By Deron Roberts, Jet Edge
We needed to replace the handheld control pendants we deploy with our products. These operator interfaces were failing prematurely because they couldnt stand up to the water-jet environment, and our St. Michael, Minn.-based company wasnt about to risk damage to our hard-earned reputation. Compounding these concerns, the manufacturer of the handheld control pendants wouldnt honor the warranty, forcing Jet Edge to replace the devices at our own expense.
These devices are especially critical, because they provide a remote operator interface to the AquaVision Di motion controller, allowing the waterjet systems operators to control the machines anywhere inside the work envelope.
With costs mounting, our company launched a review process to find a new pendant. We would be successful.
Cutting a Fine Line
Waterjet cutting is exactly what it sounds likeit uses a powerful jet of water to cut cleanly and precisely through material in a single pass, without shredding or crushing it. In the formation of the jet stream, water is pressurized up to 60,000 psi (4,100 bar) by a hydraulically-powered intensifier pump. The pressurized water passes through an attenuator (accumulator) that stabilizes the jet stream by providing constant flow and pressure.
The waterjet cutting action results from ultra-high-pressure (UHP) water being forced through a pre-mounted sapphire orifice as small as 0.003 in (0.076 mm). The pressurized water exits the orifice at extremely high velocities (in excess of 2,900 ft/sec) as a coherent stream to produce a clean cut with a kerfthe width of the groove made by the cutting toolalso as narrow as 0.003 in., maximizing material usage (See Figure 1 below). The compact, lightweight cutting head is designed for on/off applications with frequencies of 50 cycles/min.
The water jet stream is pressurized up to 60,000 psi and is forced through a pre-mounted sapphire orifice to produce a clean cut as narrow as 0.003 in.
Single parts, part arrays, mirroring, scaling, rotation, and plate alignment all are managed through the controller, which is fully networkable. That means part programs can be generated offline and easily transferred to the systems hard drive for production.
The interactive process trajectory automatically varies feed rate and acceleration based on known characteristics of the specific job recipe, such as material type, thickness, water and abrasive flow, and nozzle size, which are stored in an on-board database. This achieves required precision, while eliminating guesswork.
Dynamic tool offset, or cutter compensation, is employed real time, says Olson This eliminates the need to reload a part program to the controller if the nozzle/orifice grows due to erosion and produces out-of-tolerance parts. Optional real-time pump control allows remote starting and stopping of the pump, dual-pressure set points for hard-to-pierce materials, and unlimited data logging of every needed process parameter.
Operators use the handheld interface to control feed-rate override, test the jets, return to path, and block retrace. They can do dry runs to see the path without running the jets. With the pendant, they control the ultra-high pressure intensifier pump, which powers the waterjet, controlling the pumps pressure, turning it on and off, and changing the water pressure from low to high and vice versa.
The pendants are especially useful for plate alignment on the waterjet and for starting the cut. Without the handheld interface, the operator would have to go back and forth to the controller to jog the head to the right position (See Figure 2 below). Its also useful for adjusting the sub Zs (independent Z-axis per cutting head) because the remote pendant allows the operator to get close to the material.FIGURE 2: JOG IN PLACE
Looking for the Competitive Edge
For Jet Edge, the new handheld interface had to work seamlessly with the PC-based AquaVision Di motion controller, allowing operators to run the machine without having to stand at the PC-based controller. These pendants also had to perform as a replacement part for handheld interface units previously deployed in the field.
Equally critical was finding a durable, rugged pendant that could stand up to the rigors of the moist water jet environment. After all, the lack of a sturdy terminal was the condition that triggered our search for a replacement pendant in the first place.
Jet Edge needed more than just a supplier, adds Dauer We wanted a partner that would work closely with us to develop a handheld operator interface that would meet the technical specifications while reflecting a clear Jet Edge brand identity. We, of course, also wanted a partner that would stand behind the pendant, providing the quality and service our customers expect.
A Clear-Cut Choice
After a thorough search and evaluation process, Jet Edge partnered with Two Technologies and its 80 Series handheld terminal, a customizable, fully functional ANSI (VT-100)-compatible pendant.
We tested handheld pendants from three manufacturers, primarily by sending them to our customers to evaluate in actual manufacturing settings, says Dauer. We sent out dozens of devices we later rejected. Customers tested them for one year and determined they couldnt hold up to the operating environment. They either allowed moisture penetration or their cables broke. We sent Two Technologies pendants out for evaluation, and our customers clearly determined that they were the most durable products.
Nearly every aspect of operationfrom the viewing angle to the function-key definitionsis easily changeable using simple menu selections or direct host control. Ten distinct function keys can be redefined as characters or strings (maximum of 200 bytes overall) and saved in non-volatile memory.
Two Technologies worked with our engineering staff to develop a full-featured, water-resistant pendant that works with our PC-based AquaVision Di motion control system, states Olson. They took care of the customization and developed a handheld pendant that basically mimics the controls on our motion controller.
A standard key release detection is a particularly useful feature for setting variables and for applications where motion control is essential. I/O configurations include RS-232, RS-422 as well as standard CMOS/TTL logic levels.
The display options support a variety of optional character sets such as Latin 1 or European. With programmable character capability, we had the ability to create characters that arent supported in the displays font table. Since Jet Edge has strategic value-added partners in Europe, the Middle East, Latin America and Asia, these capabilities could prove useful.
We built the 80 Series terminals to be rugged, says Eric Eckstein, Two Technologies president and COO. The case is molded from Cycolac ABS, one of the most durable, chemical-resistant materials available. Securely framed and clamped into place, the keypad surface provides excellent splash resistance, and prevents curling or peeling of the keypad overlay.
I agree, adds Dauer. These pendants are more durable and they offer a better warranty. They are water-resistant, drop-proof, and are pretty much indestructible, unless you drive over them with a forklift.
The Final Cut
Two Technologies designed this purpose-built device to include custom firmware, an emergency-stop switch, and a custom keypad specific to the AquaVision Di process controls. A 5 Hz output signal was added to act as a heartbeat to ensure that the pendant is online and properly functioning at all times. If the pendant doesnt send the 5 Hz signal, the machine will not operate. Other customization included four LEDs in the case and a custom, permanent-wire cable. The customization was completed with Jet Edges colors and custom LED logo tag for a fully branded user experience.
The end result, says Olson is that the handheld pendant virtually mimics Jet Edges motion controller.
Training Days Shorter
Training and support costs have been positively impacted by the adoption of the new pendant solution, as well. Our customers receive training on the motion control system after their system is installed, adds Dauer. This includes training on how to use the pendant. Since the unit was customized to be a fully integrated, purpose-built control interface, its more intuitive for the operators to use, requiring less training and support. Since its much more rugged than the previous pendant, its cut service costs dramatically. Our customers are very pleased with the pendant and its functionality.
The key to success is that it was designed to be customizable, believes Eckstein. With engineered-flexibility, we specifically address the needs and applications of Jet Edge. The pendant is a purpose-built device that lowers implementation and training costs and increases customer satisfaction.
About the Author |
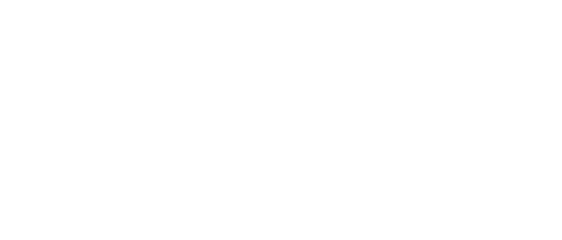
Leaders relevant to this article: