We've seen for some time now that industrial machine builders must create machines that produce more in less time. This increase in automation often speeds up the pace of work and at times can make work more hazardous to operators.
On the other hand, there still are many jobs done manually, involving heavy physical strain. One of the results of manual work, as well as the increase in automation, is that more workers are suffering from various physical issues. As a consequence, the notion of ergonomics comes in to play more in thoughtful machine design.
If you Google ergonomics, basically we find that it's the study of work in relation to the environment in which it's performed by those who perform it. Ergonomic correctness attempts to determine how the workplace can be designed and adapted to the worker to prevent a variety of health problems and still increase efficiency. So, to comply with today's ergonomic sensibilities, machine builders must find a way to make the machine operation fit the worker, instead of forcing the worker to conform to the machine.
Ergonomic design issues that machine builders must confront include:
- Operator interface height
- Operator control access
- Safety considerations (safety mats, light curtains, emergency stop operator access, etc.)
- Visibility
- Maintainability
All of this has to be included and still not jeopardize machine performance or output quality-challenging requirements in a highly competitive global market. You'll see that the line between what we call operator safety and what we call ergonomics often is a blurry one.
Ergonomically Designed Machines
A machine builder touting ergonomic design is injection molding machine builder Cincinnati Milacron in Lebanon, Ohio. Milacron's new Mosaic control for injection molding machines consists of a 15-in. TFT touchscreen display with keyboard mounted on a swing arm (See Figure 1 below). The package is sealed to IP65, and includes user-friendly software for five-stage extrusion profiling including graphic setup, a 10-stage injection profile, and 10-stage pack and hold with real-time graphical updates.
The operator display for a Cincinnati Milacron injection molding machines consists of a 15-in. TFT touchscreen with keyboard mounted on a swing arm. Milacron says it handled setup ergonomic issues with screens for data, operator buttons for machine movements, and user-friendly wizards.
Claiming it to be a setup person's dream, Milacron says it handled setup ergonomics with screens for data, operator buttons for machine movements and user-friendly wizards. The setup screens complement the ease-of-use with programming wizards based on input from injection setup specialists around the world, making the controls almost human-proof, claims Mike Litten, manager of controls development at Milacron.
Meanwhile, Minster Machine Co. in Minster, Ohio, manufactures machines, integrated systems and services for the material-forming industry. Minster's products include mechanical presses ranging from 16-ton, open-back stationary presses to 1,650 ton progressive-die, straight-side presses.
The company designs its own control system using A-B PLCs for equipment monitoring and relay-based controls for the presses critical clutch operation, where redundant and monitored schemes are employed. Russ Bensman, staff engineer at Minster, emphasizes that within the ANSI B11 series of Machine Tool standards, Minster references ANSI B11-Technical Report TR1 Ergonomic Guidelines for the Design Installation and Use of Machine Tools in the design of their press and equipment controls.
"The main control panel and pendant stations attached on the press and accessory equipment are located (See Figure 2 below) such that there still is high visibility to the work area, and they're easy-to-use and relatively consistent from machine-to machine, stresses Bensman. The ANSI guideline is available from the Association for Manufacturing Technology (AMT).
A machine builder similar to Minster is Pacific Press Technologies, Mt. Carmel, Ill. It has a history with hydraulic press technology for the metal-fabrication industry, including press brakes, plate shears, and hydraulic presses. Ergonomic considerations fit directly into every Pacific Press machine control design, while still assuring machine safety because many of the machines operate on individual cycles.
A good example of a completely safe, ergonomically-correct solution is a press cell Pacific supplied to Homac Manufacturing, Ormond Beach, Fla., a producer of electrical transmission connectors for utilities and contractors. To stay competitive, Homac realized its presses were too inefficient and hard to use and maintain. Improved efficiency without sacrificing operator safety and health entered into the analysis.
Pacific Press offered a mix of C-frame presses equipped with advanced CNC controls. Now our advanced CNC technology offers safe and simplified operation with high precision, says Gordon Baker, Pacific's sales and marketing vice president.
Each cell contains two CNC presses handled by one operator. Press placement in the cell is optimized to let a single operator monitor and control the operation. This reduces part costs and improves safety because the press CNCs are interlocked, providing an efficient, ergonomically stable environment for the operator. If an operator places two slugs in a die by mistake and something breaks, it grenades out of the die, says Mark McGrane, Homac president. Somebody could get hurt from the flying metal. The CNC controls are programmed in an interlocking fashion to avoid problems like this.
If a press senses too much pressure when closing compared to a programmed value, the CNC controls automatically stop the press and trigger an alarm. The controls are designed to keep all press parameters in a safe zone, which allows lesser-skilled operators to do setup and production.
Of equal importance are press Start and Stop buttons. In a two-machine cell, these buttons must be located such that they're always within reach of the operator, but still within distance guidelines established by the several standards mentioned earlier in this article.
Does Ergonomics Conflict With Machine Safety?
In 2003, the National Safety Council (NCS) published the Power Press Safety Manual, fifth edition, and the seventh edition of Safeguarding Concepts Illustrated. Most experts would say the content offers a plethora of how-to on operator safety, but they don't do much to raise the conversation level about ergonomics in the design of machine safety.
OSHA provides many publications on ergonomics in the general machine environment. Much of that information is included in the 1999 Ergonomics Standard, which was rescinded in 2000. Today, OSHA has no regulation addressing ergonomics in machine safety.
Perhaps the best way to understand human factors when designing machines is to integrate all the concepts currently published. To summarize, the four key principles, according to NSC, include anthropometry, visibility, controls, and consistency.
One of the above concepts to discuss in this context is anthropometry, the science of measuring the human body in terms of size and capabilities. This, in particular, is pertinent in machine safe-guarding where there are clear specifications on machine guard openings relative to operator distance from the guard.
What does guarding really have to do with ergonomics? For certain machines, this is critical. Many types of machines must have dies cleared manually before the next operation. Some presses and press brakes fit this criterion. How far away must the operator be to observe machine functions, and yet maintain the production pace dictated by that operation? This is an old debate finally decided by NSC and OHSA. However, does this make it ergonomically correct for the operator? That discussion will continue for sometime.
Ergonomically Designed Components Add Value
Pittsburgh-based Pinnacle Systems supplies operator interface and safety equipment. Pinnacle recently announced its patented UltraTouch system as a direct replacement for spring-loaded palm buttons. UltraTouch system is designed to fit into existing operator palm button stations without modification.
The switch incorporates an advanced, redundant, diverse-sensor design. Each module has two different sensors with isolated circuits and a redundant monitoring circuit built into a high-strength NEMA 4 polycarbonate module.
The U-shaped sensor actuation channel provides a triggering point for the machine operator's hand. An invisible infrared light beam is the triggering mechanism. Once interrupted by the operator's hand, both the IR beam and the location sensor must be satisfied before any action is taken at the output of the module.
Generally these modules are used as dual-redundant cycle-start actuators on most machines. They're particularly effective on presses and other machines requiring dual-operator actuation to start the machine.
To further the ergonomic value of the design, two visible LED indicators provide status of the module to the operator. A green LED indicates that the output relay contacts are closed, both sensors have been actuated, and no failures have been detected. The red LED indicates that the relay output is open and no conditions were detected on both sensors. Moreover, an ergonomic zero-force actuation requires only the passing of both hands through the module slot. The hand position of neutral, zero degrees completes the ergonomic requirements.
Ergonomics has stimulated so much attention that it actually drives innovation even at the simplest level. For example, Elma Electronic, a designer of rotary components and electronic packaging products, boasts a new actuator knob with bell-shaped knobs that offer ease of use in several machine applications. Simple features such as a soft touch material and finger grooves for slip-proof turning add both ergonomic and aesthetic value to machine and operator interaction.
About the Author |
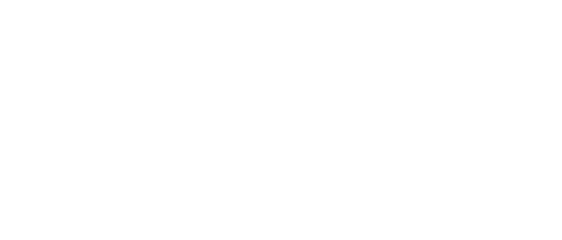
Leaders relevant to this article: