Digital technologies can help monitor employee health & safety
In the wake of the COVID-19 pandemic, employee health and safety has come to the forefront of many leaders’ minds. To help those leaders put thought into action, Amanda Del Buono interviews Kylene Zenk, director of manufacturing practice at Kronos, about how digital technologies can help manufacturers be more attentive to their employees’ overall well-being. Below is a portion of the interview. The full transcript is available here.
Read Kronos U.S. Workforce Activity Report: www.kronos.com/about-us/newsroom/update-us-workforce-activity
Learn about Kronos' employee contact tracing capability: https://www.kronos.com/about-us/newsroom/kronos-introduces-employee-contact-tracing-capability-support-covid-19-response
Transcript
Amanda: Now, how can digital transformation technologies help them to reach those opportunities and enable employee health and safety or what tools can help them?
Kylene: Ensuring a safe working environment is more important than ever. It also probably feels more daunting than ever. However, these rapid advances in workforce technologies can allow organizations to streamline certain aspects of reentry into the workforce or maintaining business continuity by automating or replacing manual processes and extending management's capabilities. Now is really the time for action versus planning. If we consider how modern workforce management processes and technologies can be leveraged today to solve some of these critical challenges with maintaining business continuity, there's a couple of examples that come to mind. One, when or if an employee tests positive or is presumed positive for COVID, it's vital to immediately begin the process of contact tracing in the workplace. Workforce data such as the time and attendance records that most employers are already collecting and have that rapid access to can be a critical aid in streamlining contact tracing in the workplace. With digital tools to analyze labor records, organizations can quickly and accurately identify who worked at the same time and the same location as an afflicted employee based on the time clock punches that they have, or other attendance data collected by their workforce management system.
This is essentially allowing companies to automate what would otherwise be a very manual and probably less accurate process. So, this approach can give employers the ability to immediately remove potential contacts from the schedule and give proper direction to help reduce risk of an outbreak at work. Kronos I'm proud to say has simplified the process of employee contact tracing for our customers. Forty thousand organizations globally now have access to a free automated reporting capability that HR and management teams can use to immediately identify potentially exposed employees if notified of a presumed or positive COVID diagnosis at one of their facilities. So, technology is playing a huge role in the contact tracing process. And then as I mentioned earlier, another way technology can support what companies are going through, as I mentioned earlier, employees' well-being can be enhanced at this time. So, we need to think about offering flexibility and support in managing that work-life balance and understanding people have increased family responsibilities.
So, with modern scheduling tools, which are accessible on mobile devices, your employees can have more control and input over their schedule that allows them to do something like easily swap a shift with a colleague. So, if you have a last-minute childcare situation arise and you need to stay home from work, you can be at home, check your phone to see who's available to take your shift. The technology makes sure that the set of employees that come up as options have the right skills and certification requirements. So the business ensures coverage to meet the demand and then the employee gets the flexibility they need to attend to their personal matter. So, when it comes to workforce scheduling, aligning the right employees to meet those demands is just one part of the equation.
Technology can also provide visibility into workforce availability and capacity, so manufacturers can easily assess the skills of its employees, which is a critical step in deploying labor resources especially now if those resources are constrained due to illness or furloughs or many other situations. As we think about how we're taking care of the people that are working day to day, we know that you can potentially get tired or experience burnout if you're working long shifts or many days in a row. The other benefit of technology is that it can make sure your employees are taking the appropriate breaks. So, getting alerts to remind them to take a meal break or just a intra-shift break. We can also deploy the technology to make sure you're giving people suitable rest between their scheduled shifts, how many hours between a shift, make sure they're not leaving the plant at midnight, and then coming in at 6:00 A.M. That's not enough rest for anyone. Leverage technology to help make sure you're deploying your resources in a safe and effective way as well.
Amanda: Awesome. Well, do you have any examples of where this technology has enabled a safe working environment, maybe from your own experiences or with your clients?
Kylene: Yes. Definitely. I've connected with several manufacturers over the past few weeks, and I've heard numerous examples of how they've quickly been able to adapt their operational and HR policies and processes in order to really support, deploy, and protect their workers and they're leveraging technology to do that. So, one of our food processing customers, their products were still highly in demand. They needed to maintain a 24/7 production schedule in order to keep up with that demand for its products. Their production facility and their production lines were not conducive to physical reconfiguration. So, it was challenging for them to think about how could they promote social distancing within their facilities. They actually leveraged their workforce scheduling technology in order to create new schedule and shift patterns, which would allow them to meet their production demands but also maintain social distancing. They were able to, with the help of technology, schedule employees into smaller groups to limit the number of co-workers that each individual employee is interacting with at any given time, you're always with the same group of people. So, if something were to happen who that employee had contact with.
Another example, I know several of our manufacturing clients have turned to mobile to facilitate critical interactions between employees and the organization. So, in order to prevent potentially sick or even folks that have been possibly exposed to illness from coming to work, we've got clients that are conducting health screening questionnaires in advance of the shift. So, employees leverage their own mobile devices from their home. They quickly respond to a few short yes or no surveys, which provides the employer with critical information about their health status and recent potential exposure so they can take the appropriate action and letting the employee know whether they should come to work or not. Another example of leveraging mobile technology is rather than use a time clock for capturing employee time and attendance information, employees are able to clock in and out leveraging their own personal phone. This benefits the employee because they don't have to touch a time clock that others have interacted with. It reduces the amount of sanitation that needs to happen. In addition with workforce management tools on their phones, employees can also access any time a variety of other important information such as their schedules and the ability to make time-off requests.
And for the employer, the employer doesn't have to worry about leveraging mobile clock in and clock out because there are geosensing capabilities within the software that'll make them confident that the employees clocking in from their facility so there's no concerns about data accuracy. And they can also feel good about the fact that they don't have lines or crowds around the time clock, which could lead to limitations in social distancing. These are just a couple of examples of how workforce management technology has reduced potential exposure and helped employers promote and facilities create social distancing and also help employees feel more trusted and supported by their employers.
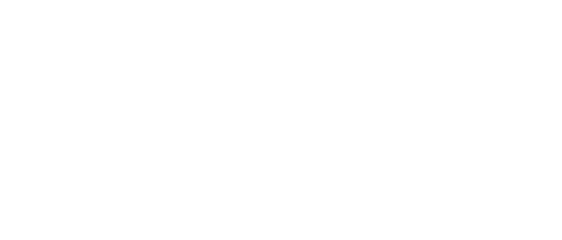
Leaders relevant to this article: