For almost 100 years, the St. Louis-based palletizing group of FKI Logistex (fkilogistex.com) has seen many changes. In its early history as Alvey Systems, it saw the development of the first palletizer in 1950 when it served the American brewing industry. The market focus quickly expanded internationally and then returned to a domestic focus in the late 1980s. Since being acquired by FKI Logistex in 2000, international initiatives are again driving company growth.
Through it all, the organization has kept a close ear to the wants and needs of the food and beverage industry, where most of its customers operate. FKI Logistex continues to focus on the palletizing segment of material handling.
“FKI Logistex palletizing equipment falls into two major categories—conventional and robotic palletizers,” explains Pat O’Connor, product manager, palletizing systems. “There are six families of conventional palletizer, varying by speed and infeed elevation. It’s pretty diverse, but the technology is fairly common throughout the families. On the robotics side, we’re divided by the type of application or product to be handled and the type of arms—load weight and arm reach. Single- or two-line systems are lighter and faster. Heavier-duty applications use up to four SKU loads at a time. Another growing robotic focus is depalletizing.”
While the majority of its palletizing clients are in the United States, this has swung both ways over the years.
"In the 1960s and 1970s, our markets were international,” says O’Connor. “Then ownership changed, and it became U.S.-centric until we were acquired by FKI Logistex, expanding our international focus once again. In our shop right now, we are building machines for Canada, Australia, Mexico and South Africa. We are exporting, but our core group of customers is still based in the U.S.” FKI Logistex has even adjusted some of its own technologies internally to create the new low-cost GS series palletizer. The GS series can fit into a standard 40-ft shipping container, a requirement for keeping international transportation costs manageable.
PC or PLC?
Never-Ending Service
Steve Robbins, senior engineer, audits (left), and Eric Bauder, manager, service engineering, work on a robotic layer depalletizing and singulating system.
Photo by FKI Logistex
“There has been a bit of movement back to the PLC recently,” explains O’Connor. “We thought the PC control was going to grow in popularity, but in some ways that has pulled back. Our typical manufacturing base is just so committed to the PLC business for the majority of the machinery in their production lines that they are hesitant to jump into machine control with PC. We find PC control more in the warehouse and distribution market than with our manufacturing customers. We still use PC for sortation in warehouse and distribution, where we’re typically the only high-tech automation in the building. In manufacturing, it’s kind of the opposite.”
Data acquisition, however, is an ever-expanding function that FKI Logistex customers just can’t get enough of. “On the palletizing side, the number of customers having us format production data for them and make it available to transfer to an overall plantwide system is growing all the time,” says O’Connor. “Most customers want to generate some statistical or time data on cases or loads of a given SKU that are palletized. For them, the customer takes ownership of the product at the time it goes on the pallet. We’re also frequently supplying the data to labeling devices which will generate print-on-the-fly custom labels.”
Stacking Up Against the Competition
What has kept FKI Logistex successful for so long has been its ability to anticipate market demands and offer solutions. Most innovation in the food and beverage industry, admits O’Connor, is driven by the consumer and retailer. “The retailers specify the type of packages they want to sell,” he says. “The move to club stores, which don’t want to dispose of dunnage, changed palletizing dramatically because we had to customize.
Initiatives like Wal-Mart’s push for sustainability and reduction in carbon footprint of products through elimination of secondary packaging will likely increase the innovation in palletizing technology. Controlling the shelf space profile is another trend, resulting in the change in shape of some products—smaller in width and longer in depth so they can fit more on the shelf.” Cost drives innovation mostly through materials. “Corrugate has become quite expensive,” says O’Connor. “It’s extremely rare that our customers would put in a line with full corrugate. We’re now seeing more film because it’s much less expensive. But there are a lot of ramifications for equipment selection. When materials are removed, packaging equipment must be adapted to handle the new packaging effectively.”
The transient work forces that many FKI Logistex customers employ also has a strong impact on the control automation FKI Logistex designs, especially when it comes to diagnostics and setup. “The diagnostics capabilities of the machines are directly related to the availability of labor to our customers,” explains O’Connor. “They’re experiencing a lot of turnover. The machines have to take advantage of their control systems to diagnose more and more of their own problems. Error logging has been available on a lot of HMIs. When the machine is down, being able to key up a screen and find out when it went down and why it went down is a big advantage. We are also doing machines that require no setup or have some automation to help the people doing the changeover and guide them through what needs to be done.”
Who Put That Robot in There?
“The robotic palletizing business is a growth business, particularly in packaging” says O’Connor. “Some of its advantages are the ability to adapt to tight locations in the manufacturing plant. It starts out with using robots to do a job, but we are seeing more robots as components of a machine where the robot will be integrated with the PLC control system of the machine. That presents some challenges because the robots typically have proprietary controllers.”
Check out our video FKI Logistex's Robotic Palletizer
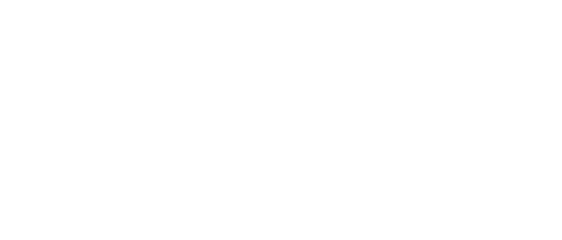
Leaders relevant to this article: