Maintainability can be defined as the ease in time and resources of retaining equipment in or restoring it to a specified operational condition. It directly affects the bottom line because it impacts operations, downtime, maintenance costs and safety.
In 2002, William L. (Bill) Mostia Jr., PE, was principal of WLM Engineering, League City, Texas. Mostia has more than 30 years experience applying instrumentation and control systems.
Maintainability is an important aspect of any system lifecycle, but some machine design engineers may not give it the direct consideration it deserves. This is primarily the result of a short-term view of capital project costs that fails to consider lifecycle costs and downstream activities.
SEE ALSO: Industrial Machine Design: Leap of Faith?
There is an old belief among maintenance personnel that, "The designers and engineers have it for a year, but maintenance has to live with it for 20 years." There is considerable truth to this because many times the machine builder or system integrator and the customer’s engineering and maintenance groups are driven by different metrics, leading to conflicting interests. The result is a rather expensive proposition for a company in the long term, but not for this current quarter; and that makes the bean counters happy.
This article takes a broad view. It discusses some of the qualitative aspects of maintainability of instrument systems, but is also applicable to many other systems.
Understand Your System Constraints
Document, Document, Document for Maintainability
First Principles
Before starting a system design, keep two principles in mind: minimize maintenance from the beginning, and get customer maintenance people involved whenever possible.
Reliability is a cornerstone to successful system operation and directly affects system maintainability. The more reliable a system is, the less maintenance it will require. Allocate costs carefully. For example, maintainability is best improved if the difficult-to-maintain parts of a system are made more reliable. Identifying reliable components, installation types and arrangements, and vendors is a key step to improving the reliability of instrument systems.
Adding fault tolerance can reduce downtime to zero and allow repair off line. More components, however, will raise the overall maintenance rate.
Getting maintenance involved early in a project can improve maintainability. This seems like a no-brainer, but your customer's company politics, local turf wars, personalities and sometimes even arrogance interfere with what is obviously a good practice. Involvement also brings ownership and an improved relationship between maintenance and engineering. At the very least, maintenance won’t be able to complain about the system if they were involved in the design.
The somewhat overworked acronym KISS (keep it simple, stupid) applies to maintainability. While we live in an increasingly complex and sophisticated world, we should strive to keep it simple wherever we can. You can design something that is really cool, sophisticated and elegant, but if it’s too hard to maintain, it will waste everyone’s time and end up on the junk heap.
Modular design divides the system into physical and functional modules, which can be arranged to facilitate design and maintenance. Easily replaceable modules with logical organization can reduce repair time, troubleshooting, training and engineering. Interconnectivity and interoperability should also be considered.
Modular design of software can do a lot to improve its maintainability.
Some thought must be given to future modifications or expansions. Nothing is static in a factory; improvements are made, additions are built, and things are modified. The design group must consider what the future may hold and make reasonable accommodations.
Standardize and Label
Using recognized national, industry and company (if your customer has them) standards and codes is good practice. It improves maintainability by reducing variations of design and installation for maintenance personnel.
Standardization of components reduces inventory and improves reliability and maintainability. The use of commercial off-the-shelf components also should be considered, though care should be taken because some commercial components may not meet the necessary industrial requirements.
While many instruments are unique and the technology can change rapidly, standardization of instrumentation can have the same benefits of reducing inventory and improving reliability. In addition, training and engineering costs can be reduced. Successful standardization requires that an OEM or system integrator's customer use proper reliability engineering techniques, and keep and analyze maintenance records to determine what should be standardized on.
Many systems consist of a variety of the same or different manufacturers' instruments. In some cases, these instruments are arranged in proprietary configurations. In others, the systems are more open, leading to some ability for spare parts interoperability, which can improve maintainability.
Out in the plant, system components must be easily identifiable. Labeling must be consistent, standardized, clear and accessible. While not a substitute for drawings, system identification that provides the capability of tracing wiring, power sources and identification of components without drawings provides for more efficient and safe troubleshooting. Proper identification is also a safety consideration because it can help ensure that the proper things are worked on and that hazards are properly identified.
Access Is Critical
Accessibility means having sufficient workspace and access to perform maintenance safely and efficiently. Adequate workspace is needed not only to repair or maintain the system, but also to troubleshoot it. Consideration should be made for opening of doors or removal of panels, removal of parts or modules, required manipulative tasks, needed body and tool positions and movements, duration of the access and potential exposure to unsafe conditions during access.
No instrument tech should need to have a four-foot tentacle with eyes on the end to work on equipment, nor should he or she need to be a foot tall or eight feet tall. If the access is difficult, short cuts will be taken, and undesirable results may occur.
Once there, we need to be able to see what we're working on. Lighting level and direction as well as component size, location, orientation, texture and coloring should all be considered.
Component accessibility within an instrument or piece of equipment must also be considered. Low-reliability components should be the most accessible. Components should be replaceable with the least amount of handling. It shouldn't be necessary to move or remove a bunch of stuff to get to what needs to be worked on. Consideration must be given not only to how a component will be removed and replaced in an instrument or system but how the component will be handled once it's outside of the instrument or system.
Physical accessibility of field installations is important. This is a balance of functionality, cost and reliability. Safety, however, must also be a prime consideration. One approach is to look at how often the instrument is accessed, and, if it's not often, perhaps the access can be done by a scissor lift or manlift, or with strict administrative and safety controls. On the other hand, if the instrument is expected to be accessed often, an access platform is probably warranted.
Exposure of the system to environmental conditions and stresses generated by other equipment, such as heat, vibration, moving parts, etc., must be considered. If an instrument is hard to get to, environmental protections and exposure guards may be bypassed to make maintenance easy in the short term. This may have negative long-term consequences.
Systems that are hard to work on may encourage unsafe work practices. Remember that the number of short cuts taken is directly proportional to the difficulty of a maintenance activity.
Streamline Testing and Troubleshooting
Equipment that's difficult to inspect or test will be less likely to be inspected or tested. Short cuts will be taken, potentially leading to not getting the desired benefits of inspection and testing.
A system should be easily tested for troubleshooting. Consider the failure modes and how they'll be detected.
Any adjustments should be simple, and the system should be designed to minimize the adjustments necessary to keep it running properly. An instrument's drift specification is an indication of how often adjustments may be required. If an instrument or instrument system requires frequent tinkering to keep it running, maintainability will be low and operators are likely to not trust the instrument.
Modern equipment typically comes with self-test diagnostics, some more than others. The required level of diagnostics is a function of the "invisibility," or level of abstraction, of the internal functionality of the instrumentation. For example, the level of abstraction for something you can measure with a meter is different from what is happening inside a microprocessor, hence, the level of diagnostics is different.
Diagnostics are not just the domain of the equipment supplier. The addition of low-tech blown fuse indicators, process variable indicators and pilot lights can go a long way toward speeding up maintenance/repair time. The use of internal status or alarm bits in programmable devices and user-designed diagnostics are another fertile area. System capabilities today make it possible to access a computer's internal diagnostics, and the resulting displays can enhance maintenance capabilities. Look for opportunities to add cost-efficient diagnostics to the instrument systems.
For diagnostics to be successful, they must have comprehensive coverage and provide speedy localization of the problem. They must also be understandable. Cryptic or generalized error messages or poorly documented diagnostics can limit their effectiveness — if a technician can’t understand what the diagnostic system is saying, how can he identify the problem?
Prevent and Predict
Equipment that is not easily accessed or is difficult to work on will be less likely to receive preventive maintenance. Maintainability is a function of the amount of preventive maintenance, but it is a complex function. The more work required to maintain a piece of equipment, the less maintainable it is. But on the other hand, the preventive maintenance also reduces the potential for failures, which improves maintainability.
Predictive maintenance, on the other hand, allows one to detect problems early and schedule maintenance when resources are available and operational needs are more easily met, which can improve maintainability.
New technologies such as web-enabled monitoring, maintenance-based artificial intelligence, multimedia data access, wireless sensors, improved diagnostics and self-validating devices will allow improved monitoring of equipment and systems, which will enhance instrument maintainability.
References:
1. Reliability, Maintainability and Risk, 5th Ed. David J. Smith, Butterworth Heinemann, Woburn, Mass., 1997, ISBN 0 7506 3752 8
2. Maintainability & Maintenance Management, 3rd Ed. Joseph D. Patton, Jr, ISA, Research Triangle Park, N.C., 1994, ISBN 1-55617-510-8
3. Assurance Technologies-Principles and Practices, Dev G. Raheja, McGraw-Hill, New York, N.Y., 1991, ISBN 0-07-051212-4
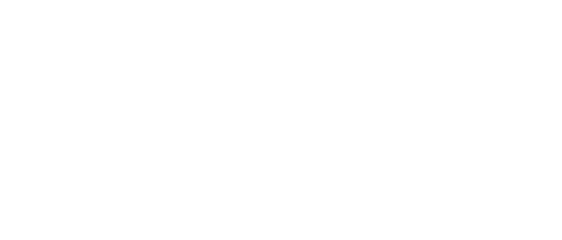
Leaders relevant to this article: