Over the past 10 years, improving plant energy efficiency has been an increasingly important topic of conversation among end users. Oftentimes the discussions will focus on lighting, HVAC or other building systems. Sometimes it will lean toward electric motors or drives and control systems. It seems that almost every inch of a plant has been scrutinized to get the most out of a kilowatt. Almost.
Innovative Manufacturing Services is an OEM/system integrator based in Glasgow, Kentucky. Since 2003, we have been front and center in the energy efficiency discussion when it comes to material handling equipment, controls, custom ergonomic workstations and field services for manufacturers across a variety of industries. As the Americas Distribution Center for Carryline Modular Conveyor Products, our systems are found on a wide range of aluminum and stainless steel products, including side grippers, and 24 mm to 220 mm conveyors.
Our customers are always asking for more “bang for their buck.” At the same time, they expect high-quality, energy-efficient components and are often willing to invest a little more up front to get lower power bills year after year. Sometimes these energy-saving components are well known; other times they come to us as pleasant surprises.
Power efficiency
About three years ago, IMS supplied work center equipment, assembly tables and controls testing equipment at a new Siemens assembly facility in Greenville, South Carolina. The Greenville plant assembles Siemens’ SimoGear family of geared motors, including helical, parallel shaft, and helical bevel gear units primarily used in modern conveyor systems often found in warehousing, logistics and distribution, airport baggage handling, automotive manufacturing and food and beverage processing.
While we worked at the plant, we took special notice of one of the gearmotors that promised to increase productivity and energy efficiency to the highest possible levels. Like most in our industry, we had standardized on a brand of helical-worm gearmotors for almost all of our material-handling systems at the time. We didn’t think there was any energy efficiency to be gained in our choice of gearmotor.
MORE: How to get energy efficiency under control
So, what caught our attention? We built the demo product lift that was used to show the power consumption on the SimoGear B Series, two-stage high-efficiency helical bevel gearmotors. So, instead of simply taking Siemens’ word for it on paper, we had hard evidence for its efficiency claims.
“They were building a new facility in South Carolina,” explains Mike Goad, president of IMS. “We talked with them about what we could do for tooling and work tables. We built them some electrical testers to run the gearmotors. In the course of all that, Siemens became aware that we built and sold Carryline conveyors in the United States, and they were looking for someone to build a conveyance system for the ProMat 2013 exhibition.”
Our engineers met with Siemens, and we sketched out something, which turned into the conveyance system, featuring Siemens components, that was displayed at ProMat. “We always design a control system to get products from Point A to Point B,” says Goad. “But the whole impetus of this project was to highlight and showcase the Siemens gearmotors and to show its field-mounted PLC and other hardware.”
Since a growing number of our customers are looking to reduce power consumption and since motors typically represent about 60% of energy consumed at a plant, we decided to give SimoGear a try.
First installation
The first installation was at a material handling trade show, where we and Siemens assembled a spiral conveyor system that included its SimoGear B Series, two-stage high-efficiency helical bevel gearmotors, as well as Siemens drives and control technologies. Since then, we’ve standardized on the gearmotor because of its efficiency rating, overall quality and good value. We’ve had dozens of installations since then with no startup issues.
“One customer of ours, an appliance manufacturer now has 50 on that system alone,” says Goad. “What we’re replacing with that particular unit is worm gears. They’re just inefficient. Theses are helical bevel, so they’re much more efficient.”
When customers are specific about their power-savings expectations, we can show them what our system with the new gearmotor can deliver. Worm gears are the least efficient type of right angle gearing—about 80% efficient in our applications. The SimoGear two-stage helical bevel gearmotor has a mechanical efficiency of 96%, far better than the worm gearmotors we had been using.
When compared to a standard helical-worm gearmotor, the difference in cost isn't huge, but for the quality of the gearmotor, it's a good price. There are other benefits, as well, like standardized bolts that are used on the conduit box cover, terminal block and ground connection. It's all about saving time for us. Not having to change tools when shifting from doing one sequence to another is a big benefit.
“On some gearmotors, it might take three different wrenches to open the conduit box and make the connections to the motor and the ground connection,” says Goad. “Siemens recognized that and made sure all the fasteners are all the same wrench size. When you’re down on your knees trying to wire up a motor, it makes a big difference.”
Our reality is this: Customers often have a preference when choosing components. Some customers will only accept Siemens, while others will show loyalty to other suppliers. SimoGear works for us because it works with any controls supplier.
“Siemens has its own motor-mounted VFDs,” explains Goad. “It has a standard wound connectable motor. It’s inverter-duty-rated.”
The gearmotors are non-painted aluminum, so they match our material-handling systems. IMS didn’t have to change the mounting bracket, faceplate or hardware. Again, less work means an easier and more efficient transition. We know customers can be reluctant to try something new, and SimoGear is still relatively new in the market place, but those who have tried it are very pleased and report no problems with the technology.
Benefits add up
Figure 1: When you have 50 gearmotors on a system, you save between $25,000 and $30,000 annually.
Since standardizing on the SimoGear gearmotor, we’ve realized other benefits that not only help our customers, but help grow our business, as well. “We have a series of gearmotors that we’ve standardized on, so we know that family of components and what’s available for our needs,” says Goad.
Before, it would take about seven days to receive the old helical-worm gearmotor from the supplier. Our new motor is assembled in South Carolina, and delivery takes only a couple of days. That helps a lot with our planning and inventory. For the customer, it helps exceed the delivery and start-up goals.
At the end of the day, there is the same burning question for every one of our energy-conscious customers: How will the gearmotors impact my bottom line? The impact will be quite positive.
Customers are saving $500 to $600 a year in power costs per gearmotor. So when you have 50 gearmotors on a system, you save between $25,000 and $30,000 annually (Figure 1). Dollars that add up quickly and can be reallocated or simply saved. IMS has extensive experience solving the industry's material handling and automation challenges. That experience allows us to be very successful in meeting or exceeding the goals and objectives of our customers.
Today, those customers are focusing more and more on energy efficiency. Conserving power will become a more sensitive issue in the future, and we all need to be aware of the available options to fulfill those customer requests. We’ve discovered that, once we explain the average savings that can be achieved in the first year of use and beyond, customers are willing to invest in an initial gearmotor purchase to receive the long-term benefits.
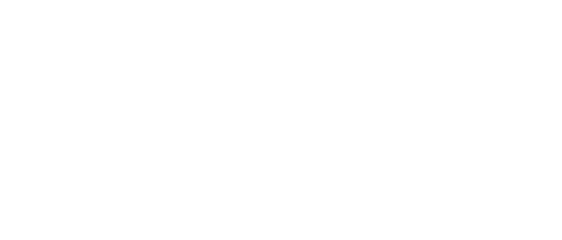
Leaders relevant to this article: