How fast and accurate automation equipment produces a precise Swiss watch
The Swiss watch industry protects the legendary reputation of its watches with the quality label, "Swiss Made." This level of quality can be achieved in terms of production technology only with fast and accurate automation equipment. This led Amax Automation in Burgdorf, Switzerland, to create a multifunctional palletizer, with robotic and handling systems such as the off-the-shelf EXPT delta robot from Festo. According to legislation by Swiss Parliament, the “Swiss Made” label means more than 60% of production costs must come from Switzerland.
Swiss quality
This is one of the reasons why the Swiss watch industry is carrying out more and more of the production steps for watches and watch parts in Switzerland. Another reason is that rising wage costs are making the suppliers in low-wage countries less attractive, not to mention the poor reproducibility of parts manufactured manually. There were also quality losses due to the precision-stamped parts being handled as bulk material. This led to more waste and higher cleaning costs.
By producing in its home market, the Swiss watch industry benefits from faster and shorter transport routes and simpler production control. The palletizers supplied by us at Amax ensure accurately sorted precision stampings for further processing, such as electroplating, painting, pad printing and assembly. The high-precision parts are different for each watch model and each brand, and they’re extremely thin, with a thickness in the range of tenths of a millimeter.
The palletizer is fed directly from a stamping press and a cleaning machine (Figure 1). It’s used to place the fragile parts in transport trays, either to go directly to downstream printing equipment or to further heat treatment operations. The equipment is replacing tasks currently done manually in Asia.
Figure 1: Extremely flexible: the multifunctional palletizer from Amax sets down up to eleven different small parts in six different lattice trays or two different JEDEC trays; other formats can be set up by the machine operator at any time via teach-in.
Source: AMAX Automation
Swiss accuracy
The multifunctional palletizer is very flexible and fast. With a throughput of 120 workpieces per minute, it places up to 11 different small parts in six different lattice trays or two different JEDEC trays (Figure 2). The machine is easily reconfigured for different parts by re-teaching points via the control panel and the software.
Figure 2: With a throughput of 120 workpieces per minute two delta robots EXPT fill the JEDEC trays.
Source: Festo
At the infeed of the machine, the parts are checked to determine whether they’re upside-down. If upside-down, they’re turned to lay face up on the belt before they’re picked by the robots.
Also read: Robots and machines become partners in motion
The subsequent steps in the assembly process require the workpieces to be placed accurately. Two integrated vision systems and a specially developed turning system ensure that only correctly oriented workpieces are set down. The system is designed to run 63 different part shapes, so significant vision system programming was required.
Difficult to pick and place
During the actual process of palletizing, the parts were placed on a single belt conveyor, run underneath the camera and then moved to the robots. The intelligent vision system SBO...-Q finds the position of the parts on the encoder-tracked conveyor belt and sends the position and angle data to the two EXPT delta robots. The delta robots use a custom vacuum gripper to pick up the parts from the conveyor belt and place them, depending on the needs of the application, in either a lattice tray or JEDEC tray (Figure 3).
Figure 3: The delta robots use a specially developed vacuum gripper to pick up the parts from the conveyor belt and set these down in either a lattice tray or JEDEC tray.
Source: Festo AG & Co. KG
The small, lightweight parts make this vision-guided robotic application more difficult. Even a slight draft of air can easily change the part's position on the belt. Additionally, the parts are so thin that it was difficult for the vacuum gripper to distinguish between a part and the belt. Reliable production required a handling system with highly precise and consistent motion sequences in order to not change part position on the belt and yet be able to grip them reliably. This is why using the right robot technology is of crucial importance.
The palletizer had many stations serviced by Profibus and fieldbus I/O. The machine included the following station assemblies:
- upside-down check and turnover
- main conveyor belt
- vision system with conveyor tracking
- dual pick-and-place robots
- destacker for plastic trays
- destacker for wire trays
- stacker for plastic trays
- stacker for wire trays
- tray handling for wire and plastic trays
- positioning unit for plastic trays
- positioning unit for wire trays
- grouping station for parts going into wire trays.
Robot with delta kinematics
It was clear that only a robot with delta kinematics could achieve the necessary flexibility and speed required to pick up the small parts in the working area. We have had our eyes on the Festo EXPT delta robot for a long time but didn't have a suitable project until this one (Figure 4). As we are familiar with Festo electric axes and have been using these for some time, we feel completely at home with the delta robot. Its kinematics are also based on linear axes. What finally led us to choose the delta robot was its optimum cost-benefit ratio and the fact that we have already been working together successfully with Festo Switzerland for many years.
Figure 4: Maximum precision is required when inserting the small and lightweight parts.
Source: Festo AG & Co. KG
Figure 5: The electric axis EGC-HD, famous for its rigidity and precision, moves a mechanical gripper horizontally. This lifts several workpieces at a time, swivels 90° and sets them down in a lattice tray.
Source: Festo AG & Co. KG
On the basis of its experience in pneumatic automation, Festo was asked to develop the vacuum gripper system. This required a great deal of know-how, since it is not easy to generate the right amount of vacuum at the right time for the gripping and ejector pulses. It was advantageous that Festo could provide both pneumatic and electric automation technology (Figure 5). We were able to use the gripper system and the robot to create a discrete development package. This also resulted in a reduction in the number of interfaces and the associated cost.
Fine-tuning in the Festo Application Centre
However, before the Festo Tripod could be put to work in the palletizer, a large number of validation tests were required. "We asked our colleagues in the Application Centre at company headquarters in Germany for support," says Daniel Minger, sales engineer, Industry Cluster Small Parts Handling and Electronics with Festo Switzerland. In order to achieve 120 cycles per minute, two delta robots would be necessary: the first one would pick up as many workpieces from the conveyor belt as possible, while the second one would pick up the rest. A Festo vision system with an integrated PLC would control both Tripod handling systems. This at least was the theory.
But in practice the situation was different: With complex applications, screen simulations are often not enough. In these cases, tests in the Festo Application Centre are needed. Under real conditions, and using workpieces supplied by the customer, the cycle times and repetition accuracy of handling systems are tested, with movements recorded using a Festo high-speed camera. Software and hardware can thus be precisely matched to each other.
Engineering know-how saves time
In the case of the Amax palletizer, the set-down accuracy in the trays was particularly critical. The laboratory conditions in the Application Centre were therefore ideal as a way of analyzing the set-down accuracy and the subsequent settling times of the delta robots, developing appropriate software algorithms and optimizing these in order to obtain the required cycle times.
The two EXPT delta robots were supplied by Festo as a complete ready-to-install system, including a CMXR robotic controller and a CMMP-AS motor controller in a suitable control cabinet. These were complemented by the intelligent compact vision system SBOI...-Q, which optically detects workpieces on the conveyor belt and signals position data to the robotic controller.
Complete ready-to-install system
Other ready-to-install handling systems were supplied for tray changing. ELGR electric axes push the trays forward, and pneumatic cylinders then lift and clamp them. An EGC-HD electric axis, famous for its rigidity and precision, positions a mechanical gripper horizontally. This gripper lifts several workpieces at a time, swivels 90° and sets them down in a lattice tray. Vertical movement is provided by an EGC electric axis.
Festo delivered the ready-to-install system solution, fully assembled and tested and with a functional guarantee, directly to the machine. We took advantage of the engineering know-how of the Festo automation specialists, which saved a great deal of time throughout the process, especially during testing and commissioning.
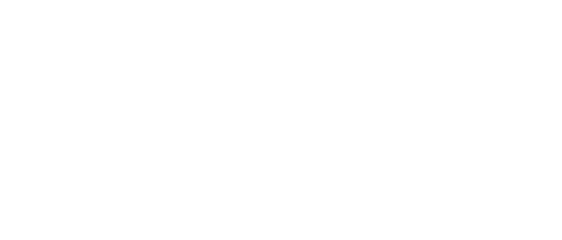
Leaders relevant to this article: