Hydraulic power can’t be beat for mobile vehicle applications where there’s adequate power on board to run the hydraulic pumps. It’s efficient, powerful, takes up little space, and is cost-effective. However, maintenance costs make alternate technologies attractive when a hydraulics-powered application is on the factory floor. At Ford Motor Co.’s St. Paul, Minn., truck assembly plant, hydraulic motors, cylinders and valves have been used on its transfer line (See Figure 1) for more than 20 years. Al Boik, Ford’s maintenance planning specialist, says increased maintenance time for oil leaks, spills and similar high-cost events was required to keep the motors running, and the outdated technology was unable to keep pace with growing production demands.
Ford's increasingly more complex front-body transfer line uses AC drives with accompanying control software to replace aging hydraulics.
DC Motors’ Support Fading
DC motors have a long history that can’t be brushed aside. “DC motors were first used because they provided adjustable speed for constant-torque applications,” says John Malinowski, motors product manager at Baldor. “DC traditionally has been the easiest and lowest initial-cost technology to use, particularly on applications requiring control with regenerative capabilities.”
The downside, he points out, is a lot of maintenance—primarily brush and commutator care. One application that’s particularly hard on brushes is extruding PVC. While DC motors were used with analog controls for years, digital controls were late in being applied to DC systems, and often the control wasn’t as good as with its AC counterparts. Malinowski adds the SCRs fire around 360 Hz in most DC controls, but they can’t react as fast as AC controls that work in the 3,000-5,000 Hz range.
DC drives have lost popularity due to a few basic issues. “In the early days of vector drives, the computing horsepower just wasn’t there to make AC drives a real contender to DC drives, but now the performance of AC drives is as good as DC or better,” states Peter Fischbach, component sales manager, Bosch Rexroth Corp.
Though they may be declining in deployment, DC drives aren’t finished just yet. As recently as the latter half of 2003, project manager Doug McConnachie, of BPB Paperboard in Purfleet, U.K., saw no reason to retire the paper mill’s DC motor-based winding equipment. Replacing old drives with ABB’s DCS 600 Multidrives let him control the tension of the winders with an accuracy of ±0.01%, providing reliable winding and minimizing breakage (See Figure 2).
Ivan Spronk, AC drives product line manager at Schneider Electric, reports that AC motors/drives are taking over in extruders and hoisting applications. “These applications once required DC motors and drives to deliver the needed motor performance,” says Spronk. “The shift to AC is largely due to improvements in AC drive hardware and software. For example, AC motors/drives can match the torque performance delivered by a DC motor/drive and provide better speed regulation and torque performance at lower cost.” Hollis thinks DC drives still make sense where the horsepower requirement is big and regeneration is required, though DC drives don’t have a corner on the market when it comes to regeneration. “With the advent of open/sensorless or closed-loop vector control, AC drives (See Figure 3 below) can control an induction motor, matching the dynamic performance of its DC counterpart, argues Bill Conway, product manager for Siemens’ 6SE70 and enclosed drives. “Regen front-ends and common bus configurations for multiple motor applications also are available to meet tough requirements.”AC Up To The Task
The fact that AC motors can do tasks once relegated to DC motors becomes more obvious to industrial OEMs as they see how motor manufacturers adjust product lines. Emerson Industrial Motors Division dropped its DC business a couple of years ago due to declining interest and sales of DC motors. “With NEMA-standardized AC motor products, the customer buys off-the-shelf and plugs into the drive to get the performance the application requires,” says Rob Boteler, Emerson’s industrial motors marketing director.As shown above, running a hydraulic pump with a VFD can save energy, and the same principle can be applied to industrial air compressors, pumps and industrial ventilation system fans. A centrifugal pump or fan running at half-speed consumes only one-eighth of the energy used during full-speed operation. This is because the torque needed to run a pump or fan is the square of the volume, and power consumption of the motor is proportional to the cube root of the shaft speed. For instance, in a perfect world (100% efficiencies), reducing the pump speed to 80% only requires 64% of the torque (0.8x0.8); the motor power consumption will be 0.8³ (cubed), or about 51%.Lou Lambruschi, product manager at Danaher Motion, says applications that benefit from AC motors and drives include wire drawing (single and multi-stage processes), yarn manufacturing and plastic and rubber extrusion.
Voestalpine Stahl’s hot-dip galvanizing line will use around 300 drives, with outputs ranging 2.2-1200 kW for a total installed drive power of 15 MW.
Is HTS in Your Future?
RECENT ADVANCES in high-temperature, superconducting (HTS) motors promise reduced size and increased efficiency for AC induction motors. Today, however, HTS is mainly being applied to motors with greater than 1,000 hp ratings because costs don’t yet favor smaller sizes.
Greg Yurek, CEO and cofounder of American Superconductor, reports, “The ability of ceramic-based superconducting wire to carry up to 150 times the current of its copper counterpart allows reduction of motor size down to one-third the weight and one-half the volume of a conventional motor, making it suitable for tight spaces.”
HTS motors are claimed to run at 98.5% efficiency with loads from 100% to 10%. Yurek says a 10,000-hp motor using electricity at $.10/kwh will pay for itself in about four years based on electricity costs only.
On the AC-drive side, power electronics manufacturers are packing IGBTs into intelligent power modules, says Ivan Spronk, AC drives product manager for Schneider Electric. This development allows enhanced control of the IGBT. Other advances include improvement of sensing motor current to provide real-time feedback to the drive and a two-microprocessor architecture for drives: one CPU processes the motor control algorithm and the other interfaces with the external I/O, communication networks and HMI. Improvements in motor control software are allowing more precise control at the low end of speed ranges, which typically is enough control to hold a hoist load at zero speed or control material flow through an extruder, previously the job of DC-based equipment.
Drive Performance / Cost Comparisons
DC SCR | Brushless DC | AC inverter | AC Vector - Open Loop | AC Vector - Closed Loop | |
Hp range | 1/50 hp - up | 1/50 - 400 hp | 1/10 - 1000 hp+ | 1/10 - 1000 hp+ | 1/10 -- 1000 hp+ |
Special motor required | No | Yes | No | No | Yes - to get full performance |
Relative speed range | Wide (20:1) | Wider (40:1) | Narrow (5:1 - 20:1) | Wider (90:1+) | Widest (6000:1) |
Speed control | Yes | Yes | Yes | Yes | Yes |
Torque control | Maybe (1) | Yes | No | Yes | Yes |
Positioning | Maybe (1) | Yes | No | NO | Yes |
Orienting (zero index) |
Maybe (1) |
Yes | NO | No | Yes |
Open-loop speed regulation | +/-1% of set speed | N/A | +/-3% of base speed | +/-1% of base speed | N/A |
Closed-loop speed regulation | +/-1% of set speed | +/-0.5% of base speed | +/-1% of set speed (2) | Becomes closed loopNo | +/-0.01% of set speed |
Can maintain full torque at zero speed? | No | Depends on control design | No | No | Yes |
Motor brushes / maintenance required? | Yes | No | No | No | No |
Can operate multiple motors | Yes, but not recommended3 | No | Yes (3) | No | No |
Relative cost | $ | $$-$$$ | $-$$ | $-$$ | $$$ |
Resource Center
- Thomas A. Westerkamp, Maintenance Solutions, www.facilitiesnet.com/ms/aug04/aug04construction.shtml
- Consortium for Energy Efficiency: www.cee1.org/; (Motors Matter: www.motorsmatter.org/)
- DOE, Energy Efficiency & Renewable Energy, Industrial Technologies Program, Motor Challenge: www.eere.energy.gov/industry/financial/feddoe6.html
- Free software from DOE (MotorMaster+, Fan System Assessment, and more): eereweb.ee.doe.gov/industry/bestpractices/software.html
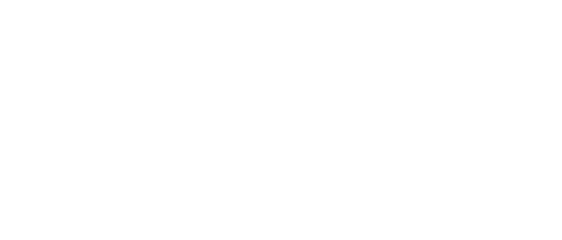
Leaders relevant to this article: