By definition, serial communication interface is a connection and wiring configuration that allows the exchange of data between various intelligent devices, one bit at a time. Serial communication interfacing (SCI) was created in the ‘60s, but coined as such by Motorola in the ‘70s. Today, it is a relatively standard method of communicating on the factory floor--particularly in legacy machine control systems.
The basic SCI contains a parallel-to-serial converter, which serves as the transmitter, and a serial-to-parallel converter that serves as a receiver. Because these two electrical circuit configurations almost always are located on separate devices or equipment, they are clocked independently. Interrupt and enable signals are the means of alerting each other that data is coming. Data speed is programmable, so receivers must be configured to match the transmitter’s transmission rate. Other characteristics include a non-return-to-zero format and the ability to operate in half-duplex mode. The latter uses only the receiver or only the transmitter; full-duplex mode uses both transmitter and receiver simultaneously.
The primary advantages of serial communication interfaces for machine builders are the simple wiring and the cost as compared, for example, to parallel communication interfaces. Also, serial communication interface cables can be much longer than parallel cables because of less cross-talk.
Many Serial Standards
The specific connectivity of the various serial communication interfaces varies depending which Electronics Industry Association (EIA) standard is incorporated. Of these, the most common interfaces used by machine builders are 232, 422 and 485. In 1997, EIA designated each as EIA232, EIA422 and EIA485, respectively. In spite of the new designation, most all documents today still use the ‘RS’ prefix.
EIA 232
9-pin D-sub Connector
The EIA232 standard is the most common serial interface used in machine automation. The most recent version is EIA232F. This change renamed some of signal lines and added a shield connection. The table below represents current EIA232 specifications. Today, connections to and from various devices vary dramatically. Perhaps the most common connection is through the 9-pin D-sub connector shown here. Another connection commonly used on machine control equipment is the 25-pin D-sub connector.
SPECIFICATIONS of EIA232 |
|
|
Mode of Operation |
SINGLE-ENDED |
|
Number of Drivers and Receivers on One Line |
1DRIVER |
|
Maximum Cable Length |
50 ft. |
|
Maximum Data Rate |
20Kbps |
|
Maximum Driver Output Voltage |
+/-25 V |
|
Driver Output Signal Level (Loaded Min.) |
Loaded |
+/-5 V to +/-15 V |
Driver Output Signal Level (Unloaded Max) |
Unloaded |
+/-25 V |
Driver Load Impedance (Ohms) |
3K to 7K |
|
Max. Driver Current in High Z State |
Power On |
N/A |
Max. Driver Current in High Z State |
Power Off |
+/-6ma @ +/-2v |
EIA422
EIA422 is a balanced, differential serial interface using twisted wire pairs. The advantage of a balanced signal is greater noise immunity. EIA describes EIA422 as a transmitter to receiver interface for point-to-point connections. EIA422 was created for greater distances and higher Baud rates than EIA232. EIA422 is also specified for multi-drop applications where only one driver is connected to, and transmits to, as many as ten receivers. The interface is normally terminated on a four-wire screw block or on a Sub-D37 connector, but other interfaces are not uncommon.
EIA422 Specifications
Max. Distance @ Rate |
1,200 m/ 4,000 ft @ max. 100 Kbps |
Max. Rate @ Distance |
10 Mbps @ 12 m/ 50 ft |
Driver Output Resistance |
100 Ohm |
Receiver Input Resistance |
4K Ohm min. |
Max. Output Current |
150 mA |
EIA485
Like the EIA422 standard, EIA485 implements differential line drivers with identical voltage swings: 0 to +5V. The main difference between the two is that EIA422 is strictly for point-to-point communications with the transmitter and receiver always enabled, EIA485 is used for multi-drop systems. By definition EIA485 is an OSI Model physical-layer electrical specification for a two-wire, half-duplex, multi-point serial connection. The EIA485 standard only specifies electrical characteristics of the transmitter and receiver. It does not specify any data protocol. Since it uses a differential line over twisted pair, like EIA422, EIA485 can span relatively large distances (up to 4,000 ft). For multi-drop connectivity, the recommended wiring is a series of point-to-point nodes via a line or bus. Ideally, the two ends of the cable include terminating resistors connected across each wire, and two pull-up resistors to bias the differential pair when the lines are not communicating. Without termination resistors, reflections could cause multiple data indications often causing data corruption. There is no standard connector recommended for EIA485.
Connecting Serial to the World
For machine builders, getting various incompatible machine interfaces to talk to other equipment is a huge stumbling block in machine design and commissioning. For example, in distributed motion control applications, the connectivity between a central controller often is either one of the many fieldbus configurations or Ethernet, which also has many protocols on the market, but the remote drives only have a serial interface. In those cases, and to simplify integration issues, interface converters are used.
“For those applications where we have to communicate to Ethernet (for example), we use off-the-shelf Ethernet-to-serial converters,” says Jim Piotrowski, application Engineer for YET, a manufacturer of high-performance servo drives often used in distributed control applications. “Most converters offer the various types of Ethernet input configurations and the ‘N’ serial protocol output required by our drives. It is easy to install and minimizes the start-up of most machines.”
Mike Justice, President of Grid Connect, a manufacturer of network converters--many of them fieldbus or Ethernet to serial converters--goes even further: “In most cases the interface supplied on most equipment is a serial port,” he says. “By nature these are not networked, so to complete a network, a serial to network converter is required. We supply two types of network interfaces for serial ports, wired and wireless. Wired converters adapt serial to Ethernet, Profibus, CAN, whatever, depending on the network protocol”. Wired converters currently are the most common serial-to-network means employed by machine builders, according to Piotrowski.
Justice continues: “In our experience, most devices ranging in cost from $500 to $5,000 incorporate serial interfaces,” adds Justice. “If the device costs more than $5,000, typically a network interface of some type is included”.
To summarize, it appears that most control equipment implemented by machine builders utilizes some version of serial interfacing described above to keep initial cost down. However, there are often several types of equipment included in any given machine configuration. To connect these various types of equipment, regardless of the serial protocol implemented in each, to a network can now be relatively easy and cost-effective through serial-to-network converters. Moreover, these converters are proving effective in interfacing installed, legacy machine controls to a new network on the factory floor.
About the Author |
Loren Shaum is principal at Comtec, Syracuse, Ind., which provides research in the machine and general factory automation markets. You can reach him at [email protected].
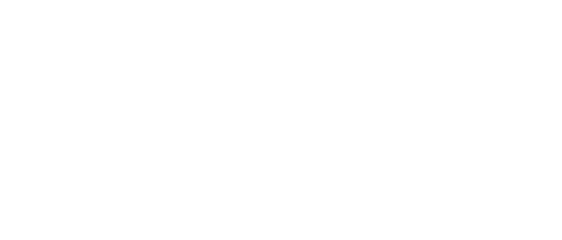
Leaders relevant to this article: