We need to measure motor speed in our dry food packaging machines to close the loop for more precise control. We narrowed our choices to either an encoder or a resolver, but we’re having trouble deciding which is best. What are the advantages and drawbacks of each technology?
—from October ’07 Control Design
ANSWERS
Resolvers Are Rugged, But Encoders Are Everywhere
Resolvers are inherently more rugged than encoders and less susceptible to electrical noise. Those are the only advantages. Not all resolvers are built the same way. You have to match your resolver to your input carefully. Though resolvers theoretically have an infinite resolution, in practice, they’re roughly equivalent to 1,000 ppr encoders. Resolvers are rarer and more difficult to obtain.
Encoders have a glass disk that can shatter. They also contain electronics susceptible to heat and possibly vibration. However, encoders are used all over the place, so it’s not like they’re super fragile. You can have encoders with very high resolution, but around a 1,000 ppr is common. Lots of places have encoders in stock, though this variety means you can accidentally pick an oddball, so work with your vendor and make sure you pick something common.
I recently went through this same issue and ended up picking an encoder.
I disagree with the comment that sufficient maintenance can make it more worthwhile to use a resolver [see Scott Gee’s response below]. There is no maintenance on either one. If there’s a problem, replace it like any other sensor. If you’re getting out a multimeter or o-scope to check a less than $500 sensor while production is down, then you’re wasting your time.
JAMES INGRAHAM, software development
Sage Automation, sagerobot.com
[via Machine Builder Forum at ControlDesign.com/MBF]
Support, Flexibility and Reliability
Resolvers had a brief heyday as the feedback device of choice. Tough and durable, their simple motor-like construction let them survive huge temperature extremes and rough environments.
However, resolvers today primarily are relegated to a small corner of the motion control market, namely, units built into the back of servo motors for feedback. Even in this application, digital encoders are squeezing them out.
All major drive and PLC manufacturers support encoder feedback, but only a handful support resolver feedback. This motivates motor manufacturers to offer encoders, not resolvers. There are just a few resolver manufacturers left.
Encoders can be fitted to many form factors. There are shafted models, hollow shaft, modular bearingless, and others. Customers can mount encoders anywhere, eliminate unreliable couplings, and fit encoders into unusual spaces.
Finally, encoder reliability now can exceed resolvers. Some encoder designs eliminate all moving, wearing parts. With magnetic sensors and fully sealed electronics, they can operate in the dustiest or wettest washdown environments and provide 100% uptime.
For your dry food packaging machines, we would recommend a magnetic encoder fitted to the back of the motor. Depending on the style or brand of motor, we would recommend either a modular, a C-face-mount, a wide-gap model, or a hollow-shaft unit. In either case, we would recommend a no-solder style of industrial connector to make your machine even more reliable.
BRIAN W. WINTER, encoder product manager
Avtron Manufacturing, avtronencoders.com
Resolvers: Tuning Required
The phrase “more precise control” would generally drive the solution toward an encoder over a resolver. The application of dry food packaging, however, might tend to drive it back toward a resolver. Consider these characteristics to help make the decision:
Encoders and resolvers can be packaged in basically the same ways, so there’s no advantage to one or the other as far as environmental protection.
The resolver is sturdy and possibly more suitable for a severe environment application with extreme continuous temperatures or very high vibration. However, an encoder can be very robust as well, so the only real advantage would be the ability of the resolver to withstand higher continuous temperatures. If your application requires the feedback device to operate in more than 125 °C environments, you probably go with the resolver.
Most motion control systems can work with resolvers or encoders, so there is no real difference in wires and interconnects. However, resolvers are analog devices, and they require a converter to format the measurement for processing by a digital computer. This conversion is done by a resolver to digital converter (RDC) or by a DSP and suitable input filtering circuitry. For example, something like Analog Devices’ AD2S80A can be used.
This is a tracking converter, which is implemented using a type two servo. A type two servo is a closed-loop control system characterized as having zero error for constant velocity or stationary inputs. Conversely, this type of system will demonstrate errors in all other situations, and the magnitude of these errors must be controlled through optimized tuning of the converter. The fact that the converter itself has dynamics becomes an important part of the system design. Being type two, the converter can introduce up to 180° of phase lag into the system. For a 12-bit converter using a 400 Hz reference , the RDC bandwidth (-3 db point) will be less than 100 Hz. Using the same reference, a 14-bit converter will have a bandwidth of 66 Hz, and a 16-bit converter will have a bandwidth of 53 Hz. A 100 Hz, -3db bandwidth means there will be approximately 3 db of peaking and 45° of phase shift at 40 Hz. As many servos attempt to close position loops near these frequencies, an added 45° phase shift would be undesirable.
Although the RDC tracking rate might not be exceeded, a system with difficult load dynamics could prove unstable when RDC dynamics are introduced. The situation only worsens when 14-bit or 16-bit converters are used. Another feature of the RDC is that the maximum slew, or tracking rate, is limited by the resolver reference, or carrier, frequency. For example, the AD2S80A RDC using a 400 Hz reference will have a tracking limit of 1,500 rpm. This value can be increased to 18,750 rpm using a 5 kHz reference. In contrast, encoders can be much simpler. When an encoder is used in a control system, there are only two issues to consider: desired resolution and the maximum rpm the encoder will work at. There are no encoder dynamics to deal with as the measurement process is fundamentally digital. An encoder provides data with guaranteed signal separation and symmetry at up to the rated speed, and that is all there is. Many encoders are now available with resolutions up to 25 bits, and some are capable of allowing the motors to run at 10,000 rpm with close to this resolution. As a result, an encoder-based application will generally have a wider dynamic range capability.
Resolvers are absolute measurement systems. They provide a unique sin/cos voltage at every point in a 360° rotation. An encoder can be absolute or incremental, and the output will be digital. Absolute encoders usually have a serial databus that the drive must communicate with to read out position measurement, so verify that the encoder and the drive are compatible. Incremental encoders are ubiquitous, and every drive made can interface to them. An encoder will be more accurate than a resolver and it’s associated conversion process.
If more performance or positioning accuracy becomes necessary later, it will be much easier to upgrade an encoder-based system. It will require only the feedback element to be replaced, and a software change to the drive, so that the new line count is accounted for. A resolver change will require reconsideration of the associated converter, supply voltage and frequency, and filtering, and this might not be possible to change unless the drive has been developed with this in mind.
ROBERT M. SETBACKEN, president, Renco
Encoders, renco.com
If You Have to Ask, the Encoder Is For You
Resolvers have been around much longer than optical encoders. As they are analog devices, outputting a sinusoidal signal that corresponds to shaft position, they allow the highest possible system performance, and are absolute within one revolution. Because the resolver outputs a sinusoidal analog signal, OEMs should use a controller capable of decoding the signal, and converting it into rotary position and speed information.
Unlike resolvers, encoders typically are constructed using a light source to shine through slots in a glass disk, and therefore provide a digital output. A light receptor on the other side of the disk sees alternating light and dark pulses. The number of pulses represents distance, while the frequency of pulses represents speed. Both the rising and falling edges can be counted, thus doubling the resolution. The addition of a second set of slots on the disc, offset 90° from the first, enables the direction of rotation to be determined. Incremental optical encoders are relatively inexpensive to build, and therefore much less expensive to purchase. Also, because the output is digital, a simple high-speed counter is all that is required in the controller.
An encoder is the best choice for this case because the application is measuring speed, as opposed to position, and is a dry food environment (i.e. not extreme). Furthermore, since the OEM is asking about the differences between the two technologies, one assumes the company does not have expertise in integrating feedback devices and the simpler encoder would be the best route.
DAVID HANSEN, global product manager,
Kinetix Motion Control, Rockwell Automation
rockwellautomation.com
How Competent Are Your Techs?
In a perfect world, you can’t beat a resolver. The exacting control across time is unbeatable. Unfortunately, things break and technicians become less technically competent every day.
My opinion (as a tech who maintained both technologies for more than 20 years) is that encoders are easier to set up and maintain, especially in high-speed production applications.
As of a couple of years ago, it was just as important—maybe more so—to consider the cost and complexity of the motion control system that supported the resolver or encoder.
Resolvers were more expensive from a total control point of view. I could teach a guy with a multimeter how to maintain an encoder-controlled system. How many shop-floor techs these days can read an oscilloscope to set up and maintain a resolver?
For years, every resolver had to have a tachometer associated with it. How many people would know that a technician’s most important maintenance tool for a resolver/tachometer combination was either rubbing alcohol and a cotton swab or a pencil eraser?
After the original encoder manufacturers improved their optics and went from single-ended to quadrature decoding, I became a huge advocate of the encoder, because I didn’t have to clean tachometer commutators any more.
A resolver is an analog device trying to exist in a digital world, so additional A/D circuitry always will be required for resolvers. Many modern controllers have software that help the user configure a resolver, but just as often an oscilloscope (and technical competency) is required.
If the customer has lots of money and a technically competent maintenance team, go for the resolver. If not, go for the encoders every time.
SCOTT GEE, chief software architect,
Innovative Software Design Technology,
isdtech.com
[via Machine Builder Forum at ControlDesign.com/MBF]
Three Choices
The question posed is a very good one. Besides dry food packaging machines, controlled servo drives are used in many other areas. The choice of feedback components to measure motor speed is vital to the ultimate control quality of the drive. Issues of resolution and position error within one signal period are distinctly in the foreground in this case.
The features of feedback components typically used for reporting speeds to servo drives differ significantly. Resolvers mostly have only one signal period per motor revolution. Therefore, the position resolution is limited. However, typical encoders have many signal periods, including optical rotary encoders, which are based on very fine graduations of 512 or 2,048 signal periods. The charts below provide a brief comparison overview of three different encoder technologies including pros and cons.
As noted, since the positioning accuracy and speed stability behavior of these machine axes significantly contribute to the quality of the end product, for best control, a position encoder with a large number of measuring steps and high signal quality is optimal.
It is important to note that irregularities in the speed stability can be caused by mechanical influences from the drive train as well as by position errors resulting from the encoder technology used. If the resolution of the measured signals is too low, or if the interpolation error is too high, errors will appear. The speed stability of certain motions in production systems can also be considered as a production parameter relevant to the quality.
Higher resolutions and accuracies can decisively improve the speed stability behavior of the motor. In addition, disturbances in the motor current are reduced significantly. The motor then operates quietly and develops only a small amount of heat.
Ideal output signals with high resolution support a high bandwidth, which means that load variations only have a minimal effect on the rotational speed.
TOM WYATT, product manager
Heidenhain, heidenhain.com
Functionality Over Technology
The choice boils down to functionality rather than technology. Both optical encoders and resolvers are reasonable devices to use for motor feedback.
Optical encoders are more prevalent in industrial speed control situations, for example AC vector controlled motors, and they have very simple interfaces that are easily accepted by most common industrial controllers. Resolvers usually are specified when either the form factor, temperature or vibration specification of an optical encoder is not sufficient for the application.
SCOTT ORLOSKY, marketing manager,
BEI Industrial Encoders, beiied.com
An Attractive Encoder Solution
Resolvers convert angle information of a mechanical shaft to electronic angle information with ultimate precision due to their measurement principle and electromechanical design. They offer excellent resolution, robust mechanical design and excellent electric and magnetic shielding from harsh ambient conditions.
However, the evolution of magnetic rotary encoders has in the mean time reached a remarkable level.
We think that resolvers still are unbeaten in accuracy and resolution, which makes them the best choice for high-performance electromotive drive systems, where form factor and price does not play an important role and smooth and precise drive characteristic is a must.
Magneto sensor rotary encoders could act as a replacement and even outperform them in several aspects as follows:
- Magnetic encoders do not contain coils as resolvers do. Therefore, there is no risk with broken coil connections, coil- and interconnect wires.
- Excellent reliability, long-term and temperature stability due to monolithic integration in standard CMOS technology without any encoder specific process or post process steps. This offers the same level of reliability as state-of-the-art automotive ICs, which is usually higher level as known from electro mechanic components as resolvers. The Hall sensor issue, with long term drift due to mechanical stress relaxation and solder heat drift, is not relevant due to our patented differential approach with small and symmetric Hall element array.
- Integrated system on chip enables entire signal conditioning on same component providing minimum signal latency and features like different output formats, zero point programming, commutation outputs for brushless motors, multi turn counters, integrated voltage regulators and protection structures.
- Redundant encoder arrangements with two independent sensor devices integrated in one small package are possible.
Small size, low sensitivity, differential Hall element arrays together with a small and strong diametric magnetized magnet makes our encoders extremely robust versus external magnetic fields. Shielding from strong electric fields can easily be accomplished by foils from non magnetic material.
Also speed performance up to several 10,000 rpm as well as temperature range of -40-150 °F ambient is comparable with resolvers.
MANFRED BRANDL, product manager
Austriamicrosystems, austriamicrosystems.com
Sine-Cosine Encoders
The choice of feedback devices for controlling the velocity loop of a servo is a tricky one. Resolvers have been used for quite a while for feedback in motion systems because they are very robust. They’re made of five wound coils, a stator sine and cosine, and a rotor receiver and transmitter. Coils are very reliable, but expensive to produce. A sine and cosine wave are energized on the stationary part of the resolver attached to the motor. The rotor resolver is attached to the rotor of the motor and as the motor begins to move, the rotor coil moves on and out of phase with the sine and cosine coils of the stator. The resulting waveform gives us the speed if we count how often the signal changes from sine to cosine. We also get direction because we can reference the result against the fixed waves of the stator. This is a simple device that provides speed and direction.
The drawback of a resolver is that it relies on a circuit that can take in the resulting signal and add resolution to it. A resolver rotor has only so much space on it—about enough room for a few dozen sine-cosine poles—but the resolution depends on increasing the amount of windings. The way to increase the resolution is to create a circuit to compute the phase differences between the sine, cosine and rotor output. A lot of servo control systems can do this, but the resolution is limited.
Encoders work pretty much under the same principle. Attached to the rotor of a motor is a glass disc with slots printed on it. Fixed to the stator of the motor is the receiver of the encoder that has two receiver transistors 90° out of phase with each other. As the motor rotor turns, the slots on the discs pass over the receivers and again there is speed feedback as well as direction. However, the speed signal is only as resolute as the number of slots you can print on the disc. For most servo systems, this number stops at 8,192, although others have been able to get as many as 32,000 onto a disc.
A new generation of encoder feedback has combined these two technologies together. Sine-cosine encoders print a sine wave on the glass disc at a low resolution (1,024 waves per revolution) with the same phased receivers as a normal encoder. Using a circuit (like with a resolver) to calculate the phase between the result against the reference, you can get a great amount of resolution (250,000 pulses per revolution, or better) out of a device that is compact and inexpensive to manufacture.
With the increased performance and reduced cost of the sine-cosine encoder, the need for the additional cost of a resolve system has been eliminated.
TOM JENSEN, engineering manager,
Elau North America, elau.com
March's Problem
ENCLOSURE CHOICES? Our packaging machines are custom designed for each application, and in many cases we find that off-the-shelf enclosures won’t work. Although the major enclosure manufacturers tout their ability to build custom panels; we have not been happy with their prices, delivery, or service. Are there better alternatives?
SEND US YOUR COMMENTS, SUGGESTIONS, OR SOLUTIONS FOR THIS PROBLEM. We’ll include it in the March ’08 issue, and post it on ControlDesign.com. Send visuals if you’d like—a sketch is fine. E-mail us at [email protected]. Please include your company, location and title in the response.
HAVE A PROBLEM YOU’D LIKE TO POSE to the readers? Send it along, too.
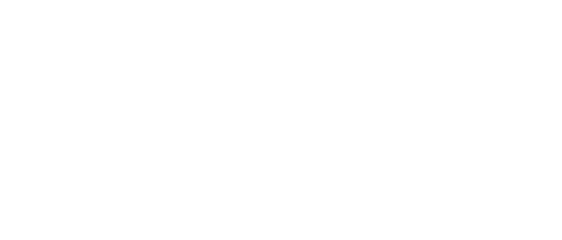
Leaders relevant to this article: