To view charts of the 2007 Salary Survey Findings, click here.
By Mike Bacidore, managing editor
Credit cards. Drivers license. Membership cards. Photos of loved ones. Debit card. Business cards. Your identity is in your wallet.
Sure, cash is in there, too. You have what you need, but the number of dead presidents in your billfold isnt necessarily indicative of who you are.
Our 2007 Salary and State-of-Mind Survey results indicate that your job is a lot like your wallet. A machine control professionals identity is not defined by a $77,325 average salary as much as it is by challenging work and appreciation for a job well done.
The pat on the back, whether it came from a supervisor or from the customer, continued its four-year climb in our survey as a motivator. In fact, almost a quarter of respondents (22%) said it was the factor they respond to best. Salary/benefits (16%) failed to rebound from its steady decline in importance over the past five years and may soon fall behind job security (12%), which made the biggest jump in standing this year. Topping the list once again though was challenging work (42%), which is why so many control designers became engineers in the first place.
My job allows me to invent, says Chris Mitchell, mechanical design engineer at Merrick Machine Co. in Alda, Neb. I design machines for the door industry. I recently designed a machine that does all the machining of the door and kicks it out pre-hung in about 42 seconds. Its a machine that does its task pretty well. We make a lot of custom equipment for the building industry. Nothings the same, but you need the same results.
Differentiate Your Work, Differentiate Yourself
Custom work is at the top of many designers wish lists, primarily because it allows them to try out new technologies in real applications. And while the project is inherently more challenging, it also can have a positive impact on salary and job security.
As an engineer, you grow in stature and pay within your organization by virtue of your experience, says John Challenger, CEO of Chicago outplacement agency Challenger, Gray & Christmas Inc. That makes you more valuable. One thing that is occurring now is that knowledge is growing so quickly that you might very well have middle-career engineers who have been working on projects that didnt use the latest technology and they become less valuable. Because of the speed of the technology, that gap can widen very quickly.
Keeping up with the latest technological innovations can be what financially separates machine control professionals in mid-career. Our survey results indicate that respondents with 11-20 years of industry experience earn roughly the same salary ($80,989) as those with 10 additional years of experience ($80,635). That plateau might be the outcome of younger engineers who keep up with the technology and older ones who dont. Familiarity with new innovations is never more apparent than it is in rookies who have just earned their diplomas.
It can be challenging to keep up with the younger engineers fresh out of college, says Charlie Ramsey, electrical/controls engineer at Harris & Bruno Machine Tool Co. in Haltom City, Texas. But experience counts. At my previous job, wed hired two engineers out of the University of Texas at Arlington. They were nice young fellows and when it came to theory, they were sharp. But they had no actual experience. Theres a difference between theory and how it actually works. But you have to constantly keep up with the technology, like protocols for PLCs, because its always changing.
Double-Sided Cutting Edge
That willingness to continue learning cutting-edge technologies has its financial rewards, but it can have a downside, too.
The speed and breadth of the technology are why you see more people who become specialists in a particular area of technology, says Challenger. While specializing in a particular area might make you more valuable, the risk is that if the project ends or you lose your job, then you might have to move to where the jobs are for your area of expertise.
Such is the lot of Machine Builder Nation in an age of outsourcing. More than half of survey respondents (54%) said their companies outsource some automation/engineering services. Yet the majority (55%) are not concerned about job security and an overwhelming number (94%) indicated they are satisfied with their jobs.
I have a good group of people I work with, says Fred Pisto, senior applications engineer/projects at GL&V USA Inc.s office in Lawrenceville, Ga. I love my job. I cant say enough about that. Weve lost some people, and some of the remaining people dont have the same knowledge of the equipment that we had. But were training them and getting them on board.
Getting on board certainly is no easy task, when the technology changes so quickly, but according to Trade in the Cyberstates 2007, a report released by AeA, a trade association for the technology industry, the engineering and tech services industry added 66,300 jobs in 2006.
Were in a fairly low unemployment environment at this particular time, says Challenger. Demand for skilled engineers is so high that there isnt much of a pool who are unable to find work. Some of the lowest unemployment in the country is for skilled engineers.
To view charts of the 2007 Salary Survey Findings, click here.
Fowler Products
Athens, Georgia
Like many other machine control professionals, Cliff McLeroy is stimulated by the need to stay up-to-date with new technology, but he loves the challenge of his work. Most of our machines are custom, so every one is different, he says. Its always changing, and it never gets monotonous.
He works with 10 mechanical engineers and 12 technicians at his company, Fowler Products, to build capping and cap-handling equipment, primarily for customers in the United States, with a few in Canada and Central America. I go through a project for a new machine, and I set up and design the control panel, says McLeroy. I do the PLC and the touch screen. I deal with the customer directly, and I like the customer contact. The machine has to be installed and run, so we have to make it agreeable to the customer. It needs to work with their existing equipment. I like being creative and finding new ways of doing things.
McLeroy began his career working as an automotive technician for many years. He decided to take his career another step further and earned a two-year degree to become an electronics technician before continuing on at University of Georgia, where he received his degree in engineering.
Harris & Bruno Machine Tool Co.
Haltom City, Texas
Charlie Ramseys 35 years of experience creating solutions for the printing industry is a valuable asset to Harris & Bruno Machine Tool Co., which provides printing and coating equipment to an international list of customers.
My job is to handle all the electrical controls and to call out all the different items wed need to design most of the power cabinets, along with any electrical that wed have to have in the control cabinet and to do the rewriting of the PLC software, he says. We do all of the initial testing here ourselves. Depending on the complexity of it, I might also go out and help on startup if its not too complicated.
More than three decades in an industry brings a lot of training and continuing education, but Ramsey is still diligent about keeping his edge. Ive gone to all sorts of different schools and seminars, he says. If I have a chance to go to a course or a school that I havent been to, Ill usually sign up. I use my AutoCAD training pretty much every day, and were scheduled to go to school for SolidWorks 3D CAD at the end of this year.
Ramsey started his climb up the learning right out of high school when he entered the Air Force. He earned an associates degree in avionics after he studied radar and countermeasures in a 50-week course and earned an associates degree in avionics. By this time, hed developed an itch for learning, and he already knew just how to scratch it.
I wanted to know how things function, he says. I like to design items and circuits and controls.
Once Ramsey left the Air Force, he earned an AA in computer technology from Tarrant County Junior College in Fort Worth, Texas. Hes worked at previous companies where he supervised up to seven engineers, but now hes the sole electrical engineer, working primarily with three mechanical engineers and another individual whos responsible for assembly and testing.
GL&V USA Inc.
Lawrenceville, Georgia
Fred Pisto is a man of many hats. And those hats make him invaluable to GL&Vs Pulp & Paper Group.
Ive always loved science and engineering, he says. When it was time to pick a career, I looked at chemistry, got my degree and went to work. I still love my job. Pisto has been involved with the paper industry for quite some time. His first job after graduating from SUNY College of Forestry on the Syracuse University campus was as a tour supervisor at Hammermill Paper. Ultimately he logged 10 years at Beloit Corp. in Massachusetts before it was acquired by GL&V, where hes been for the past 18 years.
Through the years, hes honed many skills. Ill often go out and do technical presentations with the salespeople, he says. I can handle calls from people who have problems with their existing systems. I also help the service group with service work when there are too many people wanting help and not enough people available. I even get involved with spare parts. Sometimes I receive an inquiry from a salesman or a customer or another engineer in-house, asking me to size equipment and bid it out to one of our manufacturing locations.
The main manufacturing facility for Pistos group is in Canada, but sometimes work is outsourced, not at all uncommon for a company with the size and global presence of GL&V. I specialize in the cleaners the hydrocycling group, Pisto explains. For that, we still use the same two companies we have been since Celleco was acquired.
That familiarity allows Pistos group to concentrate on meeting the customers needs down to the last detail.
Almost every piece of equipment that we sell is custom-designed for each customer, he says. We modify the equipment to fit the customers plant process and layout. During service calls, we will review the customers equipment and discuss any modifications that we feel we need to make to it to make the process more efficient. Then its up to the customer to decide whether to make the modifications.
Multifeeder Technology
White Bear Lake, Minnesota
Being part of the process from beginning to end is a satisfying element of Greg Cabaks job. The sales guys come along with something and its exciting to see the whole process from proposal to development, he explains. Our customers like to come and visit a lot. I used to spend hours and hours on the phone doing tech support, but not now. Im always excited to get hold of some new components every time. I like the testing phase. And Im always aware of the costs. I get to see the whole process from start to finish.
After completing his electrical engineering degree at University of Wisconsin-Madison, Cabak took a job building houses before he started working at Multifeeder Technology, maker of friction feeders, more than 3 years ago.
I have two halves to my jobs, he says. We make panels for relays and PLCs. Well take three or four of our feeders and tie them all together. Theyll want to mount it on a conveyor or two, and well tie all the power together. The other half of my job is designing circuit boards for our equipment.
Cabak loves the work he does with integrated systems and relishes the opportunity to gain more practical experience with mechanical, electrical and software tools. We have one mechanical engineer and one electrical engineer. Thats me. We also have two technicians one custom and one that works on the circuit boards. Several of our sales guys are trained engineers, too. Plus, weve been hiring guys at a higher rate than normal at the whole company in general.
Eagle Crusher
Bucyrus, Ohio
At 9 years old, Ray Kilgore knew he wanted to become an engineer. My grandmother used to sit with me and teach me how to do 3D drawings, he says. She showed me how to draw buildings, and thats when I decided thats what I wanted to do. She was a homemaker, but very artistic.
As early as high school, Kilgore began his formal training for the work he does now at Eagle Crusher, which designs and builds crushing equipment.
I went to Pioneer Vocational School during my last two years of high school in Ohio, says Kilgore. I was certified. Over the years, Ive added some physics courses, technical math and English courses in college. Ive also taken courses in electrical safety, overhead crane inspector, spill convention control and workplace safety. Theyre specific to our job. Part of what I also do is deal with EPA and OSHA. Working with the agencies, dealing primarily with paint, water and environmental issues, takes up about 35% of his job, explains Kilgore.
Along with the job market, wearing many hats and his continuing education are the main reasons why Kilgore feels secure in his job.
The job market definitely makes me feel stable, he explains. Engineers are needed. Its a good place to be. At Eagle Crusher, weve moved into 3D, but its taking a lot more time to get people new hires and veterans alike - oriented to it. Were just switching over to 3D modeling, so were all getting our feet wet.
Kilgores career path has been anything but conventional, yet each turn has allowed him to add to his growing wealth of knowledge. I started at a little factory called Plymouth Locomotives in Ohio. From there I went to Stuart Radiator in California before I came back to Ohio and went to Fezco Tool & Die. Then I did machinery setup for a number of years at McClain Industries. I set up some burn tables and worked with tubing benders, press brakes and cut-to-length lines. From there, I came to Eagle Crusher, where we make rock crushers. The whole rock-crushing industry and its technology attracted me.
Eagle Crusher employs about 10 manufacturing engineers, but no one is classified as a technician and no one is dedicated to design controls. Everybody does a lot of everything, explains Kilgore. I do mostly the tooling and the fixturing here. I design parts for the machinery to support production. But right now Im also doing the scheduling. We all do just about anything thats needed.
Chris Mitchell
Mechanical Design Engineer
Merrick Machine Co.
Alda, Nebraska
The secret of a good mechanical engineer is having good resources, says Chris Mitchell. Everything now is shared. I have programmer/developers here who throw things out on bulletin boards or blogs and discuss it with other engineers. Others have already done it, so why should I reinvent it? You have to know what youre looking for and who to get it from. Once you get the application data, you have to know how to use it. My success in the field has been because Ill spend all the time it takes to understand something.
And Mitchells education and career path has allowed him to become more than familiar with the building industry, which Merrick Machine serves with fabrication solutions.
I was eight years in the military, and they paid for my schooling at UCSD engineering. I took a job as a project engineer in the construction industry, laying out control systems for jails. I have a real good background in pneumatics and hydraulics. At the time they were going to PLC. Now everything is PLC servo-driven, and Ive adapted. Its called application. Plus, I walked right into 3D modeling. A designer can create and know if its going to work before he builds it. Ive had to work twice as hard as degreed engineers.
Merrick Machine employs one manager, one mechanical engineer and one electrical engineer in Mitchells area. The tight, flexible group allows the company to customize what is needed. We do a lot of custom stuff, which has to be engineered every time, says Mitchell. We have a few installers, and they call us when they have to put something together because its new. Its custom. I design a machine center and put all the drawings on the floor for fabrication. They build it. I troubleshoot it. If it works, it goes out the door.
Like so many others, Mitchell wears more than one hat, too. Youve got to wear a lot of hats, he says. Its not uncommon for me to design one day and go out and weld the next day. Ive also gone out into the field and repaired machines. That also gives me job security. There are a few jobs available, but theyre not abundant. I like what Im doing, and I like where Im at. I do what I want to do, and I answer to the owner. And that is worth its weight in gold.
Dennis Gibbs
Applications Engineer
Holland LP
Crete, Illinois
With 37 years experience as an engineer, Dennis Gibbs has accumulated a wealth of knowledge, but he worries about the future. The real problem is that there are not qualified engineers to be found easily, he says. Finding young engineers to take over for us Boomers is a real tough job.
Gibbs finds that the up tick in the economy and the improved job market impacts him directly at Holland LP, which primarily serves the rail industry. The extra work is stressful, but it does make for job security if the company wants the job done, he explains. And that means wearing a number of different hats all at the same time.
One of Gibbs main roles is to design the most cost-efficient piece of equipment that his customer desires. I design both full systems and component parts of systems, basically the mechanical and hydraulic end with some electrical, he says. We employ mechanical, electrical, industrial, project, managerial and application engineers.
And what led Gibbs down the path he chose? I was enrolled in mechanics school and kept wondering why things were designed the way they were, he explains. So, I went to engineering school and found out why. After earning his BS in aerodynamic engineering from the Aerospace Institute, Gibbs worked for Douglas Aircraft in California. Returning to Chicago, he gathered experience with a hydraulic punch and shear manufacturer and then went on to work on overhead cranes and crystallizers before beginning his tenure in building machines for the rail industry.
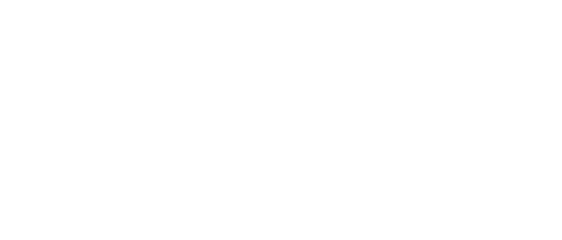
Leaders relevant to this article: