Servo motion control makes thermoformer bigger, faster and less expensive
At SencorpWhite, our latest achievement in thermoforming machinery is the Ultra 2, which we believe is the largest production steel rule die inline thermoformer in the global plastics industry (Figure 1). On the machine, which has a footprint of 50 ft by 11 ft, the process tonnage of 35 tons for form and 130 tons for trim is generated entirely by electric servo motors (Figure 2). And the steel rule die inline arrangement results in faster changeover and an overall cost that is only 10% of conventional punch-and-die systems. Onboard, 44 zones of heating are being controlled by a monitoring system supplied by Siemens, which also supplied the servos and other motion-control components for this machine (Figure 3).
Figure 1: Ultra 2 from SencorpWhite was built to be the largest production steel rule die inline thermoformer in the plastics industry. The newly designed rail transport system produces more output and less waste, while the proprietary off-load system is 70% faster than previous designs.
The genesis of this machine came from a market analysis, explains Brian Golden, product manager for thermoformers at SencorpWhite. “We determined a distinct need among our major industry segments for a more precise thermoformer with optimum control of form and trim operations, as well as a large forming area to increase production,” he says. “The Ultra 2 boasts a 34-by-48-in forming area. Typically, such a large machine would involve major challenges in motion and heat control, especially when running at higher production speeds.” The SencorpWhite engineering team then turned to its longtime suppliers Siemens for suggestions.
Figure 2: Equipped with multiple levels of control onboard, including motors, drives, PLC and HMI, the machine’s motion control system was designed on a singular digital platform, a benchmark for integrated automation design.
The Siemens plastics industry group, headed by Mathias Radziwill and Account Manager Hue Lieu, connected with our team to review all the parameters of the project. “We were challenged from the outset, as SencorpWhite was looking for a faster thermoformer to do higher-end work,” says Lieu. “Likewise, they were seeking ways to achieve faster assembly, faster operation on the machine, overall cost reduction in various areas of heat and motion control, plus finally a greater throughput due to their newly designed steel rule die and proprietary off-loading system. Just another day at the office.”
Figure 3: The steel rule die arrangement provides faster changeover at 10% of the cost of conventional punch-and-die systems.
From pneumatics and hydraulics to servos
SencorpWhite had relied almost exclusively on conventional hydraulic and pneumatic power generation for its previous thermoforming machines. For this new Ultra 2 machine, a comparative analysis was made by Hue Lieu and his team from Siemens, demonstrating to us a full list of advantages to be gained through the use of servo technology.
Chief among those advantages were the cost-to-benefit ratio, resulting from the improved accuracy of servo technology, meaning less material waste and faster time to first article; faster start and stop, which yields a more precise level of operation and also less material waste; lower power consumption, as the motor runs in an as-needed power-generating mode, rather than the conventional always-on mode; and high-dynamic and high-inertia qualities of servos, especially beneficial on this first-of-its-kind massive thermoformer. The material infeed distance and multiple stages of steel rule die operation, combined with the multi-conveyorized off-load stations, made servos an even more sensible choice.
Typically, the machine is running at 26 cycles per minutes, so our claim of “putting more parts in the box” is no exaggeration and represents a clear upside for the end user, who also benefits from the quieter operation of servos, as well as the chief benefit, the substantial power savings, which do vary depending on user workflow and machine run time.
“When you combine the size, speed and quality of this machine, plus the energy savings of servo technology, there is simply no comparison with any other machine on the market today,” says Golden. “Our partnership with Siemens on this project resulted in a better machine with trackable upsides for us and our customers.”
Servo technology gained popularity on high-precision CNC machinery but is now found throughout various industries, running injection-molding machines, extruders, various metal forming press designs, overhead cranes and heavy-duty lifts. Servo motors have recently found more acceptance in the converting world, where the load characteristics change constantly and the need for waste reduction at higher production speeds is paramount.
Servos typically involve less space and are often packaged with absolute or rotary encoders, as well as drive components. Siemens offers its Drive-Cliq open encoder interface for automatic configuration through electronic rating plates and faster system diagnostics.
Sencorp has embraced this new technology with the full expectation of improved performance and trackable benefits for both our customers and our own operations.
Time to prime
Overall, this machine was in development approximately two-and-a-half years, with the bulk of the engineering focused on the electrical and electronic controls. “The Siemens team brought our unique Totally Integrated Automation (TIA) Portal to the challenge,” says Radziwill. “This system enables complete access to the entire suite of products and software available, allowing machine builders to engage in a totally digital enterprise during machine development, performance evaluations, simulation scenarios, build stages and commissioning; plus it has full diagnostic and energy management tools. Many builders view TIA Portal as the gateway to Industry 4.0 (Figure 4).”
Figure 4: Typical parts produced on the Ultra 2 include packaging for health and beauty aids, food, medical and hardware products.
The key to the machine form and trim tonnage was the implementation of electric servos, which eliminated an array of mechanical components, with their obvious cost and assembly time expense for the customer, explains Lieu. The servos also run the indexers on the rail system, which upped the productivity of the machine by around 40%. With the industry trending toward higher-performance electric servos, we elected to move away from our previous reliance on pneumatics and hydraulic solutions for generating our tonnage.
Siemens also assisted in the development of the proprietary off-loading system on the Ultra 2, introducing the SencorpWhite team to its Simotion D motion controller, which runs the system in 100% servo mode. By use of the Siemens Scout system, we were able to test a number of drives to select the optimum combination of features and price point. This new system utilizes stationary motors, driving the need for coordinated motion control. The Scout system provided the technical solution for this requirement.
Parts produced on the Ultra 2, given its combination of volume, speed and accuracy, range from health and beauty aids and medical packs to clamshell and high-capacity containers or very high-volume jobs, where the increased number of parts per shot has tactical market advantages for customers (Figure 5).
Figure 5: The total footprint for the Ultra 2 is 50 ft by 11 ft.
In production, the inline steel rule dies allow faster changeover for the SencorpWhite customer, in hours not days. The original design called for electric motor drive. “Servos were ideal for this application, and, once we walked through the updated architecture with the guys, we all saw the light bulbs going off,” explains Lieu. “The combination of less manufacturing time, fewer components and the increase in speed with the desired accuracy won the day.”
Component selection
Visitors to the NPE2018 Plastics Show, May 7-11, in Orlando, Florida, can see the Ultra 2 in action at the SencorpWhite booth W591.
On the human-machine interface (HMI) side, the selection of the Panel Pro IP67 gave us the optimum solution for a display that could withstand any anticipated working environment.
For heating control on the machine’s 44 temperature zones, the choice was the Siplus HCS4300 control system, with detailed diagnostics that can detect internal faults in the load circuit, blown fuses and defective heater cable. Network voltage and internal temperatures are also monitored per zone. The heating on the machine is radiated top and bottom, with individually controlled zones for form and trim.
All communication is run over ASI Profinet and CAT3 safety compliance is provided.
On the proprietary off-loading station, we achieve a 99.5% breakout of the web, and the off-loader feeds a parts stacker via a specially designed five-axis servo and three-conveyor motion handling system.
“At the end of the day, we want our customers to have more good quality parts in the box, with less waste, less energy consumed and a lot more profit in their pocket,” says Golden.
ALSO READ: The fundamentals of motion control systems
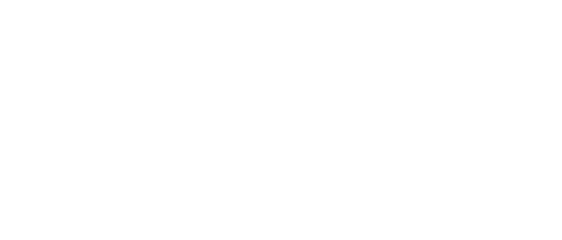
Leaders relevant to this article: