EVERY MACHINE builder would like to know what its machine control, instrumentation and electrical systems will be like in five or 10 years. The more we can plan for the inevitable changes that automation technology will bring, the better we can benefit from it when it evolves into practical machine control functionality.
One way to envision the future is to look at specific trends in automation hardware and software, but it might be better to first look at more general trends that will inevitably drive the evolution of machine automation.
THE MACHINE OF THE FUTURE WILL HAVE:
|
This machine prints serialized numbers on labels and then performs character verification inspection prior to applying the label. This process is used for tracking product during lab trials. One of the main reasons Weiler Labeling must automate is to remove the variability of operator actions. Source: Weiler Labeling
Close the Loop
Another way that automation replaces labor is through closed-loop control. Open-loop control requires constant manual observation and adjustment. Closed-loop control not only reduces labor, it also improves operations.
AutoJet Technologies, Wheaton, Ill., is the turnkey systems division of Spraying Systems, a manufacturer of high-quality spray nozzles. Autojet’s automated systems optimize spray performance to improve product quality and reduce production costs.
AutoJet makes extensive use of closed-loop control. “Manufacturers use closed-loop control to create smart production machines that can adapt to changing conditions,” reports William Kohley, vice president at AutoJet. The company provides closed-loop control with its gas conditioning system, which is used to cool hot gases and reduce gas volume at pulp and paper mills, steel mills, power plants, waste incineration facilities and cement plants.
The operator specifies the desired gas temperature; the spray controller, using temperature sensors, constantly adjusts variable frequency drive pumps to control liquid flow. “This closed-loop regulation mode is capable of generating consistent drop sizes and holding very tight temperature tolerances for peak system performance with minimal operating costs,” states Kohley.
Off-the-Shelf Automation
Machine builders enjoy another big labor saver for their automation systems when they use standard hardware and software. The PC WinTel standard now is so well-known that there is little or no learning curve for machine builders and their customers.
Fadal Machining Centers, Chatsworth, Calif., manufactures vertical and horizontal machining centers for applications ranging from medical to aerospace industries. Manager of electrical engineering Khosrow Ansari envisions a PC-based control system with a standard bus communication. The PC would use PLC-type I/O configuration and measurement devices.
He feels that would allow Fadal to standardize on control system hardware and develop proprietary software. “This would open up a host of options that could reside or be connected to the control system such as CAD/CAM, coordinate measurement machines, and remote diagnostics,” says Ansari.
Coordinate measurement machines allow inspection in operation without removing the part from the machine. According to Ansari, this is not a very common application, but it’s growing. He says quite a few end users use probing, but a measurement system often would do a better job.
Another machine builder that sees the light regarding off-the-shelf Windows-based hardware is Orthodyne Electronics, Irvine, Calif. Orthodyne is a world leader in the manufacture of manual and automatic ultrasonic wire bonders for the hybrid and semiconductor industries (See Figure 3).
If electromechanical components are becoming more expensive relative to automation systems, the machine of the future will use automation to replace these components.Machine-mountable controllers, I/O and sensors are a good example of this trend. Machine mounting eliminates the need for enclosures and associated hardware.Another prevalent trend is replacement of electromechanical drive systems with servo motors and drives. These alternatives can eliminate, or at the least enhance, a host of components such as belts, gears, and other mechanical linkages.Fiberoptic sensors replace entire classes of electromechanical instrumentation. These sensors are smaller, cheaper, more durable, and can operate at much higher temperatures than electrical and electromechanical sensors.Unlike electrical sensors, fiberoptic sensors are not susceptible to electromagnetic interference and can therefore be reliably used in industrial machinery where electrical noise abounds (see "Getting Enough Fiber? sidebar below).
Another automation component that displaces electromechanical devices is the graphics terminal. Gauges, thumbwheels, and pushbuttons typically are eliminated when a graphics terminal is used, and this changeover has been proliferating as these terminals decrease in size and become cheaper.The Machine of the Future
The direction seems clear. Machines of the future will use automation to replace labor and electromechanical components—a process that started many centuries ago. Examples of this abound, and more will crop up as automation becomes cheaper in relation to labor and electromechanical components.Some of the specific automation technologies enabling labor and electromechanical component replacement are clear and present. Others technologies such as fiberoptic sensors are in the R&D phase. Still others have yet to be discovered.As automation takes a bigger piece of the machine pie, the control professional’s job will increase in relative importance. Machine costs used to be dominated by electromechanical components, and these machines were very labor intensive to build and operate. Most of the cost of future machines will consist of automation components that promise to be ever cheaper, more durable, and higher performing.
Automation Drives Retrofit Trend
ELECTROMECHANICAL components might not be improving rapidly in terms of price vs. performance ratios, but they certainly last a long time. This creates an opportunity to improve machine performance via upgrades to automation systems. It also means that some of the machines of the future might actually be today’s machine with upgraded automation.
System integrator Concept Systems, Albany, Ore., often retrofits machines with new automation systems, and its customers see many benefits to this approach. “Often an old machine can be upgraded to produce more by cutting changeover times or decreasing maintenance downtimes simply by replacing an old, inflexible, hard-to-maintain-and-upgrade control system with a new one,” says Ed Diehl, principal at Concept.
Concept Systems replaced the Bailey DCS on this steam turbine and generator with a redundant Allen-Bradley ControlLogix system and a Rockwell Automation RSView HMI. Source: Concept Systems
Outsource Labor to the Machine Builder
THE LABOR expended in a factory to commission and start up a machine is extensive and expensive.
If the labor is performed by the machine builder’s own personnel, there are travel and lodging expenses to pay beyond the labor costs. If the labor is performed by the manufacturer’s automation professionals, extra expense is incurred because the manufacturer is not as familiar with the machine as the machine builder.
Because of these factors, Battenfeld Gloucester uses automation to allow customers to “outsource” labor to it.
Battenfeld Gloucester Engineering, Gloucester, Mass., designs, builds, installs and services customized plastic extrusion systems and controls.
“We use distributed I/O and sensors to create more intelligent control systems,” says Paul Brancaleone, engineering manager of software/controls at Battenfeld. “Our machines are becoming more modular, and this increases our internal assembly and test times.”
Because the extra time involved in producing modular machinery results in savings on the installation and commissioning side, Battenfeld customers see equipment go into their plants and be up and running much quicker, adds Brancaleone.
Battenfeld customers also outsource automation labor through remote access and diagnostics. “We can connect to the control systems remotely to help in diagnosing problems,” says Brancaleone. “This means that our customer’s equipment operators require less skill and time as the intelligent control systems remotely warn us when something is going wrong.”
Another way to outsource labor from the manufacturer to the machine builder is through quick-connection systems. Nearly all connector companies provide many types of quick style connections—ranging from spring-clamp to insulation displacement terminals to metric cords and connector sets--as opposed to the traditional screw-down components. “Decreasing the amount of time it takes to assemble a piece of equipment allows machines to be re-assembled quickly at customer sites,” says Todd Desso, product manager of industrial connectors at Phoenix Contact.
Getting Enough Fiber?
ACCORDING TO a recent article in The Economist, the most common type of fiberoptic sensor in use today is called a “Bragg grating,” which is the fiberoptic equivalent of a strain gauge. A Bragg grating is a region of a fiber where the refractive index has been modified so that it varies in a precise and periodic way, causing the grating to reflect light of a specific wavelength.
As the fiber is stretched or compressed, the reflected wavelength changes accordingly, and strain can be determined. Changes in temperature also change the fiber's properties in predictable ways. By incorporating several Bragg gratings into a single fiber--each tuned to reflect a different wavelength--it is possible to measure the variations in strain or temperature along the fiber's length.
Professor Anbo Wang and his employer, Virginia Tech University in Blacksburg, Va., created the Center for Photonics Technology to investigate and create sensors that can be used in harsh industrial applications.
The center has produced the world’s smallest known pressure sensor. The sensor is a mere 125 µm in diameter and can function at temperatures as high as 700° C. Competing sensors are limited to 500° C.
Developed by Yizheng Zhu, a Ph.D. student at the center, the sensor is fabricated directly on the tip of a fiber by micromachining and thermal fusion, giving it the same thickness as the optical fiber.
The sensor has minimal cross-sensitivity to temperature, resulting in a simplified sensor system with a wide temperature range. Its small size and low mass give the sensor an extremely high resonant frequency, resulting in a flat response over a very wide range of frequencies.
Sensitivity can be adjusted for different applications, with a pressure range as low as a few psi or as many as 10,000 psi. The sensor is another step toward the Center’s goal of developing pressure sensors that can operate above 1,000° C.
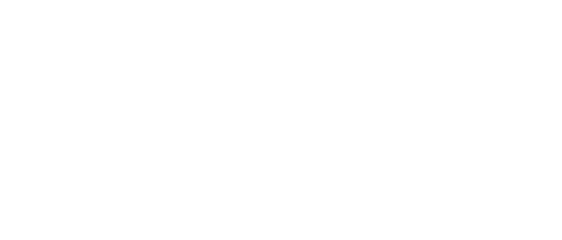
Leaders relevant to this article: