Mike Brooks has a dream. Chevron’s technology architect presented his vision for the next generation of IT systems, aligned closely with business processes and based on shared repeatable work processes in the production management domain, at the 2008 Yokogawa Technology Fair & Users Conference in Houston. And he’s looking for vendors that can help him to bring his plan to fruition.
By combining information integration with work process integration, Brooks hopes to create a ubiquitous framework for all applications, where IT functions support the business and where data access meets the needs of the work or process.
Dream a Little Dream
Chevron Technology Architect Mike Brooks would like to see IT systems align with business processes.
Source: Putman Media
“If you really want to get this done in this production management space, you need a framework to support the IT process and a place to build the work processes,” said Brooks. “It has to be a flexible IT architecture. We need an event system with triggers. At the end of this I want a work process. It looks like a football playbook. As things change we can put it together in an institutionalized way. We’ve got data modeling, but data warehousing has to be built into the system.”
Institutionalizing custom work processes, to not only lift performance but also to capture the knowledge of retiring employees, is one of the cornerstones of Brooks’ vision. “How do we get the knowledge from the guy on the third shift who always seems to know what to do?” he asked.
Turnover destroys knowledge and processes, he said. “In the production management space, we have process engineers, and each one of them still does things a different way,” explained Brooks. “When a new guy comes in, he spends two years developing new spreadsheets because the ones his predecessor created don’t make sense to him. Then a new guy comes in, and he does the same thing.”
Brooks advocated collaborative work processes enabled by, but separated from, IT underpinnings; secured data within primary systems but easy, seamless data access and sharing for secondary users; and isolated implementation and vendor packages.
“We now have an opportunity to remove the work process from the IT underpinnings,” he explained. “If I’m in any manufacturing plant, there ought to be one place I can go to find anything I want, whether it’s real-time data or startup and shutdown procedures.”
The answer to the implementation is in reusable building blocks via services-oriented architecture, said Brooks. “We’re not making shampoo. When we screw up, we get more than bubbles everywhere. Services-oriented architecture is part of the solution, and not part of the problem. Reusable services enable nimble IT architecture.”
Wireless Growth Must Be Managed
Wireless applications in the plant environment continue to grow. Unfortunately, that organic growth of wireless devices and networks can become a tangled web of interference, according to Apprion CEO Mike Bradley, who also spoke at the Yokogawa Users Conference.
“As a plant becomes wireless and those circles get bigger and cover more of the map, it has to be managed,” he explained. “You may have 5,000 points from 25 vendors, and each one has a different configuration and management tool.”
Unravel and Reweave
Wireless applications can be a tangled web, said Apprion CEO Mike Bradley.
Source: Putman Media
Because so many wireless applications are being added, all on different systems and with varying bandwidth requirements, a plant’s myriad wireless networks need one management system that sits on top to coordinate communication and avoid interference.
“There are many frequencies and protocols for a number of good reasons,” said Bradley. “There are many different application requirements for wireless. Different needs dictate different technologies.”
Technologies such as cellular, RFID, Bluetooth, Wireless HART, WiMAX, Wi-Fi and UWB all are competing for bandwidth. The same goes for the applications. Industrial sensors and gateways, asset tracking, PDAs, VoIP and video cameras all have their own needs in the wireless environment. Combine all that with varied costs and complexity—from passive RFID to proprietary systems—as well as multiple power-consumption levels, and you’ve got a roadmap for the state of confusion.
“It’s not just the level gauges,” explained Bradley. “What is needed is a standards-based system that’s open, extensible and industrially rugged. And it needs to work with sensors, access points and networks.”
As early adopters of wireless technology in their plants find themselves trying to unravel and reweave their networks, many of them are revamping their entire plants under one strategic system, while some organizations are still suspicious of the reliability of wireless applications altogether.
One company, the Lower Colorado River Authority in Austin, Texas, needed to resolve its radio-based communications with the public-address system of the Sim Gideon power plant when the two merged. When management received the price for a new hardwired PA system and realized many of the Sim Gideon systems were reaching the ends of their useful lives, it decided to turn the entire plant into a giant Wi-Fi hotspot.
Apprion also estimates more than 45% of the global 76,120 plants that could adopt a wireless infrastructure will in the future. “That’s more than 34,000 plants worldwide,” said Bradley.
Industrial users say their apprehension to adopt wireless technology primarily is because of interference from physical barriers and other RF equipment, along with the perceived difficulty to integrate the applications, according to user studies Bradley presented. In other study results, users cited device interoperability, data security concerns, interference again and the lack of standards as major points of concern.
The value of industrial wireless can be measured by business units in cost of goods sold, safety, security, compliance and sustainability, said Bradley.
Sources of the value can be measured when you analyze it by use. Framework vs. point-to-point and common-device configuration, industrially rugged C1D1 and C1D2 network nodes and common network maintenance and monitoring, for example, can be used to minimize implementation, operations and training costs and to maximize network uptime and equipment availability, said Bradley. And these uses can be measured in terms of met production targets, number of safety incidents and FERC, OSHA or EPA penalties.
The future of wireless will see the technology continue to expand, explained Bradley. “Today it’s many proprietary point solutions,” he said. “Three years from now, they will be standards-based, open and extensible framework. Today it’s process plants. In the future, it will be all industries. Most wireless activity is in North America today. In the future, it will be global.”
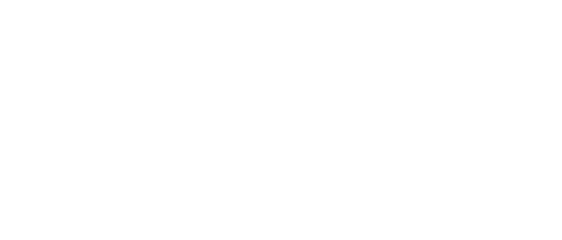
Leaders relevant to this article: