How to keep field service workers safe during COVID-19
While many are able to work from home during the current pandemic, field service workers by nature don't have this option. In this special edition episode, Amanda Del Buono is joined by Stacey Epstein, chief marketing officer and customer experience officer at ServiceMax, to discuss how organizations and individuals can stay safe while keeping essential equipment up and running.
Visit the new Field Service Job Finder from ServiceMax and Krios at https://www.fieldservicefinder.com/
Below is a portion of the interview. The full transcript is available here.
Amanda: Right, right. Well, in previous episodes of this podcast, we talk about workforce development a lot and the key to workforce development is communication. But it seems to me that, at this moment, communication has got to be more important than ever. What advice do you have about keeping the communication flowing between the service workers or the field workers and their management or whomever? What advice do you have for them to be constantly in communication or improving their communication? Or are there different things that they need to be communicating about that maybe they weren't before or they don't usually?
Stacey: Yeah. And we at ServiceMax have a piece of our solution called Zinc, which facilitates communication and really helps get real-time knowledge to workers that are in the field. And it's been quite successful for us, but there have been many times over the course of the last few years when our buyer says, "Yeah, it looks really good, but, you know, it's just not mission-critical in terms of what we're looking at today." And that has just...another thing that has taken a drastic turnaround is that everyone's not in offices where they have access to people and information that they need. So, not only do you have your field service workers out in the field, but you also have the people who have the expertise and knowledge to help them. You have them just in their homes, but you can't prevent that communication from happening because that's how problems get solved, questions get answered and the work continues to happen. So, giving those technicians a way to get to the real-time information they need has become just mission-critical.
Again, communication's not a nice-to-have anymore, it's an absolute imperative for these field service workers, especially as the whole industry is shifting to focus on the current need, which is healthcare. So, again, those non-essential items, I mean, they're not being purchased, they're not being installed, and so, you have workforces that are shifting to do something that they haven't done before. So, if I've changed my manufacturing facility to produce ventilators or whatever it is that I've now shifted my focus, I've got a whole workforce of field service engineers or technicians that aren't necessarily trained or up to speed on how to do that. So, we're asking a lot more of our field service teams and we absolutely need to be giving them the ability to reach out when they have a question to send a message to a hotline and have a one-on-one text conversation or even do a live video, which you can do in Zinc.
I mean, certainly, you could also do it in something like FaceTime, but with Zinc, you know it's secure and you can get them to the right expert. With FaceTime, you don't really even know, "Who do I call," right? But if you use a hotline and you can know that you're getting to the right expert, you can do a quick video call and say, "Hey, I'm trying to install this. I've never done it before. Am I doing this right?" And they can get help in real-time. Then that system can be live and experience full uptime in ways that it just wouldn't have happened if you didn't have that line of communication. So, I think what, again, what we all thought of as, "Yeah, you know, communication's important. But what's more important is that I'm tracking parts and that I'm scheduling my technicians properly," and now it's come to, "Hey, if I can't communicate with my field service team, I'm maybe not able to even get the job done." So, it's just become absolutely critical.
Amanda: Yeah. Yeah. Well, and at least people are seeing that and hopefully acting on it and maybe instituting different technologies or methods to do that like you had mentioned.
Stacey: Yeah. Exactly.
Amanda: So, if I'm a field service worker, what sort of support should I be requesting from management in order to keep safe and minimize my potential exposure to coronavirus? And do you have any advice on what steps field service workers could be taking on their own?
Stacey: Sure. And we've had a lot of dialogue with our customers about this. Again, I think we're all...I was saying yesterday to some of my colleagues as we're continuing to work through the situation, there's nobody out there saying, "Oh, well, you know, when this happened 10 years ago, here's what we did." Like, literally no one's ever experienced this before in the world. So, I think we're all facing new situations and everybody's evolving. We've been doing lots of dialogue with our customers and the heads of service and manufacturing at many of our companies and we've had these conversations of, okay, you know, the field service workers are, by nature, not stay-at-home or shelter-in-place. So, really having to think through how do we keep them safe in a world where they're not even really supposed to be out is a big topic. And so, we've talked about it a lot.
I think from a management perspective, there are things you could do. One is consider a swing shift model where you're scheduling the technicians to service the equipment only while security is on-site and the field service engineer is then given clearance to enter the building during off-hours, right? So, if you've got to go service a piece of equipment, can you go service it while there's the least amount of people on-site in that organization? Staggering the crew, so, limit crew members one per truck versus sometimes they'll have two or three people but if you can keep them siloed, maybe that's better. They're not mingling with each other on-site. I mean, we have a technology feature called Checklist that you can implement to ensure that field engineers are following new protocols, right? And before COVID-19, there were certain checklists that a technician would have to go through to make sure they had done the job properly, but there are now a lot more requirements and as it relates to the safety and the health of the teams.
And so, adding new checklists to make sure that they both follow but also even understand that you’ve got to get those checklists out to the team and if there's not a way to have them follow it in technology, they may not even know what it is. Even little things like our iPad app allows a customer to sign the work order when it's been completed, but you probably don't want that customer touching the technician's iPad 10 times a day, right? So, maybe now's the time to bypass that signature option and let the technician just check a box that says "bypass signature option" so that you don't have hands touching iPads. I mean, it's little things like that that can, I think, really help stop the spread and keep these technicians safe. And then, of course, there's the most obvious, do you have the proper personal protection equipment in the field? Can you supplement the PPE you're providing and give more protection? Do you have hand sanitizer in the truck? Do you have sanitizer and effective soap in the office? It's just little things like that to help remind these technicians to really keep themselves safe and healthy on the job.
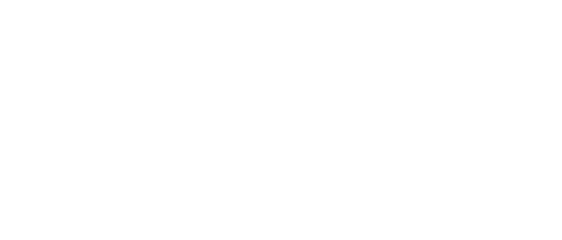
Leaders relevant to this article: