By Kenny Dunhoft, R.A. Jones
If youre a manufacturer facing industry challenges such as global competition, mass customization, and outsourcing, which of these performance characteristics do you select to maintain a competitive advantage: quality or speed?
The correct answer is both of them. To achieve this objective, a company must evaluate and restructure its internal processes and make sure it has the proper technology tools to enable those changes.
Identify Challenges, Set Goals
R.A. Jones & Co., a manufacturer of high-speed packaging equipment for the consumer products, food and beverage, and pharmaceutical industries, historically relied on AutoCAD in its engineering department. The manual process in place for adding cross-references to electrical schematic documents was labor-intensive and error-prone.
Due to the manual processes required, it normally took us three to four weeks to complete a set of drawings using AutoCAD, says Scott Richardson, one of R.A. Jones electrical controls engineers. We commonly found it necessary to cross-reference and perform manual checks on drawing packages that were 40 to 50 pages long.
There were lots of bottlenecks in the process. Each person reviewing the design marked it up and sent it back and forth to the other involved personnel. This manual process depended on humans to check for changes in the information. It shouldnt be difficult for anyone to understand why and how this process was prone to human error.
Put it all together
AutoCAD Electrical allows R.A. Jones to streamline the process of designing and building control panels for large packaging machines.
The schematic drawings are closely linked with the panel drawings ensuring no device has been overlooked.
Photograh courtesy of R.A. Jones
This meant we frequently had to backtrack and take the excess parts off the BOM once the electrical schematic design was completed, adds Tim Meyer, another electrical controls engineer at R.A. Jones.
To compete effectively, the company had to improve its ability to get products to market faster. The manager of engineering tasked company engineers with cutting design cycle times in half. That was an aggressive goal that required the electrical engineering department to consider adopting new technology that would reduce errors and eliminate costly rework.
Select Tools, Manage Implementation
R.A. Jones electrical engineering department needed an overall process change. That was very clear. It also was clear that the technology selected would be the key to enabling larger, department-wide process changes. The department conducted extensive research on the different solutions that were available, and based its decision on what it felt would provide the best benefits, namely the ability to reuse the existing data and the ease of implementing the improved processes. These were the key drivers in deciding which application to choose.
Since wed been using basic AutoCAD for more than 20 years, we had a large library of parts we wanted to continue using, explains Meyer. We were looking for a minimal learning curve. We wanted to use our legacy data in its native format with no conversions. And, we wanted a tool that would add significant value, and not just repackage our existing issues. So, choosing an application that would easily work with AutoCAD made the most sense. In addition, it was important to us that we were able to use several different control suppliers products with the software.
By selecting AutoCAD Electrical, an application built specifically to create and modify electrical controls designs, R.A. Jones could continue to use its existing library of parts because of the true AutoCAD interface; it is AutoCAD for controls design. It was an open package from the standpoint that it worked with many of the suppliers products. And since R.A. Jones had been with Autodesk for such a long time, it was very comfortable with Autodesk as a vendor.
The implementation was carried out over approximately one year, which included the following key milestones:
- Train the TrainersThe first step was to get two team members trained on AutoCAD Electrical through a local reseller. Since they were already familiar with AutoCAD, it took them about two months to become proficient.
- Expand TrainingThese two employees then conducted a wave of training sessions for R.A Jones entire electrical engineering department, approximately 20 engineers. The trainers made sure that the instruction was very specific to their firms line of business and to the tasks its engineers face every day. Each electrical engineer received two full days of training. It took approximately six months for the initial implementation. However, there were some other issues that delayed the training, so it might have been implemented more quickly. Even in the early stages of implementation, the benefits were apparent.
- Establish TemplatesThe next step was to set up templates for each machine design, so the company would have a universal template for everyone to work from, and be able to hit the ground running. Previously each machine line had custom formats. The new AutoCAD Electrical package complemented R.A. Jones efforts to modularize design templates across the board.
- Leverage Existing DataWhen the electrical engineers chose AutoCAD Electrical, they knew the program not only would introduce automation to increase efficiencies, but also would let them continue to leverage the DWG data theyd been generating for decades. For example, we had a library of AutoCAD blocks that weve been able to use with AutoCAD Electrical, explains Richardson. We simply added some additional AutoCAD attributes to those blocks so were able to take full advantage of the enhanced functionality available within AutoCAD Electrical. This functionality strongly contributed to R.A. Jones decision to adopt AutoCAD Electrical instead of competing softwares.
Basically we needed to use the data we already had, adds Richardson. We have a lot of routines internally, including some auto list routines that originally were done in AutoCAD, but were able to be converted over to AutoCAD Electrical. Things that help us do our jobs a little bit better on the electrical side, such as a stock list, made our engineers more productive. We can auto-generate from our business system for a huge advantage.
Measurable Results
By adopting AutoCAD Electrical, the company is better-equipped to maintain its reputation as an elite provider of high-speed custom designs for the packaging industry. R.A. Jones products have a reputation for durability and long usagea testament to its commitment to quality. And, with AutoCAD Electrical, its able to deliver higher-quality electrical designs in significantly less time.
Within the first six months of implementing AutoCAD Electrical, we already were seeing the benefits without disruption to our customers or to our ability to take on new projects and honor prior commitments, states Meyer. And, because we now have an automated process with AutoCAD Electrical, weve been able to eliminate many errors before they reach the assembly floor. Weve increased quality and reduced rework, and this also has helped us cut our design cycle times significantly.
Another contributor to the reduction in both design cycle times and the cost of parts inventory is the new streamlined process for producing electrical BOMs. Before AutoCAD Electrical, our electrical engineers had to estimate which parts would be needed for a design before they even completed the electrical drawings, says Meyer. Now, using AutoCAD Electrical, our team can generate designs concurrently with the BOM creation, nearly eliminating the rework on the backend, as well as preventing unnecessary part purchases because were not rushing to finish drawings and order parts. The key benefit here is that the more accurate the design is, the lower the rework costs are.
Its hard to overstate the benefits AutoCAD Electrical delivers to our electrical engineering team, adds Richardson. We basically went from an Etch-a-Sketch type of CAD system to a true engineering design package when we moved to AutoCAD Electrical. Using this software enabled us to reduce the design cycle time for a typical project. Weve also been able to cut labor costs for electrical drawings, and reduced parts inventory costs, which translates into thousands of dollars in savings per year.
Work Smarter
By using AutoCAD Electrical, the drawings delivered by the engineering department at R.A. Jones to the shop floor are highly accurate, eliminating costly rework.
Photograph courtesy of R.A. Jones
Throughout this entire process, the key to the success of this project was keeping an eye on the big picture, and remembering that this wasnt just implementation of a piece of software.
We were restructuring our entire way of doing things within the electrical engineering department, says Meyer. Many companies fall into the trap of focusing solely on the technology without viewing their processes as an integrated whole.
More to Come
Becoming a more efficient organization is an ongoing part of our business, and we continuously seek ways to improve our processes, and further leverage our technological investments. To that end, there is additional functionality available within AutoCAD Electrical that we havent implemented yet. For example, with the open API, we can create a custom application to extend the functionality to automate our BOM process even more. Additionally, there always are new tips and tricks to be learned about how to best use the software, so we continue to invest in education and have our engineers attend training seminars, concludes Meyer.
By reshaping processes within the electrical engineering department and finding the right technology to support those changes, R.A. Jones has been able to produce higher quality products in less time. As a result, it can face the challenges of 21st century manufacturing head-on and pass the test with flying colors.
Kenny Dunhoft is senior electrical CAD designer, Electrical Controls Group, at R.A. Jones. To learn more, visit www.rajones.com.
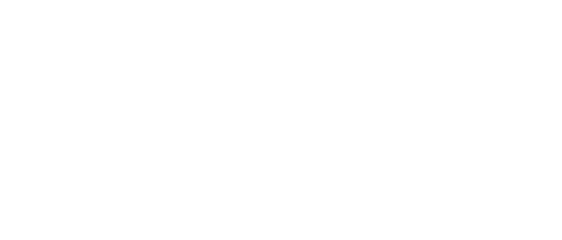
Leaders relevant to this article: