Deciding to change a software platform isn't easy. Take the case of Glasstech, which builds glass tempering equipment in Perrysburg, Ohio. "We previously used a proprietary control system based on a Motorola 6809 processor, which had components that became obsolete," explains Steve Connell, Glasstech's systems engineering manager. "This forced us to upgrade our controls. We had two primary goals. The first was the capability to control all of our products on the same platform, and the second was that the platform be acceptable in the U.S. and internationally." About two-thirds of Glasstech's sales are international (See Figure 1).Glasstech's former 6809 processor was a very robust and reliable system, Connell reports, and over the years the company developed its own motion control software for the platform. "One option was to keep a similar platform based on the Motorola 68000, but the hardware and software would require too many man-hours to develop," says Connell. "Another alternative was soft control, but we felt the software costs were too high, and support of the software controls would become obsolete eventually. We've found it's extremely difficult to support a machine running on a software platform that is 25 years old, and it's just as hard to find computer equipment to run it. We decided to require that our control systems be open, and not need a specific operating system."In addition, Glasstech needed a system that would support simulation, enterprise integration, and remote diagnostics of those faraway systems. "We decided that the ControlLogix platform provided what we needed," Connell says. "Our simpler machines did not require servo accuracy, while our more complex machines had 18 servos. This platform is scalable for both types of systems, yet is fairly cost effective on the low end. Our goal is to have this become our control system standard for the next 15-20 years."
Figure 2: Cold Controls
This crane controller has to sit out in the weather for weeks at a time, and then start up immediately. Greer chose a diskless Windows platform for it.
When you're choosing a new software control platform, integrating all the various parts poses a particular problem. "System design software and hardware are constantly growing areas, filled with a variety of niche tools," explains Greg Wempe, product manager at National Instruments. "As a result, today's design cycle is a complex mesh of software and hardware tools that, in many cases, are left up to the control expert to integrate. When selecting a software control platform, integration is a key area that is often overlooked. Software tools for niche applications are important, but they're merely tools, not a platform. A software package that spans the entire development cycle represents a software platform."Rami Al-Ashqua, product manager at Bosch Rexroth Electric Drives and Controls agrees. "Integration of all the project software tools will influence the choice of what software platform the machine builder will use for a project," he says. "Software that allows the control engineering unit to set up its I/O, program its motion, configure the amplifiers, and visualize the HMI screens is becoming a must since projects are becoming more complex and more and more machine and supervisory data is integrated into programming any machine."Integration and machine control involves software programming of the control logic, motion control, HMI, device interfaces and a host of other functions in any of several different languages, ranging from ladder logic to C++. Almost all modern software control platforms allow use of IEC 61131 PLC-type programming languages, including ladder, so your PLC programmers can move from a PLC to an open platform with no problems.If you want to employ advanced features such as HMIs on mobile PDAs, your programmers might need a more capable language than ladder logic. Fortunately, help is coming. "Engineers just coming out of school will be familiar with Microsoft products such as Visual Basic and C++," notes Rob Rawlyk, applications and engineering manager at Beckhoff Automation. "Software that can adhere to standard OSs and global programming languages will become more critical as machine builders increase adoption, and as their customers begin to demand it for more seamless integration of machines from different manufacturers."Simulation Speeds DevelopmentBeing able to simulate machine actions and responses is becoming a more important part of integration, especially when machines incorporate advanced functions and support equipment. Simulation also helps when debugging machines in remote locations.Beckhoff provides simulation capabilities in its Simulation Manager, which allows users to configure and set up systems to simulate machine operation. "This is a recognition that software development and hardware development for machines don't necessarily coincide," says Rawlyk. "In some cases, you can build and simulate an entire operation on your machine with the ability to switch back and forth to test processes in simulation mode without actually having any axes running."Al-Ashqua agrees. "Being able to simulate your project offline has always been a big plus for machine builders," he says. "It saves integration time and offers a lot of flexibility to the control engineer. Simulating a complete control, I/O, drive and HMI project allows the end user to save on-site setup time and reduce training costs for engineers and service people."The system that Eagle Technologies built for its automotive manufacturer client not only builds parts, it tests them. Part of the test involves in-vehicle simulation, and all test data has to be archived in case of a product recall. As you might expect, all such data is stored in a standard "open" database that can be accessed by higher-level software.As in the case of enterprise integration, a machine builder doesn't have to write simulation, test or quality control software, because such packages are readily available from software vendors. To make it possible for the user to do this, once again, the software control platform needs to be open.Does Open Mean PC?
"For most people, the term 'PC' evokes an image of desktop or laptop computers," says Chuck Harrell, director of marketing at Advantech. "PCs typically used in control are industrial units as small as videocassettes and mounted in racks, panels or on DIN rails. Typically, these computers are equipped with communications ports and central processing units. The operating system, often Microsoft's Windows CE or Windows XP Embedded, is embedded in solid-state flash disks in the unit. In addition, the units also rely on solid-state flash memory for applications and data storage."When discussing control platforms, the argument of PCs versus PLCs always tries to enter the game. This article doesn't focus on that value discussion, but anyone choosing a software control platform does have to make that hardware decision. Often, the choice boils down to a PLC with a PC-based HMI, or a PC-based control system with HMI/SCADA software. Both solutions get you an open system. Some "hybrid" PLCs are actually PCs with PLC features, so that gets you an open solution, too.
With an open system, you get features and benefits not available with proprietary controllers. Larry Ricci, business development manager at Applied Data Systems, says these include:
- Secure wireless network
- Web servers
- SMTP, TAPI (e-mail and pager messages)
- Multimedia (instruction books, how-to videos, etc.)
- VoIP (voice over Internet)
- Authentication and security
- Embedded databases (not on disk)
- Thin client (client and server)
- Virtual Private Networking (VPN)
- International fonts
- Video inputs
- Web browser
- XML
"If a machine builder needs to incorporate any of these functions, a proprietary system becomes much more expensive to develop and maintain," says Ricci. "Features built into an open architecture, supplied and maintained by the OS vendor, become costly overlays when added to a system that is proprietary at the core."
These functions are available in computers running Linux, Windows NT, Windows XP, Windows XP Embedded, Windows CE, and many real-time extension operating systems. "A machine builder can find single-board computers that include the OS, display interface, network interface and power supplies," says Ricci. "Integrating application packages is done easily. Software for HMI, machine control, sequence control, logic control and motion control has been modularized, and is available at a reasonable cost."
Growing on Machine Builders?
We write entire articles about real-time operating systems (see "Embed with Machines," CONTROL DESIGN, Oct. '04) but, for the purposes of this article, we'll confine ourselves to an increasingly popular RTOS for machine builders: Windows CE. It is safe to say that other RTOSs offer similar capabilities.
CE's ability to be embedded in a machine is a primary reason for the growing interest in it. Many industrial environments, especially where machines operate, are hostile to PCs and require diskless operation. Because Windows CE is able to run with a Flash disk or EPROM, instead of a hard disk, it's an ideal software platform for a machine builder. Therefore, a single-board computer or an industrial embedded PC with CE becomes a rival to PLCs in terms of the reliability, robustness and performance needed by machine builders. Panel PCs (diskless PCs with an HMI screen) also use Windows CE.
Another reason for CE's emergence is cost. A base version (Windows CE .NET 4.2 Core) costs only $3 per copy. One with a few more functions costs $15 per copy. CE also provides real-time performance needed for microsecond-level response and all the attributes of a larger, open Windows OS.
Bosch Rexroth, for example, chose CE as the RTOS for its IndraWorks software control platform because it supports everything from development tools to remote diagnostics. "IndraWorks is an engineering framework for uniform engineering workflow that allows integration of all software tools, and gives the control engineering unit a comfortable project administration with central data storage to allow multiple users to configure different parts of the project at the same time," says Al-Ashqua. "Engineering tools also are essential. Web capabilities, device support, and many other tools allow machine builders to remotely diagnose and upgrade software. Web capabilities provide not just viewing, but also commanding the machine."
Windows CE is up to real-time tasks, according to Mike Hall, technical product manager at Microsoft. In an article in Embedded Computing Design, Nov. '05, he reported that Windows CE meets 95% of the requirements of the Open Modular Architecture Controls (OMAC) User Group. "OMAC reviewed hundreds of applications and found that 95% of systems require cycle times of 1 millisecond and greater," writes Hall. "With a response time averaging 50 µsec on a 200 MHz x86 system, Windows CE meets or exceeds the requirements of all but 5% of the applications OMAC reviewed."
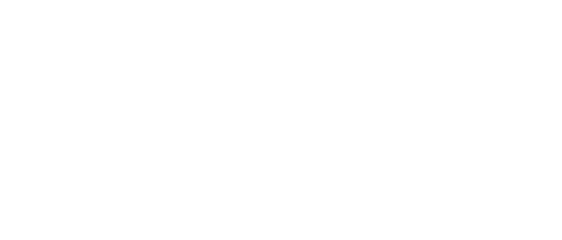
Leaders relevant to this article: