As we move full steam into 2007, several trade associations and experts from various industry segments have offered their 2006 market estimates and earlier looks at 2007 and beyond.
The leading manufacturers of semiconductor equipment projected 2006 sales will approach $41 billion according to the year-end edition of the SEMI Capital Equipment Consensus Forecast, released in December by SEMI at the annual SEMICON Japan exposition.
SEMI is a global industry association serving companies that provide equipment, materials and services used to manufacture semiconductors, displays, nano-scaled structures, micro-electromechanical systems (MEMS) and related technologies.
The forecast indicated, following a 12% market decline in 2005, the equipment market would grow 24% in 2006. Survey respondents saw the market growing at a single-digit rate in 2007, double digits in 2008 and then back to single digits to reach $50 billion in 2009.
For most of the past year, our industry experienced a significant increase in demand for semiconductor devices, as well as strong economic conditions, said SEMI president and CEO Stanley Myers. SEMI members experienced strong overall sales of chip manufacturing equipment in 2006, and anticipate a 50 billion dollar market within the next three years.
Wafer processing equipment, the largest product segment by dollar value, is expected to grow more than 26% in 2006 to $29 billion. Survey respondents anticipated the market for assembly and packaging equipment will expand 13% to $2.4 billion in 2006. The market for equipment to test semiconductors is expected to increase by about 22% to approach $6.5 billion this year.
The Japanese market, projected to grow 11% this year, remains the largest market region for worldwide equipment sales with $9.11 billion of new equipment sold into the region in 2006.
South Korea continued its expansion in 2006, with an expected 20% growth. Sales of new equipment in China and the Rest-of-World market regions grew 80% and 31% respectively.
The SEMI Year-End Consensus Forecast is based on interviews conducted between late October and November 2005 with companies representing a majority of the total sales volume for the global semiconductor equipment industry.
Printing and Converting Outlook
Veteran printing and converting industry consultant Ray Prince outlined a series of industry-wide trends during Novembers Graph Expo and Converting Expo in Chicago that he believes will shape many of the new press purchases expected to in the coming years.
He discussed the advantages and drawbacks of buying used and rebuilt equipment in addition to the benefits of buying new, including obtaining a reliable warranty from a strong supplier. When buying a used press, he urged attendees to keep in mind that there are no lemon laws for presses.
My prediction is that the next hot-selling press is going to be a seven-color with coater, Prince said. These presses will print in the four process colors plus orange, green and blue, and might offer major productivity gains through minimizing wash-ups and other between-jobs requirements.
Machine builders that offer the ability to eliminate wash-ups alone could be a major gain. With a full wash-up on a 40-in sheetfed press taking about 20 minutes, if Im doing six of those per shift, and I can eliminate that time, what that does for productivity, he exclaimed.
Longer presses, including perfectors of 10, 12 and more colors, are another major trend, believes Prince. With these presses, I can do one makeready, print one time through, with no work in process, and have one drying time, not two, he reasoned. I can decrease the amount of floor space on the floor for drying loads. The reason the long press is selling as opposed to web presses is that a 10-color perfector can do a variety of jobs rather than just one.
Another big trend is press accessory systems designed to reduce makeready time. It is amazing what some of these devices can do, Prince added. If I were looking at a new press today, anything that says it can save makeready, buy it!
Theres also a strong trend toward building presses specifically to execute particular types of jobs. We did it in web for years, he said, and now were starting to see sheetfed presses being built basically to handle a very specific product.
Prince also suggested that remote service on new equipment is absolutely essential. You cannot have presses down.
Professor Emeritus Frank Romano of Rochester Institute of Technology told a Graph Expo and Converting Expo luncheon session that after a steady, long-term decline in its number of employees, the industrys workforce is stabilizing, Romano said, partly because we no longer have many jobs left to cut.
Instead, he explained, future incremental gains in technology will have to come from equipment.
The spread of automation through all industry processes will help print combat several challenges that have tested the business in recent years. Romano noted, for instance, that competition from low-wage regions of the world will soon fade as a major concern.
As nations such as China achieve more success in world markets, the countrys standards of living and its citizens expectations rise. This will tend to increase labor costs for these markets, at the same time that automation is steadily reducing the labor component of production cost in the United States. The Chinese situation probably is not going to be an issue for very long, said Romano. Over time, transportation costs for the finished product will negate the savings on labor, and print work will start coming back to the U.S.
Also driving this trend will be the growing emphasis on fast job turnarounds and short press runs, Romano added. Wherever there is a need for immediacy--and that is the trend--we will have an advantage.
Printers revenues have increased in recent years even as the volume of print produced has gone down, Romano said, and he attributed this development to printers adding ancillary services like mailing and database management to their client offerings.
You no longer can survive by just putting ink on paper, he said. You have to offer a blend of services that your buyers want.
Packaging will remain a strong growth area for the foreseeable future, Romano said. He noted that more tags and labels are printed by commercial printers than by converters, and almost as much folding carton printing is done by commercial printers as converters.
Other foreseen growth areas include RFID and security printing. Printers may be well positioned to be highly competitive operators in an era of printable electronics, Romano said. Security printing, which includes products like lottery tickets, sports event tickets, checks, bonds and stock certificates, will be the next big market, Romano said. There will be new security features built into packaging, he continued. The pieces are all here. Its just a matter of them coming together and the prices coming down.
TOTAL U.S. MANUFACTURING TECHNOLOGY CONSUMPTIONMachine Tool Optimism
Turning to machine tool-related activity, October U.S. manufacturing technology consumption totaled almost $369 million, according to AMT, the Association For Manufacturing Technology, and AMTDA, the American Machine Tool Distributors Assn. The total, as reported by companies participating in the USMTC program, was down 9.9% from September, but up 41.4% from the total of $260.6 million reported for October 2005. With a year-to-date total of $3,188 million, 2006 was up 28% compared with 2005.
It has been two years since there has been two consecutive months with year over year growth as strong as this September and October, says John B. Byrd III, AMT President. This indicates that manufacturing technology equipment order growth is accelerating, not slowing.
The United States Manufacturing Technology Consumption (USMTC) report, jointly compiled by the two trade associations representing the production and distribution of manufacturing technology, provides regional and national U.S. consumption data of domestic and imported machine tools and related equipment. Analysis of manufacturing technology consumption provides a reliable leading economic indicator as manufacturing industries invest in capital metalworking equipment to increase capacity and improve productivity.
Latest from Industry News
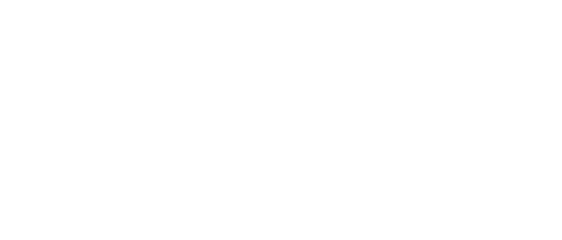
Leaders relevant to this article: