Cooperativa La Cruz Azul, the third-largest cement manufacturer in Mexico, required an entire packaging line for the flexible and fully automated filling, palletizing and packaging of different types of a new tile mortar (Figure 1). The Beumer Group solution won out over the competition, providing everything from one single source. This included the Beumer fillpac R filling system that was adapted for filling different materials (Figure 2). It also included the Beumer bag placer to ensure a more efficient filling of the high-quality materials. With this new packaging line, Cruz Azul can achieve its projected production capacity.
Figure 1: Cruz Azul required an entire line to flexibly bag, palletize and package the different types of tile mortar.
(Source: Beumer Group)
Gigantic bridges, high-rises, tunnels for roads, subways and sewage systems: some of the biggest construction projects in Latin America are currently being built in Mexico. This makes the country the second-largest cement market on the continent, right after Brazil. To hold its own against national and international competition, Mexican manufacturers are developing more high-end materials. The production at Cooperativa La Cruz Azul, founded in 1881 and headquartered in Mexico City, is aimed exclusively toward the domestic market.
Photo: 18-04-25_BEUMER_CaseStudy_Cruz Azul_02
Figure 2: Beumer Group supplies everything from one single source. This includes the fillpac filling system. It can be adjusted to the changing parameters of the different materials.
(Source: Beumer Group)
The manufacturer operates four plants with a yearly production of around 8 million tons of Portland cement, which is only one of its end products. The main plant is in Jasso in the state of Hidalgo (Figure 3). The city is located in a region that is very rich in limestone. As if the cement plant’s manufacturing production isn’t successful enough, a soccer club founded by the plant’s employees in 1927 plays in the top level of the Mexican soccer league, with national and international success.
Figure 3: One of the sites of the Cooperative La Cruz Azul is in Hidalgo, Mexico. Some of the newest products of the cement manufacturer are eight different types of a new tile mortar.
(Source: Beumer Group)
Reliability and quality
Success plays an important role for Cruz Azul. Its cement production represents 22% of the national market. With the goal to further increase this share, the cooperative developed high-quality tile mortar in eight different variations as one of its new products. "The quality of the building materials is decisive in order to remain competitive," explains Victor Luna, managing director at Cruz Azul’s Hidalgo facility. Distributors and end customers also want the products to arrive by the required date and quantity. A small amount of the mortar is sold in big bags, the majority however is sold in 20-kg and 25-kg bags. This is why the manufacturer needed an entire packaging line that could meet very specific requirements.
Due to varying material densities, and as a consequence different flow properties of the different variants of the new product line, the filling system had to be adjustable to the different materials, as well as to smaller bag sizes without extensive retrofitting of the machine through the employees. The line should then palletize precise and stable bags, stack and package them to protect the content against transport damage and atmospheric influences.
The right partner
In March 2015, after an offer from another supplier had already gone in and the project was already at an advanced stage, employees from Cruz Azul who were responsible for the project reached out to Beumer Group for an offer. "We have been working closely together for the past 30 years," says Luna. "We have a long-standing relationship and trust in the Beumer brand."
This trustful relationship is not surprising because Beumer Group’s history with Cruz Azul goes back 10 years to 2008. In an extensive order for a plant in the state of Puebla, Beumer Group provided and installed five bucket elevators and two palletizing and packaging lines in only 26 months.
They consist of Beumer paletpac palletizers and the Beumer stretch hood high-capacity packaging systems. As with the current project, one of the requirements for this line was to palletize and package various bagged materials, without extensive retrofitting of the machines. Luna emphasizes that Beumer Group provided Cruz Azul with an adaptable technology with which his colleagues are working efficiently to this day.
The Beumer Group is a manufacturer of intralogistics systems for conveying, loading, palletizing, packaging, sortation and distribution. With 4,200 employees worldwide, the Beumer Group has annual sales of about $900 million. The Beumer Group serves industries such as bulk materials and piece goods, food/non-food, construction, mail order, post and airport baggage handling.
Intralogistics
The intralogistics specialist has introduced the newly developed human-machine-interface (HMI) operator panel with an optimized user interface and graphical navigation for operating the system. It offers an even more ergonomic workflow to the user. This intuitive-interaction concept helps to define efficient working sequences. The soft-touch panel uses pictograms to guide the user through the machine control menus. The panel also gives the operator access to all required training programs and content. The systems are controlled by a Siemens Simatic S7-300.
Additionally, we developed the modular BG software suite, which is a data-processing system offering users optimal and continuous control of material flows. It can be customized to the user's requirements. Products from other companies can be integrated. Users can extend this modular solution at any time. Process data or reports are displayed on the BG Fusion user interface that works for all programs. Users can access all available data without having to switch between applications. They can also use the BG software suite on mobile devices, such as tablets.
The Beumer Group Warehouse Control System (BG WCS) module allows users to connect the BG software suite to the warehouse management system or the enterprise resource planning (ERP) system via a network connection. As a single-source provider, we can create an intelligent connection between the individual systems and integrate them into existing process and inventory control systems, while ensuring the communication between the different control levels for the user.. The customer receives everything from one single source. The risk for error sources that could result from interfaces is avoided.
Technicians carry out the electrical installations, as well as the integration of the machine and system controls. We also offer support during commissioning.
Filling technology made in Germany
Beumer Group presented the fillpac R filling system to Cruz Azul. "Changing the required parameters is simple and quick, and the different material is filled efficiently into two- to four-ply paper valve bags," explains Ralph Buchholz, director general at Beumer de México. Both companies quickly agreed on the scope and scheduling for the entire packaging line and signed the contract in April 2015.
"Cruz Azul attaches the greatest value to the quality seal, 'Made in Germany,’" explains Buchholz. "Those responsible for the project even travelled to our headquarters in Beckum, Germany, to accept the systems in person."
In October 2015, the Beumer Group provided the systems. Three Beumer employees from Germany and one from Mexico were in charge of installing the system. "We had to integrate the line into the existing building structure and bulk storage technology," reports Buchholz. "My colleagues mastered this challenge because our solutions can be easily adapted to technical and structural conditions." In this case, the engineers had to rework the suspension for the Beumer fillpac.
Precise degrees of filling
The Beumer fillpac R operates with eight rotating filling spouts, according to the impeller filling principle. This way it can safely handle even fine-grained tile mortar. The rotating filling impeller is characterized by its speed and maximum material throughput.
"The bags are weighed during the filling process," explains Buchholz. The Beumer fillpac is equipped with an electronic calibration-capable weighing unit. It ensures that the bags are always filled with the same amount of material. A special software enables filling spouts and scale to constantly compare the weight. If the determined weight is incorrect, the bags are automatically removed, discharged on a chute and opened. The collected material is fed back into the process via a spillage screw conveyor and a bucket elevator.
Figure 4: The fillpac R is equipped with a ream magazine for 700 bags.
(Source: Beumer Group)
The system has a modular structure. A ream magazine for 700 bags was also added (Figure 4). This allows Cruz Azul to further increase the efficiency of the filling system. "We equipped the system with the new Beumer bag placer because the material is so fine and volatile," says Buchholz (Figure 5).
Figure 5: The bag placer allows Cruz Azul to further increase the efficiency of the filling system.
(Source: Beumer Group)
Servo motors drive the application unit and the suction gripper automatically, precisely and energy-efficiently. All servo motors and geared motors within the complete packaging line are from SEW-Eurodrive. “SEW-Eurodrive is our standard because of its well-proven techniques, its leading market position and our long-term partnership with SEW,” says Buchholz.
The gripping system and the application unit apply the bag from the stack safely onto the filling spout. The system can pack 1,800 25-kg bags or 2,250 20-kg bags per hour with the highest precision. "The operator can also adjust the Beumer bag placer to other bag formats," explains Buchholz.
For the subsequent fully automatic, reliable and most of all fast palletizing, Beumer Group installed a Beumer paletpac layer palletizer. Per hour, it gently and reliably stacks 2,200 bags per hour in 10-bag patterns or in eight-bag patterns on pallets of 1,220 mm by 1,020 mm by 245 mm in size (Figure 6).
Figure 6: The paletpac layer palletizer can stack the bags in a 8- or 10-bag pattern onto pallets of 1,220 mm by 1,020 mm by 245 mm in size.
(Source: Beumer Group)
"A twin-belt turning device brings the bags in the required, dimensionally stable position," explains Buchholz (Figure 7). The position accuracy of this device offers a great advantage compared to conventional turning machines, because the system's components move the bags without mechanically deforming them. Two parallel driven belt conveyors move at different speeds and turn the bags quickly into the desired position. The intelligent control of the twin-belt turning device also takes the dimension and weight of the filled bag into consideration. Exact positioning, specified by the preset packing pattern, is achieved. "No adjustment is necessary, even with a product change," says Buchholz.
Figure 7: The twin-belt turning device accurately positions the bags quickly and gently.
(Source: Beumer Group)
Packed fast and safely
The finished bag stacks are transported over roller conveyors to the Beumer stretch hood packaging system. It packages 110 pallet stacks per hour with stretch film hoods with film thickness ranging from 40 to 100 micrometers. "It depends on the type of tile mortar," Buchholz explains. "The packaging protects the product against dust and humidity during storage and on long transport routes and ensures that the bags remain stable on the pallet without moving." To facilitate the work for the maintenance personnel and to ensure high system availability, the packaging system no longer needs a platform. Maintenance work, such as changing the blades or the sealing bars, is handled at floor level. Additional benefits include the compact design and the resulting low height and small footprint.
Figure 8: The stretch hood packages the bag stacks with a stretch film hood. This protects the product against damage during transportation and atmospheric influences.
(Source: Beumer Group)
"The Beumer stretch hood is extremely energy efficient," emphasizes Buchholz (Figure 8). A film transport system, which is particularly gentle on the material, introduces the previously cut and sealed film hood into the system. The sealing seam already cools down on the way to the crimping and stretching unit. Crimping can start without any delay. This allows for the elimination of energy-consuming cooling units and efficiency-reducing cooling times. This way the pallets can be packaged at high bag sequencing.
Figure 9: Once the line was put into operation, palletized and packaged products could be picked up with a forklift and delivered to outgoing goods.
(Source: Beumer Group)
In June 2016, Cruz Azul put the line into operation (Figure 9). "The new Beumer packaging line brought the project to success," mentions Luna. This means the cement manufacturer can reach its projected production capacity (Figure 10). In order to ensure a trouble-free operation, the system supplier's competent specialists stay in close touch with the customer and help out immediately in case of malfunctions or downtimes. Beumer Group also provided the necessary spare parts, ensuring high availability of the systems at all times.
Figure 10: The packaging line operates around the clock, which means the cement manufacturer can reach its projected production capacity.
(Source: Beumer Group)
The new packaging line is tailor-made for Cruz Azul’s needs, which makes Luna happy, especially with the flexible filling technology. It saves a lot of time and brings peace of mind. Plus, the different types of mortar are getting to the customer faster. With this project, Beumer Group has installed the first Beumer fillpac R in the American market. The cooperation with the system supplier will continue. Discussions are currently held regarding new projects in the fields of conveying and loading and palletizing technology.
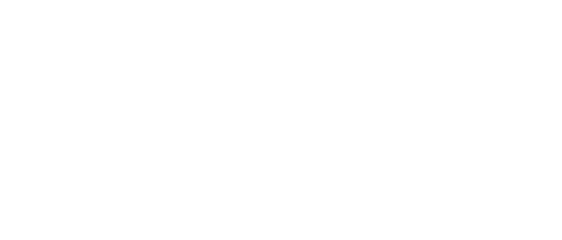
Leaders relevant to this article: