to leave it, replacing the parallel wiring to the PLC with Wago’s Profibus components and avoiding the retraining a new PLC and HMI might require. “Conversion to a different control system would have cost us two weeks, but with S7 we retained the HMI our forklift drivers were used to,” explains Hansmann.
With more bottles requiring sanitizing, labeling, conveying, filling and packaging, Bionade technicians sought machine-mount I/O to ensure seamless production and efficiency.
“Because of the harsh location, we selected IP67 components,” says Hansmann. “The latter is used in an outdoor courtyard, for controlling the return of empty pallets.”
In the palletizing section, Profibus runs at 12 MB to prevent latency at a PLC cycle time of 2 msec. Such high speeds are necessary as cases and pallets must be positioned within ± 0.5 cm through photoelectric barriers via soft S7 PLC.
To prevent EMC faults, despite long lines, Husslein installed a 16 mm² cable parallel to the bus line. If the bus line is applied, the potential equalization is fed directly next to it via a ground terminal block. The bus cable is equipped with a Wago screen clamping saddle, allowing the screen to be laid directly in front of the fieldbus node and minimizing the fault-prone section of the line.
“I’ve had other systems where a potential difference of 4–5 V occurred over a longer bus section,” says Husslein. “This wasn’t an issue until the first cell phone rang, which was enough to crash the bus or blow ASICs. This isn’t a concern now with the shielding.”
Figure 1: Bottles of Elderberry BIONADE leave the filling station. In the background, the modules from the I/O system supervise the filling system.
Source: MARTIN WITZSCH | WAGO KONTAKTTECHNIK
As the upgrade neared completion, Bionade chose the fieldbus-independent Wago-I/O-System to ensure reuse of all existing components. Engineers installed Wago components such as 4-20 mA analog inputs with 16-bit resolution and configurable modules for thermocouples.
To cope with an influx of filled bottles needing to be cased, the case packaging unit’s SSI transmitters required linking to the I/O system. The complex transmitters, which provide the location required to move and position the unit’s gripper arm, were linked without a separate transfer element via an interface module. In addition to eliminating additional hardware, this permitted direct measurement of absolute travel on the gripper arm shaft, retaining position value, even after machine outage, eliminating time-consuming recalibration.
All standard signals within the newly configured production system are processed by the new I/O modules, which offer the flexibility of fully compatible pluggable connectors for rapid wiring switchouts.
“Although this flexibility is vital to efficiency, we thankfully never needed it because there were only two outages throughout the entire installation,” says Husslein.
The facility’s aging conveyor system quickly became the center of focus. Fortified conveyors needed to keep pace with the newly invigorated production system. Processing and conveying bottles required signal isolation at high switching frequencies and low loads. In keeping with the upgrade’s directive of reuse, engineers extended the life of existing “negative logic” photoelectric barriers. Through Wago bus terminals, engineers used Wago optocouplers and relays, turning the barriers into simple switches that verify bottle placement and position on conveyors. The move saved €1,000 and substantially more time.
“The existing barriers recognized clear glass, which many other barriers have difficulty with,” explains Hansmann. “So, in addition to the €150 per barrier price tag, we’d have to invest a substantial amount time researching new ones and testing them. The Wago I/O accommodated the existing barriers’ negative circuit logic, allowing reuse.”
Engineers also limited power supply units to two Wago models streamlining on-hand stock required.
Production Springs Eternal
With the drive to boost production and ultimately the bottom line, Bionade engineers also closely evaluated conductor termination technology for all electronic and electrical installations. Recalling past experiences with failed screw-type terminations, Husslein strongly encouraged Bionade engineers to consider Wago’s promise of maintenance-free connections. The reliability of spring-type connections would allow Bionade to recoup project costs through no downtime, he argued. This would satisfy demand, especially in new areas where limited availability would damage growth and jeopardize long-term profitability.
“A 20¢, screw-type terminal once cost me one-and-a-half days of work, forcing us to enact preventive maintenance for screw terminals several times a year,” recalls Husslein. “With Wago’s Cage Clamp, we don’t need connection maintenance or even ferrules. This makes the cost-to-benefit ratio for Wago connectors in both junction boxes and rail-mounted terminal blocks compelling.”
Figure 2: Passive distributors support the frequency converters that operate at speeds of 80-90 Hz in the outdoor courtyard. Situated in Ostheim, Germany, the production facility experiences year-round rainfall, moderate summers and heavy winter snow, making resistance to temperature-cycling and moisture crucial.
Source: MARTIN WITZSCH | WAGO KONTAKTTECHNIK
In addition to employing Wago rail-mount terminal blocks for conductors up to 16 mm², the Wago X-Com system plug-in connector and rail-mount terminal block system were installed in the bottle-filling system (Figure 1). The engineers sought modular components that could be rapidly replaced without risk of wiring errors.
With increased production came the need to create a new facility to handle greater volumes of wastewater.
Biological Conservation Through Advanced I/O
Bionade production occurs within a UNESCO-recognized biological reserve, making direct discharge of additional unprocessed wastewater financially prohibitive. After analysis, Bionade commissioned the late 2008 construction of a wastewater facility, which is projected to pay for itself in just three years.
“The pre-cleaned wastewater was not only financially important, but was important to our ethos of environmental protection,” explains Hansmann.
After closely monitoring and evaluating recently installed components, engineers noted the reliability of Wago’s IP67 passive distributors, which are used for outdoor palletizing. There, they support frequency converters, which operate at relatively high speeds of 80-90 Hz in harsh outdoor conditions (Figure 2). This led engineers to express interest in installing and evaluating Wago’s all-new Speedway 767 IP67-grade, cabinet-free I/O system.
The filtering system, consisting of a pump station and four tanks—a feed buffer, two reactors with 900 m3 capacity each and a sludge tank—was in place before the actual building was complete. In the feed buffer, oxygen content, pH value and temperature are measured. Wastewater is ventilated by a rotary piston blower moving large volumes of air at a relatively low pressure. From the feed buffer, the two reactors are on a time-feed. After additional ventilation, biological cultures are added and sludge settles. The enriched sludge is then pumped to the sludge tank. The process relies on remote monitoring from several stations, making reliability crucial.
Figure 3: The newly constructed facility processes the increased wastewater. In the facility, a CANopen coupler and an I/O module have been mounted under a cable tray. On the coupler, the blind plugs with terminating resistor is visible. Looming in the background are the rotary piston blowers that ventilate wastewater.
Source: MARTIN WITZSCH | WAGO KONTAKTTECHNIK
Engineers combined the Wago Speedway 767 I/O system, the Wago-I/O-System and Jumpflex isolation amplifiers. One of Speedway’s main tasks was to process digital inputs and outputs for the end switch monitoring of pneumatic valves and drives.
“One Speedway CANopen coupler and three digital input and output modules were built into the filtering plant (Figure 3),” explains Hansmann. “We went full throttle testing Speedway by laying 20 m lines between the modules.”
Because connection is handled through coded cables, Speedway installation was effortless, explains Hansmann. Coded cables also simplified terminating resistors for the busline via Wago’s blind plugs with soldered-in resistors. Additionally, engineers were able to set baud rates via DIP switches after unpacking Speedway components, expediting install.
Similarly, programming for the wastewater facility went smoothly.
“Wago's new EDS files for the configuration in the CoDeSys programming environment represent a significant advance,” explains Husslein. “The modules need only be selected from a catalog that provides the EDS file. The mapping occurs automatically with default values. Counting or leafing through the manual, as one previously had to do for CANopen projects under CoDeSys, are things of the past. Now, this has the same functionality that a PLC user knows from the Profibus configuration or S7.”
The Speedway trial was worth the effort, summarizes Hansmann. “Most of the work was actually done on documentation. In our E-CAD program, there were no symbols for Speedway, so I drew these myself,” he says. “In contrast to this, actual project startup was easy.”
Matthias Falk is a programmer at Bionade Abfüll in Ostheim, Germany.
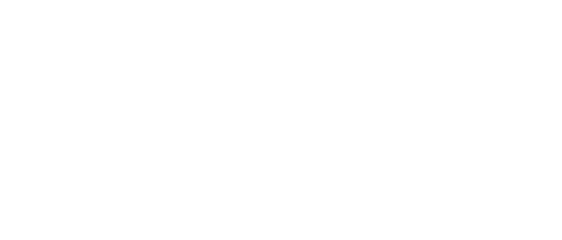
Leaders relevant to this article: