Linear motors have been around for many years, but this technology became readily available only in the past decade or so. Its now gaining popularity, but not at the lightning pace some predicted. Linear motor manufacturers boast about phenomenal acceleration rates and final traverse speeds, but, in reality, traditional competition isnt far behind.For example, performance and cost factors both have improved. Lead screw-based slides, 2 meters long, running 2 m/sec velocities, were an expensive dream just a few years ago, says Tom Solon, PE, applications engineer at Kerk Motion Products. Now, theyre available for $500. The linear motor has higher ultimate speed and accuracy, and might generate more force. But why spend five to 10 times more money, accommodate the much larger footprint, and use the necessary power if the lead screw solution is good enough?The questions Solon raises are good ones. Many of us have a Tinker Toy mentality and a desire to experiment with new technologies. Were engineers, after all, but we also understand how our decisions affect the bottom line. It can be difficult to justify experimenting with newer technologies when the lower-risk choice might still exceed targeted performance requirements at a lower installed cost.In short, they do work well. The traditional rail and screw technologies are proven over time, reminds Sheldon Prom, chief engineer at Komo Machine of Sauk Rapids, Minn. These solutions have been fine-tuned and they consistently work well. Traditional methods, even when combined with new innovations in seals and coatings, often represent a low-risk/low-cost solution.
Ball screw motion on the horizontal axis of this honing machine is allowing it to achieve speeds of 150 m/min while prolonging machine life, even in a harsh environment. Source: Sunnen Products
Despite their advantages, how do mature technologies, such as ball screw-driven slides, keep making performance enhancements? The answer has several parts.First is the availability of high-precision thread rolling (See Figure 2 below), which enables very accurate positioning and actuation at low costs, says Solon. With micron and submicron positioning accuracy and repeatability, new products can be brought to market that were previously not saleable. Kevin Gingerich, director of marketing services for Bosch Rexroth, echoes this sentiment. Technology has advanced so substantially that a rolled screw can now rival ground screws in smoothness and precision he says.
Industry observers say price-performance ratios are still frequently in favor of traditional technologies in many applications, which might be one reason that linear motors have not yet seen widespread acceptance. Ball screws provide better price-performance and size-performance ratios in applications where high thrust forces are required, says Gingerich.Referring to traditional ball screw driven slides, Solon adds the technology has advanced so much that it helps equipment designers get what they need in an affordable package, which includes parts consolidation, motor optimization, environmental compatibility and zero maintenance. In the past, it might have been necessary to overbuy to meet a single performance parameter. With today's technology, we can tailor the product to the application and keep cost manageable.
This multi-axis welder achieves 30 welds in 33 seconds, using the fast, precise motion of ball screw-driven axes. Ease of implementation and environmental compatibility are two reasons why ball screw driven slides remain popular. Source: Centerline/Bosch Rexroth
Its fair to say that newer technologies typically are developed to solve new problems. In other words, a motion system designer might find that he cant achieve his desired solution with so-called traditional technologies, explains Gingerich. He might need something smaller, faster, quieter, or more precise. Or, he might need something larger, less expensive, or easier to install. It is here that newer technologies are best applied, and where they will shine brightest.In an application requiring high speed, relatively high force and high accuracy, the linear motor solution is likely to be the only way to ensure performance, states Stephens. The stiff coupling of a linear motor cant be duplicated with ball screws, belt drives or standard actuators. The backlash and directional repeatability will suffer.However, Stephens adds, Linear motors typically are sold as frameless devices requiring a significant amount of engineering. They offer some advantages over any other form of control, but the added complexity might not be justifiable in all cases. For cost-sensitive applications requiring nominal accuracy in the 0.001 in. range, a precision ball screw-based actuator might be the correct solution (See Figure 4 below).FIGURE 4: MANIPULATED MILLING
Simplify, Simplify, Improve
SOMETIMES, there are innovations with benefits that can be applied universally to any technology. That seems to be the case with Monorail AMS from Schneeberger, a manufacturer of linear guide technology. Monorail AMS is an integrated rail system that includes a magneto-resistant feedback encoder directly in the linear rail. Weve been focusing on the integration of technologies, states Glenn Bythrow, U.S. systems sales manager for Schneeberger. Weve integrated encoder technology directly into the bearing, thereby simplifying the assembly and increasing the overall MTFB.
The rail system is industrially hardened, and reportedly can withstand the rigors of 24/7 operation. Also, it clearly offers a lower cost of ownership to the end customer by eliminating the need to purchase and install a separate secondary encoder, adds Bythrow.
This type of innovation, though not directly part of the ball screw/ball nut assembly itself, aims to raise the value of whatever type of linear motion is being used, whether linear motor, ball screw, or fluid-powered. By reducing the implementation costs for all technologies equally, it become even apparent that the lower the original system cost, then the greater the proportional cost advantage provided.
Bythrow adds, This newer, integrated technology is based on tried and true older technology. It therefore provides no additional risk to the customer, so theres no reason not to use it.
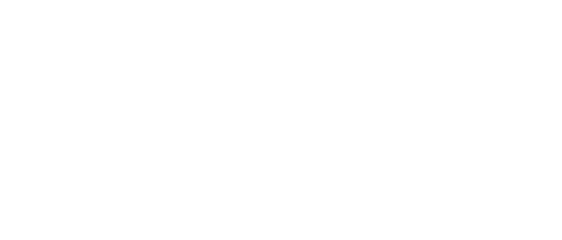
Leaders relevant to this article: