We’ve used steppers in our machining centers for a long time, and micro-stepping has helped us achieve better resolution along the way. Our problem is that we now have to operate more slowly to achieve accurate positioning. Are there advantages in changing to AC servos that are worth the extra cost? Any tips to pass along?
—from May ’07 Control Design
ANSWERS
Accuracy, Volume Warrant Servos
Stepper motors have extremely high torque, but only when deflected from their target position by nearly a full detent position. Micro-stepping can give greater resolution, but under load won’t deliver the accuracy often advertised or the accuracy of a closed-loop servo.
A servomotor can deliver full torque with little or no deflection by using the Integral Compensation in all servo control loops. It’s best to use a servo with reasonably high encoder resolution, but nothing approaching micro-stepping resolution. This is because with friction or loading going on, you won’t get the benefit of the resolution advertised for the micro-stepped step motor.
Servomotors vary in effectiveness in machine-tool applications. Typical machine tools use large ball screws, reflecting high inertia to the servo motor, so be sure to choose a high-inertia servomotor. This can be counter-intuitive because motor manufacturers advertise low-inertia servos as being more advanced or better. In many applications they are better, but not in machine tools.
If you mount handles on the rear shafts of the motors, it’s better to make them as small as possible when using servos. The added inertia of the handle will work against you for controllability.
Bear in mind that it’s a common misconception that high-inertia motors are better because they have a lot of inertia. In fact, they’re better because they have a large diameter rotor that gives the magnetics better mechanical advantage.
High inertia is a by-product of this construction, and shows the motor can perform against large or high-inertial loads. You wouldn’t want to add inertia to the back of the motor, thinking that you’re making a higher-inertia or better motor.
Because servos typically are more expensive than steppers, deciding whether to switch must consider two factors. First, the servo will offer greater accuracy under heavy loading. If greater accuracy is required, then you need a servo. Second, the servo is faster, and will make the machine more productive by quadrupling traverse rates. It’s not difficult to find out how soon a servo will pay for itself. If the machine is seldom used, servos won’t be worth it. If the machine is used all the time, servos will be a great investment.
Robert Bigler, CEO,
Animatics, www.animatics.com
AC Servo Has Smaller Footprint
Yes, there are advantages of using an AC servo versus a stepper, but don’t just look at cost. Look at the savings associated with the smaller footprint of an AC servo. This smaller footprint also will give you lower weight, which can be advantageous depending on the application. It might also allow you to make the overall machine smaller.
For performance, an AC servo is the right solution. It will cost more, but the throughput gained might be worthwhile. You mentioned that you need to run at a lower speed to achieve positioning. The advent of high-resolution feedback devices makes low and high-speed operation more feasible. A common feedback resolution used to be 1,024 lines/rev (4,096 counts post quad). Now, a typical absolute feedback device has 17 bits of resolution or 131,072 counts per revolution.
This higher resolution allows a tighter velocity loop, increasing system bandwidth and letting you settle into position sooner. Your circle, diamond, and square test will never look better.
An AC servo’s drawback is its lower rotor inertia. But, since you can use a higher resolution feedback device with increased bandwidth, you can have a higher load/rotor inertia mismatch.
Pat Berkner, product manager, rotary servo motors,
Parker Hannifin, www.parker.com
Feedback Can Be the Difference
The choice is between a stepper with a micro-stepping drive and a brushless servomotor with sinusoidal commutation. Both are AC synchronous motors, but one is controlled without feedback.
When is the extra cost and complexity of a feedback sensor with its associated circuitry worth it?
First, the feedback sensor permits the motor to always run at a torque angle of 90°, yielding the maximum torque per unit current. With an open-loop stepper, the general rule of thumb is not to exceed a 30° torque angle in normal operation, so that you always have a 2:1 torque margin for unexpected events. This means you’re always planning to get less than half the maximum torque per unit current. So, an open-loop stepper will run much hotter for a comparable size, or probably would have to be sized considerably larger than a brushless servomotor.
Second, you have to be more conservative with an open-loop stepper because a momentary problem can lead to an unrecoverable error that the controller doesn’t know about. Using feedback gives you greater confidence when pushing the system to its limits because you know it can detect and recover from a momentary disturbance.
In one sense, an open-loop stepping system really isn’t open-loop because there’s a feedback loop in the motor’s electromagnetics. But this feedback loop really applies only to proportional gain between the commanded step/microstep setting and the physical position of the rotor.
There’s no integral action to overcome steady-state errors, and there’s virtually no derivative action to provide damping. Continuous high currents are required to minimize steady-state errors without integral action, and very small micro steps are required to minimize ringing effects. In a servo system, it’s easy to add integral and derivative action to optimize feedback loop performance.
Curt Wilson, vice president, engineering,
Delta Tau Data Systems, www.deltatau.com
Horsepower Dictates Choice
Typically, steppers work well at about 1 hp or lower. If the application requires more hp, the servo’s functions and price will look more attractive.
A stepper typically is selected because of cost. Because it has a lot of torque at low-end speeds, a stepper can respond fairly well to high accelerations with the latest drive technology improvements.
If the application can’t accommodate a stall, then a stepper shouldn’t be used. Even when the motor is properly sized, the stepper can’t recover from rotor stall. The motor must be stopped/reset, or the drive needs to detect stalls and reset itself.
The drive definitely doesn’t respond well to a torque spike, which can cause the motor to go into a rotor stall. This is a case where it’s advantageous to use servo technology—and worth the extra cost.
Stepper motors can achieve very accurate positioning in applications with low speed and torque requirements. They don’t require an encoder in some cases, and if the system is well-designed they’ll maintain positioning by homing in to zero out backlash or compensate for positioning error.
Michael Perlman, business development manager,
Siemens E&A, www.siemens.com
Analyze the Total Value
The wide power range of AC servo drives and motors at various supply voltages offers excellent flexibility for machine builders. AC servos provide higher speeds of 5,000-8,000 rpm for faster rapid traverse rates for ballscrew and rack/pinion axes. Work with a precision gearbox supplier, who can handle high-speed motors, and provide the backlash specifications needed for your application.
Using high-resolution, 2M counts/rev multiturn absolute encoders and servomotors designed to reduce low-speed cogging provides smooth feed rate move performance to hold tighter tolerances.
While steppers have progressed from open-loop stepping to micro-stepping to optional closed feedback to precise absolute feedback, they often remain separate islands of control indirectly accessed by the machine’s main control system.
One OEM recently improved its longstanding machine by upgrading the setup axes from 50 steppers to integrated servos handling nearly 100 axes. While it cost $400 more per axis, a value analysis showed it was the right thing to do.
Brian Fieseler, program manager,
Rockwell Automation, www.rockwellautomation.com
Price Versus Performance
There’s an overlapping area where steppers and servos compete, and advantages each can give to a machine. The choice comes down to price versus performance.
Figure 1
Stepper vs. servomotor performance curves
To compare steppers and servos, you can search literature and plot performance curves. For example, a typical servomotor providing 3 lb-ft (35 lb-in or 4 Nm) of continuous torque is in a 3.5-in. (89 mm) square package. A stepper providing similar torque also is available in a 3.5-in. diameter package. Plotting the performance of these two motors results in the curves shown in Figure 1. Even though both provide the same continuous torque, their performance is vastly different. The servomotor has higher speed range, higher continuous torque over a wider range, and much higher acceleration torque ability.
Finally, the stepper manufacturer will advise against operating near the line defining the performance area. Allow a safety factor—some suggest up to a 20% margin. Meanwhile, the servo manufacturer will suggest considering ambient temperature when operating near the line of the continuous range.
Improvement in machine accuracy becomes possible with servos. A servomotor’s feedback device enables tight repeatability and higher accuracy. This means servos can position rapidly within the diameter of a human hair, and do it every time. Controllability and accuracy mean better part quality and customer satisfaction. The extra cost is justified.
John Mazurkiewicz, product marketing manager,
Baldor Electric, www.baldor.com
Step-Motor Upgrade Can Be Costly
A step motor operating in all step modes has excitations caused by each step that can translate to the load. Even with micro-stepping for smoother operation, special care must be taken to avoid the resonant characteristic of the motor/load combination. Remember that no matter how small, the individual perturbations are still there. If your load has sensitive equipment that’s subject to resonance, a stepper might be out of the question.
The smooth motion of a sinusoidal commutated brushless servomotor doesn’t have this limit. Certainly, there are methods that can improve the performance of a step motor, including feedback addition or even complicated commutation algorithms. But, by the time these methods are implemented, you’ll likely have exceeded the cost of the most expensive servo amplifier systems.
The servo amplifier is accurate and repeatable, whereas a stepper is repeatable but not accurate. The typical stepper motor has no feedback, and has tolerances that vary from motor to motor.
The stator positioning in the housing or the lamination stack positioning is critical. The stamping or machining of each tooth in this lamination stack also will affect each of the steps. This will move the tooth relative to the motor mounting. This is called the cardinal step, and most motors are set with 200 steps/rev at full or cardinal step moves. Repeated homing would be necessary to ensure accuracy. Mapping would help further.
With a servomotor, there are feedback options such as BISS or ENDAT that allow homing once on initialization and storing this encoder position for future reference in non-volatile memory for all subsequent power-ups. The encoder also allows the actual rotor position to be accurate.
Lee Stephens, motion control engineer,
Danaher Motion, www.DanaherMotion.com
Closed-Loop Steppers Could Be the Answer
Hybrid step motors are high-pole-count, brushless, permanent-magnet motors that can be driven in open- or closed-loop conditions. A closed-loop stepping motor and driver package such as AlphaStep from Oriental Motors doesn’t misstep when subjected to rapid velocity or acceleration load changes. An internal rotor position sensor constantly monitors rotor position.
If the rotor’s position deviation is less than 1.8° (within +1 step), the motor driver will use open-loop, micro-stepping drive techniques. If the rotor’s position deviation (error) is greater than 1.8°, control switches to closed-loop operation, and adjusts the energized stator winding to correct the rotor position (error) to less than 1.8°.
Gain tuning in servos can be critical, troublesome, and time-consuming. AlphaStep, for example, operates like a step motor most of the time, so there are no gain-tuning requirements.
Dan Jones, president,
Incremotion Associates, www.incremotion.com
Micro-Stepping Better for Robust Apps
Most micro-stepping challenges arise from sizing a stepper properly to the load inertia. With steppers, we look at the peak torque from the application, and select a stepper motor that has twice the torque at the given application speed (100% torque margin). Servos typically are selected with a 15% torque margin at the given application speed.
Load-to-motor inertia ratio also must be considered. For stepper applications in which it’s necessary to follow the commanded signal fairly closely, the load-to-motor ratio should be 1 to 1 (J load/J motor = 1). This should give sufficient pull-in torque for starting and stopping accurately. Micro-stepping is required for robust applications as this smoother, quieter method provides more torque at higher speeds. For less robust applications, this ratio will increase because ranges are typically J load/J motor = 1 to 10.
Changing load conditions such as masses, forces, and speeds can yield impulse spring effects, and the stepper’s torque margin can be compromised to some lower value. Our initial selection of a motor with two times the available torque still could lead to loss of synchronism through missed position counts.
Robert Swalley, application and support engineer,
Beckhoff Automation, www.beckhoffautomation.com
CNC Systems Allow Use of Either
The information available from servos about position and current can create valuable benefits versus a stepper system when used in a machining center.
High-feedback resolution enables the servomotor to follow the setpoints with precision, whereas the precision of a stepping motor is limited to the distance between two micro-steps. Jolts between the steps introduce resonant frequencies in the stepping motor system, which can influence the finish of the machined part.
Servos can go any speed from fast to slow with the same precision. By contrast, a stepping motor creates a tradeoff between speed and precision. Servos also offer superior acceleration and deceleration during machining due to higher overload capability for servo and stepping motors of the same nominal torque rating.
Position feedback provides continuous information about the lag between set and current position of the motor. Current feedback provides the load status of the servomotor and drive. These two data points can help detect machine collisions and motor and drive overload conditions. High-resolution tracing information can help remotely diagnose any motion or fault condition of a servomotor. Transparent integrated systems for CNC, PLC, motion, and HMI offer the possibility of diagnosing machine parts from one access point.
Information about the current in the power stage of the drive and the motor can help build temperature models. These can be used to self-protect motors and drives from overheating.
Scalable CNC systems that offer the possibility of working either with servos or with steppers depending on the end-user’s machine requirements definitely have an edge. This is because one can select the right solution without rewriting all the software in order to accommodate two separate systems.
Markus Sandhoefner, sales manager,
B&R Industrial Automation, www.br-automation.com
October's Problem
We measure a few process variables on our plastics processing machines, including temperature and pressure. We use these variables for both real-time control and monitoring. What are the challenges and benefits of upgrading these instruments from 4-20 mA to smart instruments with digital communications? Is there a benefit I can promote to customers? Is support another learning curve for us?
Send us your comments, suggestions, or solutions for this problem. We’ll include it in the Oct. ’07 issue, and post it on ControlDesign.com. Send visuals if you’d like—a sketch is fine. E-mail us at [email protected]. Please include your company, location and title in the response.
Have a problem you’d like to pose to the readers? Send it along, too.
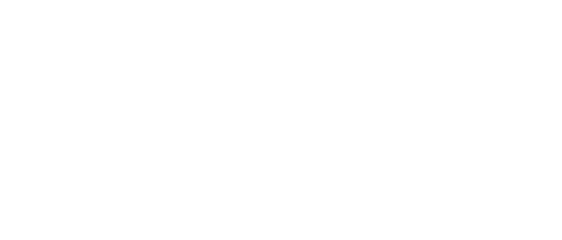
Leaders relevant to this article: