Flexible, agile and ready to deliver
Manufacturers worldwide are struggling to ensure profitability and keep up with rising demand amid an onslaught of challenges. These include environmental and sustainability issues and the need to accommodate product variations with flexible systems. The latest motion-control solutions can help to address these challenges. The combination of new components, development tools and other technologies with deep expertise in motion control can transform a sluggish factory into one that is flexible, agile and ready to deliver the most complicated market demands.
Greg Dieck is product manager, motion, at Omron Automation.
Q: What sort of motion-control technologies are enabling manufacturers to implement the agility and flexibility they need to meet market demands and product variations?
A: Flexibility has become a big concern especially as machines get more specialized. The utilization of specialized and even custom-made mechanics, motors and even drives has grown. The ability to be able to implement these products together and maintain a unified system has become a challenge. The use of open industrial networks has helped, but there are still challenges as some networks are designed for very specialized products. Being open to creating and using software that eases the time and pain to configure can help machine builders make the fits their application the best.
A: Industrial networks have allowed machine builders to choose products that fit their application and still make them work together as a complete, singular solution. The ability to put the drives on the machine closer to the motor has improved machine design. The network allows real-time monitoring that can be used in the controllers programming by the engineer to create custom functions in the controller that help keep the machine running at peak performance. These custom functions could be things like collision detection, heat sealing and changing drive tuning based of product change, as well as many others. As these networks use higher speeds, we can gain more accurate control of the motion control. With the higher bandwidth of the network, tuning can be shared by the drive and the controller to bring new capabilities to the industry. This allows for higher accuracies creating a better product while also producing less waste at the same time.
Q: How does the motion-control network help with configuration, control and even maintenance of motor/drive systems to improve sustainability?
A: Utilizing an industrial network brings benefits to many aspects of the machine. Use of a network can simplify wiring of the machine and save tremendous amounts of time during manufacturing. Configuration, programming and monitoring can now be done from a single software package and a single backup file for the entire machine. Startup and programming can be done from a single connection to the machine eliminating time to walk around and connect to different components to configure them. Monitoring can be done to multiple aspects of the machine through the network, and software packages can trace many parameters so that in-depth analysis can be done to check the performance and accuracies of the machine. The network also brings improvement to maintenance and overall equipment efficiency (OEE). Components that have parameters that need to be set, like a servo drive, can have those parameters stored and downloaded right from the machine controller. This eliminates time to get a laptop with the configuration software and downloading the parameters from a configuration backup file. Some drives now have warnings that components, such as fans or capacitors, are having problems and may be close to the end of their lives. This allows for predictive maintenance before the component failure would cause downtime.
Q: What impact have remote monitoring and connectivity had on the maintenance and useful lives of motion-control components?
A: Keeping a machine running at its peak performance and productivity is always the goal. We can use industrial networks to monitor components and watch for problems that are building—heat, high current, fan failure, capacitor life.
Omron is expanding products to be able to monitor components and monitor their health. This allows products close to the end of their life to be replaced during the maintenance shift where the machine is not in production to reduce failures and downtime.
Q: What innovations is Omron developing to improve speed and accuracy in motion applications?
A: We have seen more machines that are needing high speeds while maintain very high accuracies. Maintaining both high speed and accuracies takes a lot of power from the controller’s CPU, as well as firmware that helps the machine performs to its peak ability. Omron has and will continue to create hardware, firmware and software to improve our controller’s performance. CPUs are getting faster and with multicore CPUs we can utilize each core to gain efficiencies for the controller. Separating out processing components and running them each on their own core helps with CPU efficiencies.
A: Safety has been growing in motion and we are now combining safe motion with the other safety components to create a machine with safety at it center. This helps to keep the machine efficient in producing while still being safe for the people working around the machine. A centralized safety controller that can talk to all safety devices, either through hardwire or over the safety networks that are available is a large part a clean solution.
Omron is always working to reduce waste, carbon footprint and other hazards. Omron is making changes around the manufacturing process by using the latest in high-efficiency lighting as minimizing water usage at our facilities. We invest in ways to reduce natural resources in our products and the packaging that we ship in. We try and reduce the number of components that are needed in our products. We are reducing finite and valuable resources such as gold in our products.
We are implementing end-of-life, as well as predictive-maintenance, sensing into products that we can. This reduces the probability that our products fail during production and helps eliminate loss of energy and material due to a shutdown where waste occurs during production.
We are offering products that allow for remote access so that they can be accessed by someone to help with troubleshooting, monitoring and programming. We are also implementing QR codes on products. This reduces the amount of paper needing to be printed out to the customer by providing them all of the relevant material for the customers machines in a digital format.
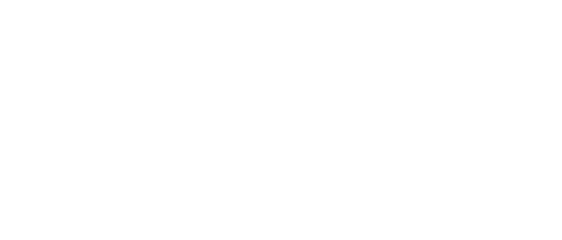
Leaders relevant to this article: