The valve spools (1) of these proportional valves are actuated by a moveable coil (2) over a friction-free permanent magnet cylinder (3). This direct actuation of the spool, coupled with high resolution feedback, allows the valves to be positioned more precisely, in less time. The end result is high speed precision. Source: Rexroth Hydraulics
āSSI [Synchronous Serial Interfaceāed.] feedback for MDT sensors represents one of the greatest advancements we have seen in recent years for hydraulic system control,ā states Bob OāBrien, principal engineer for system integrator Concept Systems, Albany, Ore. āThere is no need to rescale after replacing a probe, or to re-home the system at startup. Most importantly, this represents a universal interface for measuring position.āThese sentiments are echoed by Nachtwey, who says Delta uses open-system technologies, so it doesn't need to reinvent the wheel. āDeltaās tools run under popular Windows operating systems and Delta controllers interface to standard transducers and standard system buses,ā he states.A good example of a big, impressive standards-based hydraulic-power control application comes from Electroimpact, Mukilteo, Wash. The company is the prime contractor for supplying automation tools to the Airbus plant in Broughton, U.K., which assembles the wings of the worldās largest commercial aircraft--the Airbus A380.The huge size of a completed wing panelāup to 111 ft long and weighing 8,818 lbāposes a big material handling problem. āUsing cranes to position the panels doesnāt work,ā says Electroimpact project engineer Ted Karagias. āThe wing panels are distorted when suspended from the cranes.āElectroimpact devised a multi-arm manipulator (See Figure 3) to maintain the panelās proper form and provide precise positional control while presenting the panel to the wing structure for fastening. The company designed and built an array of six coordinated servo hydraulic arms that engages the panel along its entire length.
A completed AirBus wing panel poses a big material handling problem. Electroimpact devised a multi-arm manipulator to maintain the panelās proper form and provide precise positional control while being fastened. The machine is an array of six coordinated servo hydraulic arms, and the primary axis of movement is managed by a closed-loop servo hydraulic controller integrated with an SSI linear scale, load cell and servo solenoid valve. Source: Bosch Rexroth
Because of the interconnect ability of modern hydraulic controllers, a hydraulic axis can be integrated into the CNC just as a traditional electric servo axis would be. MJC Engineering & Technology configured a CNC for two-axis, z and rotation control. The hydraulic control module fits directly into a standard electric servo drive bank and matches the physical properties of the other drives, but it also matches the electrical connections including equipment bus and DC link. Since the electrical connections, as well as electrical interface match, the integration of the unit goes much smoother. Source: Siemens
These advances represent significant improvements in hydraulic control, but they still might not be enough to make you think about leaving your current technologies. There are other factors that could sweeten the deal. Software could be one of those factors.Like any electric servo-based system, an axis of hydraulic control needs to be tuned for optimum performance. āAdvances in programming and tuning tool technologies allow machine designers and integrators to complete optimized designs much more quickly and for lower development cost than would have been possible in the past,ā adds Nachtwey. āA robotic system integrator in Quebec completed an application with our new Tuning Wizard software (See Figure 5). The engineer tuned 10 motion axes in 15 minutes--a feat that would be impossible using standard trial-and-error tactics.āCompletion of the system installation does not mean it is the last time youāll hear about that system either. OāBrien contends that, āto the end user, ease of maintenance represents the biggest advantage that our customers enjoy. Reduction of the maintenance burden on them relates to more uptime and more revenues.ā
Programming and tuning tool technologies let machine designers and integrators complete optimized designs quickly and for lower development costs. A robotic system integrator tuned 10 motion axes in 15 minutes--a feat that would be impossible using standard trial-and-error methods. Source: Delta Computer Systems
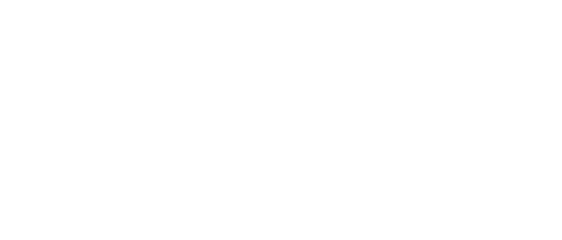
Leaders relevant to this article: