In 10 years at Bolthouse, Opperman has helped build 60 to 80 machines that sort, process, and package carrots into an increasingly diverse range of products, especially beverages. Because carrots need special handling, Bolthouse designs and builds many of its own machines, and then organizes them into long production lines. Sensors and I/O devices help these machines sort, peel, wash, trim, cut and weigh the carrots, and then roll out plastic packaging, detect ends and weigh packages. Recently, Bolthouse opened two bottling plants and one salad dressing plant, and these needed production lines and machines, too.
Traditionally, Bolthouse’s machines used hardwired I/O components, and had to run more than 300 points back from hundreds of instruments in massive cable trays to motor control centers and PLC combinations. “As we expanded into more complex processes, beyond motor starts and stops, we had analog and digital signals too, and so we kept expanding the racks as we added more hardware from the field,” says Opperman. “Now, we had 500 to 600 instruments installed, and each had individual wires and connectors. However, even though we were very careful about precisely labeling each, so we wouldn’t need a schematic in the field, we still needed two people to do troubleshooting.”
Opperman says Bolthouse began seeking to revise the increasingly unworkable wiring situation on its machines and network about five years ago. “We starting looking at the labor and material costs, and found that on a typical, smaller, $15,000 machine, we could save $5,000 by doing on-machine wiring with DeviceNet, AS-i, Profibus or a similar protocol. Basically, all the machine’s instruments would just go back to a Turck block on the machine, and then only four wires would go off the machine and back to the PLC. This meant we could save multiple hundreds of thousands of dollars over the course of building a larger project such as one of the bottling plants.” These four wires, two for communications and two for power, are usually run in a single cable. This network typically runs at 125 kbps, which gives Bolthouse all the data throughput and reliability it needs.
Tale of Two Bottling Plants
This shift in its networking strategy also occurred between the time Bolthouse built its first juice bottling plant about seven years ago, and when it built its second plant about three years ago. The two plants bottle the same juice products in all container sizes between 350 ml and 2 liters. The first plant consists of a French design, using hardware from Schneider Electric’s Telemecanique division, to run 9,000 bottles per hour. The second is a German design with hardware from B&R and Rockwell Automation that run 15,000 bottles per hour.
“Both plants use distributed I/O systems and there isn’t much difference in the machine-mount I/O at each, but the newer plant’s system is just more compact. The first plant and its machine can do different sizes, but the second one is able to do it easier. For example, the newer machines’ design and software make it easier to do lane changes to shift product,” adds Opperman. “Likewise, using DeviceNet and the other fieldbuses reduces the footprint and impact of our machines, and makes them easier to build. Running wires used to mean we had to get into the tray, and shut down the process. Now, we just run a couple of commissioning cables, and we almost can do it during a regular production break. Also, when we buy from an OEM, we now ask them to integrate their machines with our network. If they’re not prepared to offer a fieldbus, we buy the machine, and custom add it ourselves.”
In addition, Bolthouse recently updated its 12-year-old, three-stage evaporation system that makes concentrated juice. It originally had three rudimentary, closed control loops. However, this was a very operator-intensive process that involved manually adjusting the machine and inputting set-points, which allowed too much latitude and potential for product variance and errors.
“Now, we’re using machine-mount I/O to go with a recipe-based system in the evaporator that’s already in some other Bolthouse machines,” says Opperman. “To follow a recipe, it uses preset algorithms to make changes such as adjusting flow, temperature and pressure. We also have heat exchangers between each stage, and they need flexibility to handle variations between the different vegetables. All the control valves and controls need a wide operating range to manage these differing viscosities. All of these needs are helped by our machine-mount I/O cabling and components.”
Less Wiring = Less Labor
That’s what it’s all about. Saving on cabling and time during machine building and maintenance fueled initial moves to distributed I/O, and now machine-mount I/O is continuing this natural evolution.
On-Machine and On-Vehicle
AutoGlide LLC in Georgetown, Ky., uses a rackless PAC with an expandable I/O platform to save 20-40% more space than traditional mounting when building its automatic-guided-vehicle conversion kits. AutoGlide also saved 50% on installation time and 40% on wiring costs.
Photo by Rockwell Automation
“Machine-mount I/O is the next step in distributed I/O systems, which were developed for the simple purpose of replacing parallel wiring,” says Jason Haldeman, product lead specialist for Phoenix Contact’s automation systems. “The first developments were IP20 distributed I/O placed in multiple locations around machines, but these I/O stations still require parallel wiring into the machine. Machine-mount I/O extends the I/O network directly into the machine, completely replacing parallel wiring. There are many options available when it comes to machine-mount I/O. The major I/O providers support bus networks like DeviceNet and EtherNet/IP, Profibus and Profinet, Interbus, and Modbus TCP. However, the biggest differences between vendors are in their power and communication connections and wiring schemes.”
Besides allowing components to emerge from their former cabinets, molded cables and connectors with network connectivity and power allow plant-floor users to make much more rapid tooling changes, according to Mark DeCramer, Wago’s product manager. In fact, Wago is introducing its Speedway products this year, which are offering IP67-protection for PLCs and other equipment. “We’re even adding a provision for IP67 safety modules later this year, so they to can be mounted directly on machines,” says DeCramer.
Awareness Slow to Grow
Even though IP65 and IP67 devices have been available for about 10 years, adoption rates have been frustratingly slow for many supporters.
“Putting I/O devices closer to sensors shortens cable runs and saves on wiring, but results for machine-mount I/O have been a mixed bag so far,” says Graham Harris, president of Beckhoff Automation. “From 1998 until now, IP67-related technologies haven’t taken off as fast as expected. This may be because users aren’t seeing as much up front savings as they would like. Users should look at the overall, long-term costs of traditional wiring, enclosures and labor, but they often have more pressing concerns.” To help remedy this situation, Beckhoff recently introduced IP67-protected versions of its EtherCat modules, which allow users add incremental data modeling to their applications, and make it easier to drop modules into more unusual locations.
Bob Gardner, senior I/O product manager in Turck’s Network Interface division, adds that all historical PLC functions are now available in machine-mount I/O packages, such as its BL67, though many potential users apparently don’t know it yet. “Many people see that machine-mount I/O is available, but there still doesn’t seem to be that much awareness,” says Gardner. “A lot of folks are still surprised that remote I/O systems can reside on machines.”
Still, when a user is convinced what machine-mount I/O can do, the results can be dramatic and immediate. For example, RRR Development Co. in North Canton, Ohio, recently added IP67 networking and connections to the two-stage tire making machines it builds. These allowed RRR to implement a scalable architecture, machine-based information layer, and motion integration capabilities to make more flexible, capable machines faster. Bob Irwin, RRR’s sales and engineering VP, says one of its machines can now make agricultural, passenger car, light truck and motorcycle tires, which typically takes three of its competitor’s machines to do. These improvements only save about $400 in per-machine cost accounting, but easier, quicker building has allowed RRR to make 10 more of its $250,000 machines per year for a $2.5 million boost to its revenues.
“Our old system took 17 steps to make a terminal strip-type connector, but we’re down to six steps with Rockwell Automation’s On-Machine components,” says Irwin. “It used to take us 45 minutes to an hour to do a complete cable swap, and now we can do it in less than a minute. By condensing our wiring, mechanical and electrical times, we’re saving several days on the time it takes to fabricate our machines, and so our savings is that we’re able to build several more per year.”
Mounting the Machine
Once users realize the true potential of machine-mount I/O and want to use it, Harris says they need to look at their existing signal types, check the true costs of their present wiring, and evaluate their designs and space issues to see if machine-mount I/O is a rational decision for them. “Many on-machine I/O blocks have eight 24 V digital I/O points, and so users can mix and match signals on one rack,” adds Harris.
“Users need to understand how machine-mount I/O can save time on the machine’s start-up and troubleshooting. The system is designed with pre-made cables that simply connect to the proper modules,” says Haldeman. “Different manufactures use different wire schemes for their specific machine-mount I/O options. The most important to-do is to have a good knowledge of what the I/O requires for proper operation. One of the most important thinks to consider when implementing a machine-mount I/O system is picking a supplier that provides flexible product offerings across the entire IP20 and IP67 field. Not all applications can be completely converted to IP67 I/O. Most applications use a mix of IP20 and IP67 I/O, so it’s helpful if the system lets the user mix and match.”
Connecterizing I/O Pays OffA twisted-pair fieldbus eliminates a lot of point-to-point hardwiring, as well as the installation time and troubleshooting that goes with it. Turck reports that connectorized I/O can take this evolution a step further by almost eliminating troubleshooting. Turck also reports that plants implementing plug-and-play connectorization can reduce startup costs by 75%, including 10-60% savings in initial capital expenses.Turck estimates that a typical conveyor system with four diverter sections, four middle sections, and four end sections—each with three electrical control devices, one motor, small starter enclosure, two proximity switches and a machine-stop button—would cost 20-25% less overall to design and build with connectorized, modular I/O than a traditional PLC-based design. Material costs are 28% more for connectorized/modular components, but Turck reports the cost of installing a plug-and-play system can be 90% less than for cage-clamp terminations. Also, indirect savings with connectorized I/O will include 80% shorter design-cycle time, 80% shorter installation cycle and 80% reduced maintenance and downtime.
|
For example, Opperman adds that he and his colleagues at Bolthouse first got the courage to use DeviceNet on their machines about four years ago when they were assigned to double the size of a small, six-year-old, storage tank farm at their facility, and update its controls with automatic valves and added monitoring for better tank control. Consequently, the company’s engineers put in four times as many instruments and controls, but using DeviceNet and machine-mount I/O allowed them to do it for ¼ the cost of the original tanks. “Hardwiring would have taken up a huge amount of space and a lot more time to check out,” adds Opperman. “This tank farm’s original hardwiring took four people a week to check out. The new system took two people about 45 minutes to check out.
Opperman also used pre-molded cable, so hook-up time was down to about zero, and chances for error were reduced. “Both the discrete and analog I/O points now used M12 connectors, as well as some minifast and picofast,” he adds. “Also, our troubleshooting volume dropped to about zero on new installations. This is what made us brave enough to use DeviceNet in a lot of other places and machines.
“We’ve been building rapidly for years, and so we have a good idea about the hours and cost it will take to do any project. This is what drove us to use machine-mount I/O. Instead of wiring all our devices back 300 feet, we could just wire a few back 50 feet in a few places. We have a lot of harsh chemicals, humidity and temperature changes on our plant floor, and though PLCs wouldn’t survive in these conditions, we can now put IP67 blocks right on our conveyors, or put IP67-rated devices in a NEMA 4x box.”
Inevitable Ethernet, Wireless Future
Unsurprisingly, now that once machine-mount I/O components have emerged from their former cabinets to take their places on machine and production lines, they too are being beset by offers to add Ethernet and wireless networking capabilities.
“Similar to all network topologies, Ethernet is the future,” adds Haldeman. “This trend is already seen in the IP-20 I/O offering. Machine-mount technology is following right behind by creating machine-mount switches and I/O devices for EtherNet/IP, Profinet, and ModbusTCP.”
Opperman acknowledges that Bolthouse also is evaluating where it might add some wireless capabilities to its machines. “We’re looking more at wireless,” he says. “However, there are some areas where it might be more useful to use than others.”
Is machine-mount I/O worth it? In your experience, are the higher material costs up front outweighed by the installation, configuration and eventual maintenance savings? Stand up, be counted, and let us know at ControlDesign.com/ioworth.
Evolution to Machine-Mount I/O
Over the past 40 years, methods for networking input/output (I/O) components that link sensors and other plant-floor devices up through PLCs and other control and automation devices have passed five distinct milestones, according to Ed Rogin, Siemens Energy & Automation’s product marketing manager for distributed I/O. Though different applications and industries have adopted these technologies at different times and to different degrees, mainstream use of these methods started mainly in the following decades.
1960s-70s—Almost all applications used centralized I/O racks that were all hardwired and used relay logic.
1970s—First PLCs introduced, but they and all I/O points still kept in centralized cabinets.
1980s-90s—Some distributed I/O installed along machines to avoid having to bring every wire back, and some limited buses used to network them. Main CPU functions still in main cabinet.
1990s-2000s—Smaller CPUs implemented that are able to communicate between with each other, and these allow greater distribution of main-rack functions using peer-to-peer communications.
2000s to present—Increasing use of mater-slave combinations, linking to a main master that typically still has its own CPU. However, there are now more distributed CPUs on the network, so slave CPUs can control small work cells. As a result, supplier are introducing CPUs that go with their I/O devices, and protect them with IP67 molded enclosures.
Machine-Mount I/O Reaches Out
Users are implementing machine-mount I/O and other IP67-protected components in a variety of innovative applications, according to Beckhoff Automation. Here are some of the most innovative projects that Beckhoff has assisted recently.
- Prettl Electric in Greenville, S.C., builds wiring harnesses for automotive anti-lock braking (ABS) and emissions control systems, and needed to develop a new pick-and-place segment in its production line in 2006 that could remove imperfect harness wires and establish uniform cycle times for the line’s injection molding machine. Ralf Opper, Prettl’s electrical controls engineer, says his firm decided to use Beckhoff’s CX1000 embedded PC, TwinCat IEC 61131-3 software, and BC9000 Ethernet bus terminal controller networked via Modbus TCP/IP. The bus terminal controller creates a digital handshake between the injection molding and wire hardness clip assembly machines right on the production line. The pick-and-place machine also uses I/O bus couplers and servo drives networked by the embedded PC via CANopen, as well as Beckhoff’s IP67 I/O linked to its eight-channel, IP67-protected digital inputs for remote I/O points. “When compared with the effort that would have been required to wire junction boxes to multiple PLCs over and over again, IP-Link help us cut I/O wiring time by more than 50%,” says Opper.
- BMW’s plant in Dingolfing, Germany, is using Beckhoff’s IP67-protected fieldbus modules mounted on the end of a Kuka robot to insert rubber seals into the BMW 5 Series’ electric, glass-sliding/vent roofs. These seals used to be mounted manually. This system includes a coupler box that gathers I/O data from five extension box I/O modules via a fiberoptic connection for light barriers and sensors that check for uniform tension over the complete length of the rubber seal during installation. The robot’s builder, Symax Systemtechnik Sondermaschinenbau GmbH, deciced to use Beckhoff’s IP67 modules because they didn’t need any added protection and because they were half the width of alternative modules.
- To prevent breakouts in its continuous casting process, Germany-based SMS Demag also uses IP67-protected Fieldbus Boxes to collect temperature data from up to 100 thermocouple sensors. This information is evaluated via gradient analysis to help detect and heal irregularities. To reduce the expense of reading sensors with its former multi-function coupler, SMS developed its IP67-based data acquisition system, which records temperatures directly on the mold, and transfers them via Profibus to a PC with a TwinCat software-based PLC with a 250 msec cycle time. This solution identifies impending breakouts more quickly, and allows countermeasures to be initiated sooner, such as reducing flow. Also, the IP67 modules enabled SMS to replace its former multi-core master cables with one hybrid cable for bus communications and power. In fact, SMS found it could integrate these IP67 modules right into the mold’s water-cooled protective housing, which further protects them from the hydrofluoric acid used in the casting process.
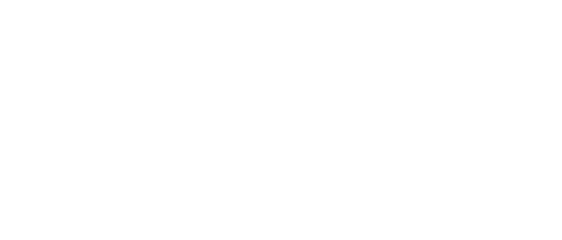
Leaders relevant to this article: