By Phil Burgert
Occupational safety requirements, increased demands for flexibility, diagnostics and Ethernet-based safety are driving use of safety relays and programmable safety controllers while providing machine builders with options.
The safety devices solve some problems for machine builders and users but also add complexity to the task of deciding what level of safety is required, according to machine builders and system integrators.
Safety Tricks
"Our bag of tricks in the safety field is expanding constantly," says Scott Bonnet, control engineer for Rockford Systems, a safety systems integrator in Rockford, Ill. "We use a significant number of safety relays since most of our business is single-machine applications and retrofits. If we are simply adding safety equipment to a machine, we typically use some type of safety relay in the interface (Figure 1)."
The number of machines involved in Rockford's projects often dictates whether relays or more sophisticated controllers are used. "As the complexity of machines and work cells advances, midsize and larger safety PLCs have become a must," says Bonnet. "Companies find the benefits of these PLCs if they have multiple zones, multiple devices and the need for integrated controls. The percentage of our business using PLCs is increasing steadily."
"Safety relays are a perfect fit to monitor a small number of safety guards or emergency stops," says Mick Garrick, lead product specialist at Phoenix Contact. "As the requirements and complexity of the safety system grows, so does the numbers of safety relays and/or safety relay expansion modules required to handle the safety control."
Some vendors, including Pilz Automation, define configurable safety relays as a safety device category for handling about five to 14 safety functions, while recommending programmable safety systems and controllers for applications with about 15 to more than 1,000 safety functions.
Safety relays and configurable safety relays are used for machine safety in at least 80% of installations by system integrators and machine builders, says Thomas Hoertig, regional sales manager for Pilz. "End users mostly expect the machine manufacturer or the system integrator to supply safety relays in the control system as part of the machine compliance to applicable industry standards," he states.
Banner Engineering terms this middle ground as safety modules, which Mike Carlson, safety products marketing manager, says can be used for four to a dozen safety functions and also have some level of configurability (Figure 2). "What they really bring to the table is the ability to interface the safeguarding solutions," he says of the increased options now available.
Keep It Simple
For most projects Maverick uses safety relays to control the press, says Iossi. "I'm not real big on programmable safety relays," he says. "With the protected logic controllers you're locking out any electrician from changing bits around and removing safeties. That's the function of it. With safety relays we have a defined standard that nobody can modify. I like that scenario better."
Dave Collins, product manager for safety products at Schneider Electric says many industrial OEMs and users want to upgrade their safety systems, but "most of them want to make sure they protect personnel without going overboard," he says. "A lot of machinery is built with a relatively small number of safety inputs, so sophisticated programmable systems would be more than what's needed and would add a level of complexity that is not needed."
However, a downside of safety relays can be the lack of diagnostics they provide, adds J.B. Titus, manager of business development and safety standards for Siemens Energy & Automation. "When the machine stops," says Titus, "you still have to go out and do some troubleshooting, find and repair the problem to restart the machine. Sometimes the diagnostics issue drives the decision."
Onward to Programmable Controllers
At some point, notes Garrick, the direct costs of components, installation time and the space needed motivate designers to look for a more cost-effective and scalable solution, and he says the next logical step is the safety controller (Figure 3). "Standard safety relay technology will be replaced with smaller, newer, solid-state safety," he says. "This solid-state safety is expandable on the safety output side and on the input side."
Safety in Safety PLCs
More customers are requesting safety PLCs to replace relay solutions, says Christine Frank, product marketing manager for Sick. "They ask for more programmable safety systems. Some end users require more decentralized control and others want it centralized," she says.
Frank says customers also are implementing more Ethernet-based safety networks and would like more safety devices that are directly connected to the safety network and have IP67-rated protection. This requires more system design support for safety systems, she says.
"Some users look at the complete architecture and use a single safety PLC to do both the general machine code control and the safety machine control all out of one safety PLC," says Titus. "Some other solutions require a conventional PLC and then a separate safety PLC and two separate buses, a conventional bus and a safety bus."
Many end users continue to use safety relays and even in some applications with a safety PLC in place, they might use safety relays on a machine, says Titus. Factors involved in this kind of combination include engineering, risk assessment and the choice of actuators, says Titus.
"If it's a simple machine that only has four to six safety points, it's probably more cost-effective to use safety relays, as opposed to putting a safety PLC on it," adds Titus. An exception would be during the design phase for the machine when consideration is already being given to a small PLC rather than safety relays. "The incremental cost to move to a small safety PLC really is quite small," he says.
"Every time you punch a button and go to another floor, we're testing that system," says Mark Burnett, control systems manager and automation engineer for the Austin, Texas,-based company. "If the system isn't operating inside the correct parameters, it will let you know or it will shut it all down. The safety system will deactivate it."
Burnett says Tower also uses a safety PLC to monitor and arm or rearm a flip-flop with a group of relays to provide "a fine degree of control and know that the circuit is operating and protecting the people it's supposed to," even when they are having a problem with a hydraulic rescue lowering system, he says.
Changes to NFPA Opened the Door
Titus notes that safety automation is experiencing a much higher year-over-year growth than other types of automation. "It's still in early adoption, but it grows at a much faster pace than the family of products that it's a part of," he says. Programmable logic controllers weren't considered sufficiently reliable for safety requirements when they were first introduced in factories in the 1970s, and standards for industry were written to exclude PLCs from any role in safety, explains Titus.
"That all changed in 2002 when NFPA 79 was republished and allowed safety PLC technology to do safety control," he says, noting other standard modifications facilitating safety automation have since been added. "By then safety PLCs had gone through several design changes and the reliability of PLC technology had achieved high marks," he says.
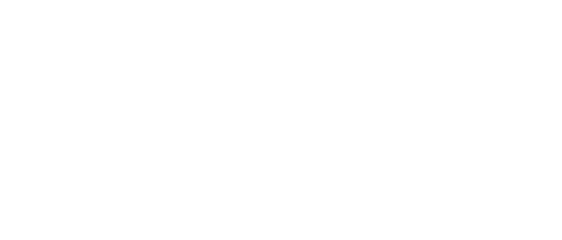
Leaders relevant to this article: