Ethernet is becoming a regular in the specifications we receive from customers that require network connectivity in severe operating environments where we install our rolling mills. Is Ethernet a good idea in the first place? Can we take advantage of lower-cost commercial hardware, or are there applications where we should use more costly industrial grades?
— From April Control Design
Answers:
Ethernet Has Much to Offer
An advantage of Ethernet is that you can run more than one protocol over the same network. Fieldbus standards for Ethernet communication are maturing. We recommend a dedicated Ethernet subnet for the industrial fieldbus. Network switches provide determinism and avoid collisions. Switches should be used instead of hubs for industrial applications. Connector and cabling companies are developing industrial-grade Ethernet connectors and related hardware.
We use DC motors in our load-sharing conveyor installations. The motors are connected in parallel to a DC drive and split the output current equally so they run at the same speed. We have a customer specification to do this with AC motors instead. It appears we'll have to use a variable frequency drive for each motor and are not certain we know how to guarantee they will all run at the same speed. Help.
Send us your comments, suggestions, or solutions for these problems.
Gateway devices for Ethernet are becoming increasingly popular. These devices map or interface other buses onto the Ethernet network, such as serial, CANbus, and a variety of fieldbuses. This is another reason why it is relatively easy to add Ethernet-based devices to existing measurement and control systems.
Wireless Ethernet technology is widely available. It offers a rated range of up to 25 mi. (40 km). Wireless devices, fiberoptic links, and other bridges are transparent to the network, so no code changes need to be made to add wireless capability.
For mission critical control loops, the software must match the hardware in terms of its suitability. The reliability of the embedded control system depends just as much on the embedded software and operating system (OS) as on the silicon. If the OS allows itself to be hijacked by instructions that are not mission-critical, then there is no way to guarantee that the system will meet its timing requirements.
Under a general purpose OS, a control loop that normally runs fine on a general-purpose OS may fail when conditions change, such as when the application intermittently sends a packet of data over the Ethernet port. On the contrary, a real-time OS will prioritize, allowing the serial instructions to execute only when the time critical functions have finished and are "sleeping."
Likewise, if an event occurs that requests the time-critical function, any lower priority operations are immediately suspended. This software pecking order allows the time critical task to exert absolute authority over the OS, preventing insubordination in the ranks over lower priority tasks. When the top dog barks, the pack is 100% dedicated to the request until it is finished.
For lower priority functions, the operating system multitasks and gives each task a roughly equal piece of the remaining processor time. This combination of even-handed sharing of lower priority jobs and iron fisted dedication to the time-critical task means that as long as there is sufficient computational muscle available, a single processor can do it all. The same embedded system that controls the temperature, pressure, and fluid in a critical chemical manufacturing process can also serve up a web page and administer a file transfer protocol (FTP) server. Those normal priority tasks run automatically in the background when the critical loop is resting, but when the time critical loop awakes and snatches back the processor, it's got control within microseconds.
Brian MacCleery,
distributed I/O product manager,
National Instruments
Yes, It's Tough Enough
Ethernet is winning the protocol wars, even in the factory, because it has proven to be capable of delivering the determinism, speed, and reliability required by the industrial space. It also delivers new levels of productivity by enabling manufacturing enterprises to become truly integrated (top-floor to shop-floor). Ethernet wins on the basis of cost because it has long been the office standard for open communications, the components are commercial off-the-shelf (COTS) brands, and the skill-sets needed to install and maintain the technology are more widely available. Also, because of the widespread use of Ethernet technology, the rate of new developments and advances in this area is accelerated compared to proprietary communication protocols.
Still, tough environments like steel mills do require tough solutions, and Ethernet is capable of meeting the challenges of these applications. Given the electrical noise and temperature extremes prevelant in these types of environments, fiberoptic cabling should definitely be a consideration. Copper cabling and wireless are often not viable options in applications where significant electrical noise is generated by large motors and drives. In addition to making the right cable choices based on the environment, it is also important to look at the specific connector requirements for each area of a given application.
Regarding other network components such as switches, the decision to use industrial grade versus office grade again depends on the environment where each specific component will be located. For example, if a switch is housed in an environmentally controlled enclosure or control room, office-grade may be sufficient. However, if the switch is going to be located in the same cabinet as control equipment or in other areas where there can be a lot of noise, industrial grade equipment may be required. An advantage with Ethernet is that you now have more options — you can take advantage of lower-cost office-grade equipment where appropriate and use the industrial grade components only where necessary.
Beyond the challenges of the physical environment, another consideration when looking at network components is existing applications that may be running very well but are built on proprietary networks. Many companies want to make the move to Ethernet but are understandably wary of ripping out all existing applications and supporting infrastructure all at once. The good news is companies can migrate to Ethernet infrastructures at a pace that makes sense for that specific organization. By using technologies such as gateways and protocol converters, companies don't have to take a rip-and-replace approach to achieve the advantages of Ethernet.
Chris Samley,
senior industrial network engineer,
Mike Smith,
industrial network engineer,
GE Cisco Industrial Networks
Equipment Protection Essential
The decision to employ the many advantages of an Ethernet capability in any location should be a decision of cost versus benefit. The increasing numbers of Ethernet-ready devices that provide continuous monitoring and communication capabilities with virtually every nut and bolt can only improve the process.
The application of a network into existing production facilities or locations subject to frequent reorganization is simplified with the use of a wireless LAN. The severity of the application environment will impact the selection of equipment, however many commercial products — bridges, switches, access points, etc.--can be deployed into industrial environments using enclosures to provide environmental protection and physical security. These enclosures can support temperature control when necessary and can also be sized appropriately to manage wired or wireless enabled controls, PCs, printers, etc.
Ed Calhoun,
engineering manager,
ITS Enclosures
There Are Limits
Keep in mind that Ethernet is used at the host level of the control system, not at the field level. Ethernet is unsuitable for connecting instruments such as pressure transmitters and valve positioners because it lacks multidrop, device power, long distance capability, intrinsic safety, and requires too many wires and special cable.
This Ethernet usually runs in the rack room where the environment is not too harsh. As far as industrially hardened wiring is concerned, there are plenty of industrial-grade switches and IP67 connectors in the market. If the environment is harsh, these are a good idea. For long distances or between buildings, use fiberoptic media. This is achieved using transceivers and converting switches. Media duplication provides a certain level of redundancy that increases the availability of the system.
For best fault-tolerance, use a protocol that supports complete redundancy including network, ports, and devices. Foundation HSE has an unmatched scheme for network diagnostics and redundancy. The application-layer protocol must be chosen with extreme care when deciding to go with Ethernet. Aspects of a protocol that must be understood include completeness, safety, availability (fault tolerance), interoperability, and openness.
Jonas Berg,
general manager,
Smar Intl.
Provides Transparent Maintenance and Diagnosis
In today's view, Ethernet technology is increasingly used in applications where high availability is required. This is due to the redundancy issues that can be solved in a cost-efficient way; e.g., while implementing network designs using switch technology. This allows the use of cost efficient hardware, i.e., commercial off-the-shelf hardware, to implement highly available networks that include "traditional" controllers and other fieldbus communication lines.
Second, the detection of a fault in the redundant setup is vital to the overall availability of the system. Switches and controllers must have internal diagnosis functionality. The status information of the switches is monitored by a special network management system that is able to generate alarms for a special maintenance staff alert through, for example, an OPC server using Data Exchange as well as Alarms & Events. This provides additional cost-savings while diagnosis and maintenance become transparent and ultimately more effective.
Karl-Heinz Niemann,
vice president R&D control products and systems,
Regional Center Germany,
ABB
Mind the Details
Unless special care is taken, there are many "single points of failure" in a typical Ethernet installation. Unless there are multiple communication paths between nodes, a single hardware or software failure can deny service to more than one user node.
Ethernet can be non-deterministic. It was designed as a "best effort" system. Even Switched Ethernet requires controlled loading to guarantee timely communications through shared resources such as the switch's output queue and port link.
The configuration of Ethernet networks is anything but turnkey. They have a tendency to require professional administrators.
Ethernet stacks do not lend themselves to maintaining accurate system-wide time without hardware help.
The unshielded twisted-pair cabling used most commonly in Ethernet systems can be affected by external industrial RF interference and sometimes emit excessive radiation themselves.
There are several commercially available solutions to Ethernet "fault tolerance," which purport to mitigate the single-point-of-failure problem. But, assuming some form of LAN redundancy is employed, the following characteristics must be kept in mind.
Determinism, priority, and QOS (quality of service) factors are subject to various competing standards and, given a desire to be free from single-sourced products, the best approach for the time being is to keep overall bandwidth usage low. The determinism is improved by "switched" Ethernet systems rather than hub-based systems but remember, in a client/server system, the link to the server is a shared resource subject to queuing problems.
Problems surrounding the non-uniform design of Ethernet components, the lack of turnkey configuration, and the EMI/RFI characteristics are best solved by dealing with an experienced systems supplier who can test all the elements of a communications system as a whole cloth and recommend a mix of components having the fewest interoperation problems.
The ability to have millisecond accuracy of distributed system time over Ethernet is an emerging technology with a few spot solution suppliers. If the application needs this accuracy of sequence-of-event timings, the solution will have to be found on a case-by-case basis.
Is Ethernet a good idea? We think so and are proceeding strongly along that path. The use of open Ethernet communications in industrial environments requiring critical control capability is a significant technical challenge¯one not being commonly addressed by the off-the-shelf IT-style solutions.
Ron Freimark,
supervisory hardware architect,
Honeywell Industry Solutions
Connections, Error Recovery, and Determinism
Ethernet combines simplicity and low cost, making it an ideal candidate for designs. Because of its wide use, Ethernet comes with low-cost tools and components. This makes it extremely attractive for solutions, as it allows low-cost development and installation. When using Ethernet for industrial control, three areas must be addressed:
1. The electrical connection. For most applications 10baseT or 100baseT, which use telephone-type wiring, are adequate. If there is a noisy environment, then fiberoptics is the best solution (10baseF or 100baseF). Both of these are standard with fiber carrying a small price penalty.
2. The communication protocols typically used are UDP/IP and TCP/IP. UDP is a "connectionless" protocol that requires less overhead in the computers, but potentially could result in lost and unrecovered packets. It should only be used in a benign environment. TCP/IP is a protocol with error-recovery capability. This causes more overhead on the network and in the computer, but is safer when lost packets are unacceptable and should always be used when distance is involved.
3. Finally, Ethernet communication is indeterminant. Any application must take this into account and have a strategy to deal with delayed communication due to collisions and retransmitted packets. A discussion of this topic can be found in our January 2001 issue of ServoTrends.
Jacob Tal,
president,
Wayne Baron,
vp of engineering,
Galil Motion Control
COTS Doesn't Quite Cut It
Because it uses a differential signaling system, commercial off-the-shelf (COTS) Ethernet inherently has relatively good electrical noise immunity. But, as the data rates increase, the immunity to noise typically decreases. Mix in the extra nasty electrical noise associated with many manufacturing applications and you've got the potential for trouble.
But with optimization and enhancements to key parameters for the cable, connectors, and node magnetics, Ethernet can be adapted for use even in tough industrial environments. Couple that with careful attention to network design and installation practices, and Ethernet will perform nearly equally to other industrial control networks.
There are a number of organizations that have written industrial installation wiring guidelines to help the user base successfully design and deploy Ethernet on the factory floor. Rockwell Automation has published wiring guidelines on its web site to aid in the design and installation of EtherNet/IP-based systems. And ODVA has made its EtherNet/IP protocol and industrial physical layer specifications openly and publicly available on their web site.
The connector and cable are very important in surviving the industrial environment. Besides more robust electrical characteristics, an important attribute for connectors used in industrial applications is sealing. ODVA is the first standards-based organization to specify an IP67-rated, sealed RJ-45 connector for use in industrial applications. Already, the connector is available through one vendor (Siemon Co., under the trade name Imax). At least two other manufacturers are in the process of completing their tooling and will make the connectors available later this calendar year.
As mentioned earlier, the cable performance is key in providing a robust high-speed channel. Such cables must be capable of rejecting noise common in industrial environments. A high-speed, differential communications system requires a highly balanced transmission system to maintain noise immunity. Optimizing the cable design for high common-mode attenuation (CMA) is key in rejecting unwanted noise from the system. In addition, the cable jackets must provide protection from chemicals, weld splatter, and diverse temperatures common to the industrial manufacturing environment. ODVA has published cable performance specifications targeted at solving the electrical noise issues. The cable manufacturers are already providing cables with special jacket designs that provide protection from various chemicals and diverse temperatures.
The use of full-duplex switches is critical to using Ethernet for control applications. Switches provide virtual point-to-point connections between devices that reduce unwanted traffic and eliminate collisions. Typical network loading in a control system will be less than 5% using 100Mb/sec. full-duplex switches, making it behave for all practical purposes as a deterministic network. And last, if the Ethernet control segment is going to be linked to the plant/building Ethernet, the network designer should use properly configured firewalls to isolate the network from unwanted traffic and protect it from security problems.
Bob Lounsbury,
sr. physical layer engineer,
Rockwell Automation,
Chairmain of ODVA EtherNet/IP Physical Layer JSIG
Advantages Abound
There are significant advantages in going with an Ethernet solution. Since most companies today use Ethernet within their business systems, extending Ethernet to your automation systems allows you to leverage your current information systems experience and expertise. In addition, the availability of commercial off-the-shelf (COTS) products from countless suppliers provides value pricing and long-term availability. Ethernet also interoperates well with higher-level application packages such as engineering resource planning, asset management, and other management information systems.
But not all Ethernet solutions are created the same. The Ethernet specification defines the physical signaling, connector, bus arbitration, and basic addressing. But Ethernet does not define the format or meaning of the actual message being delivered.
There are many different protocols that run over Ethernet, such as High-Speed Ethernet (HSE), ProfiNet, EtherNet/IP, and Modbus/TCP, as well as countless other proprietary solutions. While these protocols use Ethernet, they essentially speak a different language and therefore will not directly interoperate. Moving data between the different protocols will require a special gateway that incurs additional costs and possible loss of functionality.
The Ethernet specification does not offer a specification for redundancy, which is critical for the automation process. To solve this deficiency, look for a fault-tolerant Ethernet solution that does not require proprietary hardware. For example, the Fieldbus Foundation's High Speed Ethernet (HSE) allows you to build a true fault tolerant network through the use of redundant interfaces and redundant devices. The use of a "hot spare" is fully defined within the HSE protocol. And, the HSE redundancy specification is fully compatible with COTS Ethernet equipment.
When you consider the Ethernet equipment found in your business, simple RJ-45 connectors and $20 hubs will not provide the ruggedness needed in harsh manufacturing environments. To solve these problems, vendors have developed industry-hardened Ethernet connectors and switches that can tolerate the plant atmospheres and vibrations. But the entire facility will not necessarily be contained within a harsh environment. A final solution may consist of a combination of both hardened Ethernet components along with standard commercial switches. Since both are Ethernet, no special gateway is required.
Finally, Ethernet may not provide the complete solution. Consider an Ethernet solution in combination with a proven fieldbus. Ethernet is a point-to-point network. Distances between an Ethernet switch and device are limited to 100 m using wire or 2,000 m using fiber. In addition, Ethernet does not provide network power or offer an intrinsically safe solution. Pairing an Ethernet solution along with a proven fieldbus solution offers the best of both worlds.
Stephen Mitschke,
senior technical consultant,
Fieldbus Foundation
Ethernet Is Evolving
Ethernet is ideal for automation/industrial controls because of the advances in connectivity and I/O flexibility over the last few years. The "off-the-shelf" Ethernet cards have made it a very flexible medium that is easily implemented with both PC and PLC-based controls. Ethernet is not for every application, but it is quickly evolving to fill-in the gaps, similar to the way Profibus and DeviceNet have evolved in the past.
However, Ethernet is most advantageous because the engineers involved with the plant networks have a great deal of familiarity with this technology. Considering other protocols may not do the job for less, it is wise to make the initial investment in Ethernet now and grow your controls with the technology.
Marc Immordino,
product manager,
Wieland Electric Inc.
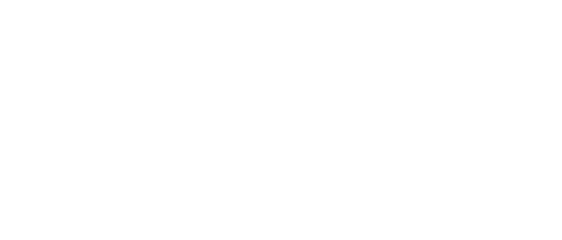
Leaders relevant to this article: