QUESTION:
---From March 2007 Control Design
ANSWERS:
I’m Still Waiting
I have not seen any wireless sensors for these applications, but I can see how they would be useful for equipment preventative maintenance reasons. I have been advocating that motion control vendors consider making vibration monitoring at least an option as part of their motor/controller design to make it easier for OEMs to provide this functionality without adding separate sensors, I/O, and the logic to go with it. Particularly these days with more and more equipment going shaftless, this feature would be a benefit. This concept wouldn't eliminate the need for devices the machine builder is asking for in areas that need to be monitored and which are not independently driven.
Chris Cote, manager – R&D Electrical Engineering, Goss International Americas
Tough Sell for Users
In my experience in the bulk material-handling industry, moving our clients into using networked fieldbus I/O is sometimes a hard sell. So, using wireless sensors as I/O might be asking a little too much. If the wireless sensors are used for monitoring and not for critical control, I can see a growing need for reliable and inexpensive wireless sensors. These sensors must be easy to maintain and configure by maintenance personnel. Wireless sensors will have different needs and requirements depending on what industry is being served. While these sensors might not take hold in one industry, another industry could have an immediate need, allowing wireless sensors to fill a needed role in process control.
Norm Seidel, Electrical Design & Controls, Smoot--Division of Magnum Systems
How We Do It
The practicality of wireless sensor technology has made great leaps forward in the past couple of years, and wireless sensor networks that are affordable, reliable, and easy to connect to PLCs and PCs now are on the market.
The following relates to a wireless network—such as the SureCross from Banner Engineering—that consists of one or more sensors connected to a node that collects data from the sensors and transmits it to a gateway. It’s important to note that multiple sensors of different types can be attached to one node, so you could monitor temperature, vibration, presence, and numerous other traits at the same time from one node. The gateway, which can receive data from multiple nodes, can control a machine directly or be attached to a control device (other than a safety device), PLC, or PC. This network architecture enables complete bidirectional signal verification, so all devices acknowledge that they’ve received communication from the sending device.
The method a network uses to sustain a signal affects its reliability. Among the most reliable yet cost-effective methods is frequency-hopping, spread-spectrum (FHSS). The information the sensor gathers is transmitted in small packets across numerous radio frequencies in a unique pattern, called the hop-code pattern. If interference on one frequency prevents a data packet from being received, the transmitter moves to the next frequency in the pattern and resends the data packet.
In the rare instance that the signal between a node and gateway is interrupted, devices attached to the network can perform a user-specified action. For example, if the gateway loses communication with an ultrasonic sensor that monitors the level of fluid being pumped into a tank, the pump can shut off until the signal is restored.
Part of the beauty of this type of wireless network is that it can be retrofitted into existing industrial systems, it can operate independently to manage a machine, or it can be used in conjunction with a PLC and/or PC software. Supported communication protocols include EtherNet/IP, Modbus RTU (RS485/RS232) and Modbus TCP/IP, and RS485/RS232.
The cost for a simple wireless network with a gateway and one node is about $1500—far more cost-effective than wiring and easily justified in many applications.
Ty Fayfield, president, Sensonix
Connect Them to Fieldbus
If each sensor must be wireless, then the solution is not a fieldbus. But if the physical arrangement of the sensors permits connection to a fieldbus or fieldbus-compatible I/O, with wireless connection from that point, then wireless Profibus or Profinet could be used. Such situations might include rotating machinery where slip rings are not practical, machines with linear motion where festooned cables are not practical, or autonomous machinery such as automatic guided vehicles. These kinds of applications are common and there are many suppliers of wireless connectivity for Profibus or Profinet. In fact with Profinet, standard IEEE 802.11 wireless components can be used. An additional benefit from this approach is that safety functionality can be integrated. Profisafe integrates safety with standard fieldbus functionality seamlessly over Profibus and Profinet. A number of applications using wireless and Profisafe have been installed.
Carl Henning, deputy director, Profibus and Profinet, North America
Close, But Maybe Not Yet
I think the promise of wireless sensors for machine builders and in factory automation is to provide additional data points for tighter control, predictive maintenance, and greater efficiencies of operation. Technology certainly exists to provide reliable and easy to interface wireless solutions for sensor communication.
Of course, inexpensive is a relative term, and I think the price per node that machine builders are looking for to eliminate their sensor wiring or to enable new sensor applications does not yet exist.
This being said, there are new wireless technologies and products in the industrial space every day that certainly will help to lower price points. And several standards activities (IEEE 802.15.4 based) hold promise of interoperability between different manufacturers’ products, thus creating the economies of scale needed to lower prices. The technology issues now being debated are how to make products based on this technology truly robust and reliable enough for factory-floor applications. I anticipate these issues to be sorted out in the next couple years.
Pat McCurdy, product marketing manager, interface product line, Phoenix Contact
Yes, but Mind the Choices and Details
Wireless sensors have been available for at least a decade now. The replacement of wired sensor networks by wireless for monitoring and control applications is a fast emerging and popular trend.
Modern consumers of wireless sensors are influenced by two major factors. The first is the skyrocketing cost of wires, wiring, labor and the other costs associated with installation, commissioning, and testing. Wireless systems are expected to bring down these costs. Factor 2 is the compelling advantage offered by wireless sensors for easier maintenance, relocation of sensor devices within the premises, and mobility in comparison with wired counterparts.
The most popular and widely available wired sensor networks are based either on RS485 or the Controller Area Network (CAN). These networks can be found installed aplenty in industrial buildings, factories, warehouses, and other commercial buildings. There are a few wireless standards in play today that are fast “unwiring” these wired networks, notably Bluetooth, ZigBee, Z-Wave, and the emerging Wibree.
Bluetooth is a mature standard and sells in large volumes, but Bluetooth’s technology and its high data rate make it more suitable and a very popular choice for being a voice and data link accessory for mobile phones today. However, the electronics that make up the Bluetooth solution can be inherently more expensive and can be overkill for sensing applications.
Z-Wave is a standard that is promoted by the Z-Wave Alliance and one that offers total wireless sensor network solutions.
Wibree is promoted by Nokia and a few of its alliance partners as a short-range wireless attachment to mobile phones, at a fraction of the cost of Bluetooth.
The ZigBee standard was developed specifically for wireless sensor networks and is available to subscribers and members of the ZigBee Alliance. The ZigBee Alliance is backed by a number of large control equipment manufacturing giants, semiconductor manufacturers and sensor equipment manufacturers. With this backing, ZigBee arguably enjoys high popularity and a larger installed base in comparison to Z-Wave and Bluetooth. There are several other proprietary solutions (some of the proprietary solutions are customized versions of these standards) that have been deployed as well.
Commercial deployments of ZigBee-based wireless sensors have been happening over the past few years with increasing scale. There have been deployments of Z-Wave and Bluetooth based products as well, but the extent and scale of such installations are not well known. Commercial deployments of Wibree-based products are unknown as well.
Wireless sensors are available today for mass deployments. These solutions are available from system integrators and wireless sensor network solution providers. The solution providers supply these products by designing, assembling the different discrete components and modules of a typical wireless sensor device, including the sensor itself, and manufacturing the products. Integrated wireless-sensor, single-module solutions from control appliance and sensor manufacturers are expected to be available by Q3/Q4 2007.
With increasing deployments of wireless sensors and sensor networks happening on a mass scale, costs spiral downwards. Further cost reduction would happen with the availability of these devices and systems on a wider scale by industrial product manufacturing giants such as Johnson Controls, Honeywell, Eaton, Philips and others. These firms are in the process of building solutions with wireless enablement. With their wireless solutions launched, some of these companies expect a cost savings of up to 20% in wiring and maintenance costs, the benefits of which will be passed on to the consumer over time. Competition will refine and regulate these costs as well.
Product reliability is a key success factors and one that determines a product’s success and popularity in the market. To ensure reliability, the wireless sensor device manufacturers put their products through certain reliability engineering tests such as stress tests and accelerated life tests. We put our products through a suite of additional reliability tests simulating harsh field conditions and noisy RF atmosphere.
Some of the wireless sensor devices might degrade in performance due to interference among themselves and/or from other wireless networks such as WiFi. These interference conditions also need to be simulated and tested in the lab as part of the reliability tests. By going through these tests and achieving manufacturing quality assurance, wireless sensors devices exhibit good reliability. However, it is recommended that the users run a comprehensive field trial with a limited set of wireless sensor devices prior to mass deployment.
Generic wireless replacement solutions for wired sensor systems are available. Connectivity to PLCs or PC-based systems can be as simple as plug, configure, and play through standard interface ports such as RS-232. Sensors for temperature, presence, and vibration can be easily integrated into these wireless platforms and quickly configured with the help of software tools that are provided by some of the solution providers.
Ram Satagopan, chief technology officer, Airbee Wireless
Examples and Questions
This is a question being asked on a global basis by equipment providers and end users of that equipment. It’s a strong indicator of awareness of the intrinsic benefits that can be realized through wireless communications.
Taking a current view of the question, two approaches have been taken. The first is citing specific examples of wireless sensor use with the measurement capabilities cited in the question. The second approach is to address cost, reliability, application ease, and the value proposition for wireless sensors in an industrial environment in a way that helps machine builders relate their needs to the offerings of wireless technology vendors.
Here are a few examples:
- On-line vibration monitoring of a paper machine at a large pulp and paper mill with the objective to maximize paper machine availability: 12 critical points were selected for wireless-based vibration monitoring, on-site installation required one and a half days and cost a small fraction of a conventional wired system. Upon startup two bearings were identified as failing which resulted in cost savings well in excess of the total project cost.
- On-line continuous temperature sensing of 2500 hp circulating water pump motors used in a large nuclear power based generation station: The objective was to minimize unplanned generation outages due to motor failure. At a cost less than 2% of conventional wired approaches and 50% of a single manual inspection, two pending motor failures were intercepted. Three scheduled motor overhauls and one motor rewire were deferred as unnecessary. User direct cost savings of more than $1 million over a one-year period were realized.
- Wireless monitoring of pipeline compressor station for failure prediction: The objective was to improve station productivity. Within two weeks of the installation, the system identified a crack in a compressor impeller blade as well as the onset of other pending failures. Cost savings estimate developed by the end user was $3 million.
Other applications can be cited including coal pulverizer monitoring, pipeline compressor monitoring, robotic manufacturing cell actuator monitoring, and pump bearing monitoring.
The above examples hold questions that need to be answered for all projects.What is the initial cost of the wireless sensor as well as the user’s total installed cost? Will the wireless device meet the performance and environmental requirements for the application, and can the wireless sensor and its associated gateway work seamlessly with the existing monitoring and control application without requiring extensive on-site technical support?
Another area that needs to be addressed is the role of the user’s corporate IT group in ensuring that the wireless sensors meet corporate security requirements, as well as proper management of the available RF space in the facility. While detailed answers to these questions require application-specific information, there are some practical guidelines that can help set realistic expectations.
The acquisition cost of a wireless unit will be influenced significantly by the level of embedment of the wireless sensor in the machine being considered. In many cases, the housing cost for an externally attached wireless device, along with the cost of the specific sensing element, represents the dominant cost element of the total wireless sensor installation.
As an initial approach, and for an externally attached unit, cost parity with a conventional non-wireless unit is a reasonable initial expectation that can be refined as more specific application details become known. For wireless sensors that are fully embedded in a machine, which also supplies power to the wireless unit, initial cost estimates would include the sensing element and supporting electronics for the wireless sensor. Costs for typical electronics can be as low as 15-20% of an externally attached unit. The major cost savings will come from dramatic reductions in installation costs typical of wired sensor approaches. The range in total installed cost reduction, including the cost of the wireless sensor, while dependent on the specific site, can be 40% to 90%. Additional benefits in soft cost areas are just as significant.
Achieving reliable performance of a wireless sensor not only requires that the wireless device provide acceptable communications performance, but also that the wireless sensor can survive required environmental conditions. Meeting the first requirement is best answered by knowing the link margin (a measure of the wireless RF signal strength) that can be achieved under specific conditions. This information should be available from the wireless technology supplier and should be further supported with a basic site survey. This survey ensures that the sensor can survive the field environmental conditions meeting. This is achieved by the unit meeting industrial certification standards for the application, such as NEMA, FM, CSA, CE, and ATEX.
Ease of application is a critical area. One of the most significant industry problems is the graying of the work force. End users are struggling to maintain their production assets as the available work force shrinks. Ensuring that the wireless sensor can be attached simply to typical monitoring and control systems that are PLC, PC or DCS-based is critical. The wireless communications channel should be a transparent pipe that gathers information from a sensor and presents it in an\accepted industry instrumentation communication format such as Modbus, HART, 4-20 mA, Ethernet, or OPC. This is a key requirement for success.
At a minimum, the selected wireless sensor approach should be sufficiently secure to prevent unauthorized access into the user’s major computer systems. A simple approach is to ensure that no IP address is required for the wireless sensor. Other features should include secure attachment of devices on the network and prevention of unauthorized attachment of rogue devices.
Gene Yon, president, Accutech
August's Problem |
Should we switch to servo motors?
We've specified steppers in our machining centers for a long time. Micro-stepping helped achieve better resolution along the way. Our problem is having to operate more slowly to achieve accurate positioning. Are there advantages in changing to AC servos that are worth the extra cost? Any tips to pass along?
Send us your comments, suggestions, or solutions for this problem. We’ll include it in the August 2007 issue, and post it on ControlDesign.com. Send visuals if you’d like—a sketch is fine. E-mail us at [email protected]. Please include your company, location and title in the response.
Have a problem you’d like to pose to the readers? Send it along, too.
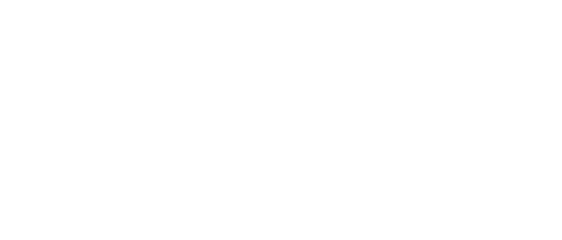
Leaders relevant to this article: