By Hendrik Stoltz, Elopak
A machine OEMs transition to the world of modular design is like a journey. In the case of Elopak, the journey begins with a visit to the supermarket to understand how critical modern machine design is to a liquid food packaging company such as ours.
Look on any gable-top carton of milk, juice, even sugar or molasses, for the Pure-Pak logo. Elopak was formed in 1957 as the European licensee of Pure-Pak and became a major supplier of Pure-Pak cartons in Europe. In 1987, Elopak purchased the U.S. assets of Ex-Cell-Os packaging systems division. Today Elopak, based in Norway, is one of the worlds leading companies within liquid food packaging.
The Pure-Pak carton forms, shipped flat to dairies and other liquid food distributors, look to the consumer much like gable-top cartons have always looked, but Elopak also designs and builds huge machines with technology to fill Pure-Pak cartons. Our Elopak subsidiary in New Hudson, Mich., is the main global production source for Elopaks filling machines, like our Pure-Pak P-S120UCUC stands for ultra cleanwhich in our view is the cleanest high-speed filler on the market (Figure 1). It can form, fill and seal 12,000 cartons/hour in sizes up to one quart or 1.15 l and insert a plastic screw cap. It offers features like a HEPA clean air system, individual clean-in-place (CIP) stations, carton sterilization and hygienic filling. Almost 11-ft tall, the main body of the 15-metric-ton machine is a tight squeeze for a 40-ft ocean container. It has more than 2,000 electrical components, and its electrical documentation PDF file is about 25 MB, or 750 pages.
Time to Change
All of our machines offer options that to this point have been designed into each individual unit. That approach entails a great deal of duplicate design. We came to the realization more than two years ago that we had to change the way we do our engineering. In essence, we had to turn the organizational structure upside down.
Modular Necessity
Figure 1: Elopaks P-S120UC filler has more than 2,000 electrical components and its electrical documentation PDF file is about 750 pages. Anchoring its new design strategy around a new E-CAD approach allows Elopak to offer different configurations of the same machine as standard.
Source: ELOPAK
Concurrent with the launch of the TDMU project, we concluded that our existing electrical computer-aided design (E-CAD) software was woefully inadequate, prone to generating incomplete reports, dropping drawing files and data and failing to reproduce some graphic elements in PDF files. Much time was lost verifying the accuracy and completeness of work. Hundreds of pages of data per project had to be entered and verified manually to generate reports.
Of critical importance, vendor support was virtually nonexistent, and neither the software nor the vendor could accommodate our TDMU objectives. We felt that our E-CAD software should be like a traveling partner in this project, helping to broaden the possibilities rather than being a passive observer or, worse, a hindrance.
The Analysis Is Clear
An analysis by one of our electrical engineers, Michael Ballinger, showed our legacy E-CAD was costing Elopak in a range of $25,000-$30,000 annually per engineer, based on $20 for each hour of lost productivity caused by its deficiencies and insufficiencies. Elopak has six electrical engineers for hardware design, so the annual lost productivity cost could exceed $150,000.
Ballinger was tasked with performing an analysis of possible replacement E-CAD packages. Our objectives were to achieve greater stability, reliability and productivity through increased design automation. To keep up with global standards, we needed to adopt IEC/DIN standards, which have been driving the global language in electrical design. These objectives all were designed to help facilitate introduction of TDMU. Moving toward parts standardization compelled us to give consideration to how our parts database could be accessible through the E-CAD.
We established an objective drawing competition between two E-CAD finalists. The package consisted of PLC I/O, a heater circuit, a controlled-loop PID, terminal diagrams, panel layouts, power generation and associated reports, says Ballinger. Both programs could do macros, although each does them differently. We wanted to know how much time and how many mouse clicks it would take to draw that circuit in both E-CAD environments, implement the I/O in that circuit, put the panel layout on paper and generate the reports, and to compare the reliability of the reports.
The test proved to be no contest because the other vendor pulled out. Eplan exceeded our expectations, says Ballinger. I had implemented the competing E-CAD system at my previous employer and had a very favorable impression of it. I didnt know Eplan. The other vendor should have stayed in the competition, but Eplan still would have won based on how it performed.
One area where Eplan clearly outperformed the competition was a series of little shortcuts integrated into the software, adds Ballinger. For instance, Eplan automatically draws the wire connections between devices and allows the user to name any symbol the same name as another symbol, and cross-referencing is immediately established, he explains. Fast becoming one of my favorite features is the ability to be in the same page as another user over our network and see live updates that they make.
Likewise, we dont believe that tools drive fundamental change, but its fundamental to have the right tools, so people are equipped to make change happen. From an organizational perspective, this applies to all engineering disciplines. Eplan presented a platform concept for us, that is, products built on the same database platform, sharing data and synchronized during all project phases.
Consequently, Elopak purchased Electric P8 and three other Eplan products: Fluid, Cabinet and PPE, along with Eplans application programming interface (API) extension, which was used to create the data bridge between Electric P8 and Windchill. An updated parts database was created and resides in the PLM system, which will feed data back to Eplan.
Our Eplan implementation strategy was to have all electrical engineers trained right away on Electric P8, whether or not they were going to use it immediately. A number of smaller projects were undertaken to ease them into Eplan. Among those was a cap-orientation project to design a stand-alone unit that can be mounted on current filling machines to orient caps with printed logos to the upright position when attaching them to the carton. Another involved the design for a new, stand-alone, servo-driven chain conveyor and linear servo drive carton loader to be retrofitted onto current models.
E-CAD Enabled Redesign
Figure 2: The first machine redesigned was broken down and rebuilt into functional units. Electrical enclosures, cabling and switchgear were reconfigured. With manual processes automated, the job was shortened by 20-25%, compared to its legacy E-CAD.
Source: ELOPAK
Adding the Eplan Project Options module that became available last year led to another project that ties in directly with TDMU. This module automates the creation of machine configurations, says Ballinger. I can select a predefined option from a dialog box and insert it, and the stored values are applied throughout the project automatically in a fraction of the time I would need to redesign it in our legacy E-CAD. The module has been used already to insert all 10 available options for the E-PS120UC, ranging from a simple circuit change on one page to a complete power distribution design change across many pages.
For Mark Taylor, executive vice-president of Eplan in the U.S., one aspect of Elopaks implementation of Eplan stood out. Elopak understood exactly where it wanted to go, says Taylor. It had that vision with its legacy E-CAD but wasnt able to realize it. With Electric P8, Fluid, Cabinet and PPE, it has a complete lineup for electrical, hydraulic and enclosure design and plant process management without having to use three or four different vendors.
Biggest Is Yet to Come
Our biggest project yet in our new E-CAD framework is under way. Were redesigning the controls platform of each of our current filling machine models from a Mitsubishi PLC system to a Siemens Simotion-D Motion/PLC system. The switch to Siemens is a strategic objective to implement what we believe is leading technology and to better conform to the TDMU philosophy.
The first model to complete this electrical redesign is the E-PS120UC. It was broken down and rebuilt into functional units. All electrical enclosures, cabling and switchgear were redesigned for Siemens products, and all motion control was redesigned to Simotion and Sinamics. With the formerly manual processes Eplan automated, the timeline for the job was shortened by about 20-25%, compared to what it would have taken in our legacy E-CAD. We were able to go into the build stage of that machine faster and with far fewer errors than we were accustomed to, says Mike Jessup, Elopaks controls engineering manager.
Ballinger adds, As long as the engineering time is up front and everything is laid out well at the beginning, I think well cut development time in half. Longer-term, we would like to get to the point where the design of all our machines is in Eplan, so when our customer unit sells a machine, they can choose the configuration and the system will give us the prints. Thats not to eliminate my job or my co-workers jobs, but it would let us get away from having to tinker with every single machine and focus instead on developing new technology.
Eplans global orientation has also made it a good fit. Using Electric P8 not only allows our engineers to draw to DIN standard but also convert projects to other standards automatically. Elopak has units in more than 40 countries and customers in many more, and 85% of the machines we build in Michigan are exported. Our engineers will tell you that our new ability to condense data and documentation into a single cohesive, intelligent PDF file for sharing and displaying in different languages and changing languages with ease has proven itself with our customers.
Hendrik Stoltz is director, Elopak Equipment Supply (EQS), and vice president of engineering and manufacturing for Elopak. Learn more about the company at www.elopak.com.
For a complete list of I/O Systems articles, white papers, news and products, visit www.ControlDesign.com/iosystems.
Latest from Vertical Industries
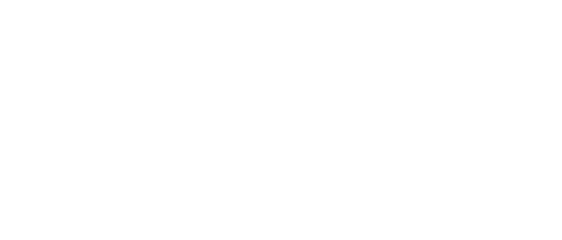
Leaders relevant to this article: