Jeff Hoch is a freelance journalist specializing in science, environment, and technology issues. He can be reached at [email protected].
For troubleshooting, preventive maintenance, software upgrades, or connectivity to enterprise-level applications, the web-enabling of industrial machines might seem like an obvious must-have technology option that adds relatively little to the purchase price of machines. Indeed, a growing percentage of industrial machinery builders already provide web connectivity as an option or standard feature, with more industrial original equipment manufacturers (OEMs) jumping on the bandwagon every year.
But the actual end uses of the technology vary widely, and many potential customers are reluctant to embrace web-enabled machinery. At the machine level, much of the impetus for web-enabling has been a function of OEMs providing technology to end users, rather than strong demand from customers to OEMs.
Tough Communication Constraints
Fluid Air Inc., manufacturer of process equipment for pharmaceutical companies, only recently began to build some of its equipment with technology to elevate machine-level data to higher systems. The Aurora, Ill.-based company has incorporated Ethernet-capable processors and single-point I/O with its fluid-bed coater/granulator/drier and its high-shear granulator, as well as in the retrofits of pharmaceutical process equipment made by other manufacturers.
We're not getting directly pushed in this area, says Jim McAndrew, director of control technologies. We're not having people come up and say, 'I want to be able to view machine data on my web browser.' Rather, people were making observations that it is a real bear getting information from each piece of equipment.
The pharmaceutical industry may not be a good example of industries that rapidly embrace new technology — it's a notoriously slow adopter of computer-based technologies, partly because of regulatory restrictions. For example, explains McAndrew, quality assurance personnel, with somewhat limited access to the plant floor, traditionally have gathered process data through a laborious patchwork process before taking the information off the plant floor for analysis. Fluid Air is working with customers to develop strategies to gather manufacturing information for use both in the factory and elsewhere in the enterprise while still complying with regulations.
We're collecting an awful lot of data on the equipment, but all of that is in the manufacturing area of the pharmaceutical plant, where only certain people are even allowed to enter, McAndrew says. So for us, web technology is about getting that information out to a larger corporate audience. That helps our customers improve their business by having access to all this data we gather, but it's data that very often gets very dusty and unused back there on the plant floor.
Providing the data in a usable format has been a stumbling block for Fluid Air and its customers. For many years, a lot of vendors, not just ourselves, have been putting data in SQL format, but that only takes you so far, McAndrew explains. You've got access to the data, but unifying that data between the equipment vendors and then the quality (system) vendors has presented an issue. We have a lot of interest in the work that's being done by the World Batch Forum with its XML schemas that might give us some third-party definitions for sharing data back and forth in XML format between big ERP systems, laboratory systems, and our plant floor data.
McAndrew says the addition of web-enabling technology has been well received by end users thus far. By essentially making their machines web servers and serving their data in a web-enabled format, we've been able to offer our customers a solution, without having them invest in a bunch of new software, he explains. They can use their web browsers and just buy one server. They don't have to invest in new infrastructure because they have the plant-floor Ethernet now and, of course, they've always had the business Ethernet set-up.
Real-Time Remediation
Much of the vendor community is backing the premise. By providing a real-time view into machine performance, industrial OEMs can greatly increase customer satisfaction and repeat business, notes Kevin Roach, vice president of global solutions business with GE Fanuc Automation. When support personnel receive calls but don't have access to real-time data, each call is often treated as an emergency because the service organization is flying blind--even though the problem may be minor or have a simple work-around." The wrong expert might be deployed, or the right technician might be sent out with the wrong replacement parts, increasing mean time to repair (MTTR). That causes customer dissatisfaction.
There is definitely a need and a movement toward importing low-level information up through the infrastructure, says Glen Taylor, PE, product manager with Berkeley Process Control. I guess everyone would say that we need and want the technology to move [data] across the web, but it's shrouded in security concerns and other issues like that. One such issue faced by Berkeley's semiconductor industry customers is standards development, such as trade organization Sematech's e-diagnostics initiative.
Reluctant Audience
Some end users are reluctant to let even their industrial OEM partners have access to their machinery data, and often forgo potential benefits of having communications capabilities on the equipment.
McKinley Machinery, a builder of corrugated box converting equipment, has installed modems on every piece of equipment made in the past four years, so McKinley technicians could remotely assist with software upgrades and diagnostics. Three years ago, McKinley gave customers the option to add wireless Ethernet with handheld remote control. Although interest is high among sales prospects, customers still express concerns about using the technology.
I'd like to go real web-based, says McKinley chief control engineer Greg Sachs. The obstacle has been to get people to plug the machines into their internal networks and then tell us where it is so we can connect to it at any time.
Sachs believes end users may not be fully using the available technology. As an example, he cites his equipment's rubber blades that spread ink for flexo printing modules. The blades need to be replaced about every 100 hours of run time, and the machines themselves could reliably generate a signal to do the required preventive maintenance. But many end users have been reluctant to connect the equipment to the manufacturing systems.
People still seem to think if I put a machine or process on the web, I am exposing my entire revenue stream, my entire business to some hacker, whether it's intentional or unintentional, notes Jeff Jervah, U.S. manager for automation product marketing for Schneider Electric. Web-enabling something does not necessarily mean putting it on the World Wide Web. It means using Internet technologies to allow access to information that comes from those devices that can be accessed on a corporate intranet or, with the proper security and tools and permissions, on the World Wide Web.
Potential Cost Savings
The suppliers say a simple cost-benefit analysis shows companies that do purchase machine-level, web-based communications capabilities--and actually use them--are finding considerable operating cost savings in multiple ways. Jervah says adding an Ethernet web server module to a Schneider Electric PLC along with some minor programming would most likely add only a few thousand dollars to the cost.
For less than $10,000, you've web-enabled an entire PLC control system, he says. Whether you're producing shovels and you have a line that's been down for a couple of hours, or you're manufacturing microelectronics equipment and you're down for two or three hours, that $10,000 pales in comparison to the lost productivity during that time frame.
Additional savings can be realized in the routine maintenance of the control system, plus the less tangible benefits of having ready links to user manuals or spare parts lists. If I, as a value-add machine builder, have made some optimization in the code and I want to provide it to you, I don't have to fly somebody out; I don't have send it to you on a disk or by e-mail; and we avoid having your people bring the system down if need be, or make an online security change, Jervah argues. With the right security access, I can do that from a remote location and provide that optimization, whether it's code changing that leads to the optimization or simply some tweaking after start-up or after the system has been running for a period of time.
Here's the Sales Pitch
Littell Intl., Addison, Ill., uses GE Fanuc PLC controls in its specialized tinplate shear machinery, which makes extremely accurate, high-speed straight or scroll cuts in coils of steel or aluminum for can manufacturers. By connecting a PC to the PLC through a TCP/IP Ethernet card, Littell's customers can exchange data both across the enterprise and among devices. The result for Littell customers has been enhanced real-time decision-making capabilities and productivity.
We want to offer our customers a flexible system than can be customized to meet their needs, says chief electrical engineer Jeff Mazrimas. This new web-based control platform helps us do that cost-effectively and efficiently.
But getting that message across to end users isn't easy. When Ormec Systems Corp. started putting TCP/IP connections on its PC-based motion control equipment in 1995, sales reps didn't even pitch it to customers. The web was still in commercial infancy, and TCP/IP was just emerging as a leading communications protocol, so neither was much of a selling point at the time.
Ormec did, however, tell its users the advantages they would get. They would have multiple communications channels open to the controls; they could debug and send data while the machine was running; and they could upload and download files over a single link at the same time. It wasn't so much that we sold them on the technology, recalls David Carr, vice president of marketing and development for Ormec. We just told them what the features were and they loved it. Virtually nobody asked how we did it.
One of those early adopters was an end user with multiple manufacturing plants replicated across the country. Debugging and diagnostics were less of an issue for the company than software maintenance and production reporting. Whenever they had a machine software update or had to generate daily production reports, they would go out on their Ethernet-based intranet and gather the data or send those updates, says Carr. The guy who figured out how to do all of that became a very big hero, because it had been a big maintenance problem for this customer. If you can take new technology and save your company money, that advances your career.
Or it advances your customer base. That's a valuable message machine builders can bring to their customers. Roach notes that end users may opt to have the machine builder become more closely involved with managing a machine or process, such as through maintenance subscription services.
Control the Control Options
Most intra-organizational data-sharing that does not involve direct manipulation of control parameters is easily the most pervasive use of machine-level web technology. Security issues mentioned earlier are perhaps the biggest stumbling blocks for many end users to embrace most any element of control of critical manufacturing machinery.
HMI vendors such as Rockwell Software offer products that let end users choose between read-only displays and remote controlling capabilities. Rockwell Software's RSView32, for instance, may be had in a web server version that does not permit modification of control settings from remote locations.
Someone on the Internet cannot make changes to the process and start or stop things, explains Darryl Walther, product manager for visualization business at Rockwell Software. As a read-only system, there are no control implications at all.
Wireless May Have a Place
Some end users of web-enabling technology are finding that wireless access to machine data affords them more value than hard-wired connectivity.
A lot of times, wired networks cannot be deployed due to confinement issues or harsh environments such as excessive heat or water, says David Crump, communications specialist with Opto 22. Wireless also avoids the cost of dropping land lines, which, if they're not already in place, are a substantial cost.
Opto 22 recently partnered with Swedish wireless-technology giant Nokia to develop a cellular-based communications system that can connect factory-floor machines, storage tanks, or other equipment to manufacturing or enterprise computing systems. Thus far, no industrial OEMs have embraced the technology, but Crump claims end users have begun to use the system on their installed equipment.
Despite numerous advantages to both the machine builder and end user, the future use of web technology on industrial machines may continue to be a slow upward climb.
The future use of web technology for hard control of machinery is less promising than its use for monitoring purposes. Vendors and users alike seem cool toward the notion that machine control from remote locations might be as commonplace as some technology vendors and media pundits have forecasted.
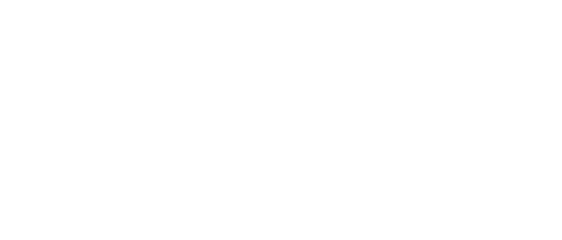
Leaders relevant to this article: