By Phil Burgert
Minimizing a machine operator’s interaction with his machine’s panel display while still providing proper access is an important objective of machine manufacturers and their automation suppliers. The goal is to keep the operator on task of producing goods, not trying to discover and diagnose malfunctions.
Similar requirements apply to access allowed for maintenance tasks and remote monitoring that allow review of operations without unnecessary production interruptions.
Simple, Flexible, Safe
“Ninety percent of the information required is on the one and only screen the operator needs to look at,” says Bill Richardson, electrical design supervisor for Prodomax, a designer and manufacturer of automated welding and assembly systems in Barrie, Ontario.
Richardson says 80% of his company’s robotic zones and cells are equipped with an operator panel and his company generally uses standardized screens. “For operator access—not access for a maintenance person or anyone else—the screen is available with messages and faults automatically that are generated automatically,” he says.
George Schuster, who worked on the Prodomax project as business development manager for automotive solutions at Rockwell Automation, notes that “passive,” “configurable,” and “lockable” were central designs elements, and he touts them as the fundamental guiding principles for panels and how people interact with a machine.
Passive design involves safety systems that workers are not required to engage, such as pressure mats and light screens, says Schuster. “An untrained person should not be harmed just by walking through a door, for instance,” he says.
Configurable system design, adds Schuster, creates modes of safe operation for enabling or disabling portions of a machine that can be used in a variety of situations, such as maintenance tasks. “This is a strategy to remove any incentive for the user to bypass the system,” he says. “Most people bypass safety systems because they have to get their jobs done.”
Lockable system designs allow an operator, maintenance worker or technician to configure a system for a certain mode of operation and place a personal lock on that configuration, to ensure that no one from outside the machine can access it. “A lockable system is a much more expeditious way to get in there, lock the system, lock the gate open, do the repair, get out, and get that machine running again,” he says.
“We don’t require the operator to go through great detail to find out what’s wrong with the machine,” says Richardson. “If for any reason that machine comes to a stop in its normal operation, it is our responsibility to make sure we have generated the message to the operator why that machine has stopped.”
The trick is to let the system provide the information. “We don’t need the operator wondering what he should do next, what screen he should open up, should he be looking for a sequence screen or anything like that,” says Richardson. “We generate the messages to keep the operator on track of his job, not troubleshooting or diagnosing an operation.”
WHAT YOU NEED
Figure 1: An operator initiates an automatic robotic welding machine cycle after a sheet metal part load is completed. Prodomax designs its systems so the HMI is wherever the operator works so he can look at the screen at the same time he watches the process or function.
Source: Prodomax
Richardson emphasizes that Prodomax designs its systems so the HMI is wherever the operator works (Figure 1). “He needs to look at that screen at the same time he looks at the process or the function he is performing,” says Richardson. “If the operator is loading multiple components into a fixture and a light comes on because he’s not getting all parts present, he needs to be able to look over and see what is missing. You shouldn’t have to walk out of the area to see that information. He has to be in the area of his work envelope.”
Prodomax considers it important to provide information on a single screen, to keep the operator concentrating on making parts, rather than diagnosing other issues. “We’re building the machine to make parts,” says Richardson. “The more time an operator spends diagnosing or finding out what is wrong, that’s time spent not making parts.”
Access Options
Access to operator panels can be granted in a number of different ways, including magnetic card swipe, barcode, optical scan and inductive read systems, explains Mark Witherspoon, director of North American automotive operations, Euchner USA. “However, not all systems are created equal, meaning some systems are not as secure as others, and some are not designed for certain environmental conditions,” he says.
Barcodes are not secure because the barcode can be copied easily on any available flatbed printer, explains Witherspoon. Magnetic card swipes are more secure, but are subject to damage and demagnetization—nuisance problems for the user, he says.
“Optical systems, such as fingerprint scanners, can be secure but are typically designed for a clean office-type setting and do not work well in industrial environments that might have airborne dust, coolant, oils or other industrial contaminants that can create a film or cause a smudge on the scanner lens,” says Witherspoon. Inductive transponder coding systems, the same technology that is used in automobile ignition systems, are very secure and are designed specifically for plant floor conditions.”
Controlling operator panel access is important because critical parameter screens are often available through the main HMI, says Witherspoon. Unauthorized access by persons not qualified to make changes to certain processes or parameters can have potentially catastrophic consequences for safety of the employees and for machine performance.
Dave Whittenton, managing manager for production machines for Siemens Energy & Automation, notes that trouble arises when an operator attempts to use a machine and is not familiar with the safety functions and features. “You can imagine what kinds of problems might occur,” he says, noting that Siemens recently had meetings with customers that experienced severe problems with metal forming when employees trying to operate machines they weren’t familiar with.
“It might not be a personal injury, but there’s an injury to the machine when it is not operated correctly or not stopped when the problem is acknowledged or seen and they don’t know how to shut off the machine properly,” says Whittenton.
The main intent of any access control approach is to restrict access to critical portions of a machine process so only personnel approved by the company have access, says Witherspoon. He noted that one of the ways to monitor access control is to electronically track the access of employees using those critical portions of the machine, machine fault conditions and security breaches.
This is most commonly done by data logging via supervisory control and data acquisition (SCADA) type software applications. Controlling access based on safety issues or allowing access to normally safe guarded areas is a different issue and should be handled only with an access control product specifically approved for use in safety applications, he says.
Proper access to the control system or to critical parameters of the machine process can be implemented only with a full understanding of what is possible at each level of the operator panel setup, says Witherspoon, adding that it can be dangerous to arbitrarily assign access levels to personnel without understanding what they actually will have be able to access.
Operator Access to the Info
“We use our HMI to obtain feedback and real-time data from our machine PLC,” says Tom Ignatowski, product manager for welders and heating equipment, Thermatool, East Haven, Conn. The company builds equipment for pipe and tube manufacturing (Figure 2). “We use it for trending purposes to monitor voltages, currents and frequencies that are running through the equipment,” says Ignatowski, “and also for diagnostics to help troubleshoot equipment. The feedback pinpoints where the problem is and gives resolution instructions.”
The operator panels include the ability to see data on operations inside cabinets without needing to permit access to the cabinets and risk contact with high voltages, he says. “You can leave the cabinet fully closed and know what is going on with the PLC and other controlled components internally just by looking at the display,” says Ignatowski.
JUST THE FACTS
Figure 2: Thermatool’s HMI monitors machine voltages, currents and frequencies and for diagnostics to help troubleshoot equipment quickly. The feedback pinpoints where the problem is and gives resolution instructions.
Source: Thermatool
Thermatool provides access to as-built schematics in the HMI so customers don’t have to try to find and work from paper-version copies,” says Ignatowski. The company also uses the HMI’s Ethernet port to connect machinery to remote offices where managers can access and monitor what’s happening on equipment in real time. “Some of these screens are protected, so you need a password to get to them,” says Ignatowski. “We also have setup screens built into the HMI for our customer service people, so they can access the setup screens and change functions or change constants.”
Gary Labadie, marketing manager at Pro-face America, the supplier of Thermatool’s HMI, adds that many factories use passwords for access-control security but notes that in a big facility “a password is only as good as a guy who can keep his mouth shut. After that, security is completely blown.”
In operator interface applications, Pro-face uses level security and individual password security, but it adds traceability, says Labadie. “If someone does access a panel and make a change, that change will be captured with the person’s ID and the timestamp of when those adjustments were made,” he adds.
Many manufacturers think of traceability for products on manufacturing lines, but they don’t think about the traceability of a manufacturing process change and the cause of the change, says Labadie.
Skilled Access Only
Siemens’ Whittenton notes that factors involved with good machine access control range from determining the best location for an operator panel to the type of information provided on the panel. “More manufacturers tell us that good labor in these plants is becoming scarce,” says Whittenton. “They see a lot of turnover in the labor force.” As a result, he notes, education of the labor force is also complex, dynamic and changing.
The task then is “to have better machine security regarding whether an operator is fully trained on safety requirements, compliance issues if this is a regulated industry and to make sure that they are properly prepared to operate those machines,” he adds.
Operator panel access control technologies can improve the reliability and quality of production, says Whittenton. “Some things can be done very easily and quality-checked right at the operator panel,” he says, noting that instruction now provided on the machine previously required off-site training.
“A paper-based trail could tell the management and maintenance people that a person had been certified,” he says. “But who really checks those papers or the clipboard? That’s not done that often, and if it is done it is done after the fact—after the problem already has occurred.”
Phil Burgert is a freelance writer, specializing in the technical trade media.
Machine access problems can create headaches far beyond machine downtime. Sometimes unprotected access to controls can be downright dangerous. Do you have a horror story about out-of-control access? Tell us about it at www.ControlDesign.com/access.
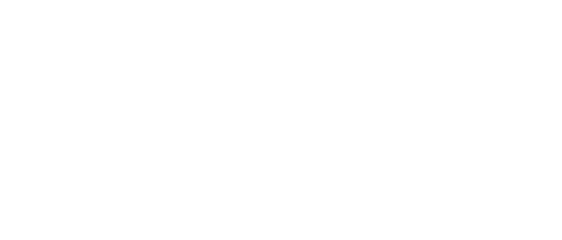
Leaders relevant to this article: