We use DC motors in our load-sharing conveyor installations. The motors are connected in parallel to a DC drive and split the output current equally so they run at the same speed. We have a customer specification to do this with AC motors instead. It appears we'll have to use a variable frequency drive for each motor and are not certain we know how to guarantee they will all run at the same speed. Help.
Answers:
Sized Is Everything
Multiple AC induction motors can be operated from a single inverter provided that the inverter is sized correctly for the number of motors and their respective operating loads. The problem with this method is that the speed of a standard induction motor tends to slip somewhat with respect to the line frequency as the motor's load varies, so speeds will not be synchronous. The solution to this is to use three-phase, inverter-duty synchronous induction motors to ensure that the motor speeds remain synchronous with the line frequency.
Mike Marhoefer,
Mgr., Electronics Group,
Bodine Electric Co.
Go Peer-to-Peer
We have implemented load sharing with both AC and DC drives successfully for many years. Both technologies work equally well but for the topic of this discussion we will concentrate on the AC solution. Taking for granted the motors are mechanically coupled we use two VFDs and configure one unit in speed or frequency control as the master. The slave unit will run in torque control and gets its torque set point from the master. To accomplish this the torque setpoint from the master can be sent to the slave via an analog I/O, but we recommend a peer-to-peer serial communication for greater precision.
[sidebar id="2"]
If the motors are not mechanically coupled, we need to decide what is more important for the application: load sharing or speed matching. If speed matching is the goal, run each VFD in a closed loop vector mode. If load sharing is the goal, use a comparator to bias the speed of one VFD to equalize the loads.
Craig Nelson,
Applied AC & DC Drives Product Manager,
Siemens Industry
This Won't Break the Bank
The answer is first a question of output. What is needed or expected as the output of the conveyor equipment? What resolution is needed to produce perfect product? Inches of conveyor travel equals revolutions of the motor equals pulses of feedback on an encoder either with or without an index pulse. For example, sheetrock is very sensitive and is manufactured good side down. It "moves" as it is in process. This will cost plenty in waste and handling expenses if the individual conveyor belt speeds are not controlled and easily adjusted by regular plant electrical personnel.
What are the variables? Are belts that stretch with age involved and does this growth need to be accounted for? Is the product stable or does it move as it cures? The answer can only be determined after these questions are answered, unless a synchronizer is used on each variable-speed AC or DC drive in the application.
For the retrofit of an existing line, trying not to break the bank, the following has worked with documented, fantastic results for many continuous output process lines.
A master speed control with encoder feedback to close the loop is given a command to achieve a process speed. This controller then controls one of the VSD units to smoothly run a link in the process line. Any number of additional motors with a VSD are then fed a signal from a synchronizer controller that has just one job: "follow with the strength needed to produce perfect product." The only shared signals are the master control signal and an encoder signal. The synchronizer gets a feedback encoder signal from the motor it is controlling to ensure the proper dialed-in digital ratio, 9.9999 to 0.0001, is maintained. Each motor needs a synchronizer control of its own.
The one most important thing to remember is that the conveyor system will tell you which piece of equipment will in fact be the master. This master will be the hardest to start, stop, and maintain smooth motion on. If each other link in the system is driven to synchronize speed with this "slug," the product will move smoothly from belt to belt as in sheetrock, or on parallel pin conveyors as in light bulb manufacturing. The design of master/follower motors in the system may be series, branch, or mixed. Again the system and its product will determine what piece of equipment is directly synched or digitally ratioed to each other piece of equipment.
Please consider the E-stop circuit, too. E-stop the master and let the entire drive system follow it down in a controlled motion. Removing AC power from today's microprocessor-based equipment is at times the worst, most damage-causing way to stop.
J.D. Ryan,
Sales Engineer,
Northwest Power Products
Closed-Loop Drives Work Best
You have options here. With one drive per motor, you can configure the drives in series and tie the analog output (programmed to monitor the output frequency) of the first drive to the analog input of the second, and so on until all the drives and motors are connected. They will follow the reference given the master drive if the analog inputs are tuned properly to provide the correct output frequency. You could use this configuration if the speed control tolerance is reasonably loose or if cost is a concern. Be aware that there may be some time lag between speed changes at the first drive and the last if several drives are connected together.
To gain a higher degree of precision, use closed-loop flux vector drives in parallel. The closed-loop method adds cost but provides the best speed and torque control. In parallel, each drive would receive its own speed reference. Load-sharing would not be a problem because the closed-loop system inherently ensures high degrees of speed regulation that are comparable or superior to DC drives.
For the highest degree of precision, use a closed-loop flux vector drive system with electronic line shafting software built into the drive, or into a PLC. This software will virtually guarantee that all of the motor shafts will rotate at the same speed at the same time.
This also could be done using multiple AC motors in parallel with a single AC drive. If the performance of the DC parallel configuration is acceptable, then an AC solution would work as well. This would have to be done using an open-loop volts/hertz drive, but the performance would be comparable to that of the DC system.
Charles Manning,
Inverter Product Marketing,
Omron IDM Controls
Many Motors, One Drive, One Speed
Connecting multiple AC motors to one AC variable frequency drive will achieve the same result. Since both motors, assuming same number of motor poles, are driven at the same frequency by a single VFD, the motor's speed will be the same at no load. Because asynchronous motors have inherent slip, if one motor has a greater load than the other motor(s) in parallel, its speed will slip more (decline), therefore, transferring more of the load to the other motor(s), essentially, load sharing.
Key applications notes: The inverter should be sized using the following formula: (Motor 1 FLA + Motor 2 FLA + etc.) x 1.1 must be less than or equal to the VFD-rated continuous current. This is because the parallel reactance of multiple motors is less than the reactance of one motor of the same total HP. Working into a lower reactance results in higher current peaks to the drive.
Also, external motor overload devices must be supplied for each motor. The VFD cannot protect individual motors when they're connected in parallel.
Rick Roberson,
Sr. Inverter Application Engineer,
Mitsubishi Electric Automation
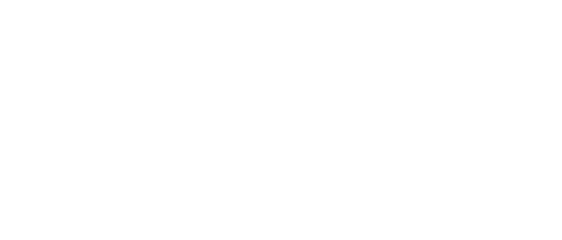
Leaders relevant to this article: