I need helpful DAQ software. I’m a controls engineer proficient in hardware, PLCs, and ladder logic. I don’t have any other software programming experience, and I don’t want to get into large-scale SCADA packages like Citect or Wonderware. What should I look for in a software package in terms of tools, wizards, and other special features that would most easily allow me to implement some basic data acquisition?
—from September ’07 Control Design
AnswersConnections, Systems, and Reporting
Today, automation software extends far beyond the reach of basic data acquisition, offering users real-time data-capturing and visualization options. These packages are relatively easy to configure and install.
First, you need to evaluate what parts of your control system you’ll need to connect with to retrieve the data—and where you’d like to send the information. Software solutions that easily integrate with your control system will help your control-and-information layer communicate best. Features such as PLC programming and system setup tools will help you streamline the production process.
Data Monitoring
Once logging starts, a real-time trace is displayed to keep the operator informed.
Top-of-the-line automation software programs have tools needed to collect manufacturing information at the machine, line, plant and enterprise levels. Real-time information reporting tools help you gauge machine performance by identifying the root causes of production inefficiency quickly and easily. Data historian programs offer you the ability to capture time-series data, for accurate batch comparisons and improved order/product tracking across the enterprise.
A number of display formats and analysis tools can help you extract the most value out of the production information. When paired with an operator interface—placed directly on-machine or in the back office—advanced automation software solutions provide a window into operations. In fact, many programs feature fully customizable production dashboards, so users can compare key performance indicators using graphs and charts.
SCOTT MILLER, business manager
Rockwell Software, www.rockwellautomation.com
Know Your Data
Ask yourself these five questions.
- What data is important?
- What data is useful to display to the machine operator?
- What data is worthwhile to acquire?
- How fast does the data change, how often should you sample, and how much data should you acquire?
- What is the budgeted time and cost for an HMI/SCADA software tool?
For example, say an OEM mixer builder’s customer wants a graphical user interface to capture data, perform calculations, and trend it after the fact. A PLC is used for A/D conversion of the sensor inputs. Four variables are of interest: hp (0-2) and rpm (0-300) on one screen, and product temperature (50-450 °F) and barrel temperature (0-500 °F) on another screen. The cycle time of the continuous mixing process (test cycle) is one hour. The data to be collected and logged is manually triggered by the operator after the barrel temperature has reached a sufficient level and the mixing can start. Once logging starts, the real time trace is displayed to keep the operator informed. Data logging stops when triggered manually by the operator when the test is deemed finished.
The purpose of data acquisition is to understand machine behavior, improve efficiency, and perform diagnostic troubleshooting. With these objectives in mind, it’s desirable to log data at least every 6 sec (600 samples per hour), recall recent trend history on screen, save data, and do detailed historic trending analysis at a later time. It’s also useful to let the operator redline or mark any sample times of interest for further study.
A sample plot produced with InstantHMI software (see figure) illustrates the features described above. The screen includes temperature data fields and legend for plot variables, plot scales, buttons to trigger datalog, mark chart, and status LED. All these elements including plot should be available as widgets for easy pick-and-place screen creation. In addition, it should be easy for you to define tags to identify PLC memory locations—same as in ladder logic—that store the A/D values for the sensor data.
RAMAL MURALI, president
Software Horizons, www.InstantHMI.com
Intuitive Interface
This question is typical for many controls engineers, who don’t have time to learn a high-end SCADA software package. What users look for is a product that provides an intuitive, easy-to-learn, and easy-to-use interface with the functionality they need now and in the future.
Consider these questions:
- Can the software support data acquisition from the various data sources you’re using, and is there any cost to support this interface? For example, can you use existing sensors connected to a PLC or RTU, or is proprietary hardware required? Does the software have drivers to interface to the PLC (RTU) or is a third-party OPC server required?
- Does it support data acquisition by batch or continuous stream?
- Does it have the means to scale the measurement data?
- What options are available to store the streamed acquisition data? Is data stored in a proprietary file format? Can it be stored to Microsoft Excel, Access, or relational databases such as Microsoft SQL Server?
- Does the software have the ability to easily configure data acquisition rates?
- Are tools provided to display the acquired data (both online and historical) and provide dynamic configuration of the pens?
- Can the product support data analysis either through internal functions or add-on software such as ActiveX controls?
- Does it have an intuitive, configurable interface with appropriate configuration wizards?
- Is remote viewing of the data required?
JOHN DUNLAP, vice president, marketing
InduSoft, www.indusoft.com
Data-Logging Support
Since you’re a machine builder, I’ll assume your primary goal is to capture your data and store it locally on the machine without needing remote database connectivity, but you’d like the ability to export the captured data for analysis or to move to another system.
Several products support data logging in the Level 1 and Level 2 HMI space. For your application, ease of configuration should be the primary goal. Look for a package that lets you log the data you to a local file, Microsoft Access database or SQL server by using a simple connection to the tags that you have already created for PLC communications. This will give you the flexibility to set up your data acquisition application quickly and easily, yet allow scalability for a customer who wants to integrate with a higher-level system.
Finally, consider the HMI capabilities of the products that you evaluate. Look for a product with the graphics and tools that will help differentiate your solution and add value to the basic machine operation by making it easier and more intuitive to use.
ANDY BALDERSON, product sales
Parker Hannifin, www.parker.com
List Your Requirements
Generally, a data acquisition system could include many components for getting I/O data (PLC, RTU) into PC, PLC protocol drivers, scaling and engineering unit conversion, data logging, data retrieval, data archival, backup, restore, data import/export for reporting, reporting, and trending. If you want to perform supervisory control, then it will include alarm detection, alarming system, security, validation, failover, redundancy, scripting, and supervisory logic. For graphical data display, you might need a visualization subsystem with animation and trending.
Vendors offer a range of products from a simple small HMI system with 64 tags or I/O points to thousands of tags. The systems can handle all of the above requirements in a gradual manner. Most of these HMI packages don’t require any programming background. You use the features that you need. Alternatively, if you use a standard PLC for control, you can get simple proprietary panels with built-in HMI and driver from many embedded panel vendors. There are third-party data logger programs also available for similar applications.
RASHESH MODY, vice president
HMI & SCADA, Wonderware
www.wonderware.com
FEBRUARY’S PROBLEM
I WANT TO USE machine vision to measure color variation and perform real-time control on our paint nozzles. I am not an expert, so I need a machine vision system that will be relatively easy to design, install, and maintain. Can I do this myself with assistance from the right vendor, or should I look for a systems integrator that specializes in machine vision?
SEND US YOUR COMMENTS, SUGGESTIONS, OR SOLUTIONS FOR THIS PROBLEM. We’ll include it in the Feb. ’08 issue, and post it on ControlDesign.com. Send visuals if you’d like—a sketch is fine. E-mail us at [email protected]. Please include your company, location and title in the response.
Have a problem you’d like to pose to the readers? Send it along, too.
More, More, More
Answers from Rami Al-Ashqar at Bosch Rexroth, James Davis at Opto 22, John Ditter at Wago, Ron Dawson at Kessler-Ellis Products, Bjoern Falke at Phoenix Contact, Cindy Hollenbeck at SoftPLC, Gary Mathur at Moore Industries, Corey McAtee at Beckhoff Automation, Nathan Pocock at Software Toolbox, Maria Santella at ICP DAS, and Erik Syme at ProSoft Technology can be found at ControlDesign.com/RealAnswersNov07.
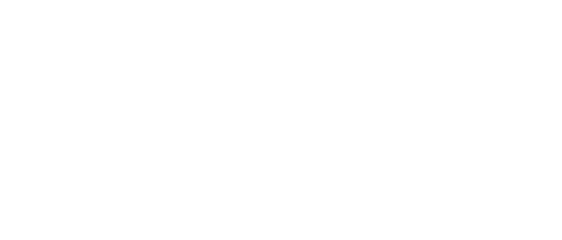
Leaders relevant to this article: