We often need custom cable and connector assemblies engineered specifically for our machine automation applications. Is it best to just make these ourselves, or should we go outside? If we go outside, how do we find a good source that we can count on?
—from June ’07 Control Design
ANSWERS
Most people feel a molded cable is best. We agree, so this answer will assume you prefer a molded cable assembly.
If you use a single-ended cable, it’s possible to stock molded cables in several lengths that can be cut down if necessary to reach the required length for your application. Determine how many different lengths you might need. Can 80% of these needs be accommodated by cutting down a few different stock lengths? If yes, you can keep those items in stock, and cut to length for most of your needs.
If you require double-ended cable assemblies, you can stock a few different lengths of single-ended molded cables and apply a field attachable connector on the opposite end—the end going in the least hazardous side of the application—after cutting to your desired length.
Can you plan in advance for the cables you need? If you can, and if you have significant quantities, there are many cable manufacturers that can help you. If your required quantities are small, you’ll need to find a cable manufacturer that can produce smaller quantities.
We have a system we call Open Variant, an automated production cell that lets you select from a variety of cable and connector options for both ends of the cable and select your desired length, but doesn’t require large quantities.
If you need custom-length assemblies and can’t plan in advance, then you really have no option other than to stock your own cable and field-attachable connectors.
Ted Brunk, national sales – connectivity
Hirschmann, www.hirschmann-usa.com
Form a Business Relationship
Typically, it would be cost-effective to have this work done by a manufacturer that specializes in this area, but some connector manufacturers won’t touch a custom job unless the volumes are high enough, or they have a strong partnership with the customer, and know that in time it eventually will be profitable. Other factors to consider are UL certifications and safety issues arising from improper in-house design and development.
A good way to find a reputable connector assembly company is to go online to any of the industry publications. Most have a directory listing of manufacturers. Once you find a few, call them to see what their custom capabilities are, and perhaps visit their facilities to see if they can show you work in progress. Begin to form a new business relationship. Then make your decision.
Ronald Bezz, national sales and marketing
Lumberg, www.lumberg-automation.com
Cables Are Like Porsches
As with any skill set, given time and trial, your machinists can build cables, but you’ll be taking them away from the expertise and skills they were hired for. Building the cables only answers half the problem. They also need to be built correctly. This means using the correct wire, no internal shorting, correctly soldered connectors, secure strain relief and hooding, and accurate testing to make sure they meet all the required specifications.
Think about it this way: If you own a Porsche you could try to figure out what might be wrong and attempt to fix it yourself, take it down the road to the neighbor who moonlights as a mechanic, or have a certified Porsche mechanic fix it. Considering high-end machines and computers can approach or exceed the cost of a Porsche, this analogy is appropriate.
So how do you decide which company to choose? First and foremost, base your decision on the longevity of the company. You want an established stable company because it will have perfected its techniques and cabling procedures. Do you really want a newly established company using you as its guinea pig, while it learns how to correctly build cables?
Ask co-workers and peers which companies they recommend. Read reviews of these companies online. Take a look at the company’s web site. Do they offer a great variety of cables? If so, then they should be able to handle any unique cables you request from them. If you need a larger quantity of a certain cable, the right custom cable company should have the partnerships in place with their factories to have your unique cables professionally molded. Ultimately it will come down to whether you think the company trustworthy enough to build your product to your expectations in a reasonable timeframe.
Dave Maher, sales
Pacific Custom Cable, www.pacificcable.com
Proper Tooling Ensures Reliability
This is a question I’m sure many companies struggle with. On the surface, assembling cables appears to be easy. Just crimp or solder contacts to wire, perform some mechanical assembly and off we go. Not so fast.
There are many different connector systems available that perform differently, and are assembled and tested with a variety of tooling. Tooling can be expensive, and sometimes can exceed the cost of the cables. The performance of your cables can drastically affect your application. Proper crimp tooling is essential to ensure reliability. Cables can fail immediately or over time due to improperly crimped terminals. There is nothing worse than sending a technician on an expensive service call to fix a $10 cable.
Partnering with a qualified cable assembly shop is the path most companies choose these days. Some require a very high volume of assemblies, but many of them don’t. Some will design cables from the ground up and most will help with design suggestions and improvements.
As with most things, word of mouth is a great way to find a qualified shop. If you typically spec a certain connector manufacturer’s products, it can recommend cable shops that are the right size for you, and are tooled for most of its connector systems. Many shops will work with you on stocking common components to help with quick turn deliveries.
However, if your needs usually are immediate, you should consider having this capability in-house. Just make sure you have an experienced employee to oversee this, and invest in proper tooling. Cable shops often run lean and have busy production schedules that make immediate deliveries and frequent changes difficult.
Steve Smith, custom product supervisor,
L-com, www.l-com.com
Most Manufacturers Know Their Stuff
In general, materials used in these assemblies need to be determined based on the environment to which they’ll be exposed. For example heat, oils, and chemicals all affect the choice for the most suitable material for the application. In many applications, the materials aren’t affected by the environment, and are selected based on the experience of the cable manufacturer, preference of the user, or even material cost.
You’ll find the workmanship of most connector/cable manufacturers to be exceptional. They use the latest tools to ensure reliable connections. If the connectors will be exposed to fluids or other materials that can enter them and cause premature failures, you’ll want to consider connectors that are fully encapsulated by molding material, and also provide additional sealing at the connection point.
Jeff Schoenberg, , connectivity division
Turck, www.turck.com
Ask Questions to Be Sure
Some companies that have been manufacturing in-house feel that if nothing is wrong, then why fix it? Nothing might be visually wrong with their cables, but there must have been some pain associated with their assemblies to even think about outsourcing. This is the perfect time to solve the problem and remove the pain.
When looking for a wire harness manufacturer you need to keep in mind there is more involved than just one person putting together a cable assembly. As in every industry, everyone has a niche product or specialty. Ask around and ask the competition who they use for cable needs or just hop on the Web and start looking for wire harness manufacturers or cable assembly houses.
Some of the standards you should look for when choosing a manufacturer are ISO-certification and the kind of testing offered. In this $20 billion industry of cable assemblies, some companies don’t even test for conductivity before they ship product. That’s downright scary, and this is why you need to ask questions.
So, does the company you’re considering do 100% electrical testing or does it do hi-pot testing?
Does this company follow the Wire Harness Manufacturer’s Association standard A-620 for all of its harness builds? There are only about 200 active WHMA members that are truly solid cable harness manufacturers. WHMA was organized in part to offer an industry standard and a solid reference for perspective buyers.
Is the company UL/CSA certified on manufacturing? Does it test for connector or insulation resistance?
If you still don’t feel confident, ask if you can call one of the company’s top accounts to learn what they’re offering this customer. Or just move on and find a wire harness manufacturer that you do feel confident in using.
The kind of material used is a big part of a quality build, but having quality material won’t necessarily provide you a quality harness. Other key factors are engineering knowledge, purchasing experience, vendor relationships, and industry requirements. But most of all, you need a company that is willing to listen and find out what you are ultimately trying to accomplish.
Most wire harness manufacturers should have at least one designated engineer on staff to help with application analysis and design. A solid engineer can diagnose small problems like using the wrong cable size for the connector or even help save money by showing you an equivalent component.
Another area that should be considered is the purchasing department. A solid purchasing team can source components or specialty wire that could be unobtainable with an inexperienced buyer. An experienced purchasing team can provide the best price, ease worry over price increases, and avoid component elimination.
Sean Loomis, major account manager,
Custom Cable, www.customcable.com
Invest in Quality
So, what expertise is needed to make a cable? Plenty if you want it to be cost-effective, reliable, on time, and compliant to codes. Underneath those shiny connectors and outer jacket is where the major differences lie.
Voltage ratings, shielding, connector material, and jacket material have a way of disappearing in the specifications. You know best what is expected in this cable for everyday operation. If you have the expertise to ensure electrical, mechanical, and compliance integrity, then perhaps the cable should be made in-house. If your abilities lie elsewhere, you might opt for the custom cable house solution or use the component suppliers’ recommended cables.
Choosing a vendor is a dynamic two-way process. The safest way is via standardized auditing procedures. ISO9000 vendors give you the advantage of knowing what the company processes are and how they adhere to these policies. The company expertise is documented. In the case of dealing with independent, non-ISO vendors, knowing the same information is the difference between success and failure. There are many good quality vendors, so you have to weed out the ones that cannot comply with your needs.
Delivery and price questions are the most commonly asked of vendors. The quality of the material as well as the quality of the workmanship is assumed but should not be. You should choose the material since the aforementioned intimate machine knowledge is there. Perhaps you have dynamic expectations, and if the vendor is unaware they could make the cable from a totally unacceptable product.
Some vendors supply cables that certainly comply with the needs of the drive, but also may give you some unseen advantages not evident to the untrained eye. EMI is one issue that causes problems with custom cables. If a vendor uses improper material for shielding, a very expensive rebuild and re-testing could result.
Compliance testing and lab time are at premium prices. An error avoided is savings earned. In most cases, the component supplier should have information on your requirements including application notes, specifications, and accepted practices. A bottom-line rule of thumb is to avoid having the work of an otherwise strong machine undermined by basing decisions exclusively on up-front costs of custom cable and connection assemblies.
Lee Stephens, motion control engineer
Danaher Motion, www.DanaherMotion.com
NOVEMBER’S PROBLEM
I Need Helpful DAQ Software
I'm a controls engineer who is pretty proficient in hardware, PLCs, and ladder logic. I do not have any other software programming experience, and I do not want to get into large-scale SCADA packages like CITECT or Wonderware. What should I look for in a software package in terms of tools, wizards, and other special features that would most easily allow me to implement some basic data acquisition?
Send us your comments, suggestions, or solutions for this problem. We’ll include it in the Nov. ’07 issue, and post it on ControlDesign.com. Send visuals if you’d like—a sketch is fine. E-mail us at [email protected]. Please include your company, location and title in the response. Have a problem you’d like to pose to the readers? Send it along, too.
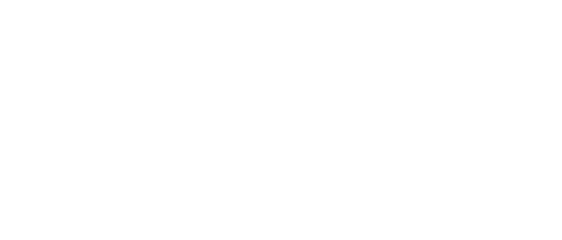
Leaders relevant to this article: