PLCs have long been the control platform of choice for industrial OEM machinery. These workhorses have performed well for years and are ubiquitous across the OEM landscape. Nevertheless, new factors are coming into play that make PCs a compelling choice for many monitoring and control tasks. Applying a PLC to a task suited for a PC can result in a complex, expensive, and high-maintenance control system.
Cost Plus
PLCs are often considered the low-cost option, but machine control and data-handling requirements often make a PC the economical choice. “None of the PLC manufacturers we contacted could provide the motion control [with linear interpolation], recipe storage, and OI requirements within our budget,” says Tim Burnier, vice president of engineering, Research Automation, Aurora, Ill.
While Research Automation manufacturers various types of machinery, this example focuses on their seal trimmer. The seal trimmer has seven axes of motion with about 50 I/O. Two encoders (in addition to seven associated with the motion) are used to monitor tool holder location. Recipe storage requires capacity for 1,000 part numbers, and each number has about 75 variables associated with it. The operator interface has more than 50 screens customized to each application and customer.
PLCs were not only expensive for this application, they also needed multiple platforms. “And we were concerned about the robustness of the drivers used for communication among these platforms,” notes Burnier. The PC solution allowed control, data handling, and operator interface to be executed on one platform.
Research Automation chose an integrated operator interface and motion control PC-based solution. “Eason Technology provided, installed, and configured an operator interface (OI) with a Galil seven-axis PC/104 motion control system. The OI software included the drivers required to share variables with the motion controller,” says Burnier.
High Speed Demands a PC
That's not a misprint. PLCs have always been thought of as the first option for real-time control of high-speed applications, but this is a misconception. “There is a perception that PLCs are hard real-time controllers with scan time deviations of less than 100 microsec., but this isn't the case,” says Nat Frampton, president of Real Time Development, Pearl River, La. “In today's real-time operating system discussions, the PLC is classified as a soft real-time system.” Real Time Development provides system integration services to OEMs.
Very-high-speed applications require dedicated control boards that plug into the PC bus. PLC scan times are neither fast enough nor deterministic enough to handle such tasks. “PCs provide the speed required by applications such as quality rejects of discrete parts, high-speed sortation, and many motion control applications,” says John Nesi, strategic marketing manager, Rockwell Automation.
I/O scan times are one of the key speed requirements for a control system, but processing of I/O data is also important. “A PLC could perform the machine sequencing [without problem], but could not come close to the speeds required to interface to high-speed, on-line sensors,” reports Michael Iaquinta, vice president of tobacco operations for Automation and Control Technology, Columbus, Ohio. ACT makes custom precision measurement systems for the tobacco and metal industries. "The PC also allows us to add I/O without impacting processor speeds."
Another important speed requirement is data handling and manipulation. This is an area where PCs excel. “PLCs simply do not have the high-speed arithmetic and data handling capability required for our application,” says John Wargelin, director of operations for Pile Dynamics, Cleveland. "A PLC could control the pile driver, but for the high-speed, data-intensive tasks, we needed a PC." The company's pile driver analyzer monitors movement, acceleration, and force of pile drivers.
Pile Dynamics worked with Applied Data Systems to implement a PC-based solution running under Windows CE. “Specialists like Pile Dynamics can encode their vast know-how into a rugged device that can be used by a construction worker at the site,” adds Larry Ricci, business development manager for Applied Data. "For end users, it is like buying a world-class Ph.D. consulting engineer in a box."
One Platform for a Total Solution
Many OEM control systems must perform three functions: machine control, operator interface, and communications to other computing systems. PLC-based systems often employ a PLC for control, a graphics terminal for operator interface, and a PC or other protocol translation device for communications. A PC can perform all three of these functions in many machine control applications.
Hadley Design, Edmond, Okla., builds robotic medication-transfer systems, often using a PC to perform multiple functions. “The PC communicates to a robot, to an automated medication-retrieval system, and to a thermal identification tag printer,” says CEO Jeff Hadley. "The PC must also communicate via Ethernet to a separate computer system for data backup, to a pneumatic tube system control computer, and to Ethernet I/O."
System control and monitoring is via Entivity Think & Do software running on a flat-screen PC. “The system provides a user-friendly graphical operator interface, the ability to communicate across multiple platforms, and ease of connectivity,” adds Hadley.
Tri-Tec/GSA, Tecumseh, Ontario, and Germany's GSA GmbH are automation system OEMs that offer a variety of material handling solutions to the industrial market. Tri-Tec switched from PLC to PC control. “The PC solution gives us a hardware solution that includes a processor, HMI screen, and programming device all rolled into one,” says Bill Laing, a computer programmer with Tri-Tec. "With a PLC, those items were purchased independently, significantly driving up the cost."
Tri-Tec’s multicell linear and area gantry robot system is programmed in a flowchart language well-suited to PC-based control. “Flowcharting allows easy definition of distinct functionality and is understandable to a wider percentage of the work force,” says Laing. "As the workforce rolls over, programmers will be able to use higher-powered languages to best handle machine functionality and also the data handling and report generation demanded by today’s customers."
Another OEM decided on PC-based control because of single-platform capabilities. “The PLC solution was considered, but a PC running an HMI and a Visual Basic application would still be required,” states John Foreman, R&D engineer, Optical Dynamics, Louisville, Ky. "The VB application is needed to perform database look-ups from a remote data host." Optical Dynamics makes optical lens production machinery.
A PC was able to handle all tasks required by the control system: machine control, operator interface via a custom VB application, database management with VB, and communication to another computer. “The fast development time, simple programming, and tight integration with the VB application made this a fantastic approach,” adds Foreman. "The tag-based addressing and flowcharting made the program so simple that even the mechanical engineer on the project could read, understand, modify, and troubleshoot with ease."
Optical Dynamics used Steeplechase visual logic control and Phoenix Contact Interbus-S I/O. “The easy connectivity to customer computer systems, the availability of high-level programming languages, and the flexible architecture made the PC-based control solution most attractive,” concludes Foreman.
PCs Preferred
PC-based control systems can be easier to pre-test and debug for certain applications. “With PC control, the operator interface and most of the control functionality could be tested without being connected to the system I/O,” says Tim Jager, controls engineer with DMC, Chicago. DMC performs system integration for a variety of OEM applications.
For one project, the customer’s plant ran continuously, so downtime had to be limited. This necessitated off-site debugging. “We used Think & Do with Ethernet I/O to control a pallet-routing machine,” adds Jager. "Software development, I/O checkout, and debugging would have been more difficult with a PLC-based system, and likely would not have allowed us to meet the schedule."
Another DMC project automated a test stand for a manufacturer of carbon monoxide detectors. DMC used National Instruments LabView software running under Windows to control the system and interface to serial test instruments. “Complex data must be passed to three different serial test instruments for controlling and measuring gas concentrations,” says Leon Grossman, controls engineer with DMC. "These instruments require communication strings that would be difficult to implement in a PLC. The queuing logic was another requirement not suited to PLC control."
Sheffield Measurement is a manufacturer of coordinate measuring machines. Sheffield is owned by a firm that makes PLCs, but they prefer PC-based control. “Our measurement processor (MP) originally ran on an Intel 8086, an 80186, a 486, and then a cost-reduced version on a 386,” says Robert Brandstetter, PE, senior design engineer with Sheffield in Dayton, Ohio. "The MP does all machine interfacing as well as all real-time processing of critical tasks in the microsecond range."
Sheffield has been running the MP software on a computer for more than 30 years, so the company invested a tremendous number of man-hours in perfecting computer-based control. Porting the software to a PLC would be time consuming and fraught with risk. Speed requirements also dictated the use of a PC.
PLCs Perform the Basics
The reasons for using PC-based control are numerous and often esoteric. The justifications most often cited by OEMs for PLC control are few and basic. According to many industrial machine builders, PLCs are still the best in terms of cost, size, and reliability. These factors are of critical importance in many machine control applications.
Day-old news is not worth the paper it's printed on, so newspaper printing is an application where reliability is absolutely critical. “Our printing presses are in a 'must-run environment' because the time window for printing a newspaper is less than four hours,” says Jan Lindstrom, vice president of technology, KBA North America York, Pa.
Given enough time and resources, a controls engineer can do just about anything. This includes shoehorning a PLC into an application suited for a PC, or vice-versa.
However, in the real world of financial and time constraints, it pays to use the control platform that fits the application. Across various OEM applications there are very specific factors that drive the PC versus PLC decision.
PLCs have long been the control platform of choice for industrial OEM machinery. These workhorses have performed well for years and are ubiquitous across the OEM landscape. Nevertheless, new factors are coming into play that make PCs a compelling choice for many monitoring and control tasks. Applying a PLC to a task suited for a PC can result in a complex, expensive, and high-maintenance control system.
There is a host of reasons why PLCs are the best control solution for KBA’s printing presses. “We use PLCs because we can combine different PLC models from GE Fanuc and use the same code,” adds Lindstrom. "Training of service personnel is simplified because of their familiarity with PLCs." Lindstrom says PLCs can use the same code over a number of years because PLC manufacturers are very good at managing life cycle compatibility.
KBA engineers also feel PLC networks are more reliable and predictable than their PC counterparts. “All the components in the network are sourced from one manufacturer, and this increases reliability,” concludes Lindstrom. "While Ethernet is a standard for PC networking, it has not been standardized relative to the message body."
System integrator DMC recently completed a PLC project for a cubicle divider assembly machine. The machine was controlled by a PLC and a pushbutton interface. The program consisted of a simple sequence that extended and retracted the appropriate pneumatic cylinders when the operator pressed a pushbutton. An operator interface was not required for the system, nor was any data storage.
"The cost, complexity, and programming time associated with a PC-based system could not be justified for this system,” says Tim Jager, controls engineer with DMC.
PLC control was the best choice for another DMC project that interfaced a vision inspection system to an injection molding machine. “The interface between the vision system and the injection molding machine consisted of 13 I/O points and required simple sequencing,” says Greg Frey, controls engineer at DMC. "Therefore, a PLC with an operator interface suited this application due to cost and proven reliability in harsh industrial environments."
PC vs. PLC: Basic Instincts
As these examples illustrate, it pays to carefully select the right controller for the application. Table 1 lists some of the main reasons for using a PC, and Table 2 summarizes the main factors for selecting a PLC.
As always, end user preference will drive many control platform decisions. If a machine builder sells to an industry that prefers PLCs, a PLC may have to be used for control even if a PC would be a better option. The selection of the control system is not always driven by technical factors because clients often have a built-in bias for one type of controller.
The Customer Is King
LMI Technologies, Windsor, Ontario, has a rather unique reason for using PC-based control. LMI designs and manufactures rugged, non-contact, two-dimensional and three-dimensional vision inspection systems for automotive manufacturing applications. LMI has been a long-time user of Siemens PLCs.
LMI's control requirements could be met by either PLCs or PCs, and there was no compelling technical reason to switch to PC-based control. Nonetheless, LMI switched to Siemen's WinAC soft PLC solution because it was the only way to standardize on a single control platform. “Automakers in Germany wanted a Siemens or Bosch PLC,” says Andy Bondy, director of European support at LMI. "The French wanted Telemecanique, and the Japanese demanded Omron or Mitsubishi. Customers in North America insisted on Siemens, Allen-Bradley, Modicon, or some other make of PLC." See the problem?
Using a soft PLC solution, LMI created a system that features an open-architecture PC instead of a proprietary PLC. The move has reduced technical support problems because now users only have to learn the architecture and programming for a single platform. "We converted to the soft PLC solution, which is based on an industrial PC," continues Bondy. "This lets us hide a PLC inside the cabinet without having to meet requirements for PLC compatibility. It also gives us Profibus networking, and it’s easier to program."
The WinAC solution is a little more expensive than a dedicated PLC, but Bondy believes it’s worth it in the long run. "When an automotive line goes down, we are talking about a lot of money," insists Bondy. "When we have a WinAC system on the site, we know how to diagnose and fix problems quickly. When we have dozens of different PLCs—especially those that we see very rarely—it's difficult to get back up to speed quickly."
Top Five Reasons to Use PC-Based Control
- The operator interface software can run on the PC; no additional OI hardware is needed.
- Communication with other computing and control systems is easily executed.
- Very-high-speed control requirements can be satisfied.
- The end user doesn't try to specify a particular brand as with PLCs.
- Extensive data handling and manipulation are more suited to a PC.
Top Five Reasons to Use PLCs
- There is a limited amount of space available for the control system.
- The environment is harsh, with high temperatures, vibration, and/or contaminants.
- Uptime is absolutely critical.
- Single sourcing of hardware and software creates a single point of accountability.
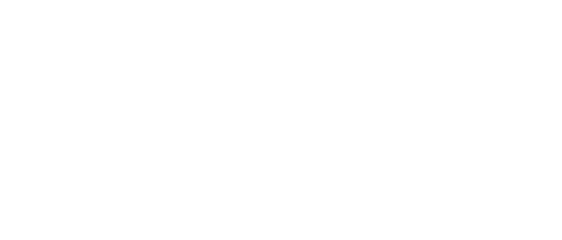
Leaders relevant to this article: