THOMAS EDISON was correct as usual when he said genius is 1% inspiration and 99% perspiration. But without that 1%, you might as well be flipping burgers or X-raying bags at the airport. If it’s such a crucial catalyst, however, where does inspiration come from, and where can we get more?
Necessity is invention’s traditional mom, but fatigue is no doubt its dad. “A need or problem encourages creative efforts to meet the need or solve it,” states the dialogue in Plato’s Republic. After yet another long day’s labor, every wage slave eventually says “there’s got to be a better way,” though only a few actually seek it.
The fact is that good ideas can come from anywhere. In machine building and other endeavors, innovations logically grow from the experience of builders, integrators, and end users. They also come from repeatedly talking to customers, genuinely listening to what they have to say, and taking the too-rare step of acting on it.
Innovations also come from technical professionals exploring areas they don’t usually work in, such as an IT person getting onto the plant floor, or vice versa, and occasionally blurting out an idea that everyone will soon say was obvious all along.
Sometimes ideas just click in, seeming to appear from nowhere like that proverbial bolt from the blue. You might be looking at a component or device you’ve used for years, when suddenly you see something about it you hadn’t before. It’s as if a mythological muse whispers a new way to use it, or as if an occult hand points to a new solution. Other times, ideas are the culmination of a long process of preparing and waiting for technical, economic, or other conditions to allow a long-sought goal to become possible.
Whatever the spark, it burns brightly in the mind, and waits for all that well-known sweat to make it a reality. And whether you’re inventing the lever, Archimedes’ screw, chronometer, steam engine, lightbulb, semiconductor, nanotube-based circuit, or whatever comes after, that reality will be different and hopefully better as a result. Sure, agriculture’s hard, but it beats hunting and gathering. Certainly, my PC and the Internet might crash, but it’s better than buying typewriter ribbons and looking up Plato’s quotes at the library. In short, innovations large and small create organizational change, unlike offering the same old PLC in tropical colors!
These are some of the attributes shared by the three winners of CONTROL DESIGN’s First Annual Innovator Awards. These companies and their machines represent significant departures from how their processes were done before, and their end users bear witnesses to how these innovations improve their applications.
So, check out their stories because, while nothing succeeds like success and you need money to make money, present innovations can fuel future inspiration. That’s good news because we’re going to need more nominees and winners next year.
Sabel Engineering’s TL-10 robotic, top-load, case packer uses three conveyors to index bags of Mamacita’s empanada dough, simultaneously build cases, and pack 90 bags/min. with less errors, wiring, and repetitive motion.
Packer Treats
Dough with Care
SPEED AND gentleness don’t often go together willingly, especially in case-packing applications. Employees at Mamacita Inc. in Vineland, N.J., had used Sabel Engineering Corp.’s all-in-one case erecting, loading, and sealing machines to run plastic tubs of salsa, and recently wanted to use the same or similar equipment to pack 15 and 21 oz. bags of empanada dough in 24-bag cases. However, these 6-in. stacks of basically fluffy tortillas or pancakes were far more delicate, and would need a much lighter touch than the tubs, especially at Mamacita’s desired 90 bags per minute.
“We’d worked with Sabel before, and were very happy with their previous generation loader, but the new product couldn’t run on the usual technology,” says Jon Mangel, Mamacita’s vice president. “The dough needed to be handled carefully, but at high speed.” Coincidentally, Sonoma, Calif.-based Sabel was already working on a packer with a servo-driven positioning base and a robotic, vacuum pickhead, according to Noel Barbulesco, general manager, and Hitan Patel, controls and R&D manager.
Because the most critical task for such a machine’s process is precisely staging the bags for loading, Sabel’s TL-10 9 x 8 ft footprint, robotic, top-load, case packer uses three conveyors driven by B&R Industrial Automation Corp.’s Acopos servo drives. Pacmation Inc., a B&R distributor, helped implement and program TL-10 and its drives.
The first conveyor is a random-feed, in-feed conveyor that transports the bags toward the loading station, and guarantees adequate spacing between individual items. The second is a positioning conveyor that indexes the 5-in. and 6-in. diameter bags forward, and forms groups of four in a predetermined pattern. The third is the loading position conveyor, which quickly advances the group to the pick station, where the bags of dough are loaded into cases or bags with Fanuc Robotics’ six-axis M-6iB arm.
Though the three conveyors perform different tasks throughout this process, they’re synchronized with each other at all times. TL-10 uses Ethernet Powerlink communication protocol to broadcast positioning information from one servo drive to the other via standard Ethernet cables. Less than 400 µs cycletimes allow fast updates of information between the drives, and eliminate the need for added encoder wiring between the drives. This simplifies and reduces troubleshooting, which also can now be done via the Internet.
In addition, Sabel decided to use an independent valve manifold connection to simplify connecting pneumatics to TL-10. This function used to require multiple large cable harnesses, but it now needs only one cable to connect all points via a remote backplane. The machine’s two control cabinets, one for controlling the robot arm and one for the rest of the controls, also are connected by one cable. TL-10 further reduces wiring and terminal blocks by connecting its sensors directly into a slice I/O system, which saves space and reduces costs.
The machine’s HMI is integrated with the I/O and a 10-in. touchscreen that serves as the main control unit. It displays drive positions, speeds, error messages and other data, which makes it easy for operators to make setting changes, and inform the OEM of standardized error messages for easy troubleshooting over the phone.
“Ethernet and the integrated controller allows us to do HMI, motion, control logic, and communications all in one device,” says Barbulesco. “This helps because, as an OEM, we don’t have to marry so many types of equipment, and make sure they work in sync. It also saves time and labor for the end user.”
The machine’s second critical process is presenting erected cases at the loading station. “There are other top-loading machines, but they don’t have good case-erecting and transport systems,” adds Barbulesco.
TL-10 uses a servo-driven, walking-beam mechanism to present the cases properly at the bag-loading station. Acopos servo drives were combined with Bosch’s actuators to provide smooth, accurate positioning of the cases for loading. Flat cases are dispensed from a magazine, erected, and, after sequentially folding the bottom flaps, moved into loading position. Once a case is loaded, it’s discharged, and moves to the tape-sealer station.
“TL-10 allows us to operate a lot more efficiently, prevents errors, and eliminates a lot of repetitive motion tasks for our employees,” says Mangel. “The staff was apprehensive because this was our facility’s first robot. However, when they saw that it’s designed to work with them and not replace them, they even nicknamed it ‘Little Mickey’ after our line supervisor.”
Mangel adds that TL-10 also is very adaptable, and can handle any product line changes quickly. “In the past, our configuration was set, but now we can change over to other product parameters easily. TL-10’s controls, Ethernet, and servo capabilities really take previous PLC-type functions to a different level.”
As a result, other applications, such as dairy and bakery, that hadn’t been able to use robots in the past, may be able to use TL-10 for packing. “Integrating the three conveyor modules for food processing enables users to easily change between a lot of different products,” says Patel. “The robot and interface allows packing parameters to be changed onscreen in five minutes or less, instead of the 20 minutes it would take on older machines that need to switch out much more equipment. In fact, this easy changeover means TL-10 can be moved to an entirely different application or plant, and only have to make programming changes and 10% fewer mechanical changes.”
MarquipWardUnited reports that PC-based controls via Lightbus increased its sheeter’s production speed from 1,100 ft/min to 1,500 ft/min. Marquip also replaced its metal knife cylinder with a carbon-fiber cylinder, which had reduced vibration, enabled faster speeds, and increased knife life.
PC Controls Keep Pace
With Knife Sheeter
INNOVATION requires a lot of patience sometimes, but constant communication between machine builders and end users can help them be ready when technology catches up, and makes their ideas possible.
John Jahn, project management director at MarquipWardUnited in Madison, Wis., says his company’s sheeting systems used PLCs for many years, but were frustrated that a system with a dozen machines would need a PLC for each device. However, while PC-based controls could manage an entire line, they were initially seen as too costly and unreliable for Marquip’s sheeters. For awhile, the firm even used a high-speed control hardware module that it built itself, but recent events have made it unnecessary.
“Industrial-standard PC motherboards declined in cost and increased in reliability in recent years,” says Jahn. “This allowed us to make the leap, and move our critical processes to using this technology.”
Mark Schuppel, engineering manager at end user ECM Converting Co. in Mendon, Mich., says previous sheeters were limited by their four-line LCD displays, which required constant paging to view data and enter orders. “The older sheeters also had limited diagnostic capabilities. So, they could indicate they weren’t ready to run, but they weren’t much help beyond that.”
Marquip’s dual rotary knife sheeter is used to cut and stack converting materials, such a paper, plastic, and foil. The sheeter includes brushless, high-torque, knife-cylinder motors combined with low-inertia knife cylinders to reach high cutting speeds. It can cut short sheets as small as 20 in. long.
Besides providing a more open system requested by many customers, moving to PC-based controls also simplified the sheeter’s architecture, as well as reducing system components, installation costs, and engineering effort. The new controls for the dual rotary knife sheeter include Beckhoff’s C6240 industrial computer running its TwinCAT software, 15-in. operator interface panels, and Lightbus’ I/O with its PCI card inside the PC. Lightbus helps maintain the dual rotary knife sheeter's extremely high speed, handling Marquip’s millisecond signal transmission requirements.
“TwinCat is almost 100 times faster than our previous PLCs. For example, our former machine’s modulation was seven times per second, but the PLC couldn’t keep up and control it, so we had to use a different, dedicated, high-speed process,” says Jahn. “We evaluated 11 PC-based systems, but TwinCat really made us believe PC-based control could be reliable because it operates in a protected mode, running beneath Windows, and makes sure the sheeter’s controller get the CPU time it needs. So, if Windows crashed, the software’s algorithms would keep the sheeter application running. And, as long as PCs can run Windows, our control software will be able to run on whatever it evolves into.”
Marquip reports that PC-based controls via Lightbus increased its sheeter’s production speed from 1,100 ft/min to 1,500 ft/min. Marquip also replaced its metal knife cylinder with a carbon-fiber cylinder, which had reduced vibration, enabled faster speeds, and increased knife life. Also, average installation time for the sheeters was reduced by more than 30%, even though every end user usually needs some customization for its applications. PC-based controls also are saving user approximately 60% on spare parts.
Jahn adds that PC-based control also benefits users in three other areas: an improved interface for data display and training, an 80% decrease in spending on spare I/O modules that the PLCs used to require, and less dependence on proprietary hardware. “The new sheeter also has a wonderful, one-screen representation of what’s going on, including sheet size, quantity, where we’re at in an order, and how fast we can run compared to how fast we’re actually running. This system allows us to easily integrate order entry, which come from customer service, through our corporate PC server, and are loaded directly into the sheeter’s HMI via BlueQ software.
Schuppel confirms that adds that ECM’s new sheeter has increased his company’s production by 20% because it has a higher speed curve on cutting 19 to 88 in. sheets. Also, better tracking and control have allowed ECM to increase line speed during skid discharges from 50 ft/min to 226-308 ft/min. The sheeter also increased its material width from 72 to 87 in., and is more flexible, according to Schuppel.
“Many vendors used to stock paper on their floors, and customer would pick the closest size to what they wanted. We’re now telling customers to let us know what size they want, and we’ll deliver it in two days,” says Schuppel. “Service is now the name of the game, and Marquip’s equipment and support is what allows us to do it. We meet weekly, and it seems like every other month we’re jointly working on some new improvement, such as the zone-controlled decurler they helped us develop. It varies tension on specific parts of the web to prevent curling of heavier products, and we’re using it every day now.”
AMA’s Delta-based controls combine and automate seven Flow Drill steps, which allow Tubular Products to reduce cycle times by 75-80% from 5-6 minutes to 45 seconds for the 35-40 holes it drills to make its electric vehicle frames.
Hole Control Drills
Down Cycle Time
IT NEVER hurts to ask what’s possible, especially when you can get two innovations at once. So, while drilling holes at 2,200 rpm, slightly melting the surrounding metal, and tapping in bolts that don’t need back nuts is good. Combining several machines and automating this entire process is better.
That’s what engineers at Tubular Products Co. in Birmingham, Ala., thought when they ran across Flow Drill’s technology on the web and at a tradeshow. Craig Armstrong, Tubular’s engineering manager, says his company knew Flow Drill could help it build frames for electric vehicles, such as golf carts, but Tubular also wanted to consolidate several steps in its framing process. As a result, Tubular enlisted Advanced Machine Automation (AMA) to design and build its combined machine. AMA is a system integrator and turnkey design/build company.
Tubular previously used seven separate machines to drill 35-40 holes in the eight pieces of tubing it needs to build its frames. “It used to take five or six separate processes to drill the holes in our frames, but our automated Flow Drill puts all of them into one machine,” says Craig Armstrong, Tubular’s engineering manager. “This dramatically reduced our cycle time by 75-80% from 5-6 minutes per frame to 45 seconds. This means we get all the business because we can pass these savings on to our customers.”
To understand how these huge improvements were achieved, it helps to know how Flow Drill works and how AMA automated it. Flow Drill traditionally is used on standalone, manually operated machinery to drill .021 in. to 2.500 in. diameter holes, in which thin-walled steel, aluminum, or copper tubing is tapped to provide 120% stronger pull-test mountings without backing nuts. Flow Drill’s carbide bits turn the material into a glowing, plastic state, and then 300 lbs of pressure is used to push it into the tube, creating a tappable hole three times longer than the material’s thickness. Most former automated Flow Drill operations had been accomplished with ball screws, servomotors, and drives.
“However, we found that hydraulics hold position more rigidly than ball screws, which can wear and loose their rigidity. Previous electronic and servo technologies wouldn’t hold position either, so we had to use clamps, or build some equipment with bigger, more expensive CNCs,” says Keith DeMonia, AMA’s general and engineering manager. “Hydraulic controls also allow operators to type in value changes, and put in offsets to change position without requiring an act of Congress.”
Because faster drilling requires more immobility, AMA automates Flow Drill’s usual operations by using hydraulic cylinders with Temposonic’s linear transducers for position feedback, which is fed to Delta Computer’s RMC75-D08 controller. This controller also operates an Atos proportional valve to position the part or sometimes the spindle unit to ± 0.001 in., and hold position during operation, while a Suhner spindle unit running at 2,200 rpm does the actual drilling. The part then moves to a tapping position where Suhner’s automatic tapping head is used. AMA reports its hydraulic solution is about three-quarters as costly as previous methods, and its ± 0.001 in. location offers an acceptable positioning tolerance, even after adding the cost of the hydraulic unit.
“Now, instead of shipping frame with holes, we’re producing completed parts,” says DeMonia. “So, instead of requiring customers to put these frames in a jig and put in RIV nuts, they can send these frames straight to assembly, and use their own self-tapping screws. This saves an entire production step.”
AMA reports the key to its operation is to tune the controller properly, so there will be absolutely no oscillation or vibration during the cycle. This would instantly shatter Flow Drill’s bit. Used properly, one Flow Drill used on an AMA automated machine will typically produce 8,000-10,000 holes before having to be replaced.
“The reason we need a motion controller is because proportional valves must be constantly readjusted. This is because the part being drilled has forces acting on it, such as the bit touching it and trying to move it, and so the valve has to react quickly enough, and move to apply more pressure or fluid,” says DeMonia. “A typical PLC is too slow to do this because it has to do a program scan, scan for the control, and then say ‘do your stuff’ to the controller. Our Delta motion controller operates more autonomously, and basically says to the system ‘we’re there and in position’ in 0.01 sec. Because it just controls position and doesn’t need a program scan, the controller’s scan time is a lot faster than a PLC.”
Because good ideas lead to even newer ones, DeMonia adds AMA’s automated Flow Drill is already being used to prevent leaks by providing better joints in HVAC unit frames. In addition, AMA just installed this same Delta, Atos, and Tempsonic combination to reducing the time it takes to cut and chamfer hot water heater cores from 5.7 sec to 3.7 sec.
STUDY METHODOLOGY |
To find the winners of this First Annual Innovator Awards, CONTROL DESIGN solicited nominations from its readers, including machine builders, system integrators, and automation suppliers. Respondents completed several essay questions, describing in detail the machines they were nominating. They related their machines’ functions, operating parameters, beta testing, end-user installations, notable use of automation and controls, uniqueness compared to its competition, impact on throughput, quality, flexibility, reliability and operator safety, and impact on the builder’s market position. CONTROL DESIGN’s editors then reviewed and nominations, conducted follow-up interviews with nominees and end-users, and selected the winners.
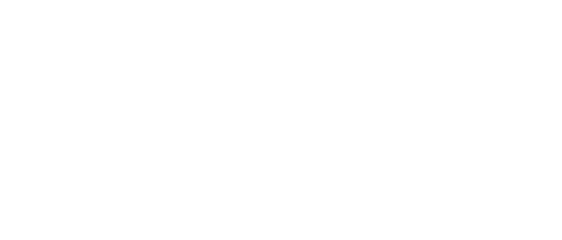
Leaders relevant to this article: