The biggest trend affecting all businesses, but especially the industrial automation business, is the extremely tight labor market. Other important trends affecting this sector are supply chain problems, the push for more safety and reliability in manufacturing, and the increasing complexity of the automation ecosystem.
Increasing automation in manufacturing is the obvious solution to an extremely tight labor market. In 2018, the World Economic Forum predicted that robots will have displaced a total of 75 million jobs worldwide by the end of this year. The use of industrial robots has tripled in the past 10 years, according to a report from Statista, and this trend has only accelerated recently, especially in the manufacturing industry. In fact, California Manufacturing Technology Consulting reports that 90% of all the robots in the world are found in factories. As more robots are equipped with artificial intelligence, which makes them much more versatile, the presence of robots on the manufacturing floor is going to grow even faster.
Also read: Jack of all brands, or master of one?
Contributing to this significant rise in the use of robots in manufacturing is the dramatic decrease in the price of robots, as Statista has pointed out.
The use of robots is no longer limited to large manufacturers. Middle-market manufacturers can now afford to use robots instead of humans on their lines, or to use robots that work with humans—so-called cobots—in order to shorten production time, increase quality and decrease payroll costs.
Because today’s tight labor is demographically driven—a smaller generation of workers is replacing a larger one—this problem is likely to be with us for some time, which means the drive to automate manufacturing is only likely to accelerate in the future. And, because the same supply chain issues that are bedeviling the economy are present in the manufacture of robots, manufacturers would be wise to get ahead of the curve and order today the robots they are likely to need tomorrow.
The second trend driving automation in manufacturing is businesses’ desire to “de-risk” the supply chain, as many have recently experienced the pain that can come from depending on others to provide parts or to handle some aspects of the manufacturing process. Just-in-time manufacturing, which depends on carefully managed supply lines, is becoming a relic of the 20th century because manufacturers can no longer depend on others to meet delivery schedules. The most tangible effect of this move to solve supply-chain problems is the onshoring of manufacturing—moving it from countries like China, which are becoming more closed economies and more competitive to non-Chinese businesses.
Because labor rates in America are much higher than in China, and only moving higher as the labor market tightens, this move to onshoring manufacturing is also fueling the rise of automation because manufacturers cannot afford a Chinese-size workforce to maintain the same level of production. And, because America is a world leader in artificial-intelligence technology, the onshoring trend is likely to exponentially speed up the use of automation in manufacturing as American plants apply advanced technology to their operations, instead of relying on an offshore plant to figure out ways of enhancing productivity.
The third trend driving automation in manufacturing—the increasing demand for safety and reliability in manufacturing processes—is not a new issue, but one that is receiving increased emphasis due to stepped-up government regulation and a more sophisticated workforce that is hyper-aware of safety issues and is more empowered because of the tight labor market to demand that safety be a priority.
As Ron Moore, an author and expert on manufacturing excellence, has pointed out, reliability and safety go hand-in-hand. A reliable machine is a safe machine because it acts in predictable ways and, thus, is less likely to cause an accident. Moore’s research has proven that worker injury goes down as the reliability of manufacturing equipment goes up. Automated equipment, of course, is the most reliable and predictable—thus, safe—machinery on the planet, so the growing demand for safer manufacturing is invariably leading to greater use of automation. I see no reason why this trend will do anything but become stronger and more prevalent in the future.
The final major trend we are seeing permeate the industrial technology sector is the ever-increasing complexity of the automation ecosystem. There is greater computing power in the field than ever before, more sensors and instruments, more complex devices, including those enhanced with artificial intelligence, and more complex systems in general. And everything has to talk to everything else, not just within a single plant, but plant to plant, country to country, and from manufacturing to distribution to retail.
Every move we make to use automation and AI to enhance the manufacturing and distribution process adds further complexity to the entire system, and this is where automation can create problems, as well as solve them. Perhaps the most pressing issue in manufacturing is the integration of different devices, different analytics and different software platforms in the manufacturing process. Industrial technology companies that can successfully address this problem—a problem that will only get worse as automation becomes more ubiquitous in many industries—will have a definite competitive edge in the coming years. Indeed, a company that can assure that divergent systems work smoothly together will be positioned to call the shots in the industrial-technology sector, as it will become the maestro conducting all the players in the manufacturing symphony.
It is an exciting time to be in the industrial technology business as all the major trends—a tightening of the labor market; the desire to de-risk the supply chain; the drive to safety and reliability; and the incredible complexity of the automation ecosystem—point to the ever-increasing importance of automation, and the move to onshoring manufacturing will only speed this up.
Gene Bazemore is a managing director with investment bank Founders Advisors, based in the firm’s Dallas office. He co-leads the industrials practice and leads the firm’s automation and IIoT sector. Gene has more than 20 years of experience acting as both a principal and advisor to companies executing mergers and acquisitions, joint ventures, and debt and equity financings. He began his career as a process controls engineer and transitioned into investment banking, where he specialized in industrial technology areas such as automation, instrumentation, sensors and electronics. Contact him at [email protected].
Latest from Financials
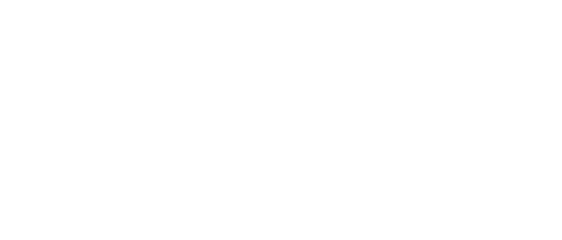
Leaders relevant to this article: